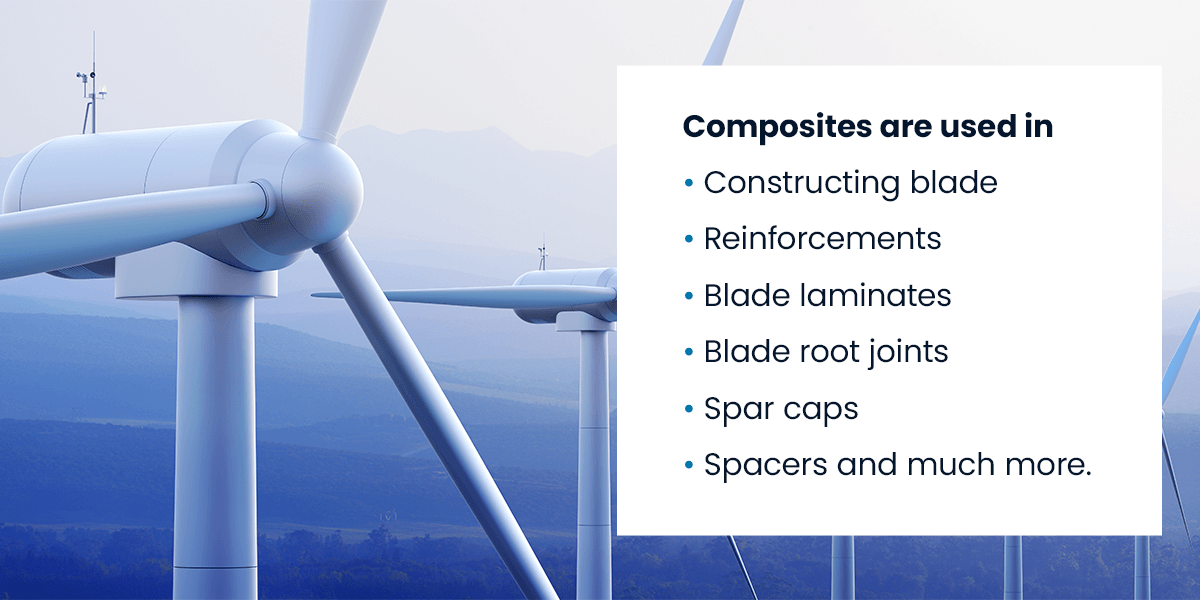
The application of composites in renewable energy generation has grown exponentially over the years. Their physical characteristics allow for design flexibility and high durability, which are excellent for reducing costs. Using composite materials in the electric power industry also improves performance and efficiency.
This article will explore the advantages of using composites in solar, wind, and hydropower generation. We’ll consider examples of composite materials used in various applications and their benefits compared to traditional parts.
Composites in Solar Power Generation
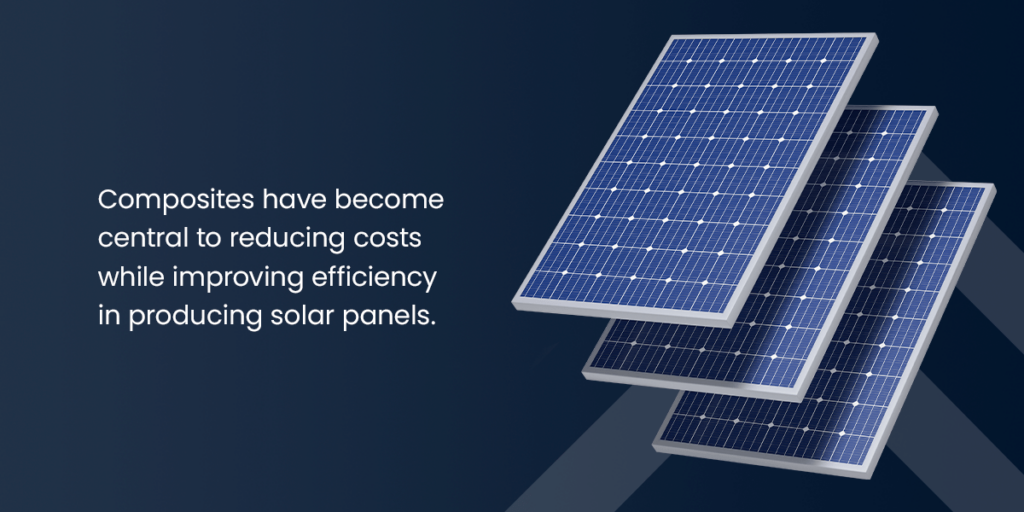
Composites have become central to reducing costs while improving efficiency in producing solar panels. Their characteristics allow for optimal design and durability, resulting in a sturdy increase in demand. Here are the advantages of using composite materials in the construction of solar panels:
1. Lightweight and Durable Materials
Composite materials offer high strength-to-weight ratios. This aspect makes for easy transportation and installation, a need in the solar panel industry. Regardless of the setting, you can reduce costs and facilitate deployment.
