Thermoplastics are versatile materials essential in countless applications, from everyday items to advanced engineering. These polymers become moldable when heated and solidify upon cooling, which allows for recycling and reshaping. In this article, we unpack what thermoplastics are, explore their applications, and examine their sustainability, giving you a clear view of the role of thermoplastic materials in both current industries and future developments.
Key Takeaways
Thermoplastics, which soften when heated and harden when cooled, are widely used across various industries due to their ability to be shaped and reshaped multiple times without losing their chemical properties.
Common types of thermoplastics, such as Polyethylene (PE), Polypropylene (PP), and Polyvinyl Chloride (PVC), possess unique properties making them suitable for a range of applications, from packaging to automotive parts, though they vary in their resistance to chemicals, heat, and degradation.
Advancements in thermoplastic recycling and the development of biodegradable options are central to improving the sustainability of these materials, despite challenges in recycling efficiently and reducing environmental impact.
Exploring Thermoplastic Polymers
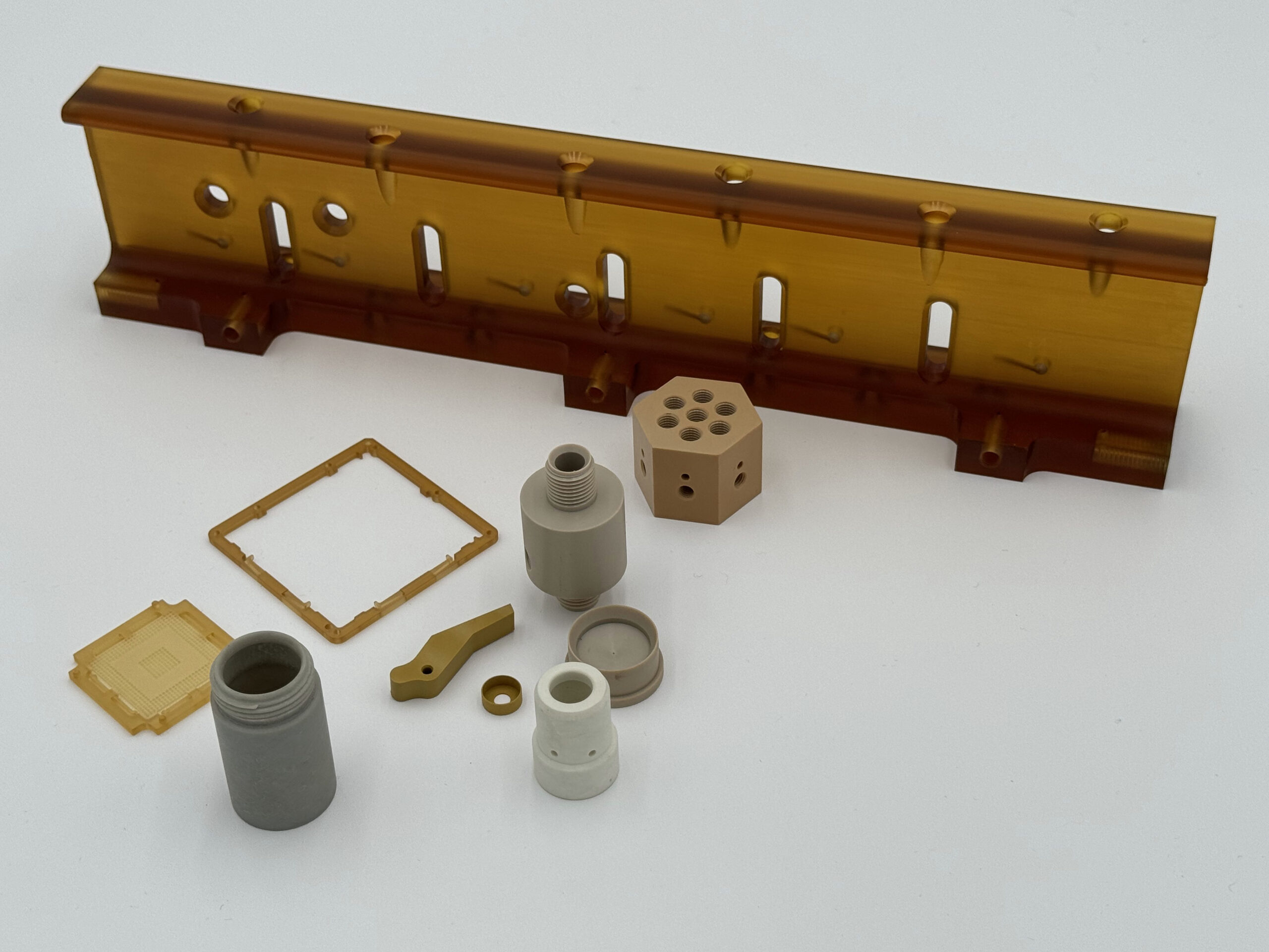
Thermoplastics, also known as thermoplastic polymers, are a unique variety of plastic that retains its chemical properties despite repeated heating and cooling. Unlike thermosetting polymers that form irreversible bonds during curing, a thermoplastic polymer uniquely softens upon heating and hardens when cooled. This unique characteristic allows thermoplastics to be shaped and reshaped multiple times, making them ideal for a wide range of applications.
