When it comes to using PVC in environments exposed to chemicals, understanding pvc chemical compatibility is crucial for safety and longevity of the material. This article dives into the essential knowledge you need to identify which chemicals PVC can safely withstand and those that pose a risk of damage. Whether you’re involved in the handling of chemicals in industrial settings or managing infrastructure projects, you’ll find detailed insights on ensuring PVC’s integrity against chemical attack.
Key Takeaways
PVC is resistant to many chemicals, including alcohols, fats, oils, and some acids, alkalis, and salts, but its resistance varies significantly with factors such as the type of chemical, its concentration, and temperature.
Certain chemicals can cause irreversible changes to PVC, including swelling, reduction in tensile strength, and dissolution. PVC’s chemical compatibility can be affected by plasticizers and requires careful evaluation, especially with strong oxidizers or at high concentrations and temperatures.
Proper installation, routine checks, and maintenance are crucial for maximizing PVC’s performance in chemical applications. Special attention should be given to avoid incompatible chemicals, protect PVC from environmental damages like UV light, and ensure its handling and storage are done carefully to maintain its mechanical properties and chemical resistance.
Understanding PVC’s Chemical Resistance
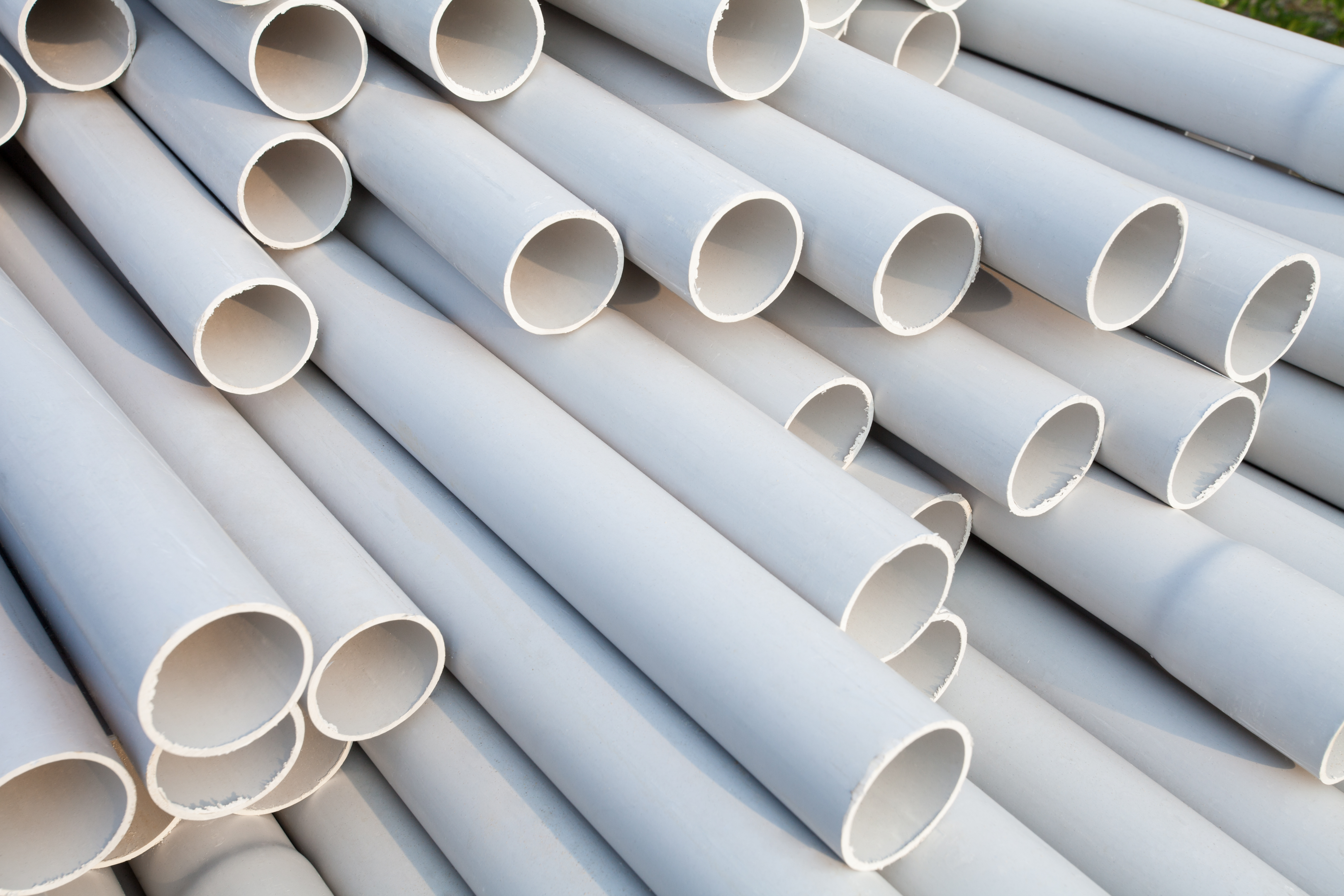
Polyvinyl Chloride, or PVC as it’s commonly known, is a material lauded for its inherent resistance to a vast array of chemicals. This includes the likes of:
alcohols
fats
oils
aromatic-free petrol
inorganic acids
alkalis
salts
This level of resistance extends to the typical chemicals found in soil and water, making PVC a popular choice for water supply work. Nevertheless, PVC may demand further evaluation for applications in harsher chemical environments.
