Understanding the compatibility of chemicals is essential for safety in any space where chemicals are used. This guide explains the pivotal concepts you need to know to prevent dangerous chemical interactions. We’ll give you the tools to identify hazardous combinations, safely store chemicals, and utilize compatibility charts effectively, ensuring a secure environment in your laboratory, plant, or classroom.
Key Takeaways
Chemical compatibility is crucial for safety, requiring an understanding of chemical reactions and appropriate methods for storing and handling chemicals to prevent dangerous outcomes such as fires and toxic releases.
Chemical compatibility charts are key tools for ensuring safe interaction between chemicals and materials, using a rating system from ‘A Excellent’ to ‘D Severe Effect’ to guide storage and handling practices.
Regular safety precautions, including the use of Personal Protective Equipment (PPE) and proper storage measures, are necessary to prevent hazardous incidents in the handling and storage of chemicals.
Understanding Chemical Compatibility
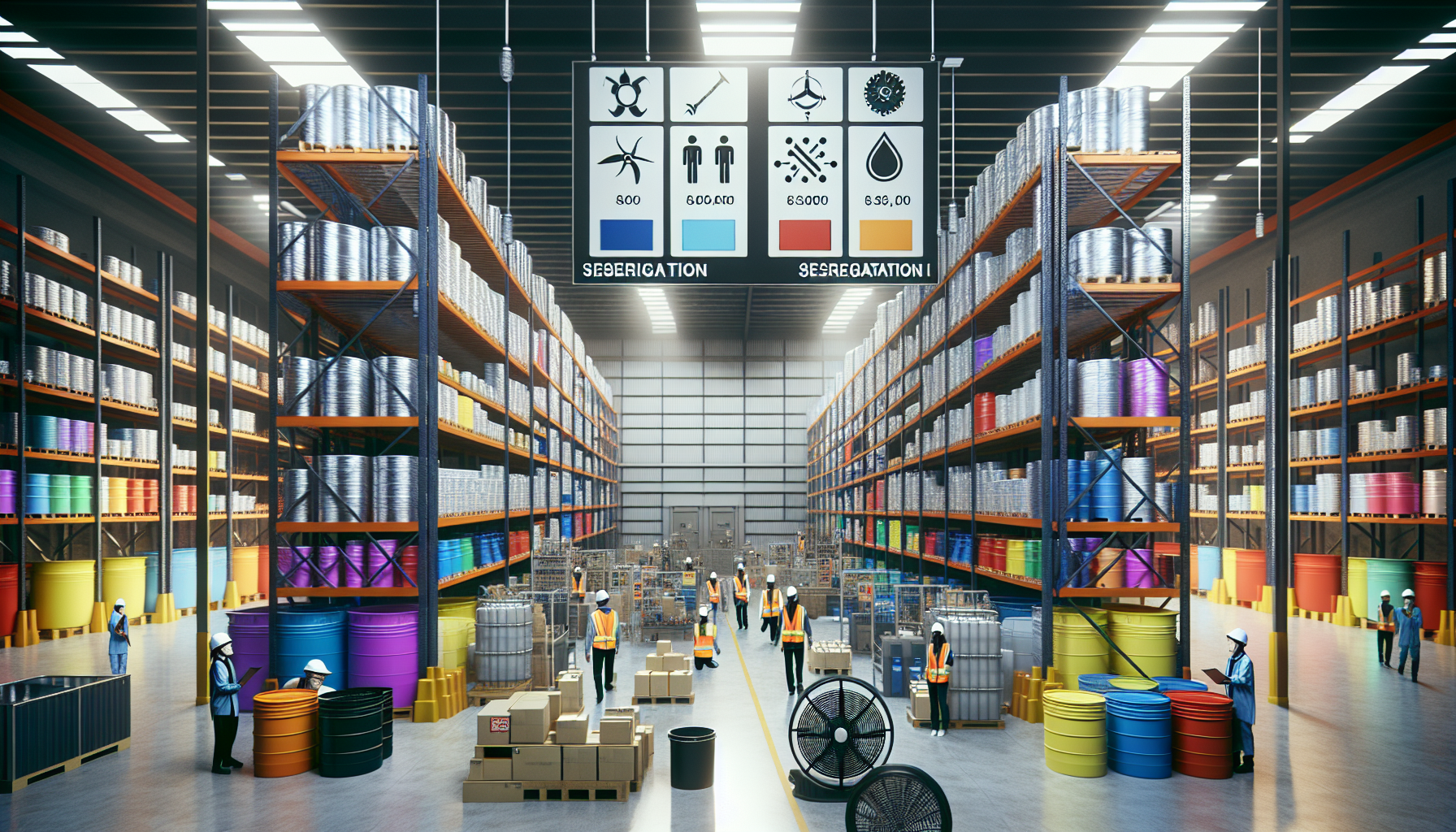
Chemical compatibility is a bit like a dance. Each chemical has its own dance steps, its own rhythm, and its own behavior. When two chemicals come together, the question is, can they dance together without stepping on each other’s toes? Or will their interaction cause a commotion on the dance floor?