Their potential for repeated processing and molding has fostered widespread use of thermoplastics across different industries. You’ll find them in everything from low-stress applications like plastic bags to high-stress engineering parts such as mechanical components. Their versatility, combined with their unique properties, makes them a key player in modern manufacturing and product design.
Amorphous and Semi-crystalline Thermoplastics
There are two primary categories of thermoplastic polymers: amorphous and semi-crystalline. Amorphous thermoplastics are like the rebels of the polymer world. They don’t follow a structured molecular arrangement and soften gradually over a range of temperatures, rather than having a distinct melting point. This randomness in their molecular structure also makes them more transparent compared to their semi-crystalline counterparts.
On the other hand, semi-crystalline thermoplastics are the conformists. They have an ordered molecular structure and transition from a solid to a liquid at a specific, sharp melting point. When semi crystalline thermoplastics melt, their orderly crystalline regions transition to a more random arrangement, much like an organized dance turning into a freestyle jam. Unlike their amorphous cousins, semi-crystalline thermoplastics don’t experience a phase change until they degrade.
Key Advantages of Thermoplastics
Thermoplastics play an understated yet pivotal role in contemporary product design. From food containers to car parts, these materials offer numerous advantages that make them a popular choice for manufacturers. First and foremost, thermoplastics are strong and lightweight, which makes them versatile for diverse uses. They’re also resistant to fatigue, meaning they can handle products that are subjected to repetitive use.
The ease of molding thermoplastics into intricate shapes with fine tolerances makes their manufacturing highly cost-effective. Traditional methods like injection molding and thermoforming utilize the easy processing characteristics of thermoplastics, which contribute to reduced production costs.
Other notable advantages include corrosion resistance, colorability, and the ability to strongly adhere to metals, which enhances their impact resistance in adhesion-required applications. Additionally, these materials are resistant to chemical attack.
Limitations and Challenges
However, thermoplastics, despite their numerous advantages, do present a unique set of challenges. One of them is creep, a phenomenon where thermoplastics can stretch and weaken when subjected to long-term stress loads. This is compounded by their lower melting temperatures, which can lead to deformation. Certain thermoplastics with low melting points can degrade or deform when used in applications involving high temperatures, limiting their suitability for these environments.
Some thermoplastics also exhibit poor resistance to various organic solvents, hydrocarbons, and polar solvents, which can compromise their structural integrity. For instance, Polyetherimide displays good resistance to some chemicals, such as alcohols and hydrocarbon solvents, but may dissolve in partially halogenated solvents. These challenges necessitate the use of advanced manufacturing designs and equipment capable of withstanding high temperatures, especially when processing high-temperature thermoplastics.