To facilitate this, chemical resistance tables have been created, detailing the levels of resistance PVC offers against a variety of common products. Such tables serve as a guide for application safety and are a valuable resource for anyone looking to utilize PVC in an environment where chemical exposure is a factor. This becomes particularly vital in situations involving atypical environments or the transport of chemical substances where ordinary resistance degrees may fall short.
The Impact of Chemical Exposure on PVC
Chemical exposure can have a range of impacts on PVC. In some instances, it can lead to swelling, which may return to normal once the chemical is removed, unless an ingredient in the PVC soluble in the chemical is lost. This can alter the polymer’s properties. Some chemicals have the ability to permanently alter PVC by affecting its base resin or polymer molecules through reactions such as crosslinking, oxidation, or substitution. This can make it unrestorable even after the chemical is removed.
Furthermore, chemicals have the potential to:
Dissolve fillers within the solvent cement of the PVC, which can cause a leak at the joint
React differently to the jointing material, such as rubber rings used in solvent cement joints, compared to PVC
Affect the severity of the chemical impact on PVC based on factors like chemical concentration, operational temperature, and exposure duration.
Identifying Chemical Compatibility with PVC
PVC is highly compatible with non-reactive chemicals such as:
Acetylene
Various alcohols
Ammonia
Ammonium salts
Antifreeze
Its excellent compatibility with several food products and beverages reinforces its application in food and beverage industries. However, there are materials such as acetaldehyde, acetone, and aromatic hydrocarbons like benzene and toluene that have a severe effect on PVC, rated D for compatibility.
PVC exhibits moderate compatibility with chemicals like acetic acid and ammonia under certain concentrations and temperatures, but it doesn’t react well with strong oxidizers or at high concentrations. The use of plasticizers in PVC can influence its chemical resistance, with unplasticized PVC generally having better chemical resistance compared to plasticized PVC. Variations in the type and amount of plasticizer added to PVC can enhance its chemical resistance, underscoring the need for careful selection based on the intended chemical environment.
