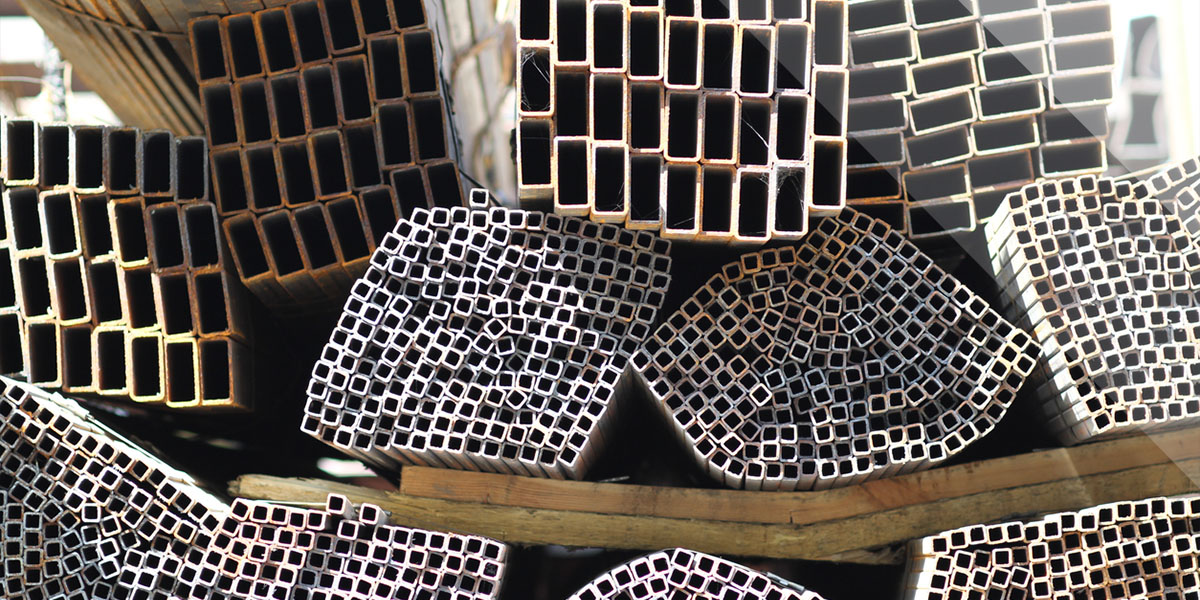
Thermoset composites have the unique ability to be adapted for various functions and industries, including aerospace and transportation. You can use a wide range of materials in the design of composite. This flexibility also poses a challenge when it comes to choosing the best material for your application. In plastic design, it’s important to keep the function in mind to achieve the desired outcome. Explore other considerations for composite materials design.
What Is the Material Composition of Composites?
Composites are made up of several different materials. The composition consists of epoxy and resin reinforced with a combination of carbon and glass fibers, which are all layered to form an extremely rigid and robust structure. More than 95% of thermoset composite parts are made up of epoxy resins and polyesters. Other resins used include phenolics and silicones.
Polyesters
You can use polyesters in any molding process for thermosetting resins. They can cure resins at room temperature and normal atmospheric pressure, or 350 degrees Fahrenheit and under higher pressure. Polyesters have several advantages, including low cost, easy handling, good mechanical, electrical, and chemical properties, and dimensional stability.
You can compound polyesters to be hard and brittle or flexible and resilient as well as weather and chemical-resistant. For fire resistance, there are halogenated compounds. Polyesters can also be used in ready-to-mold resin bulk molding compound (BMC) and sheet molding compound (SMC). BMC is a premixed material made with resin, filler, glass fibers, and other additives. SMC consists of glass fiber reinforcement, resin, filler, and additives made into a sheet form.
Epoxies
This low-molecular-weight, syrup-like substance is cured with hardeners. The hardener forms part of the finished product, so it’s chosen to add desired properties to the thermoset. You can cure epoxy at room temperature, but heat curing produces higher properties. Epoxies have excellent adhesive features and are widely used in laminated structures.