Popular Types of Thermoplastics
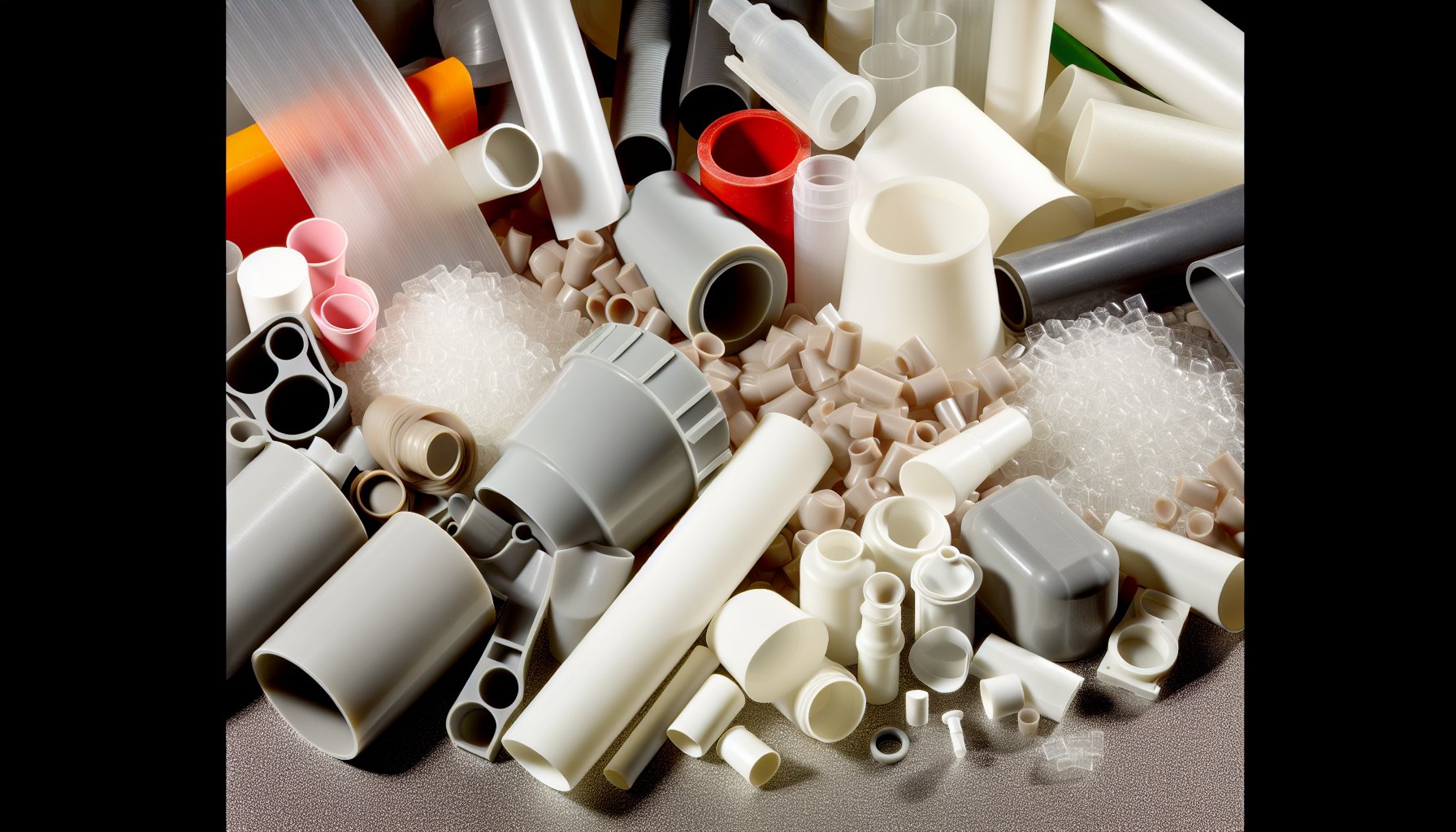
In the expansive realm of thermoplastics, some types, due to their popularity and extensive use, stand out. These include Polyethylene (PE), Polypropylene (PP), and Polyvinyl Chloride (PVC), each with unique properties and applications.
Some popular thermoplastics used in a variety of applications are:
Polyethylene: known for its resistance to moisture, flexibility at room temperature, and the ability to be heat sealed
Polypropylene: appreciated for its balance of thermal, chemical, and electrical properties, along with its moderate strength, making it a preferred choice for injection molding
Polyvinyl Chloride: used for its durability, chemical resistance, and flame retardant properties
Nylon (Polyamide): known for its high strength, toughness, and resistance to abrasion
These thermoplastic resins are widely used due to their unique properties and versatility.
