In the quest for materials that withstand arctic chills, low temp plastics like G10 Cryo emerge as champions of resilience and performance. This article unveils how these plastics defy the deep freeze, supporting applications where failure is not an option. Learn about their unique properties, applications that depend on their reliability, and how to select the right low temp plastic for your needs—all without the complexities of materials science jargon.
Key Takeaways
Thermoplastics become stiffer and more brittle at low temperatures, affecting their durability and performance, but these effects are reversible when temperatures rise.
G10 Cryo, a glass epoxy material, is especially suited for low-temperature applications due to its high mechanical strength, dimensional stability, and low thermal conductivity, making it a popular choice in the medical, aerospace, and marine industries.
Choosing the right low temp plastic depends on factors like chemical resistance, thermal degradation, operating temperature range, and impact strength, with polymer chemistry being instrumental in enhancing a material’s cold resistance.
Understanding the Effects of Low Temperatures on Plastics
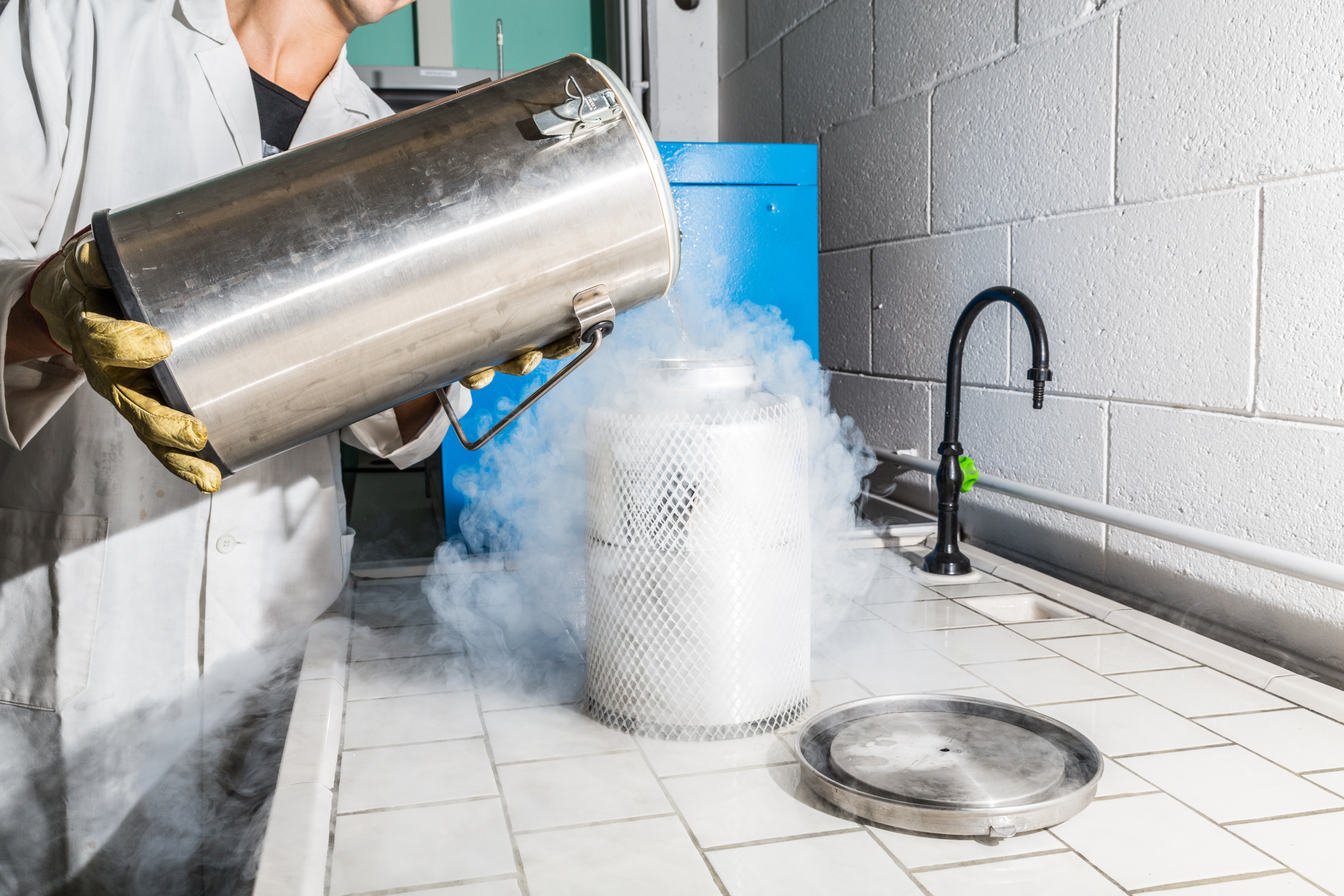
Most materials, plastics included, exhibit significant changes in their physical and mechanical properties when temperatures fall. The impact is so profound that it can alter how these materials behave, affecting their durability, performance, and longevity.