The consequences of a disastrous chemical dance-off can range from:
Excessive heat generation
Over pressurization
Release of toxic gases
Full-blown fire
In order to maintain a safe environment, it is crucial to comprehend the characteristics of each chemical, their reactions, and how they interact with others. This includes understanding how they respond to other substances and the appropriate methods for storing chemicals. For example, if a tango dancer (a specific chemical) has a tendency to spin wildly (a certain chemical behavior), it’s best not to pair them with a waltz dancer (another chemical) who prefers a slower pace (different chemical behavior). In other words, it’s essential to understand chemical behavior during handling and storage to ensure safety. With the chemical behavior listed, one can make informed decisions on how to handle and store these chemicals safely.
Identifying Incompatible Chemicals
Recognizing incompatible chemicals is a vital measure in maintaining a safe environment. It’s like being a vigilant DJ at a dance party, ensuring that the right songs are played to keep the dance floor safe and enjoyable. Certain chemical combinations, like certain dance pairings, can be dangerous. For instance, mixing acids and bases or acids and bleach can generate excessive heat, toxic fumes, or even result in fires. Similarly, nitric acid or perchloric acid can react violently when in contact with organic materials, leading to heat generation or fires.
Hence, the appropriate separation of incompatible materials, using physical barriers or distance, is necessary to prevent any contact between them. Storing chemicals alphabetically may seem orderly, but it may result in hazardous pairings. For example, storing Sulfuric Acid next to Sodium Nitrite could increase the risk of acid gas formation in case of accidental leaks or structural failures. It’s like ensuring that two dancers with conflicting styles don’t end up doing a duet!
The Principles of Chemical Storage
Similar to how dancers need an appropriate stage for their performance, chemicals also need a suitable area for storage to guarantee safety. The physical layout of chemical storage should prevent chemicals from being stored above eye level, specifically avoiding top shelf storage, to minimize spill risks and ensure easy handling. Shelving must be sturdy and secured to walls, with an anti-roll lip to avoid container falls. In simpler terms, think of it as providing each dancer with a well-lit, sturdy stage, free from any potential hazards.
Storing chemicals is not solely about setting them in a secured area. It also involves considerations like:
Temperature control
Ignition prevention
Adequate ventilation
Clear identification
Proper segregation to manage the risks of incompatible materials
Different classes of chemicals must be stored according to their reactivity, similar to how different genres of music are segregated in a music library. This separation of corrosives from flammables, acids from bases, and provisions for secondary containment help avert chemical reactions. In essence, the principles of chemical storage ensure that each dancer is in the right place, at the right time, doing the right moves.
