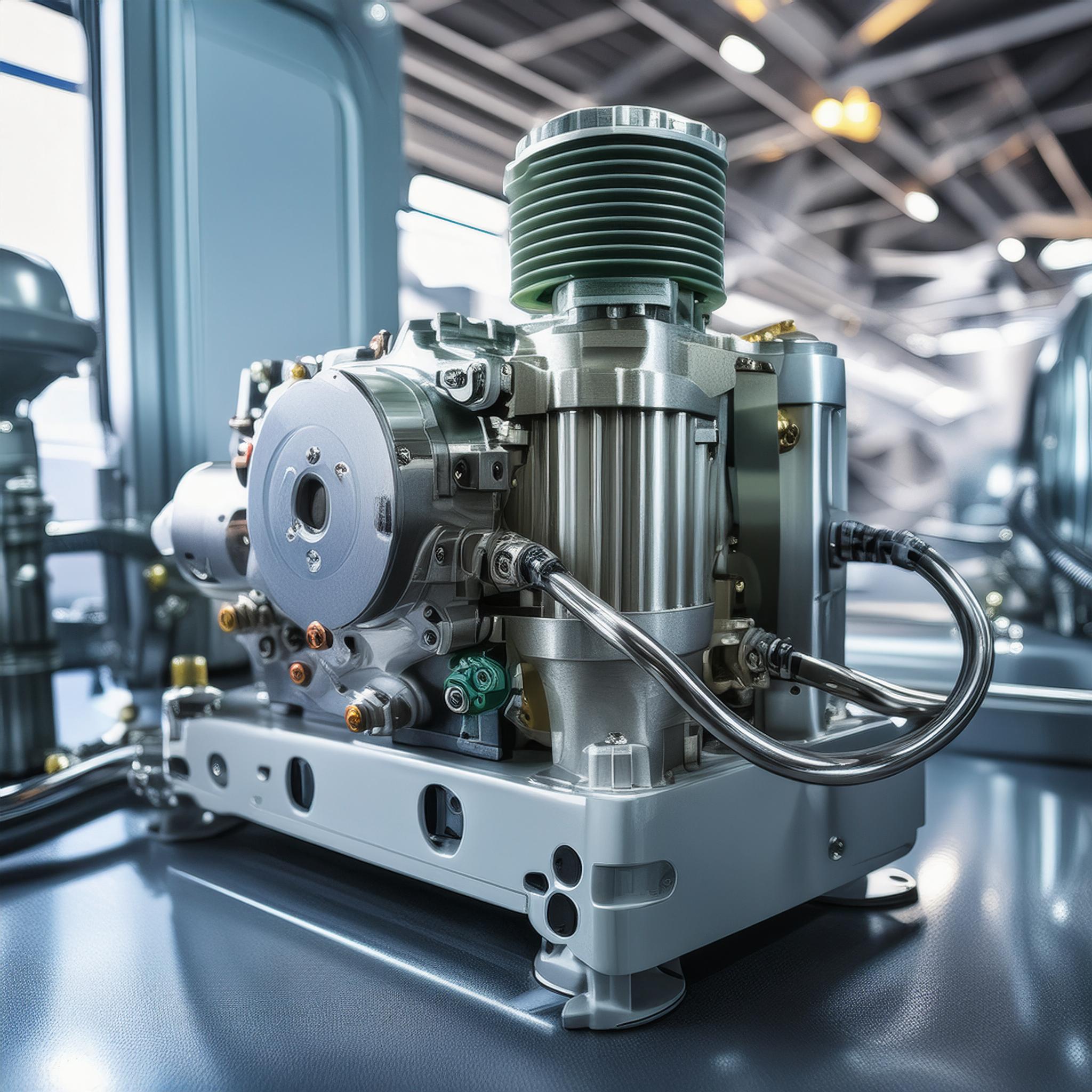
Manufacturing relies on a multitude of intricate parts, and at Atlas Fibre, we specialize in producing one of the most essential components: the vacuum pump vane.