But what exactly happens to plastics when they are subjected to low temperatures? How do they react, and what are the implications of such reactions on their use in cold environments?
The impact of cold temperatures on molecular chains
Thermoplastics, a type of plastic that can be heated and reshaped multiple times, experience dramatic changes in their molecular chains as temperatures plummet. They become stiffer, harder, and their impact strength – the ability to absorb energy without breaking – decreases. However, these changes are not permanent.
These materials regain their original properties when the temperature increases, a feature referred to as reversibility. This unique ability to adapt to fluctuations in temperature makes thermoplastics a preferred choice for various applications in cold climates.
How temperature decreases affect material properties
When the mercury dips, typical increases are observed in the mechanical properties of plastics, such as tensile strength and Young’s modulus. However, this comes with a downside. Plastics become less ductile, meaning they can’t stretch without breaking, and their fracture elongation – the extent they can stretch or deform before breaking – decreases.
This transition from ductile to brittle behavior can pose significant challenges, especially in applications that require plastics to withstand stress and strain without cracking or breaking.
The role of thermal conductivity in low-temperature environments
In cold environments, the thermal conductivity of a material (explore the thermal conductivity of composite materials here), which is a measure of its ability to conduct heat, significantly influences the performance of plastics. Most plastics have low thermal conductivities, which means they are poor conductors of heat. This characteristic is advantageous in cold environments as it helps preserve heat within the material, preventing rapid temperature changes that could lead to cracking or deformation.
However, as the temperature drops below 50K, the thermal conductivity of plastics decreases even more, following a cubic relationship with temperature. This characteristic, which affects heat transfer, needs to be taken into consideration when designing plastic components for low-temperature applications.