Decoding the Chemical Compatibility Chart
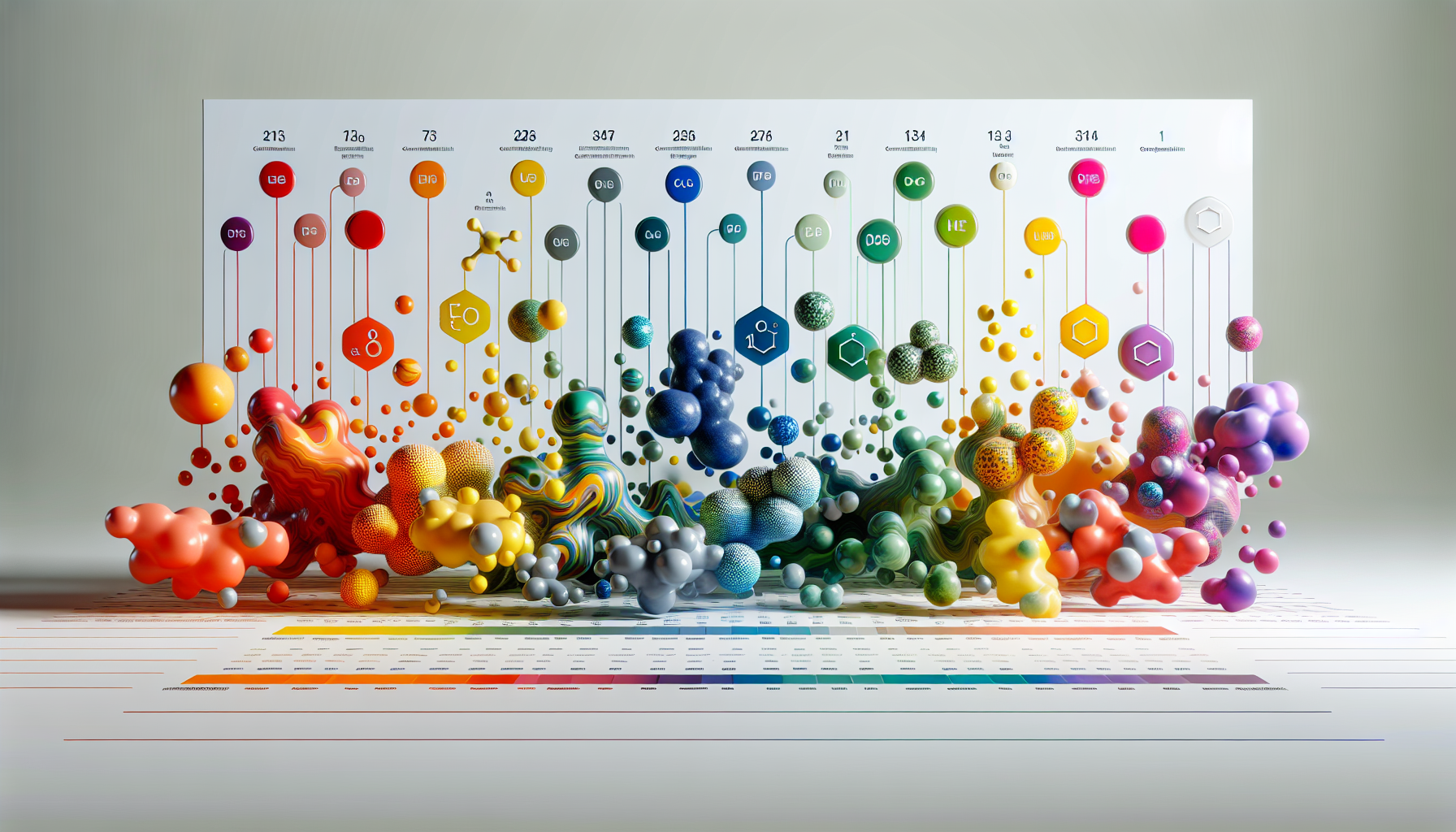
Entering the realm of chemicals might seem like traversing a complex labyrinth, particularly when attempting to comprehend the interactions between different chemicals and materials. This is where the chemical compatibility chart comes into play, serving as a crucial reference tool for appropriate chemical compatibility. Much like a dance card at a ball, the chart lists out which chemical ‘partners’ can ‘dance’ safely with which materials. Working with these charts ensures safe storage and handling, preventing the use of incompatible chemical combinations.
