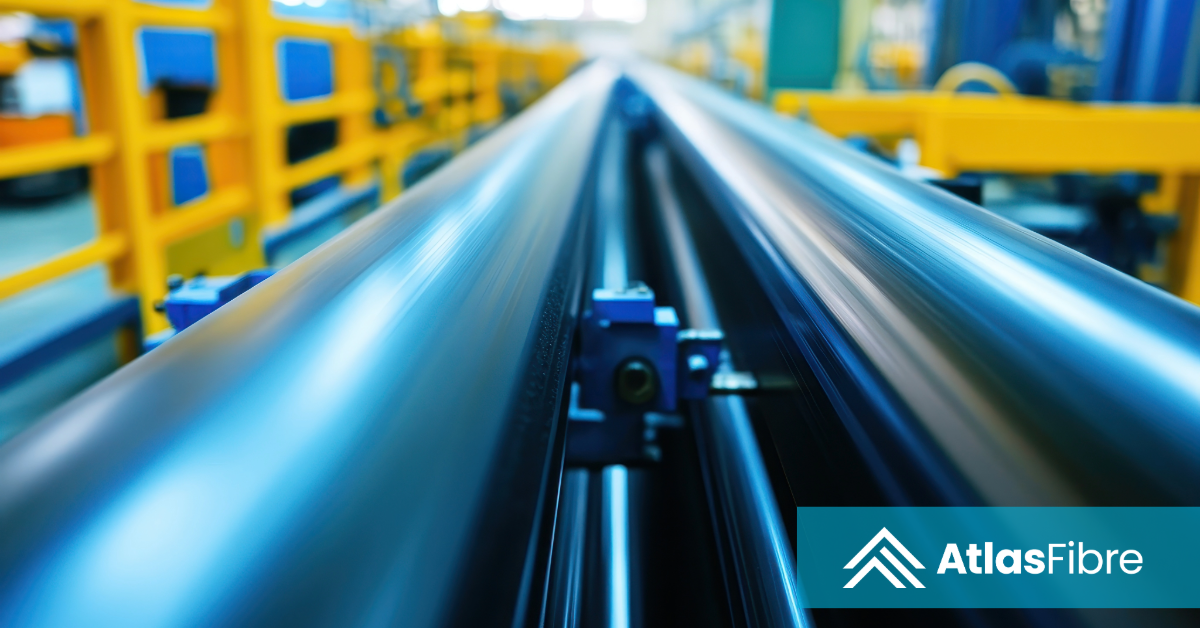
Thermoplastics can offer distinct advantages over thermoset composites in certain high-temperature environments, particularly when considering mechanical resilience, chemical stability, and processing flexibility. Explore a comparison below and connect with an Atlas Fibre material and machining specialist for more information and to discuss your project:
Key Advantages of Thermoplastics in High-Temperature Environments
Superior Impact and Fatigue Resistance
Thermoplastics like PEEK (polyether ether ketone) are less brittle than thermosets, enabling better resistance to mechanical stress, vibration, and thermal cycling. This ductility reduces cracking risks in applications like aerospace components or automotive under-hood parts exposed to fluctuating temperatures.
Higher Service Temperatures in Advanced Grades
While standard thermosets (e.g., epoxy) typically withstand temperatures up to 220°C (428°F), high-performance thermoplastics like PEEK or PEI (polyetherimide) can operate continuously at 260°C (500°F). This makes them suitable for extreme environments such as jet engine components or medical sterilization equipment.
Chemical Stability Under Heat
Thermoplastics maintain resistance to corrosive fluids and solvents even at elevated temperatures, critical for chemical processing or oil/gas applications. For example, PEEK resists hydrolysis and aggressive chemicals better than many thermosets when heated.
Ease of Repair and Recyclability
Unlike irreversible thermosets, thermoplastics can be remelted and reshaped without degrading their properties. This allows for cost-effective repairs or recycling of high-temperature parts, reducing waste in industries like energy or manufacturing.
Thermal Cycling Performance
Thermoplastics’ ability to expand and contract without losing structural integrity makes them ideal for applications with frequent temperature shifts, such as electronic housings or battery components in electric vehicles.
Comparison Table: Thermosets vs. Thermoplastics in High Heat
Property | Thermosets | Thermoplastics |
---|---|---|
Max Service Temperature | Up to 220°C (epoxy) | Up to 260°C (PEEK) |
Impact Resistance | Lower (brittle) | Higher (ductile) |
Chemical Resistance | Good, but degrades over time | Excellent under heat |
Recyclability | Not recyclable | Fully recyclable |
Thermal Cycling | Prone to microcracking | Resilient to expansion |
Applications Leveraging Thermoplastic Advantages
- Aerospace: PEEK fasteners and brackets in jet engines (high heat + vibration resistance).
- Medical: Autoclavable surgical tools (sterilization at 260°C).
- Energy: Seals and valves in geothermal systems (thermal cycling + chemical exposure).
While thermosets excel in static, ultra-high-heat scenarios (e.g., electrical insulation), thermoplastics are preferred for dynamic, chemically aggressive, or recyclable high-temperature solutions.