Glass Epoxy Materials for Low Temperature Applications: G10 Cryo
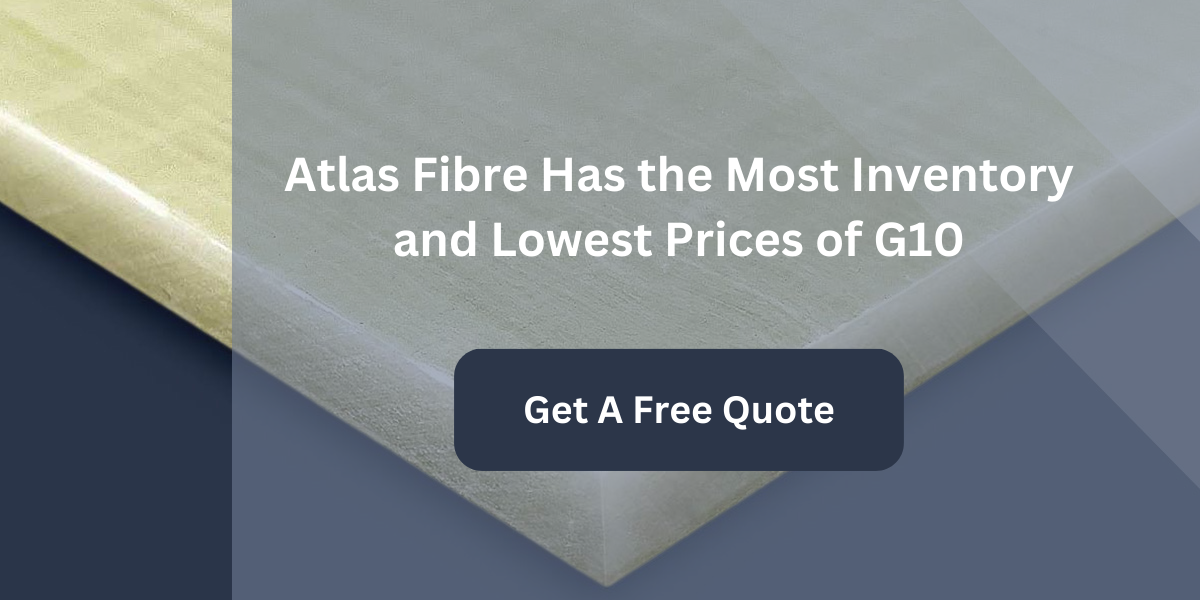
G10 Cryo stands out for its exceptional performance in cold environments amongst the multitude of low temp plastics available. Introduced in the 1950s for printed circuits, G10 Cryo is a glass epoxy material known for its excellent electrical properties, chemical resistance, and high strength. It has since found applications in a range of industries, thanks to its unique properties that make it ideal for low-temperature applications.
Characteristics and advantages of G10 Cryo
Thanks to its composition of woven fiberglass and an epoxy resin binder, G10 Cryo boasts high mechanical strength and dimensional stability. It can endure subzero temperatures without significant loss of properties, making it suitable for long-term use in demanding cryogenic environments.
Additionally, G10 Cryo possesses unique thermal conductivity properties, making it an ideal material for specialized applications such as cryogenic biotechnology machinery, spaceflight hardware, and low-temperature physics equipment.
Common uses and industries for glass epoxy materials
G10 Cryo and other glass epoxy materials have found widespread use across various industries, including the medical, aerospace, and marine sectors. Its excellent electrical insulation properties make it a preferred choice in applications where such attributes are critical.
In the aerospace sector, it plays a crucial role in applications operating at cryogenic temperatures, common in various aerospace applications. Furthermore, its suitability for low-temperature usage makes it an essential material for reliable performance in Arctic exploration structures and other applications exposed to extreme cold weather conditions.
Comparing G10 Cryo to other plastics in cold environments
When compared to other plastics, G10 Cryo stands out for its superior performance in cold environments. It exhibits low cold creep (the slow, permanent deformation of a material under mechanical stress) and high resistance to thermal shock, attributes not commonly found in many other plastics.
Furthermore, it is compatible with stainless steel due to matching thermal contraction rates, which is beneficial for cryogenic composite structures. The cryogenic grades of G10, G10CR, and G11CR display uniform material properties at low temperatures, overcoming the variability challenges of standard grades G-10 and G-11.