Manufacturers provide these charts, and they are customized to demonstrate the compatibility of certain components within pumps or any systems handling chemicals. Typically, they are organized with chemicals listed alphabetically in the left column and various materials listed along the top row, allowing for easy comparison to assess compatibility.
So, the next time you find yourself in the labyrinth of chemical compatibility, remember that the compatibility chart is your trusted guide, helping you navigate the maze with ease.
Interpreting Ratings: From ‘A Excellent’ to ‘D Severe Effect’
Similar to how a dance performance is evaluated on a scale from poor to excellent, a comprehensive rating system is used to assess the compatibility between chemicals and materials. An ‘A’ rating, akin to a standing ovation, implies nearly complete material inertness, with the material showing negligible effects when exposed to the specified chemical. ‘B’ signifying a moderate effect, may lead to minor material corrosion or discoloration and marginally affect mechanical properties. In this context, it’s important to b good at understanding these ratings to make informed decisions.
On the other hand, a ‘C’ rating denotes partial chemical attack or absorption, potentially resulting in swelling of the material and reduced component lifespan, akin to an average performance. ‘D’ indicates a lack of resistance to chemical exposure, leading to immediate and severe damage, rendering the material and chemical combination unsuitable, much like a disastrous performance. Understanding these ratings ensures that you can conduct the chemical ‘dance’ safely and effectively.
Factors Affecting Compatibility: Temperature and Concentration
Similar to how the tempo and style of music can alter the mood of a dance, factors like temperature and concentration can cause variations in the compatibility of materials with chemicals. Resistance to chemicals is a function of both temperature and concentration, and the compatibility chart usually assumes an ambient temperature of about 70°F (21°C) unless otherwise noted. A material’s resistance to a chemical can change depending on the concentration of the chemical it comes into contact with.
Variations in temperature, concentration, and additional environmental conditions can affect the performance of materials and their compatibility with chemicals. For instance, Hastelloy C is compatible with:
Sulphuric Acid at 98% concentration and up to 60°C
Sulphuric Acid at 80% concentration up to 20°C
Hydrochloric acid at 10% concentration at 20°C
Hydrochloric acid with limited resistance at 40°C
Like a dancer who can perform a perfect pirouette in practice but falters in a different environment, chemical compatibility can vary under different conditions, such as the chemical effect during a C Fair event.
Selecting Materials for Chemical Exposure
Choosing the right partner is vital when dealing with chemicals. Just as a dancer chooses shoes with the right grip for a performance, selecting the right material that can withstand chemical exposure is crucial. Chemical resistance is essential when selecting materials for exposure to chemicals, with thermoplastics and elastomers particularly gauged for their resilience against chemical damage.
To prevent corrosion in pump components in contact with chemicals, manufacturers can employ protective coatings or construction from inherently corrosion-resistant materials. Materials selected based on chemical compatibility must also be assessed for wear when in contact with non-lubricating fluids. It is recommended to conduct initial suitability testing of plastics in specific chemical environments to ensure long-term performance and safety, as chemical resistance can vary and slight corrosion may still occur.
Remember, just as a pair of dancing shoes is chosen for specific dance forms, materials should be selected based on the specific chemicals they will be exposed to.
