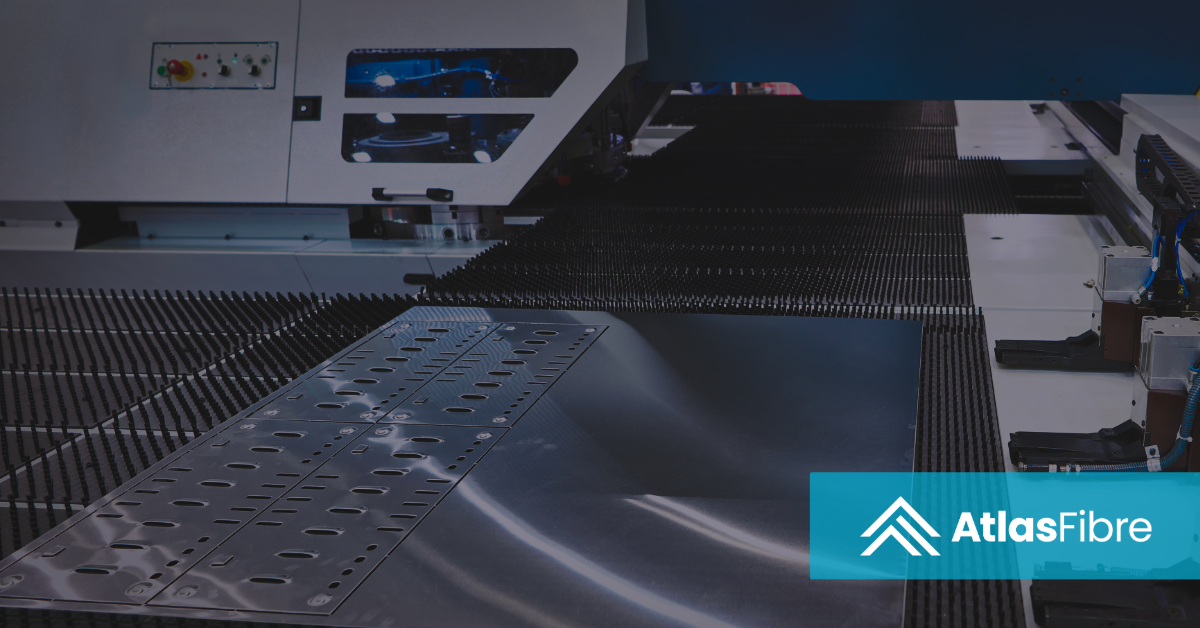
Every year, millions of parts are stamped out of thermoset laminates — and it’s easy to see why. Punching (or die cutting) remains the most cost-effective method for producing high volumes of flat, consistent parts with tight tolerances. But success with punched laminates isn’t just about choosing the cheapest method — it’s about matching the right material, tooling, and process to your application.
Discover which laminate grades work best for punching, how to maximize part quality and minimize waste, tips for die design and press tonnage, and insights on how our team helps yours get it right the first time and every time after.
Why Punching Works for Industrial Laminates
When you need thousands or even millions of identical parts — think washers, gaskets, electrical insulators, or custom flat profiles — punching is unbeatable for speed, consistency, and cost per piece.
But what really makes punching shine is pairing it with thermoset laminate materials. Thermosets like phenolics, epoxies, melamines, and vulcanized fibre bring unique benefits to demanding industrial applications. These materials don’t just handle heat and electricity — they excel at retaining their mechanical strength and dimensional stability under stress.
Unlike metals or thermoplastics, thermoset laminates don’t soften when reheated; they maintain their structural integrity, which is ideal for parts that need to hold shape under high temperatures or electrical loads. And because thermoset laminates are typically produced in sheet form, they’re a perfect fit for flat-part punching — enabling manufacturers to turn raw sheet stock into thousands of identical parts with minimal waste, minimal tooling wear, and maximum repeatability.
This synergy — precision punching paired with the robust performance of thermoset laminates — is why industries from aerospace to electrical power trust this method to deliver parts that protect systems, insulate components, and keep operations running smoothly.
Materials Matter: Choosing the Right NEMA-grade Composite
Different thermoset laminate grades behave differently when punched because of their base reinforcement, resin system, and bond strength. Softer grades like vulcanized fibre or paper phenolics shear cleanly and easily, while glass cloth laminates are tougher but more prone to edge chipping — requiring careful die design and sometimes preheating to ensure a clean cut.
So what’s the ideal advanced material for your punching project? Explore some of the composite laminates offered by Atlas Fibre along with guidance on their suitability for punching.
- XXXP Phenolic: The gold standard for close-tolerance punched parts. Requires preheating for clean results. (See Atlas Fibre XX or XXX)
- XPC: Great for washers up to .031” thick. Minimal edge cleanup needed.
- Vulcanized Fibre: Highly versatile, easily punched or steel-rule die cut.
- FR2 & FR3: Punchable but watch for edge cavitation.
- FR4, G10, G11: Possible, but some chipping at edges begins above .032” thick.
- G7: Too hard and brittle — best to machine instead.
Keep in mind that phenolic laminates often require preheating to prevent cracks. And once preheated, they can’t be reheated — post-baking increases hardness, making punching more difficult.
How Much Press Tonnage Do You Need?
Determining the right press tonnage is essential for clean, efficient punching.
To estimate the required tonnage, you can use a simple calculation: multiply the perimeter of the part by its thickness and then by a material-specific factor. For example:
- Vulcanized fibre and phenolic laminates typically require about 7 to 10 tons per square inch
- Glass epoxy laminates like G10 need around 10 to 15 tons per square inch
- Glass melamine grades, such as G5, are harder and may demand 15 to 20 tons per square inch.
Punching brittle materials can create sharp peak loads and sudden breakthroughs, so it’s good practice to size your press up to 50 percent higher than the calculated requirement. This approach, established by industry testing as far back as the 1960s, is still considered a best practice today for ensuring consistent, high-quality parts.
To estimate the punch power required for NEMA materials like phenolics and glass epoxies, try out Atlas Fibre’s Punch Tonnage Calculator.
The Next Step in Precision Punching
Punching remains one of the most efficient ways to produce high volumes of flat, precise parts — and thermoset laminates make it possible to do so with exceptional strength, stability, and performance. By understanding how different laminate grades behave during punching, and by designing the right tooling and press setup, you can get clean edges, tight tolerances, and repeatable results that keep your operations running smoothly.
Whether you need simple washers or complex insulation profiles, our team is here to help you choose the right material, optimize your die design, and make sure every punched part meets your expectations. If you’d like to see how precision punching could work for your next project, we’d be glad to talk it through with you — no pressure, just practical advice to help you get the best results possible.