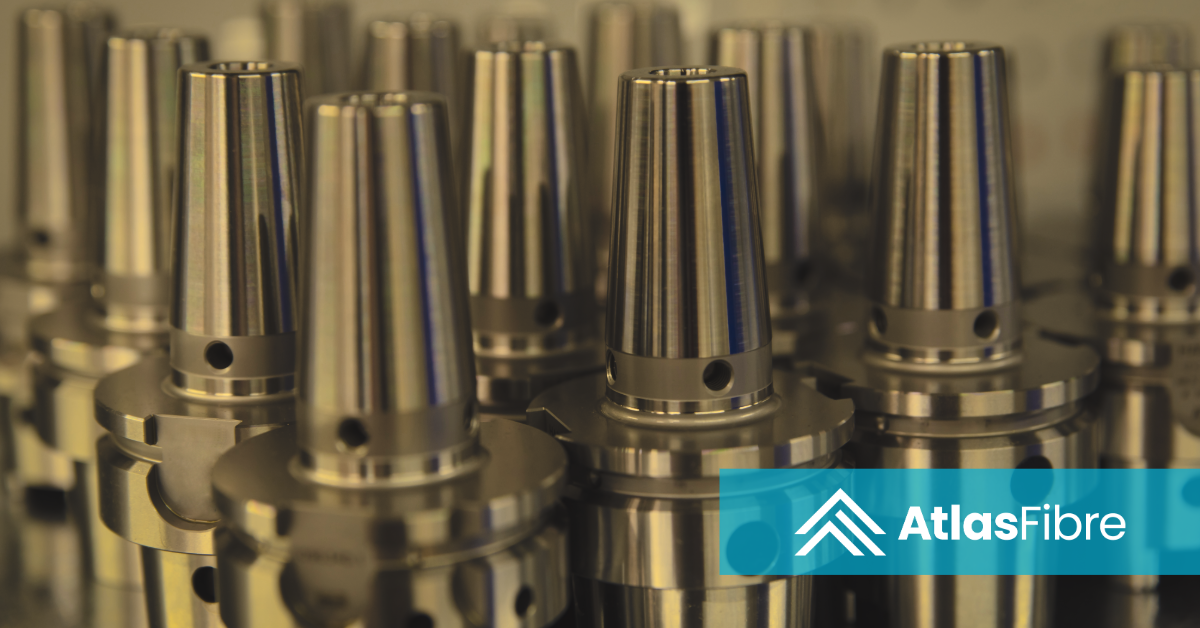
When you’re shaping tough, high-performance composite materials, the difference between a rough mess and a flawless finish often comes down to one hidden detail: tool balancing. You wouldn’t drive your sports car with the wheels out of balance, right? The same idea holds true when you’re spinning a tool at 20,000 RPM or higher — especially when dealing with composites that can’t afford the slightest wobble.
Here’s how to keep your tools dialed in, your vibration down, and your workpieces pristine.
Why Balancing Matters More with Composites
Composites are amazing — strong, lightweight, and engineered for extreme performance. But they’re also abrasive and surprisingly sensitive to vibration. Even minor imbalance in your tool can mean chipping, delamination, or fiber pull-out, leading to poor surface finishes or scrapped parts. So when you’re machining carbon fiber, glass-filled polymers, or any high-end laminate, proper balance isn’t optional — it’s your secret weapon.
Start With a Balanced Tool Assembly
First rule: balance the entire assembly — not just the cutter. That means the tool holder, cutting tool, retention knob, and any adapters should all be tuned to spin in harmony at your operating spindle speed. High-speed spindles above 20,000 RPM demand near-perfect balance.
Hydraulic chucks are a go-to here. They clamp evenly, reduce run-out, and help keep the tool from pulling out mid-cut — something you definitely don’t want when your expensive composite sheet is on the table.
Three Proven Ways to Get That Perfect Spin
Balance doesn’t happen by accident. Here’s how the pros fine-tune their setups:
Balancing Rings: Think of these like adjustable counterweights for your tool holder. Dial them in until you find that sweet spot.
Add or Remove Weights: Some tool holders have spots for set screws or plugs. Add or pull weights where needed to cancel out imbalance.
Material Removal: For stubborn cases, carefully mill or drill tiny amounts of material from the tool holder — but always keep structural integrity in mind.
Measure Twice, Cut Once (and Balance Again)
How do you know when you’ve nailed it? Sensors. Vibration sensors, accelerometers, or laser displacement tools can pick up the tiniest imbalance. Make adjustments, re-measure, and repeat until your tool spins like a dream.
Rigidity is King
Composites punish vibration. A rigid setup means less chance for chatter, delamination, or tool wear. That goes for your entire setup: machine, tool holder, workholding, and workpiece clamping. Secure everything like it’s a race car on a dynamometer.
Keep It Sharp and Stay Ahead
Regular inspection is your friend. Tool holders wear out, retention knobs get battered, and a tiny nick can throw balance out the window. Sharpen your cutters often — dull edges vibrate more and chew up composite layers.
And if you hit a head-scratcher, call in reinforcements. Your tool providers can help you spec the best balancing strategy for a tricky composite application.
Balanced Tools, Better Parts, Longer Life
At the end of the day, investing a little extra time in proper tool balancing pays off big: smoother finishes, fewer scrap parts, longer tool life, and a spindle that’s not working overtime to fight unnecessary vibration.
So next time you fire up the CNC to tackle that aerospace-grade carbon fiber, remember — perfect balance isn’t just for ballerinas. It’s the hidden hero of every great composite cut.