Plastics and Chemical Resistance
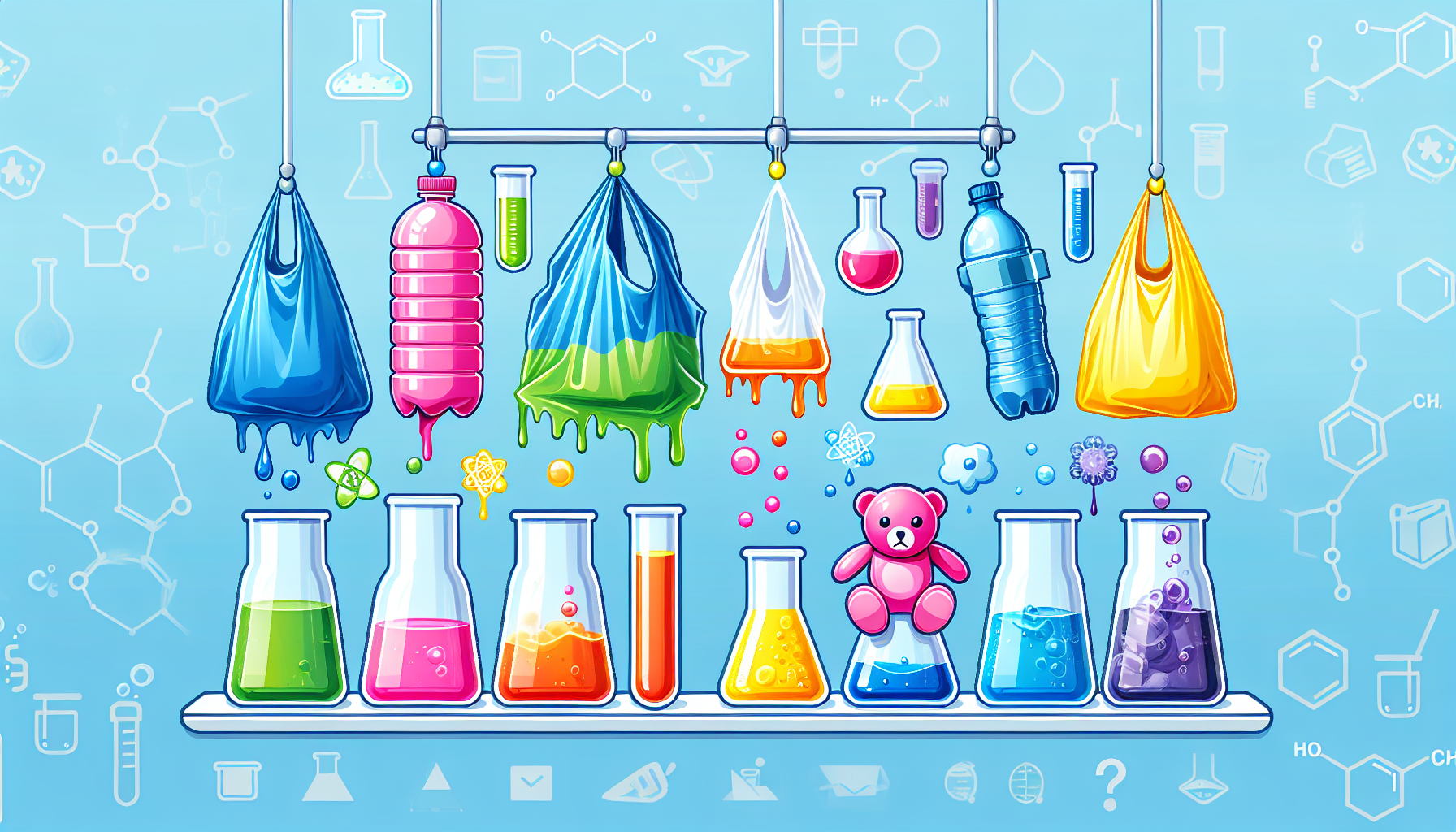
Like professional dancers, plastics are also versatile. They can adapt and resist a wide variety of chemical interactions, including those with mineral acids and organic acids. However, incompatible chemical interactions with plastics can lead to detrimental effects such as softening or swelling of the material. The resistance of plastics to chemicals is well-documented, with plastics showing various levels of resistance to chemicals such as acetic acid, hydrochloric acid, hydrogen peroxide, and sulphuric acid.
Just as a dancer’s resistance to fatigue varies with the intensity and duration of the dance, a plastic’s resistance to a chemical can change depending on the severity and duration of exposure. It’s this ability to resist and adapt to different chemicals that make plastics a popular choice for chemical exposure.
Conducting an Initial Test
Similar to how a dancer practices before a performance, it is important to conduct initial testing of materials with chemicals to guarantee safety and compatibility prior to permanent installation. Compatibility chart ratings are based on short-term exposure, typically 48 hours, and do not guarantee long-term suitability.