2. Improved Efficiency
Solar panels were traditionally produced using float glass, which was rigid with good light transmission properties. They also served as suitable moisture barriers. The challenge was that they required coating to reduce reflectivity and repel dirt, increasing costs. They also added weight, making roof installation difficult, and became cloudy over time, reducing their energy efficiency. The glass was replaced with a thin, clear polymer film of ethylene tetrafluoroethylene as a solution.
Using solar panel composites boosts power efficiency to new levels. For example, lightweight panels arrayed in honeycomb patterns enable more panels per array. These panels can enhance the absorption and conversion of solar energy, resulting in increased electricity generation. Again, replacing glass and aluminum with polymer-cored composite improves panel durability while reducing weight.
3. Corrosion Resistance
Solar panels encounter some of the harshest conditions. They are exposed to weather elements like ultraviolet light, humidity, rain, and varying temperatures. Parts made of aluminum lack strength, reducing the solar panels’ life span. Composite materials have high corrosion resistance, making them suitable for outdoor applications and withstanding severe weather conditions.
4. Design Flexibility
Panel design is vital in solar energy design, making composites the ideal material. Composite materials allow you to design panels in varying shapes, sizes, and configurations with high precision. The flexibility also allows for integration in different applications, expanding the possibilities.
6. Reduced Maintenance Cost
Composite materials require less maintenance than traditional materials. They resist corrosion, eliminating the need for frequent part replacements and repairs. Reducing the frequency and scope of maintenance cuts down expenses, which appeals to most users.
Composites in Wind Power Generation
Composites are widely known in wind energy generation. They are used in constructing blade reinforcements, blade laminates, blade root joints, spar caps, spacers, and much more. Composite materials are also used in building access structures like ladders and platforms.
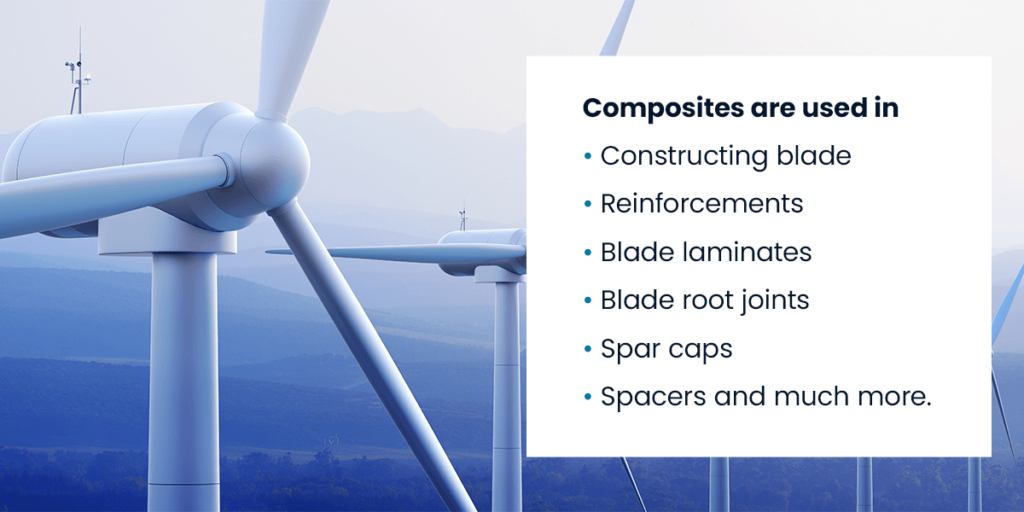
1. High Strength
Composites like fiberglass are widely used as reinforcement materials in many wind applications. These materials are robust and durable, allowing the wind turbine blades to withstand harsh conditions like strong winds.
Carbon-fiber-reinforced polymer is often used for blade parts subjected to stress. While fiberglass remains ideal for blade construction due to its longevity and price, recent techniques enable you to combine fibers in the same polymer to create a hybrid material with some carbon fiber benefits at a lower cost.
2. Lighter Blades
Composites are significantly lighter than traditional materials like steel. Lighter wind turbine blades reduce the weight of the rotating parts. Consequently, mechanical stress drops and turbine performance rises. Also, the lightweight materials allow you to increase the blade length without compromising integrity, boosting the energy capture level and efficiency.