Factors to Consider When Choosing a Low Temp Plastic
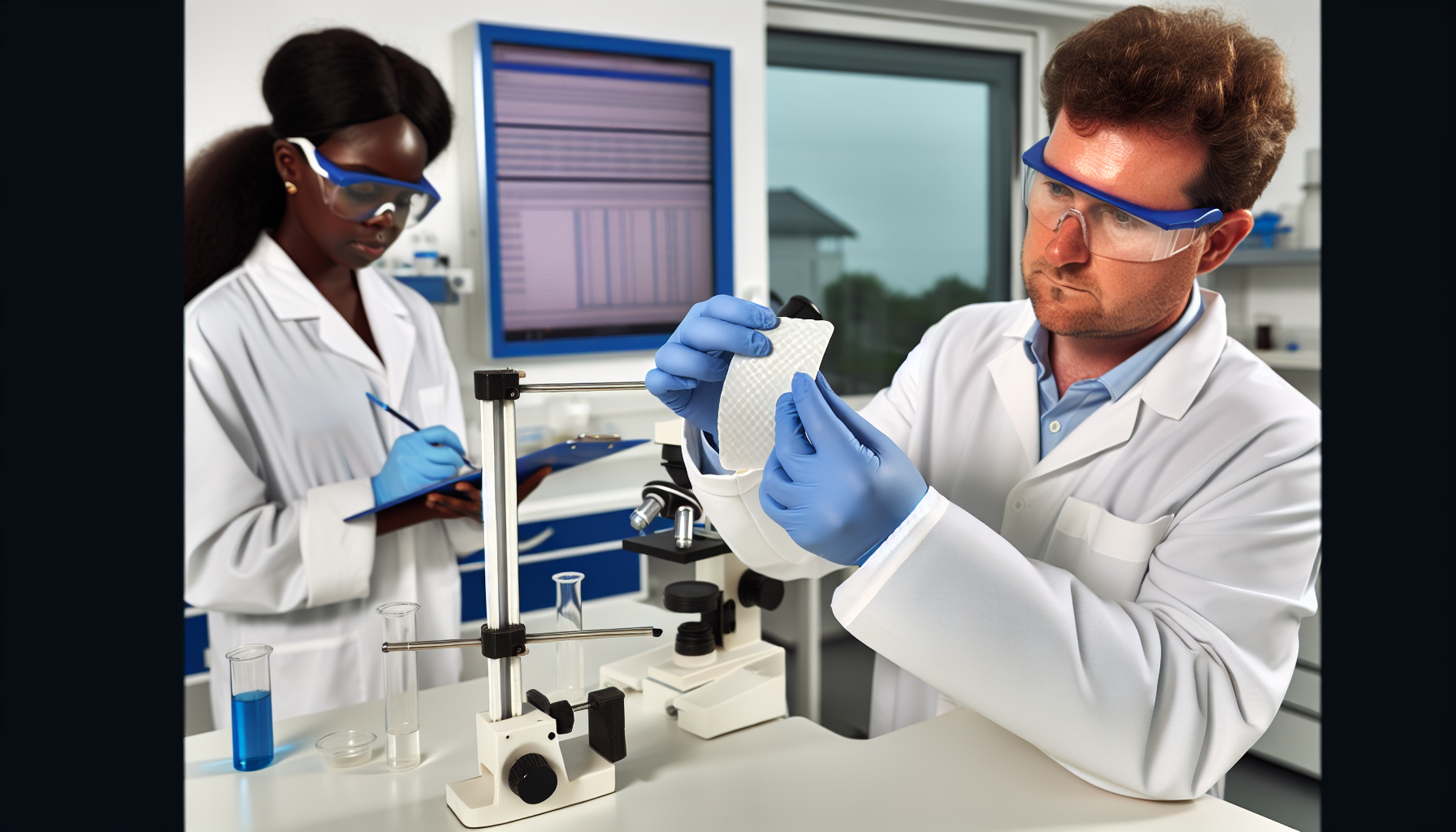
The decision to select the correct low temp plastic for a specific application should be made cautiously. It requires a deep understanding of the material’s properties and how they are affected by low temperatures. Certain factors, such as:
Chemical resistance
Thermal degradation
Operating temperature range
Impact strength and wear behavior
play a crucial role in this decision-making process.
Chemical resistance and thermal degradation
For low temp plastics, chemical resistance is an essential property. It prevents corrosion, weakening, and loss of functional abilities due to chemical attack over time. Factors like molecular structure, mechanical load, additives, solvent and chemical reagent concentration, duration of exposure, and temperature can influence a polymer’s chemical resistance.