The information on chemical compatibility charts is not assured for accuracy or completeness, making personal validation of this information under application-specific conditions crucial. Failure in thermoplastics such as environmental stress cracking can occur under chemical exposure, stressing the importance of testing for such failure modes. This step is akin to the dress rehearsal before the final performance, ensuring that everything goes smoothly when it truly matters.
Chemical Compatibility and Safety Precautions
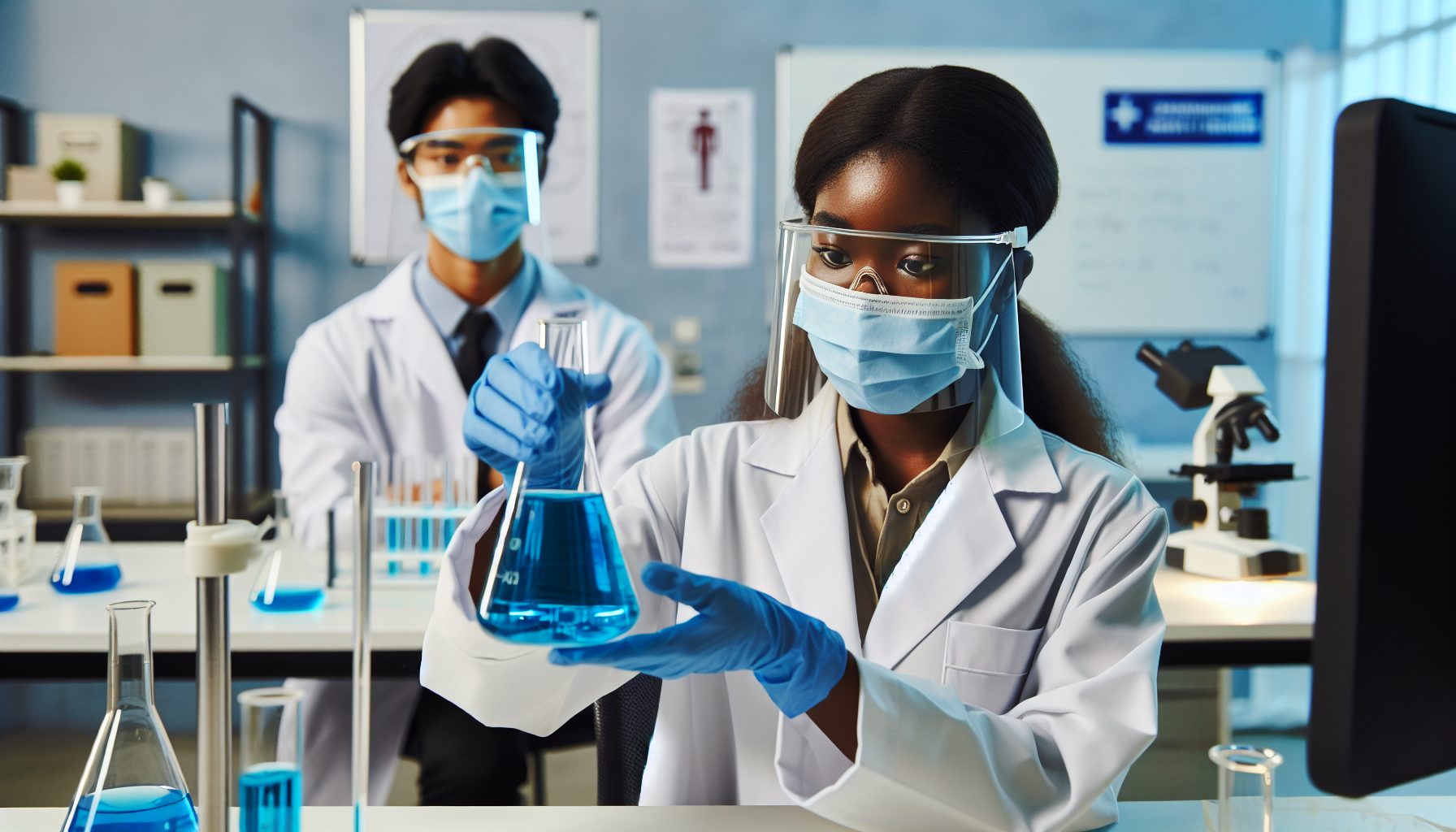
In the world of chemicals, safety takes the lead. Regular inspections are necessary to identify hazards such as leaking containers, spilled chemicals, temperature extremes, and blocked exits to ensure safety in chemical storage areas. Just as a dancer wears appropriate attire and shoes to protect themselves during a performance, handling chemicals requires the use of Personal Protective Equipment (PPE) such as pants, closed-toe shoes, lab coat, chemically resistant gloves, and eye protection.