A vane pump operates by moving fluid through the oscillating motion of vanes within the pump. These rotary pumps feature paddle-like vanes attached to a cylindrical rotor, forming individual compartments that capture and transport fluid efficiently.
Vane pumps are vital in fluid power systems across various industries, including automotive and aerospace. Their efficiency in transferring fluids under diverse conditions makes them indispensable for powering hydraulic systems. To ensure optimal performance, meticulous design and careful selection of materials for these components are crucial.
Let’s look at the different types of vane pumps and the advantage that thermoset composites provide in terms of durability, corrosion resistance and dimensional stability.
The Different Types of Vane Pump
Vane pumps operate on a simple yet effective principle: using rotating vanes to create suction and discharge fluid. They classify these pumps into various types based on their design and operational characteristics.
Let’s explore some of the common types:
External Vane Pumps
Also known as rotary vane pumps, these feature vanes that are free to slide into or out of slots in the pump rotor. As the rotor spins, centrifugal force pushes the vanes outward, maintaining contact with the pump casing. This action creates chambers that draw in and expel fluid, generating continuous flow.
Internal Vane Pumps
Internal vane pumps have vanes that protrude from the rotor and rub against the inside of the pump casing. This is different from external vane pumps. As the rotor rotates, these vanes trap and propel fluid between the inlet and outlet ports, facilitating fluid transfer.
Variable Displacement Vane Pumps
These pumps offer the flexibility to adjust fluid output by varying the displacement of the vanes. Operators can change the angle or position of the vanes to control flow rates according to need. This helps improve energy efficiency and system performance.
Each vane pump type has its own benefits and uses. The materials that the pumps are made of determine their performance and durability. Traditionally, manufacturers have used materials like metals to produce vanes. However, the introduction of thermoset composite materials has revolutionized this aspect of pump manufacturing.
Start Using Thermoset Material for Vane Pumps
Thermoset composites are an excellent material choice for vane pumps because of several key advantages over other materials. Thermoset material has low friction and self-lubricating properties, reducing wear and increasing part efficiency (minimizing friction against the pump housing compared to metal vanes). Composites with corrosion and chemical resistance properties can handle many different fluids, including corrosive chemicals, without getting damaged.
Engineers design thermoset composite materials to offer exceptional mechanical properties, chemical resistance, and thermal stability, making them an ideal choice for vane pump components.
There are numerous advantages of using thermoset composites as the preferred material within vane pumps:
Strength and Durability
Thermoset composites boast high strength-to-weight ratios, surpassing traditional materials like metals and polymers. This superior strength ensures longevity and reliability, even under demanding operating conditions, reducing maintenance costs and downtime.
Corrosion Resistance
Vane pumps often handle aggressive fluids that can corrode conventional materials over time. Thermoset composites resist corrosion well, making pumps last longer and reducing the chance of contamination in fluid systems.
Dimensional Stability
Thermoset composites stay the same size, even when pressure or temperature changes. This keeps pump performance consistent by keeping vane-to-casing clearances precise.
Customizability
Manufacturers can tailor the properties of thermoset composites to meet specific application requirements, whether it’s optimizing for wear resistance, temperature tolerance, or fluid compatibility. This versatility allows for customized solutions that enhance pump efficiency and reliability.
Thermoset composite materials are a good option for vane pumps in various industries. They are lightweight, corrosion-resistant, have low friction, and can be machined precisely. These materials also help improve efficiency, extend service life, and lower operating costs.
By integrating thermoset composite materials into vane pump design, manufacturers can unlock new levels of performance, efficiency, and reliability.
Using advanced materials is bringing innovation to pump technology, whether in industrial machinery or automotive vehicles. This marks a new era of improvement in fluid power and hydraulic systems. Industries are working on making fluid power systems more efficient and sustainable, and thermoset composites will be important in this process.