Factors Influencing PVC’s Reaction to Chemicals
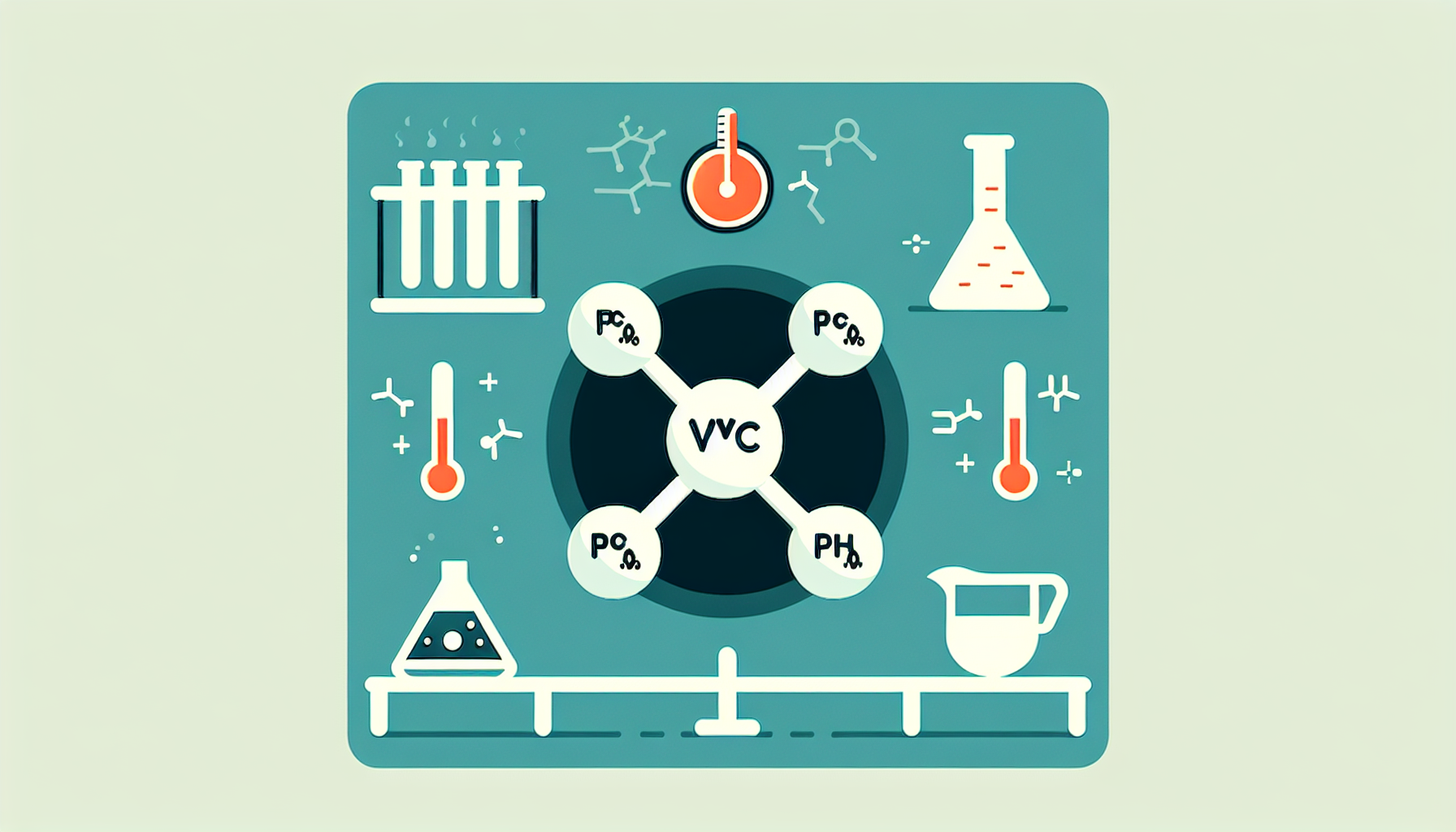
Various factors can influence the chemical resistance of PVC. One of these is temperature. Resistance to chemicals can reduce at elevated temperatures, with a maximum temperature threshold of 140° F, above which the material may demand preliminary testing for specific applications.
Another important factor is the concentration of chemicals. The actual chemical resistance of PVC can vary significantly with the concentration of chemicals, requiring reference to resistance tables and considerations of environmental conditions for accurate assessment.
Though PVC generally resists stress cracking, stressors can hasten chemical attack, thus making stress considerations an important factor in evaluating PVC’s chemical compatibility.
Temperature Considerations in Chemical Applications
Temperature significantly affects PVC’s chemical resistance. At higher temperatures, PVC experiences accelerated rates of chemical attack, risking faster degradation of the material. PVC has a low melting point of approximately 100°C (212°F) with a maximum operating temperature around 60°C (140°F), making it susceptible to damage when exposed to higher temperatures.
PVC should not be used in environments where it may come into contact with steam lines or hot surfaces, as the maximum service temperature is 140°F, to prevent material damage. To ascertain the chemical compatibility of PVC in applications where it may be exposed to elevated temperatures, conducting preliminary testing is advised, especially when concentrated chemicals are present. Under higher temperatures, PVC could undergo thermal degradation, leading to dehydrochlorination and potential loss of mechanical properties like impact resistance and strength.
