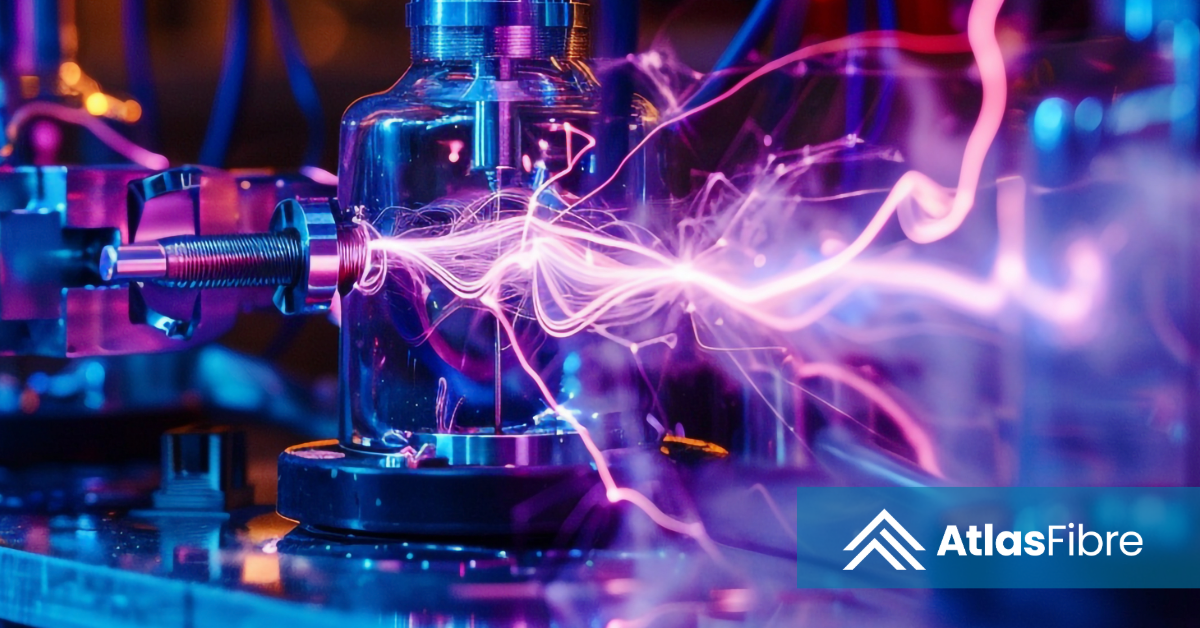
In industries where precision and safety are paramount—such as electronics manufacturing, aerospace, and cleanroom operations—managing static electricity is a critical concern. While conductive and insulative materials play important roles, dissipative materials strike a unique balance, offering safe, controlled discharge of electrical charges.
What Is a Dissipative Material?
A dissipative material, sometimes referred to as static-dissipative or electro-dissipative, is engineered to control how static electricity flows across or through its surface. Unlike conductive materials that allow electrons to race to ground, or insulative materials that trap charges, dissipative materials allow charges to drain slowly and predictably. This controlled discharge helps prevent dangerous static sparks and minimizes the risk of damage to sensitive electronic components.
Key Properties of Dissipative Materials
The performance of dissipative materials hinges on a few crucial characteristics:
Surface Resistivity: Typically falls between 10⁵ to 10¹² ohms per square, offering a moderate resistance that allows safe discharge of static. This places dissipative materials between conductive and insulative materials on the resistivity scale.
Controlled Charge Flow: Charges migrate gradually, which reduces the risk of electrostatic discharge (ESD) that can destroy microelectronic circuits or ignite flammable vapors.
ESD Safety: Because of their ability to mitigate sudden discharges, dissipative materials are the go-to choice for ESD-protected environments, such as semiconductor cleanrooms, PCB assembly lines, and flammable material handling zones.
How Do Dissipative Materials Work?
Static electricity is generated when two surfaces come into contact and then separate—causing electrons to transfer from one to the other. Without a safe path to ground, this charge can build up and release suddenly, creating a spark or surge.
Dissipative materials act as a middleman between extremes. They provide a pathway for excess charge to migrate toward ground, but unlike a conductive material, they do so slowly and predictably, making them safer and more stable in sensitive applications.
Common Applications
Dissipative materials are integrated into a wide range of industrial and commercial environments where ESD protection is a priority:
Protective Packaging: Used in ESD-safe bags, containers, and foam inserts that shield electronic components during shipping and handling.
Flooring and Work Surfaces: Found in assembly benches, workstations, and industrial flooring where technicians handle circuitry or delicate parts.
ESD-Safe Apparel: Shoes, gloves, and lab coats made with dissipative fibers prevent charge buildup on workers.
Cleanrooms and Hazardous Environments: Essential in environments handling volatile chemicals or combustible materials, where a single static spark could lead to disaster.
Example: Otter brand antistatic ESD shoes with “OTTER” and “ANTISTATIC” molded into the sole are a practical illustration of dissipative technology at work.
Property | Conductive | Dissipative | Insulative |
---|---|---|---|
Surface Resitivity | < 10⁵ Ω/sq | 10⁵ – 10¹² Ω/sq | 10¹² Ω/sq |
Charge Flow | Very fast | Slow, controlled | Very slow (trapped) |
ESD Risk | High (if ungrounded) | Low (controlled discharge) | High (charge buildup) |
Typical Use | Grounding, shielding | ESD protection, packaging, apparel | Electrical insulation |
Dissipative materials are more than just a line of defense—they are a critical component of modern ESD protection strategies. By allowing static charges to dissipate safely, they preserve product quality, protect workers, and ensure compliance with stringent safety standards. Whether used in a cleanroom, a PCB manufacturing facility, or an electronics warehouse, dissipative materials keep processes flowing—and sparks at bay.