Phenolics
These are the oldest thermoset plastics with excellent insulation properties and moisture resistance. They have relatively good chemical resistance except in the case of strong acids and alkalis. High-pressure methods such as compression molding and continuous laminating are used to process reinforced phenolics.
Silicones
Silicones have excellent thermal stability, even up to about 600 degrees Fahrenheit. Dielectric properties are outstanding, and they have low water absorption. In terms of chemical resistance, silicones perform well except in the case of strong alkalis.
Glass and Carbon Fiber Reinforcement
The most common reinforcement materials are glass and carbon.
Glass fiber has a tensile strength of 500,000 psi and makes up 90% of thermoset resin reinforcements. These fibers come in several different forms, including:
- Continuous strands bundled together into rovings, which is the strongest option
- Chopped fibers
- Chopped strand mat
- Woven fabrics
- Multiaxial fabrics
- Milled fibers
Carbon fibers can be short and fragmented or long and continuous. The main feature of carbon fibers is their high strength-to-weight and stiffness-to-weight ratios. They have excellent fatigue resistance, and the chemical resistance is better than glass-reinforced thermoset options, especially in alkaline environments. Like most inflexible materials, carbon fibers have low resistance to impact and are rather brittle.
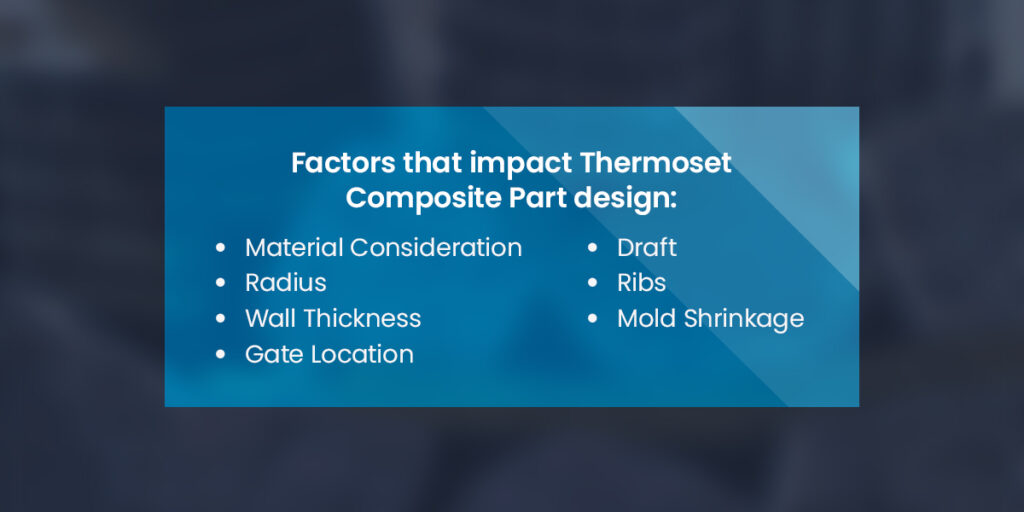
How to Design a Thermoset Composite Part
When designing plastic parts, a few essential factors include material selection, tooling, and part design. It’s important to design parts based on the end user in mind to ensure you create a functional element. Let’s look at the factors that impact design.
Material Consideration
Choosing the right plastic is complex and involves several considerations, such as:
- Temperature: Thermal stress may occur during assembly, finishing, and shipping.
- Chemical resistance: Consider the effects that may occur if the part comes in contact with any solid, liquid, or gas.
- Agency approvals: Government and private institutions have standards for properties such as heat resistance.
- Assembly: The part may go through different steps, such as adhesion, mechanical fastening, and welding.
- Finish: The composite can produce different desired finishes, such as smoothness and gloss.
- Availability: Consider the resin availability and how much you need for production.
Radius
Determine the radius in relation to the part’s thickness in order to eliminate high-stress areas and avoid possible breakage. A general rule of thumb is that the thickness of the corner should be 0.9-1.2 times the nominal thickness of the part.
Wall Thickness
In the case of injection molding, consistent wall thickness is essential for preventing wall defects. Melted plastic naturally flows to the areas of least resistance, which causes thickness inconsistencies. These flow characteristics must be taken into account to ensure a uniform part.