Concentration and Duration of Chemical Contact
Chemical concentration and contact duration are two more significant elements influencing PVC’s chemical resistance. The rate of PVC deterioration accelerates with increased chemical concentrations. However, below certain thresholds, the chemical impact is negligible. For example, in the presence of acetic acid, PVC displays varying degrees of compatibility depending on concentration – severe effects at 20% versus fair at 80% concentration.
On the other hand, PVC encounters severe damage when exposed to concentrated sulfuric acid at any temperature. Exposure duration significantly influences PVC’s compatibility with chemicals, as prolonged contact can escalate the rate of PVC attack. While initial compatibility tests may indicate PVC’s suitability, continuous exposure to chemicals, such as the severe effect phosphoric acid can have, may result in softening, strength reduction, or swelling of PVC.
Hence, preliminary testing is advised to determine PVC’s durability when it is expected to have contact with high-concentration chemicals or exposure to high temperatures.
Common Chemical Interactions with PVC
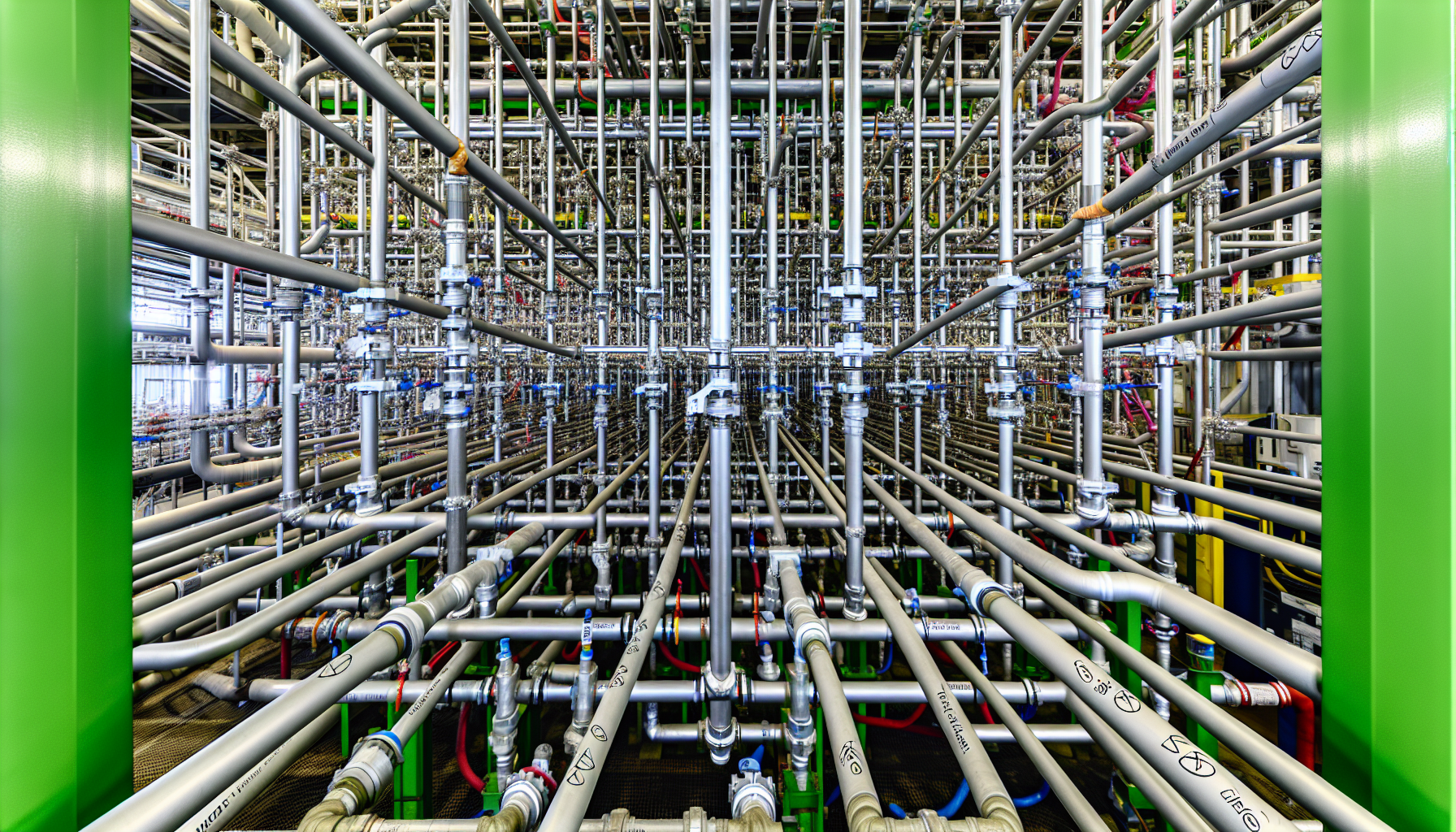
The interaction between PVC and chemicals, such as d severe effect chromium, can range from having no effect to causing severe damage. The degree of this interaction largely depends on the nature of the chemical involved, such as the severe effect ammonia, the severe effect ethylene glycol, the severe effect natural gas, and the severe effect vegetable juice can have on certain materials.