Polyethylene (PE)
Polyethylene (PE), a versatile homopolymer composed of repeating ethene monomers, stands out among thermoplastics for its toughness, abrasion resistance, and chemical resistance. Whether it’s the flexibility of Low-Density Polyethylene (LDPE) or the strength and rigidity of linear low density polyethylene (LLDPE) in products like plastic films and bags, or the durability of High-Density Polyethylene (HDPE) in items such as milk jugs, detergent bottles, and large pipes, PE showcases its adaptability in form and function.
Moreover, PE has the following properties and uses:
It is resistant to a variety of solvents and dilute acids
It is used for its insulating properties in electrical applications
It is a cost-efficient material choice
It can be shaped into products via injection molding and blow molding techniques
PE serves as an example of the versatility and adaptability of thermoplastics.
Polypropylene (PP)
Polypropylene (PP) is another popular thermoplastic, characterized by its semi-rigid nature, cost-effectiveness, and excellent chemical, electrical, and fatigue resistance. PP’s wide array of applications spans from reusable food containers and medical equipment to ropes, automotive parts, and even living hinges due to its fatigue resistance.
Constructed from repeating propylene monomers, PP has a good balance of thermal, chemical, and electrical properties, along with moderate strength, making it a preferred choice for injection molding. Despite its many benefits, PP has disadvantages such as susceptibility to UV deterioration, difficulty in painting due to poor bonding qualities, and high flammability.
Polyvinyl Chloride (PVC)
Polyvinyl Chloride (PVC) is one of the most widely-used types of plastics, found in products such as packaging, home furnishings, children’s toys, automobile parts, building materials, and hospital supplies. Rigid PVC, also known as uPVC, is used extensively in construction for items like pipes, window frames, and doors due to its strength and resistance to moisture and chemicals. It also finds use in the medical industry for artificial limbs.
Flexible PVC, created by adding plasticizers, is utilized for various purposes including:
Electrical cable insulation
Imitation leather
Inflatable products
Medical applications such as tubing and blood bags
However, the use of PVC raises environmental concerns due to its presence in a multitude of consumer products and its impact on the environment during disposal.
Advanced Engineering Plastics
Thermoplastics extend beyond the popular types we know. There are also advanced engineering plastics—specialized materials with superior mechanical properties and exceptional resistance to high temperatures. These include the likes of PEEK, PPS, and PEI, which are often used in applications where high performance is essential.
For instance, PEEK is known for its ability to maintain mechanical properties, chemical resistance, and electrical insulation even at elevated temperatures up to 240°C. Enhancing PEEK with additives or reinforcing fibers results in higher impact resistance, stronger tensile strength, and improved thermal properties.
On the other hand, PBI fibers, known for their extreme thermal and chemical stability, are utilized in high-performance protective clothing such as astronaut suits and firefighter gear.
PEEK
PEEK (Polyetheretherketone) is a high-performance engineering thermoplastic known for its good abrasion resistance, low flammability, and low emission of smoke or toxic gases. By adding glass or carbon fibers to PEEK, properties such as creep and fatigue resistance, thermal conductivity, and heat distortion temperature can be significantly enhanced.
PEEK can be fabricated using conventional methods like injection molding, extrusion, and compression molding. The processing conditions during fabrication play a critical role in determining its crystallinity and mechanical properties. Ongoing research and development efforts in the aerospace industry are improving PEEK’s performance and manufacturing processes.
PPS
PPS (Polyphenylene Sulfide) is a versatile engineering thermoplastic that offers robust chemical compatibility, high-temperature resistance, and significant mechanical strength. It can sustain high temperatures with a melting point of 280°C and consistent performance up to a continuous service temperature of 220°C, advantageous for heat-exposed applications.
The material offers significant mechanical strength, demonstrated by a tensile strength of 102 MPa and a compressive strength of approximately 21,500 PSI. Specialized grades like Techtron® HPV PPS provide enhanced wear resistance.
Additional attributes of PPS include excellent dimensional stability, electrical insulation properties, and inherent flame resistance with a UL 94 V-0 rating.
PEI
Polyetherimide (PEI) is an amorphous engineering thermoplastic known for its high heat distortion temperature and outstanding mechanical and electrical properties. Some key features of PEI include:
High glass transition temperature (Tg) of 217°C
Excellent thermal endurance
High heat distortion temperature
Good dimensional stability
Good chemical resistance
These properties make PEI suitable for a wide range of applications that require high performance in extreme conditions.
