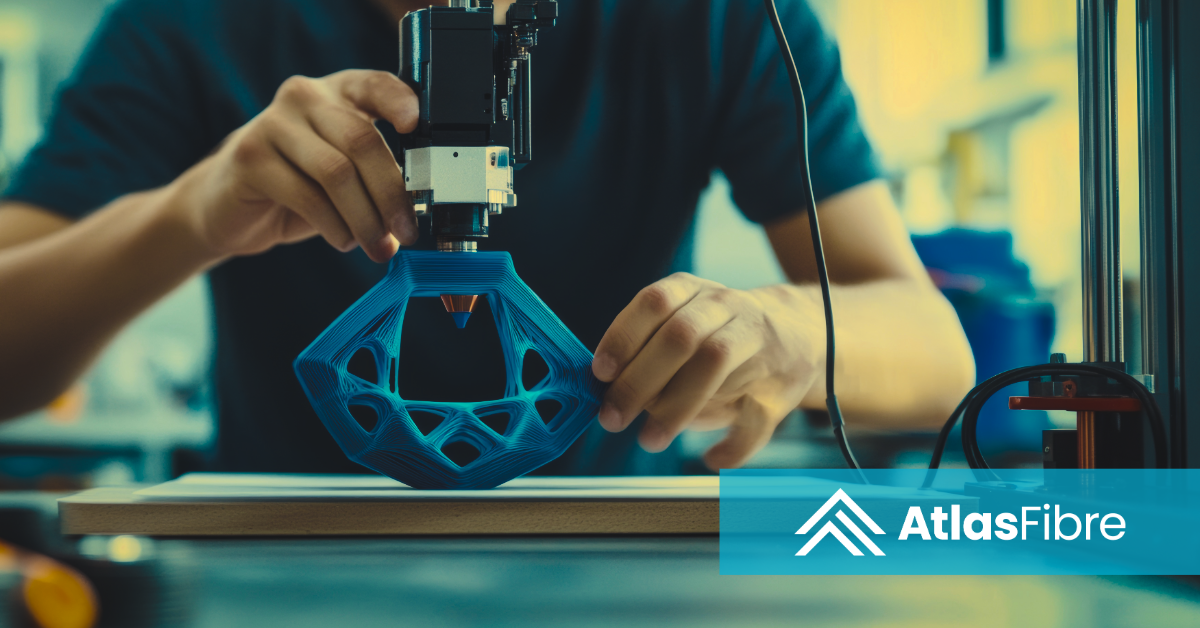
So you’ve made a killer prototype. Maybe it’s a gadget that solves a real-world problem, or a part that pushes performance to the next level. But here’s the cold truth: a prototype that looks good on your workbench doesn’t always mean it’s ready for the real world of factories, supply chains, and mass production.
The secret? Follow the same playbook used by smart manufacturers to turn bright ideas into rock-solid, manufacturable products — without blowing your budget or timeline.
Keep It Simple: Design for Manufacturability
Rule number one: don’t overcomplicate things. Great design doesn’t mean fancy — it means functional and practical.
Fewer Parts, Fewer Problems: Every bolt, bracket, or tight tolerance adds time, cost, and potential headaches. If you don’t need it, lose it.
Go Standard: Reach for off-the-shelf components whenever you can. Standard parts mean faster sourcing and lower costs — no need to reinvent the wheel.
Document Everything: Don’t let design details live only in your head (or on a napkin sketch). Clear drawings and a bulletproof bill of materials keep your team, suppliers, and partners on the same page.
Prototype Early, Test Often
You can’t fix what you don’t test. Modern methods like 3D printing and CNC machining let you build and tweak physical prototypes fast.
Iterate Like Crazy: Each new version should bring you closer to a design that’s easy to build, assemble, and deliver — not just one that works in the lab.
Small Batches, Big Payoffs: Before you spend big on production tooling, run small pilot batches. They’ll reveal hidden flaws that could sink a full-scale rollout.
Listen to the Market: Prototypes aren’t just for your shop floor — get them into users’ hands. Early feedback can save you from costly redesigns later.
Never Compromise on Quality
Scaling up is where quality can slip through the cracks — unless you plan for it from day one.
Set the Bar High: Define clear, measurable standards for performance, durability, and safety.
Control, Control, Control: Use proven methods like Six Sigma and Statistical Process Control (SPC) to catch defects before they ship.
Stay Vigilant: A good process today might need fine-tuning tomorrow. Regular audits and data reviews help you adapt and improve.
Build for Scale — But Stay Flexible
You want a setup that can crank out ten units or ten thousand — without blowing up your costs or your sanity.
Flexible Production Lines: Design workflows that can expand or shrink as demand shifts.
Automate Where It Counts: Robotics and smart tech aren’t just for mega-factories anymore — they’re how small players stay competitive.
Bulletproof Supply Chains: Work with suppliers you trust. And always have a Plan B if your main source dries up.
Keep an Eye on the Bottom Line
A design that’s easy to manufacture but too expensive to sell won’t survive.
Smart Materials: Pick materials that balance performance, availability, and cost. Sometimes, the “good enough” option beats the exotic one.
Lean and Mean: Simplify your assembly process, reduce waste, and adopt lean manufacturing principles to keep costs down.
Team Up to Save: Bring your designers, engineers, and buyers together to spot hidden savings across the entire product lifecycle.
Don’t Get Caught by Compliance
Nothing halts production like a surprise certification roadblock.
Know the Rules: Research safety, environmental, or industry-specific certifications early.
Keep Records Clean: Detailed documentation of your materials and testing will save you headaches when auditors come knocking.
Train Your People, Win for Life
Even the best design and best machines need smart humans to run them.
Invest in Your Team: Train workers on new tech, evolving standards, and better ways to do the job.
Listen Up: Your people on the shop floor often spot problems first — give them the power to speak up and fix issues fast.
Ready to Build?
Taking a prototype to full production isn’t rocket science — but it is a science. Apply these strategies and you’ll avoid costly mistakes, deliver quality products, and get your big idea into the hands of the people who need it.
Because in the end, a prototype no one can build is just a paperweight.