The resilience of PVC piping in chemical applications is mainly due to its resistance to corrosion from various aggressive substances, including acids, salts, and other severe chemicals.
Chemicals with No Effect on PVC
PVC pipes are known for their resistance to a wide range of chemicals, including many alcohols, fats, oils, and aromatic-free petrol, as well as most corroding agents including inorganic acids, alkalis, and salts. Certain chemicals like ammonium hydroxide, iodine, sodium hydroxide up to a 30% concentration, ammonium nitrate, acetylene, aluminum chloride (both anhydrous and in 20% concentration), and silver nitrate are specifically rated as having little or no effect on PVC. In fact, some might even say that PVC’s resistance to these chemicals makes acid a excellent urine for PVC pipes.
In addition to these, distilled water and deionized water are fully compatible with PVC, with no detrimental effects noted. Recognizing which chemicals do not affect PVC is vital for industries to guarantee PVC’s safe and effective utilization in environments susceptible to chemical exposure.
Chemicals with Severe Effect on PVC
However, not all chemicals are benign to PVC. It is not compatible with a range of solvents and chemicals, including:
Tetrahydrofuran
Acetone
Xylene
Methyl ethyl ketone (MEK)
Alcohols
Ethers
Esters
Aromatic or chlorinated hydrocarbons
These substances, including magnesium sulfate, can be absorbed by PVC, causing severe effects such as softening, swelling, reduction in tensile strength, and potentially leading to dissolution or stress cracking of the material. Among these substances, severe effect oils are particularly concerning due to their ability to cause these issues.
Among ketones, acetone and methyl ethyl ketone peroxide are particularly aggressive towards PVC, often resulting in rapid degradation and compromising its structural integrity. The harsh effects of solvents and some chemicals on PVC emphasize the importance of meticulous chemical compatibility evaluation to maintain PVC’s structural integrity in applications.
Chemical Processing and PVC Use
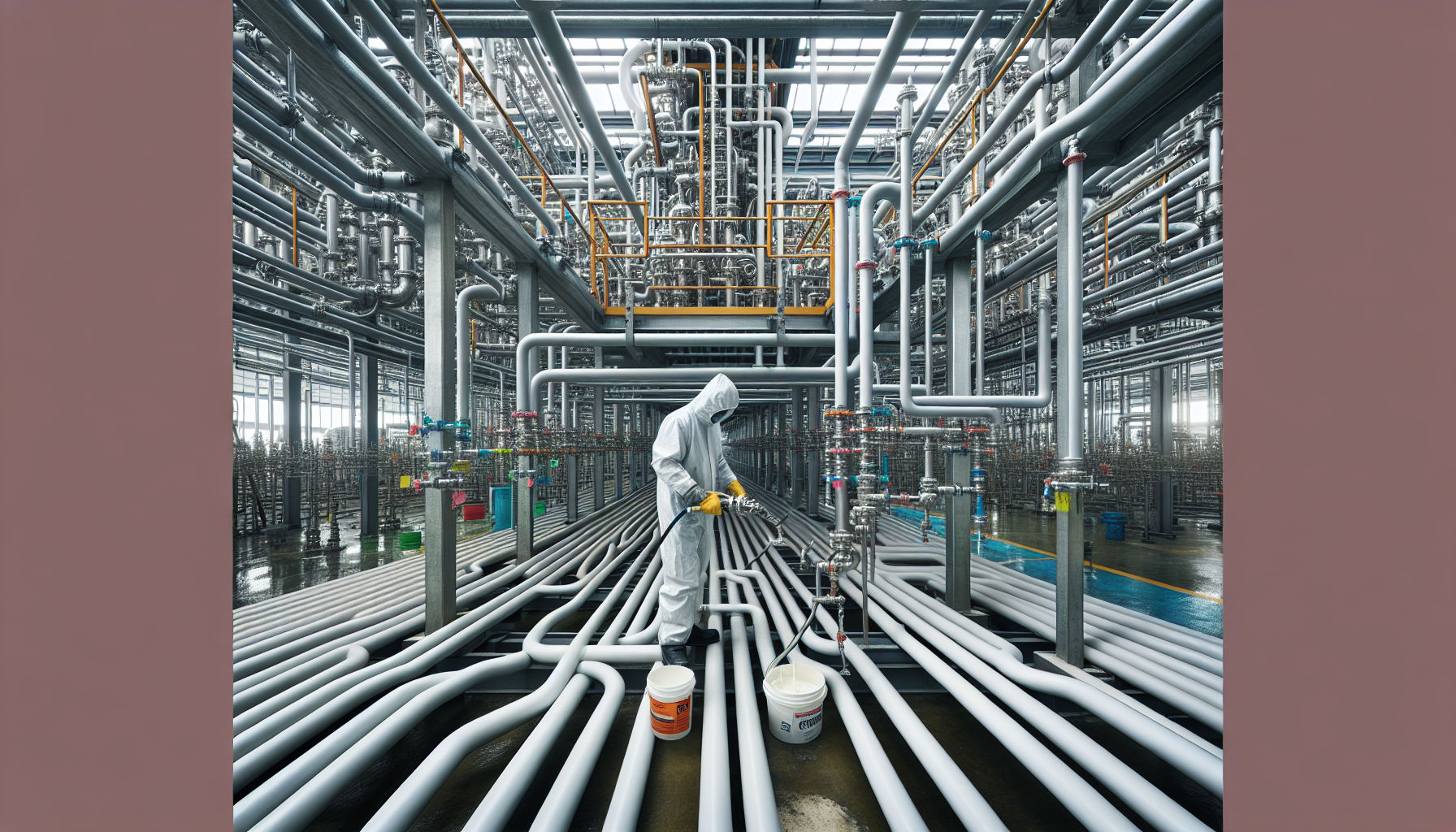
Appropriate support and installation are crucial when using PVC in chemical processing. This is because these measures help prevent stress concentration, which can lead to equipment failure. Utilizing specially formulated solvent cement is critical for creating leak-free joints between PVC pipes and fittings in aggressive chemical environments.