The unique properties of PEI make it especially suitable for high-performance electronic and electrical components, as well as applications in the automotive industry and microwave cookware. Despite its numerous benefits, the handling and processing of PEI require adherence to specific temperature controls and careful handling to ensure safety.
Thermoplastics in Everyday Life
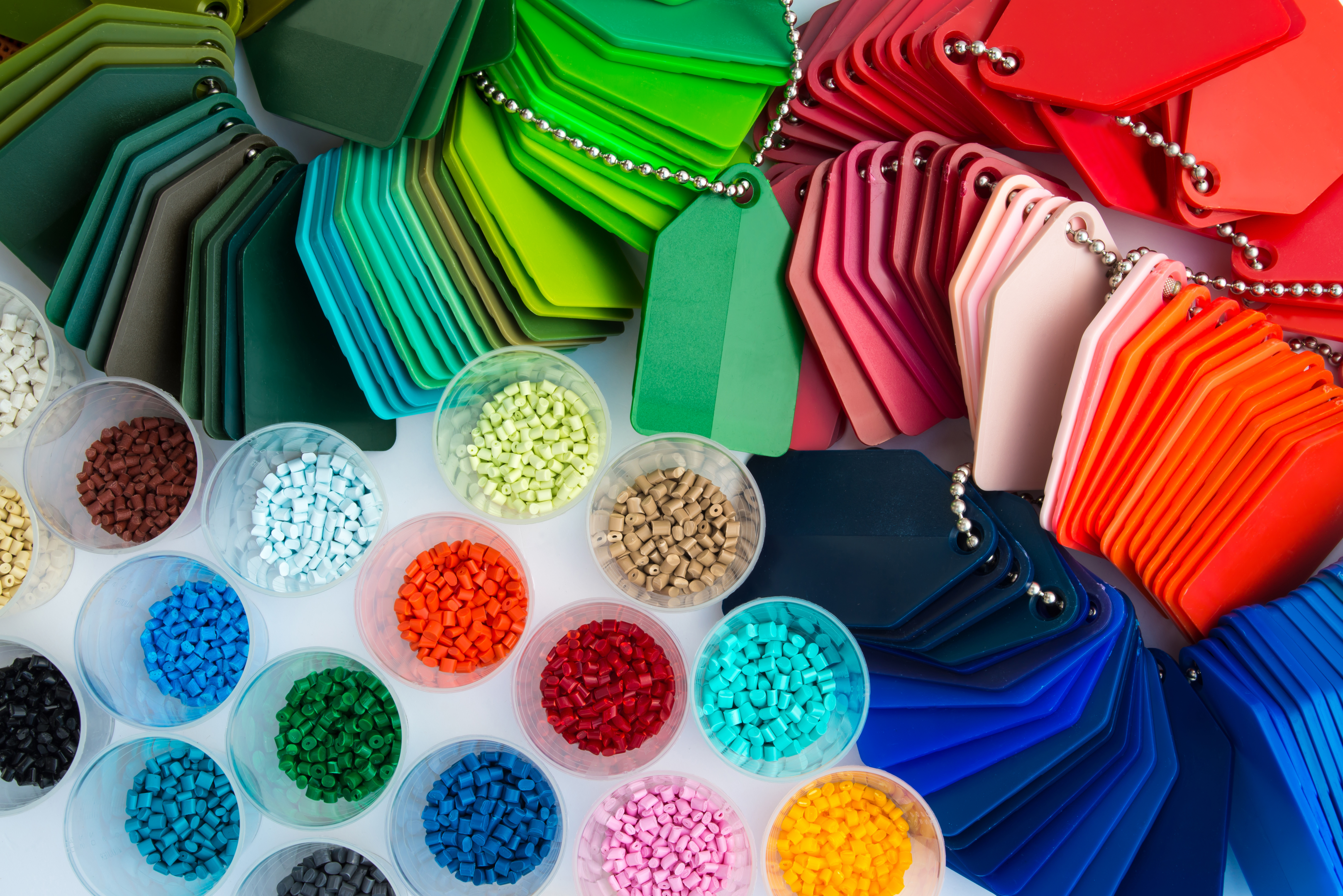
Thermoplastics are a common sight in daily life. Their versatility spans a broad range of applications, including:
Polyethylene in plastic bags
Polypropylene in food containers
Nylon in carpets and musical instrument strings
Manufacturing medical implants
Optical products
Architectural parts
Sports equipment
Smart textiles
The advanced material properties of thermoplastic material make them suitable for various uses.