3. Design Flexibility
Composites are easier to design. Their properties allow manufacturers to optimize their shape and length, considering the ideal aerodynamic characteristics. Wind turbines can operate in different wind conditions, speeds, and directions. Ultimately, users benefit fully from the energy-generating capabilities of wind turbines.
4. Enhanced Cycle Fatigue Resistance
In wind turbines, blades go through numerous high-stress cycles. As a result, cumulative damage happens over time. Metals like steel will harden and become brittle over time, and a regular cycle can eventually be enough to destroy it. In comparison, composites can withstand intense stress for long periods due to their improved high-cycle fatigue characteristics, making them ideal for this application.
5. No Risk of Corrosion
Conventional wind turbine blade materials like steel are susceptible to corrosion. The implication is high maintenance frequency and costs. Composite blades don’t feature components that can rust, so corrosion is never a risk. They are suitable for offshore wind farms where exposure to saltwater and harsh conditions are prevalent.
6. Reduced Noise and Environmental Impacts
Composite blades are quiet because they dampen vibrations. Additionally, wind turbine blades made of composite materials have less of an environmental impact than conventional blades. Using thermoplastics for wind energy generation can reduce manufacturing cycles. They also enable thermal joining, affording the wind industry increased throughput and cost savings.
Composites in Hydropower Generation
Hydropower is one of the oldest and largest renewable energy sources in the United States. It accounts for 28.7% of total renewable electricity generation in the country.
There’s a high need for manufacturers in the industry to invest resources into developing sustainable composite solutions. Composite materials can offer a myriad of benefits in hydropower generation.
1. Lightweight and Durable
Composite turbines are lightweight compared to traditional steel turbines. They have a high strength-to-weight ratio, suitable for those looking to enhance product longevity. They can withstand vibration and extreme loads. The weight also contributes positively to installation and transportation.
2. Improved Hydrodynamic Performance
Composites like carbon fiber can potentially enhance the construction and repair of turbines, lock gates, and other vital components. Small and microturbines, in particular, can benefit from the unique properties of fiber-reinforced plastics. Composites can also be engineered to reduce drag and enhance water flow. These attributes can improve turbine efficiency and power output in hydropower plants.
3. Design Flexibility
Manufacturers can tailor composite materials to their desired configurations. They are easily customizable, allowing you to meet the specific project requirements. You can design the required size, shape, and structural characteristics to optimize performance while improving the structural integrity of your penstocks, turbine blades, and intake structures.
4. Reduce Cost
Hydro components made of composite materials are durable and resistant to degradation. Their inherent resistance to water damage, ultraviolet radiation, and adverse environmental conditions add to their longevity. These features help users cut costs on replacements and repairs, which is vital in the industry. Quality products also reduce downtime.
Contact Atlas Fibre With Your Composite Needs
Are you searching for a reliable manufacturer of composites and thermosets? Look no further. Atlas Fibre is North America’s leading producer and supplier of thermoset composites. We have years of experience in the industry and will work to meet your unique needs. Contact us today to learn more.
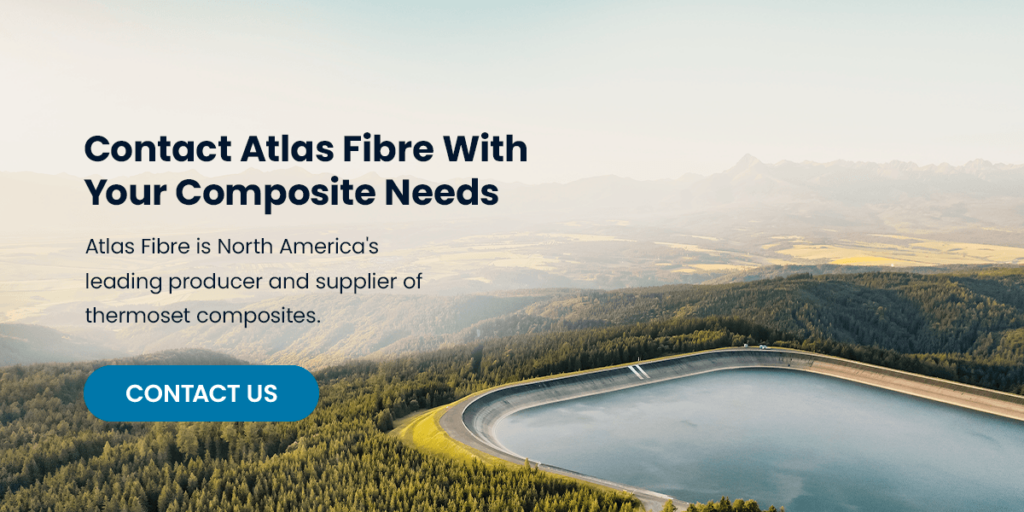