Atlas Fibre is more than just North America’s leading supplier of thermoset composite material and an expert fabricator of these advanced plastics. We’re also a partner in your businesses’ operation.
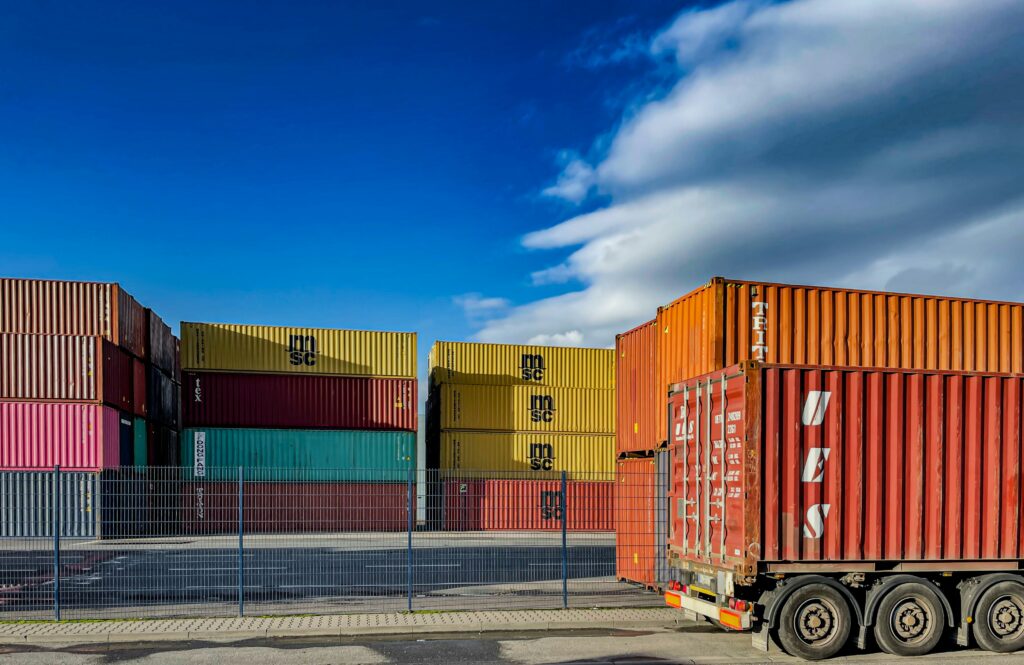
We take every aspect of our own enterprise so seriously that we find it helpful to highlight how a company like ours – one that manufactures, distributes, supplies and yes, fabricates this material – can change how an entire industry thinks about order delivery – but that’s what we’re doing!
To improve our order delivery process over the last year, Atlas Fibre has taken big steps. We’ve implemented programs, technology and processes to streamline production and planning and enhanced our supply chain management. We’ve invested in automation software and solutions in every department, remained focused on improving key quality control mechanisms, and never lost sight of customer service. And we’re just getting started.
Let’s explore some of the ways that Atlas Fibre guarantees that your order of thermoset composite materials arrives when you need it.
Production Planning and Scheduling
Over the past year, Atlas Fibre has implemented a state-of-the-art and highly efficient production planning and scheduling system. Utilizing sophisticated forecasting tools lets us anticipate demand and plan production for efficiency (meaning our facility runs 24-hours per day). This lean approach to manufacturing improves our own internal resource allocation but also eliminates waste (reducing costs) and minimizing delays for our valued customers.
Enhancing Supply Chain Management
In addition to leveraging supply chain analytics to identify bottlenecks and improve logistics operations, Atlas Fibre has been committed to optimizing every component of its supply chain. Implementing robust inventory systems and maintaining strong relationships of our own ensures the timely delivery of raw material, shapes, and parts.
Investment in Automation and Technology
Technology has always been a critical part of this industry, but it’s not limited to the machines alone (though they are amazing). Investing in technology in 2024 is investment in both hardware and software (including software that automates repetitive tasks and processes to increase throughput or reduce errors). Enterprise Resource Planning (ERP) system enable us to streamline different aspects of our operation (including order delivery) and other digital tools provide granular insights on order tracking, inventory management and real-time shipping updates.
Improvements to Quality Control
Quality isn’t a job at Atlas Fibre, it’s a way of life. We’ve so deeply ingrained quality control into each process and step of the thermoset composite laminate manufacturing and distribution offering that we believe we’re the only machinist of advanced plastics in operation today that so confidently and proudly demonstrates its commitment in such a clear and unambiguous way. To ensure that our facility is free from contaminants (we have our own Class 1K clean room and are a “plastics-only” machinist. The result of this rigid focus on quality? Fewer defects, which means fewer reworks and less burden on the order delivery system
Optimizing Warehouse and Distribution
It’s not possible to be the largest (and best, of course) distributor of thermoset composite laminate in North America without having warehouse space that is optimized for distribution and delivery. By implementing a warehouse management system, Atlas Fibre always knows the precise location of inventory and status or order fulfillment. An optimized warehouse layout and material handling processes make faster picking and packing possible.
Focusing on Customer Service
We don’t fabricate parts or distribute raw materials – we make bonds and connections that will stand the test of time. It’s like customer service is the epoxy to our raw material! Our dedicated and incredibly knowledgeable team strives for excellence and precision in its communications, capable of providing real-time order status updates, delivery timelines and more upon request.
Everything we do at Atlas Fibre revolves around getting our raw material or a fabricated part onto your shipping dock. The approaches outlined above summarize just some of the steps we’ve taken to streamline operations, reduce lead times, and deliver orders efficiency to customers.