From your morning cereal box to the phone you’re holding, thermoplastics are everywhere. Consumer products, such as toys and telephones, are often made from ABS due to its lightweight nature and high impact resistance. The ubiquitous presence of thermoplastics in everyday items underscores their importance and versatility.
Packaging Materials
When it comes to packaging materials, thermoplastics like polyethylene and polypropylene are the go-to choices for their durability and flexibility. High-Density Polyethylene (HDPE) is the material of choice for milk jugs, water bottles, and cereal box liners due to its notable strength and resistance to chemicals.
Biaxially Oriented Polypropylene (BOPP) films, known for their enhanced strength and clarity due to stretching in both the machine and cross directions, are frequently used in snack packaging and for producing clear tape. Whether it’s keeping your food fresh or ensuring your parcels are secure, thermoplastics play a crucial role in the packaging industry.
Medical Devices
In the medical field, thermoplastics are hailed for their biocompatibility and durability. Polypropylene is used for medical products due to its resistance to heat, impact, and chemicals. Similarly, PEEK is biocompatible and suitable for medical applications because of its low friction, good dimensional stability, and excellent sterilization resistance at high temperatures.
Polycarbonate is utilized for items such as eyeglass lenses and surgical face shields due to its transparency and durability. Acrylonitrile Butadiene Styrene (ABS) is used in medical devices like tendon prostheses and tracheal tubes, owing to its rigidity and impact resistance. From eyeglasses to surgical equipment, thermoplastics revolutionize healthcare with their unique properties.
Automotive Industry
In the automotive industry, thermoplastics, which are products of the chemical industry, play a significant role due to their lightness and fuel efficiency. The adoption of thermoplastics in lieu of traditional materials such as steel leads to improved fuel economy and decreased CO2 emissions.
Continuous fiber-reinforced thermoplastics enhance strength and stiffness, contributing to lightweight vehicle structures. Long fiber reinforced thermoplastics are used in car structural parts such as door modules and bumpers, offering advantages like flexibility in design and ecological benefits. From bumpers to dashboards, thermoplastics drive the modern automotive industry.
Sustainability and Recycling of Thermoplastics
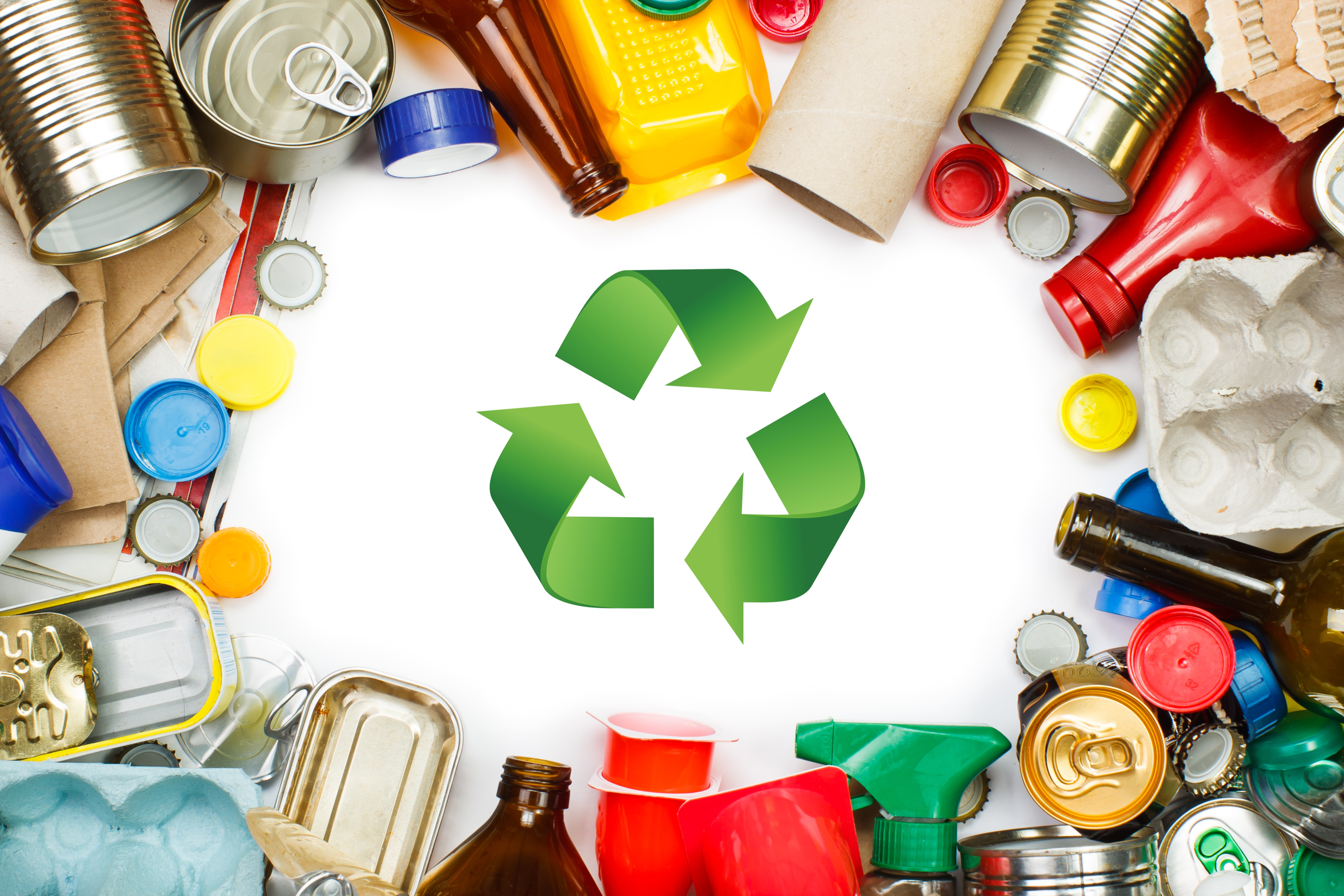
In addition to their versatility and durability, thermoplastics also contribute to sustainability. Most thermoplastic polymers can be recycled and reprocessed multiple times without significant degradation, contributing positively to environmental conservation. Moreover, advancements in recycling practices, such as pyrolysis and chemical recycling, are being developed to enhance the efficiency and minimize the environmental impact of recycling thermoplastics.