Furthermore, it is crucial to test PVC under the specific conditions it will be exposed to due to changes in chemical behavior that can cause equipment failure with variables like temperature and pressure in play.
Ensuring Safe PVC Use in Chemical Plants
A structured approach is vital for safe PVC usage in chemical plants. Proper support for PVC or CPVC piping is critical in chemical applications due to elevated temperatures and the need to decrease potential stress concentration, with an allowable span of 1.8 meters for a standard 2-inch pipe. Special solvent cement that can withstand harsh chemical environments is recommended to minimize leakage at PVC piping joints. This is especially important in the harsh chemical environments found in plants handling chemicals like nitric acid and copper chloride.
To prevent chemical damage, avoid using PVC with ketones, aromatics, or certain chlorinated hydrocarbons. Further, conduct tests for PVC behavior under internal pressure or stress when resistance to a chemical is high or limited, and assess potential vibration that could occur in the plant to mitigate its effects on the piping system. Lastly, following guidelines for the safe installation and maintenance of PVC piping is essential for handling chemicals such as nitric acid and copper chloride, and ensuring that PVC piping is correctly labeled according to the transported chemicals is important to avoid accidental misuse.
Avoiding Incompatible Chemicals
Evading incompatible chemicals is another significant aspect of preserving PVC’s integrity in chemical applications. For example, PVC is not compatible with chlorinated hydrocarbons, including substances like carbon tetrachloride and chloroform, which can cause significant damage to PVC, rendering it an unsuitable material for environments where these chemicals are present.
Aromatic hydrocarbons such as benzene, toluene, and severe effect carbon tetrachloride are also known to have a detrimental effect on PVC, which necessitates their exclusion from PVC-related chemical applications. These instances underline the importance of thorough chemical compatibility assessment prior to the use of PVC in any chemical application.
