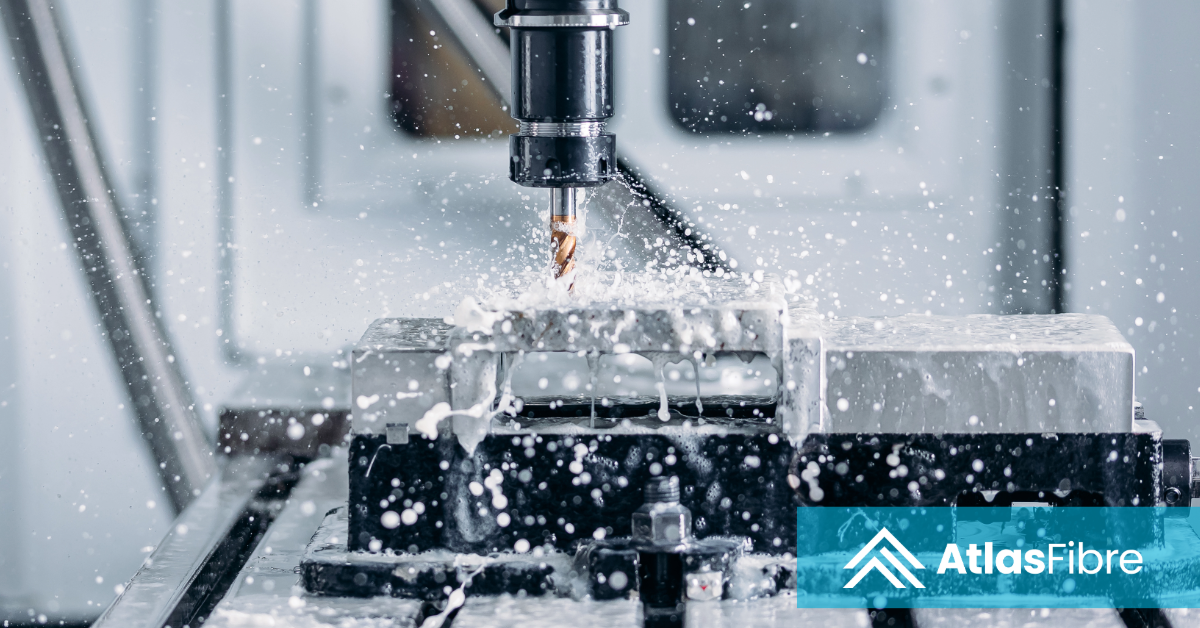
Why Material Stability Matters in Multi-Component Assemblies
When a jetliner crosses the sky, every bolt, bracket, and panel must fit together perfectly. Miss by a few thousandths of an inch, and the consequences can be catastrophic—or at the very least, expensive.
For companies designing high-precision assemblies, “tolerance stack-up”—the way tiny manufacturing variations pile up—can quietly turn into a full-blown quality risk.
And if you’re not thinking about how material stability plays into that equation, you could be setting your product up for failure before the first part even ships.
The Hidden Risk: Tiny Errors, Big Problems
In any assembly, each dimension comes with a tolerance: a little wiggle room to account for manufacturing variation. No single deviation is a problem. But add a dozen parts together, each nudging a fraction of a millimeter off course, and suddenly that perfect design no longer fits, functions, or flies the way it should.
That’s tolerance stack-up.
In metals, where dimensional stability is high, the effects can be predictable. But thermoplastics—and, to a lesser degree, even thermoset composites—respond differently to the world around them. Moisture absorption, heat expansion, even time itself can cause slight shifts. And when those shifts accumulate across multiple components, things can get ugly fast.
Not All Materials Handle the Real World the Same
When engineers think about stack-up, they often assume material behavior will stay constant from CAD model to field deployment. Reality disagrees.
Material | Dimensional Stability | Key Risks |
---|---|---|
Metals (e.g., Aluminum, Steel) | Very high | Minimal thermal expansion, predictable behavior |
Thermoplastics (e.g., Nylon, PEEK) | Low | High moisture absorption, high thermal expansion |
Thermoset Composites (e.g., G10/FR4, Phenolics) | Moderate to high | Good stability, but sensitive to environment compared to metals |
Thermoset composites sit in a sweet spot: far more dimensionally stable than thermoplastics, but still not quite the rock-solid performers that metals can be. Environmental changes—like factory floor humidity swings or thermal cycling during operation—can still induce slight movements in composite parts.
In the wrong design, those movements can push a once-functional assembly out of spec.
The Real-World Difference: Choosing the Right Material
A leading electronics manufacturer once faced an unexpected issue: circuit board enclosures, initially machined from thermoplastics, warped just enough in humid conditions to cause board stress and connection failures.
Switching to a glass-reinforced thermoset composite with a lower moisture uptake rate immediately solved the problem—saving millions in recall costs and brand damage.
Similarly, a defense contractor found that thermoset composite panels held their flatness across desert-to-arctic deployments better than aluminum panels, which suffered minor expansion shifts that added up in sensitive optical housings.
Material choice isn’t just about strength or weight—it’s about stability over the lifetime of the product.
How Atlas Fibre Manages Tolerance Stack-Up
At Atlas Fibre, we take tolerance stack-up personally—because for the industries we serve, failure isn’t an option.
Here’s how we help control the risks:
- Flatness Control: We source and machine thermoset materials with tight flatness specifications to minimize dimensional shifts before fabrication even begins.
- Precision Machining: Our CNC systems are dialed in specifically for composites, accounting for thermal loads and material response.
- Environmentally Informed Fabrication: We machine and inspect in controlled environments to limit the effects of temperature and humidity.
- Spec-Driven Fabrication: Every machined component is built not just to drawing—but to real-world function, anticipating how assemblies behave under field conditions.
The result? Assemblies that fit right, function right, and stay right—long after they leave the shop floor.
The Takeaway
When it comes to precision assemblies, the devil is in the details—and the material.
Ignoring material stability is like stacking playing cards in a wind tunnel: you might get lucky for a while, but eventually, things fall apart.
Smart engineers think beyond the tolerance tables. They choose materials that stay true to form, machine them to spec, and partner with fabricators who understand that perfect drawings need perfect execution.
Because at the end of the day, it’s not just about making parts—it’s about making parts that last.