However, the economic viability of recycling thermoplastics is influenced by factors including the demand for recycled products, the costs associated with recycling, and the availability of virgin materials. Nonetheless, with continuous advancements and increasing regulatory pressures, the sustainability of thermoplastics is set to improve.
Biodegradable Thermoplastics
Despite most traditional thermoplastics being non-biodegradable, alternatives like PLA, PVAL, PVOH, and PHAs exist that are biodegradable. These biodegradable thermoplastics offer environmentally friendly alternatives to traditional thermoplastics. For instance, Poly(lactic acid) (PLA), a well-known biodegradable thermoplastic, is increasingly used in a variety of applications such as packaging and disposable cutlery.
The rising environmental impact of thermoplastics, specifically single-use plastics, has propelled increasing regulatory pressures and the search for sustainable alternatives. With the development of biodegradable thermoplastics, we are taking a step closer to a sustainable future.
Recycling Process
Recycling thermoplastics involves a series of steps:
Collection
Sorting
Cleaning
Shredding into flakes
Washing to remove impurities
Melting and extruding into pellets for creating new products
However, challenges arise from the requirement for precise separation by type and the presence of contaminants, such as mineral and organic acids, in corrosive environments, which can limit the quality and applicability of the recycled material in high-performance areas.
Recent technological advancements in the recycling of thermoplastics include:
Automated sorting equipment
Optical sorting technology
Compatibilizers for mixed waste
Solvent-based purification
These advancements have significantly enhanced the efficiency and purity of recycled thermoplastics, making the recycling process more efficient and sustainable.
Safety Considerations

Considering the safety aspects of thermoplastics is essential, despite their numerous advantages. Most types of thermoplastic are safe to use when utilized as intended, which encompasses a broad range of applications. However, adhering to recommended handling and processing protocols is essential to maintain the safety of thermoplastic materials in various applications.
Toxicity Concerns
Despite most thermoplastics being deemed safe, certain types and uses do raise toxicity concerns. For instance, phthalates, commonly used as plasticizers in PVC, are increasingly scrutinized due to potential health risks. Also, PVC releases toxic hydrogen chloride gas when involved in accidental fires, which is a significant risk to human health and safety, resembling a chemical attack.