Material selection must also take into account thermal degradation, as increasing temperature, chemical concentration, and exposure time can all contribute to a decrease in a polymer’s chemical resistance.
Operating temperature range
Another important factor to consider when choosing a low temp plastic is the operating temperature range. This range stipulates the limits within which a plastic can function without significant deterioration or loss of mechanical properties. Materials must be selected based on their ability to perform dependably across their entire operating temperature range, which may encompass both high and low extremes.
Thermoplastics like DuPont™ Vespel® that have consistent thermal expansion rates aid in designing parts that operate reliably over diverse temperature ranges.
Impact strength and wear behavior
Finally, the impact strength and wear behavior of a low temp plastic are critical considerations. Cold temperatures cause plastic molecular chains to shrink, affecting the mechanical properties and resulting in a temporary loss of elasticity, increased hardness, and brittleness.
Selecting a material that maintains high impact strength at low temperatures is crucial, especially for applications that require the material to resist breaking or cracking under stress.
Polymer Chemistry’s Role in Cold Resistance
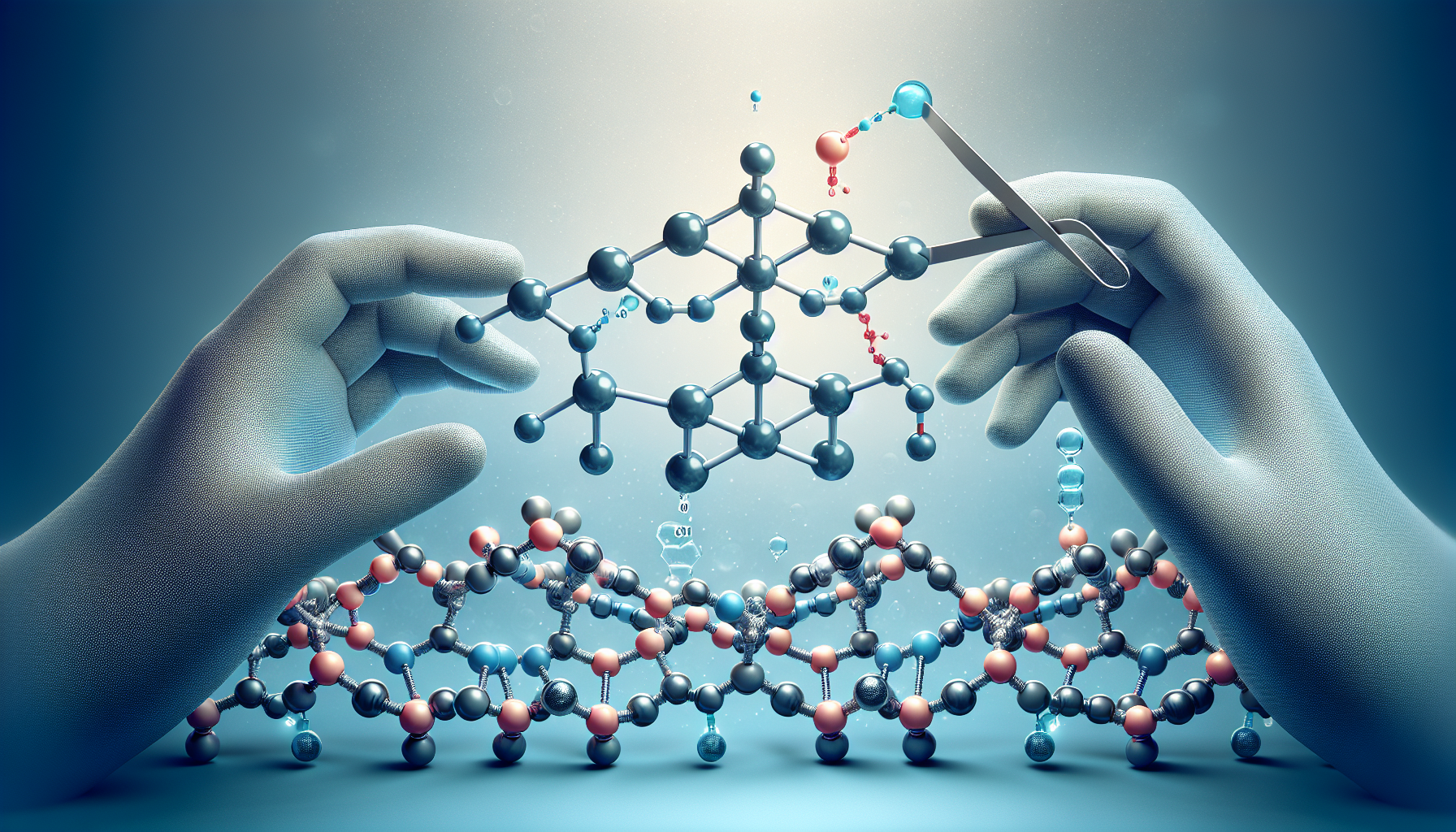
The cold resistance of a material significantly depends on its polymer chemistry. By manipulating factors such as plasticizer content, degree of crosslinking, and polymer chain flexibility, it’s possible to alter a polymer’s glass transition temperature (Tg) to enhance its cold resistance.
Let’s delve deeper into this concept and how high-performance polymers are designed to withstand high temperatures and extreme temperatures.
Understanding glass transition temperature
A polymer transitions from a hard, glassy state to a softer, rubbery state at the glass transition temperature (Tg). Understanding Tg is vital because it indicates the point where there can be drastic changes in a part’s mechanical properties and overall performance. Factors that affect a polymer’s Tg include:
Molecular weight
Chemical composition
Thermal history
Environmental factors such as pressure and moisture content
Therefore, a thorough understanding of Tg is crucial for selecting materials for applications that need to perform well under cold conditions.
Examples of high-performance polymers for extreme temperatures