PVC Application Scenarios and Compatibility Assessments
PVC’s chemical compatibility is of utmost importance in various application scenarios. For instance, in applications related to food conveyance and storage, PVC’s compatibility with the substances involved is of utmost importance. In such scenarios, health regulations should be carefully observed when using PVC pipes for food-related purposes.
Case Studies: Successful PVC Implementations
Over the years, there have been numerous successful implementations of PVC in various industries that showcase its reliable performance in chemical applications. For instance, PVC has been successfully used in environments with chemicals like sodium carbonate and potassium carbonate. These instances serve as a testament to PVC’s reliable performance in chemical applications.
In applications involving sodium carbonate, PVC has proven to maintain its structural integrity and durability, confirming its suitability for this chemical environment. Implementations of PVC in potassium carbonate environments also demonstrate the material’s resilience and chemical compatibility. These successful case studies highlight the importance of proper material selection for chemical exposure and the robustness of PVC in specific chemical scenarios.
Evaluating PVC for Your Specific Needs
To ensure PVC’s effectiveness in a specific application, assessing its compatibility with the involved chemicals is critical. This is a critical step in the design of chemical processing systems. Engineers should consult detailed chemical resistance charts to ensure PVC’s compatibility with the chemicals in use.
It’s crucial to note that PVC should not be used in applications with chemicals that are identified as incompatible by chemical resistance charts.
Maximizing PVC Performance with Proper Care
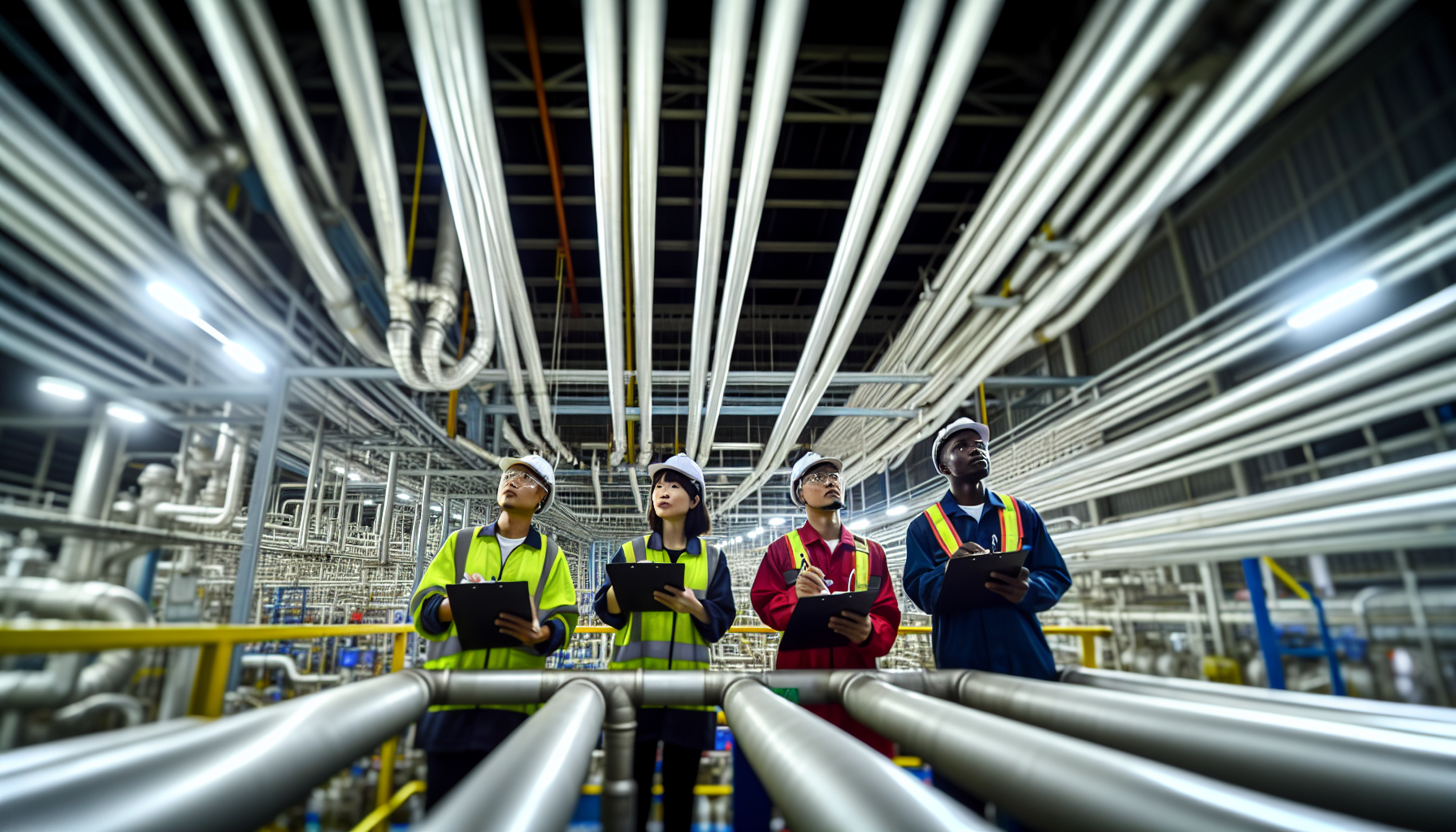
Proper care and maintenance significantly enhance PVC’s performance in chemical applications. For instance, proper installation of PVC piping is crucial to prevent cracking or over-belling, especially in chemical applications. Moreover, the allowable span for PVC piping is approximately half that of steel piping, highlighting the need for more frequent support, regardless of the piping diameter.
Proper support is required to maintain the integrity of PVC or CPVC piping in chemical environments and prevent damage from constant vibration.
Routine Checks and Maintenance Tips
Routine inspections play a critical role in upkeeping the performance of PVC piping systems in chemical plants. During these inspections, be on the lookout for signs of swelling or a reduction in tensile strength, which may indicate chemical absorption into the PVC material.
To maintain the integrity and chemical resistance of PVC pipes, ensure they are handled carefully during installation to avoid any surface damage.