However, there are safer alternatives available. For instance, Polypropylene (PP) is acknowledged by the FDA as a non-toxic alternative to PVC, especially beneficial for applications in foodservice and packaging. Therefore, it’s crucial to choose the right thermoplastic for the intended application to ensure safety.
Safe Handling and Processing
To minimize potential risks during manufacturing and application, it is crucial to handle and process thermoplastics safely. Methods like:
Injection molding
Extrusion
Thermoforming
Blow molding
Rotational molding
Each require adherence to specific temperature controls and careful handling during the curing process to ensure safety, making the use of heat resistant medical equipment essential.
Implementing proper safety techniques in handling thermoplastics reduces hazards and enhances overall workplace safety. Whether you’re molding a plastic toy or fabricating a medical device, following proper safety protocols ensures not just the integrity of the final product but also the safety of all involved in the process.
Innovative Applications and Future Trends
The use of thermoplastics is not limited to common applications. They are increasingly being used in innovative applications and are shaping future trends. From sporting goods to disaster-resistant buildings, thermoplastic composites are finding their place in high-performance applications due to their advantageous properties like lightness, stability, and damage resistance.
3D Printing
3D printing is one such innovative application. Selective Laser Sintering (SLS) and Fused Deposition Modeling (FDM) are two prevalent 3D printing technologies that employ thermoplastics to create both prototypes and production components. Materials like PEEK can be used for 3D printing using FDM, thanks to its low moisture absorption, while PLA is commonly utilized for its ease of printing in FDM applications.
With advancements in 3D printing technology, the possibilities for thermoplastics are expanding into new horizons.
Composites for Disaster-Resistant Buildings
The construction of disaster-resistant buildings also utilizes thermoplastic composites. Their advantages include:
Lightness
Strength
Corrosion resistance
Durability
These qualities make them an attractive alternative to traditional materials like steel and concrete. Thermoplastic composites are increasingly used in construction for building and bridge structures in harsh environments or high-risk areas for natural disasters due to their resilience to environmental impacts.
With this innovative application, thermoplastics are not just shaping our everyday lives but also shaping the future of construction.
Emerging Technologies and Materials
New technologies and materials are emerging in the field of thermoplastics. New thermoplastic materials with adaptable crosslinks are being developed, creating materials that blend the advantageous properties of both thermoplastics and thermosets. Moreover, advanced materials such as UBQTM, developed from unconventional resources like 100% unsorted household waste, are contributing to the reduction of environmental impact.
High-performance polymers, like polybenzimidazole, are emerging with characteristics such as superior stability and ability to retain stiffness and toughness even at high temperatures. With these emerging technologies and materials, including advanced polymer chains, the future of thermoplastics is looking brighter than ever.
Summary
From our water bottles and phone cases to 3D printers and disaster-resistant buildings, thermoplastics permeate every facet of our lives. Their unique properties make them a versatile, cost-effective, and sustainable choice for a wide range of applications. While there are challenges and safety considerations to address, ongoing research and technological advancements continue to unlock new potentials for these materials. With the emergence of innovative applications, advanced engineering plastics, and sustainable alternatives, the future of thermoplastics is not just promising—it’s already here.
Frequently Asked Questions
What are 3 examples of thermoplastics?
Common examples of thermoplastics include acrylic, polyester, and polypropylene. These materials are widely used in various applications due to their ability to be easily molded when heated and then hardened upon cooling.
Is thermoplastic good material?
Yes, thermoplastics are a good material due to their durability, lightness, and relatively low production costs, and they can be melted and recast almost indefinitely.
Are thermoplastics toxic?
Thermoplastics are considered some of the most eco-friendly and non-toxic materials available in the market today, making them a safe choice for various applications.
Is thermoplastic better than plastic?
Thermoplastics are more versatile but less strong and durable compared to thermoset plastics, which are stronger and more durable but cannot be reformed. Therefore, the choice between thermoplastic and thermoset plastic depends on the specific requirements of the application.
What are the main types of thermoplastics?
The main types of thermoplastics are Polyethylene (PE), Polypropylene (PP), and Polyvinyl Chloride (PVC), each with distinct properties and uses.