Owing to their long-term thermal stability and creep resistance, high-performance polymers like:
Ultem®
Radel® R
PEEK
DuPont™ Vespel®
are essential in applications involving extreme low temperatures. These polymers maintain ductile behavior at low temperatures with low rates of thermal expansion, which is ideal for cryogenic applications.
Their electrical insulating properties are even retained in extreme cold, which is essential for maintaining performance in electronic applications within low-temperature settings.
Strategies for improving cold resistance in plastics
Improving the cold resistance of plastics involves a combination of material selection and engineering strategies. Adding plasticizers can make plastics more flexible at low temperatures by lowering the glass transition temperature (Tg). Conversely, increasing crosslinking or molecular weight can raise Tg and potentially improve cold resistance.
Furthermore, advancements in materials science, such as the integration of radiation resistance, reduction of cold creep, and improvement of impact strength, are helping to enhance the resistance of plastics to low temperatures.
Testing Methods for Evaluating Low Temp Plastics
Low temp plastics must undergo rigorous testing to ensure their reliability and performance in cold environments. Various methods and standards are used to evaluate the mechanical properties of plastics at low temperatures, helping manufacturers and engineers select the most suitable materials for their applications.
Importance of low-temperature testing
Understanding how plastics harden and become brittle in cold environments is crucial, and low-temperature testing provides this insight. These tests help manufacturers ensure the proper selection of plastics for applications subject to extreme cold, such as in aerospace and maritime environments.
Methods like using ultra-low deep freezers to evaluate plastic retraction, crystallization, brittleness, and stiffening are employed to test how plastics perform at significantly cold temperatures.
Common testing procedures
Common standards for low-temperature testing of plastics include:
ASTM D1329
ASTM D2137
BS ISO 2921
ISO 1432
ISO 3387
ISO 812
These tests evaluate properties such as brittleness at low temperatures and flexibility retraction.
Crystallization tests measure the impact of cold on plastics by monitoring hardness increases either after a set storage duration or determining the time it takes for a specified hardness increase to manifest.