Wall thickness considerations are not a risk for rigid composites where fabric dipped in resin is stacked and compressed. This process offers natural uniformity for the part.
Gate Location
Gates are another vital aspect of injection molding as they ensure that the resin flows appropriately into the mold and distributes throughout the part. The type of gate and where you place it significantly impact quality and viability. These locations can also translate to well-distributed plastic for thickness consistency.
Draft
The draft refers to how the vertical walls of the plastic part taper. If a piece does not have a draft, this affects how it ejects from the mold, and it may sustain damage during ejection. Typical draft angles are between 1 to 2 degrees but can vary depending on the part specifications and restrictions.
Ribs
Including ribs can help reinforce the part’s strength. Depending on the type of material you use, the thickness should be 50% to 70% of the relative part thickness to avoid sink marks.
Mold Shrinkage
During plastic part molding, parts can shrink by as much as 20% in volume. Here are a few ways to avoid shrinkage issues:
- Adjust the formulation.
- Adjust the design to get the correct dimensions based on the expected shrinkage.
- Optimize the processing parameters such as melt temperature, molding temperature, and cooling time.
What Are the Benefits of Stock Laminate Shapes in Plastic Part Design?
Thermoset composites have long been produced in stock shapes, such as sheets, rods, and tubes, and fabricated into the desired geometry. This approach may not start with a net shape, but it does have several advantages:
- There’s no need for specialized tools or molds, allowing for faster prototyping.
- The high-speed, automated process ensures highly repeatable and consistent results, ideal for large volumes.
- Stock shapes have already been produced and are ready to use for a new application or as a starting point for a new material.
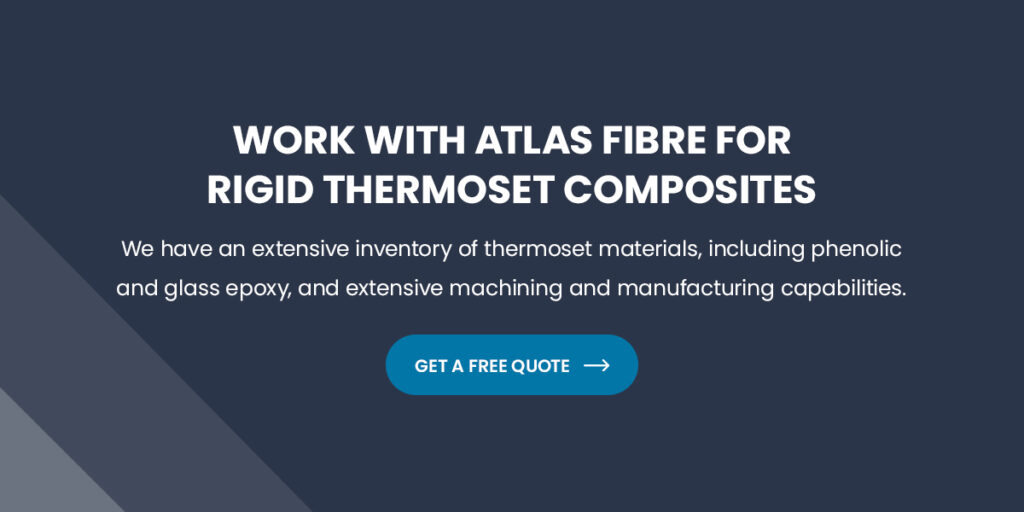
Work With Atlas Fibre for Rigid Thermoset Composites
At Atlas Fibre, we specialize in rigid thermoset composites. Our thermoset manufacturing process involves dipping fabrics into resin, stacking these pieces, and compressing them. This process lends itself to better performance at higher temperatures and is more cost-effective than other approaches. After creating the thermoset base, we use various machining methods to create custom components.
We are the leading supplier of thermoset composite laminate in North America. We have an extensive inventory of thermoset materials, including phenolic and glass epoxy, and extensive machining and manufacturing capabilities. To learn more, contact us for a quote today!