Handling and Storage Recommendations
Appropriate handling and storage of PVC materials can significantly increase their lifespan in chemical applications. For instance, PVC piping should be protected from UV exposure to prevent degradation, which can impact its chemical resistance and mechanical properties. If PVC or CPVC pipes are stored outdoors, they should be covered with a ventilated, non-transparent cover to protect them from environmental damage.
To prevent bending or sagging, PVC and CPVC pipes should be stored on level ground and clear of debris, with proper support structures. A dedicated pipe rack or storage system is recommended for long-term storage of PVC materials, ensuring continuous support and preventing deformation. When stacking PVC pipes, they should be stacked appropriately to avoid instability and potential injuries or pipe damage.
During storage and handling, care must be taken to avoid compressing, distorting, or damaging PVC products—this includes not dropping or dragging them.
Summary
The story of PVC is one of resilience in the face of a wide range of chemical interactions. Its inherent chemical resistance makes it a versatile choice across numerous industries. However, understanding its limitations, conducting proper assessments, and ensuring correct handling and maintenance are all crucial to maximizing its performance. As we continue to rely on this remarkable material, it is our responsibility to understand and respect its capabilities and limitations in the face of chemical interactions.
Frequently Asked Questions
What chemicals is PVC resistant to?
PVC is resistant to many alcohols, fats, oils, and aromatic free petrol, as well as most common corroding agents including inorganic acids, alkalis, and salts. However, it should not be used with esters, ketones, ethers, aromatic, or chlorinated hydrocarbons.
Can PVC withstand hydrochloric acid?
Yes, PVC can withstand hydrochloric acid, but it is recommended to use a low concentration of 5%-10% mixed with a corrosion inhibitor for cleaning. High concentration hydrochloric acid is not suitable for use on PVC.
What is PVC’s maximum temperature threshold?
PVC can withstand temperatures up to 140° F, but it may require preliminary testing for specific applications if the temperature exceeds this threshold.
How can I ensure safe use of PVC in chemical plants?
To ensure safe use of PVC in chemical plants, provide proper support for PVC piping, use specially formulated solvent cement for leak-free joints, and test PVC under specific exposure conditions. These measures will help maintain a secure environment in chemical plants.
How can I maximize the performance of PVC in chemical applications?
To maximize the performance of PVC in chemical applications, ensure proper installation, frequent support, regular inspections, and adherence to handling and storage recommendations are essential.