Interpreting test results for material selection
The selection of materials for cold environments heavily relies on the results of these tests. Tensile testing, for instance, provides insights into a material’s tensile strength and Young’s modulus at different temperatures, helping to predict how a material will perform under stress in a cold environment.
Materials like PVDF, PE, and ABS, for instance, show an increase in tensile strength at lower temperatures, suggesting they could be suitable for use in cold environments.
Case Studies: Successful Applications of Low Temp Plastics
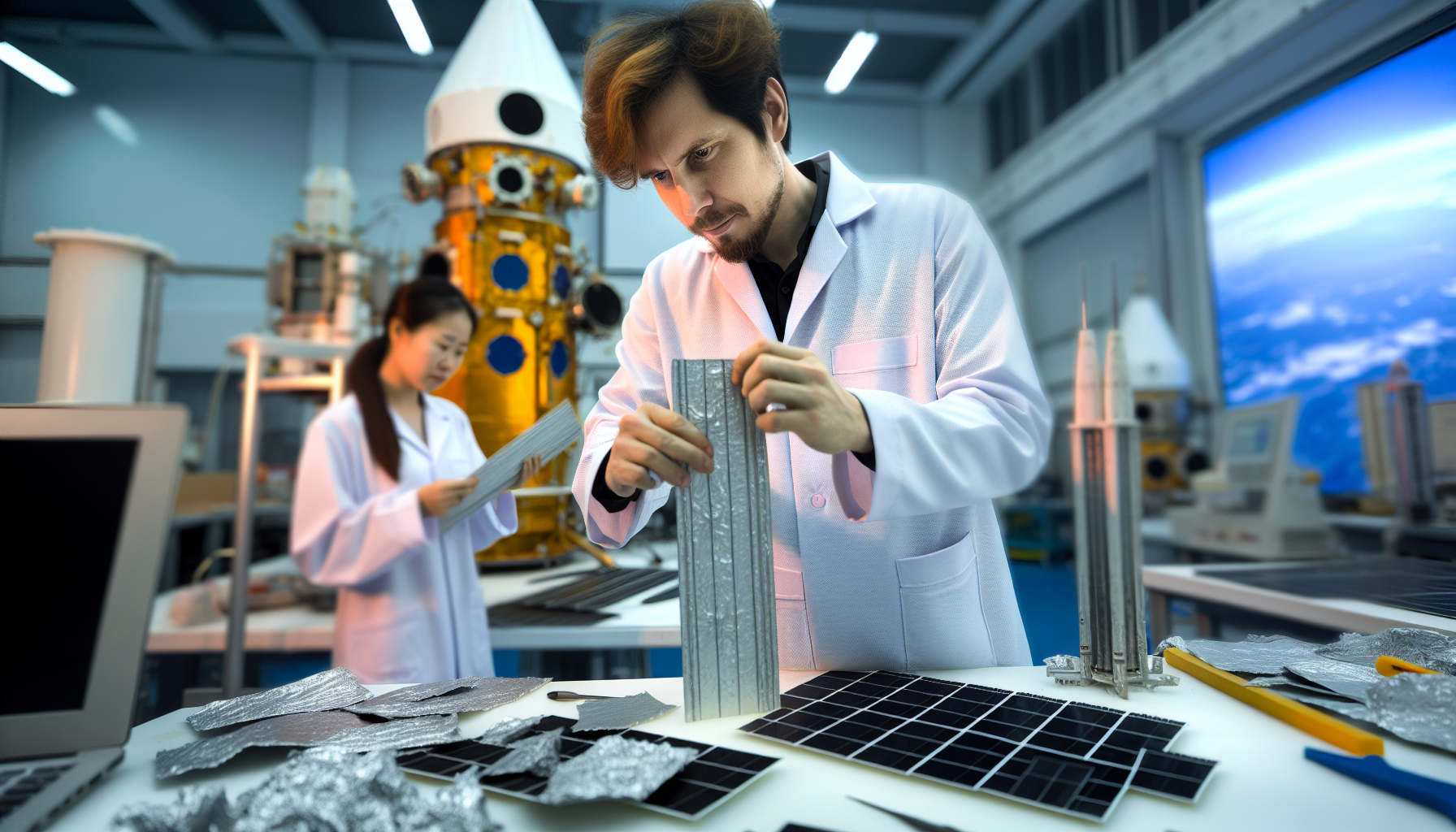
Exploring real-world examples where these materials have been successfully used in various industries provides a better understanding of the benefits of using low temp plastics. These case studies will demonstrate how low temp plastics perform in actual applications, providing a practical perspective on the theoretical concepts discussed so far.
Aerospace and cryogenic conditions
Low temp plastics and composites, due to their favorable properties at cold temperatures, find application in the aerospace industry, particularly in structures of satellites, spacecraft, and launch vehicles. Support elements such as struts and straps, as well as electrical insulation for superconducting magnets, are made from materials that retain their properties in cryogenic temperatures.
Materials like PEEK and Vespel® are commonly utilized as bearings, seals, and thermal insulators in environments with extremely cold temperatures.
Shipping industry and cold-resistant piping systems
In the shipping and offshore industries’ plastic piping systems, high performance plastics like polyethylene (PE), acrylonitrile butadiene styrene (ABS), and polyvinylidene fluoride (PVDF) are commonly utilized as plastic materials. These materials offer durability and corrosion resistance in demanding marine environments. Selected for their high impact strength at low temperatures, these polymers are also chosen for their resistance to erosion and decay under seawater conditions.
These materials are subjected to mechanical tensile tests at different temperatures and strain rates to evaluate their suitability for low-temperature environments, particularly for applications such as pipes for liquefied natural gas, which is stored and transported at -163 °C.
Outdoor equipment and extreme weather conditions
Materials that can maintain their structural integrity and function even in extremely cold weather are required for outdoor gear and equipment. Material choices for these conditions must consider the possibility of plastic becoming brittle at low temperatures. Plastics used for cold weather gear must have low-temperature impact resistance to avoid breakage.
Polycarbonate is highly suited for outdoor usage in extreme weather due to its low-temperature flexibility and impact resistance.
Summary
In conclusion, the selection of the right plastic for use in low temperature environments is a complex task that requires a deep understanding of polymer chemistry, material properties, and the impact of cold temperatures on these properties. By taking into account factors such as thermal degradation, chemical resistance, operating temperature range, and impact strength, and employing appropriate testing methods, manufacturers and engineers can make informed decisions in selecting the most suitable low temp plastics for their applications. As we continue to push the boundaries of human endeavor into ever more extreme environments, the role of these materials will only become more critical.
Frequently Asked Questions
What plastic can withstand low temperatures?
LDPE and HDPE are plastics that can withstand low temperatures, making them suitable for outdoor applications in cold regions. They are commonly used for items such as pipes, cables, and plastic bags in cold environments.
What plastic melts at low temperatures?
Polyethylene (PE) is a type of plastic that melts at a low temperature, usually around 105°C to 135°C (221°F to 275°F). It is commonly used for various applications due to its low melting point.
What are low temperature thermoplastics?
Low temperature thermoplastics (LTTPs) are activated using relatively low heat, typically water between 60–70°C or 140°-170°F. This is in contrast to high temperature thermoplastics, which require higher activation temperatures.
What is G10 Cryo and why is it suitable for low-temperature applications?
G10 Cryo is a glass epoxy material that is suitable for low-temperature applications due to its excellent electrical properties, chemical resistance, and high strength.
What role does polymer chemistry play in a material’s cold resistance?
Polymer chemistry can influence a material’s cold resistance by adjusting factors such as plasticizer content, degree of crosslinking, and polymer chain flexibility, which can alter a polymer’s glass transition temperature (Tg) to enhance its cold resistance.