Choosing suitable gloves is critical for handling chemicals, as effectiveness varies. Glove manufacturers provide chemical resistance guides to aid in selection. Additional PPE such as:
Chemical splash goggles
Face shield
Fire-resistant lab coat
Kevlar gloves covered with neoprene gloves
is needed when handling highly reactive substances like pyrophorics. Respirators may be required to protect against dust and fumes if other administrative and engineering controls are inadequate. Respirator use must be accompanied by medical evaluations, fit testing, and training.
Following a Laboratory Hazard Assessment can help identify which proper PPE should be used for specific chemical handling activities. Confirming chemical resistance and suitability of materials for specific chemicals is crucial, though not legally guaranteed, necessitating consultation with technical teams for selecting materials.
Establishing Suitable Guards
Just as safety measures are necessary for every dance performance, handling chemicals also demands appropriate guards and protections. Using suitable guards and personal protection is critical when handling chemicals because unexpected reactions can occur due to variations in handling conditions, leading to serious injury. Suitable guards in a laboratory setting include both administrative and engineering controls designed to reduce workers’ exposure to hazardous chemicals and fumes.
Chemical storage areas are equipped with clear warning signs such as:
‘No Smoking’
‘Flammable Liquids’
‘Acids’
‘Corrosives’
‘Poisons’
These signs provide critical information and ensure the protection of workers. Just as a dance stage is marked with safety lines and signs to avoid accidents, chemical handling areas should be clearly marked with suitable warnings and guards.
Personal Protective Equipment (PPE) Recommendations
Just as a dancer selects their attire based on the dance form, the choice of Personal Protective Equipment (PPE) should be based on the chemicals involved and the specific tasks at hand. For general chemical handling, it is recommended to wear:
Pants
Closed-toe shoes
Chemically resistant gloves
A laboratory coat
Eye protection
Glove selection should be based on the chemicals being handled, with the appropriate type determined by consulting the glove manufacturer’s chemical resistance guides.
When handling pyrophorics, use the following personal protective equipment (PPE):
Chemical splash goggles
A face shield
Flame-resistant gloves covered with disposable neoprene gloves
A Nomex® lab coat
Appropriate footwear
Respiratory protection is necessary when exposure to dust and fumes exceeds permissible limits, which requires medical evaluation, fit testing, and proper training before use. The selection of PPE is as important as knowing your dance steps, as it not only ensures safety but also enhances performance.
Case Studies: Real-World Chemical Compatibility Scenarios
Just as we gain insights from others’ performances, real-world scenarios of chemical compatibility can provide valuable lessons. These scenarios, both successful and cautionary, serve as powerful lessons, emphasizing the importance of understanding chemical compatibility and implementing appropriate safety measures. Whether it’s a pharmaceutical company avoiding cross-contamination or the semiconductor industry ensuring product integrity, these success stories underscore the importance of proper compatibility measures.
On the flip side, there are cautionary tales that highlight the consequences of neglecting chemical compatibility. Instances such as an incompatible chemical being stored in a polyethylene container leading to a hazardous spill, or a laboratory experiencing an explosion due to improper storage, serve as stark reminders of the dangers of disregarding chemical compatibility.
Success Stories: Proper Compatibility Measures
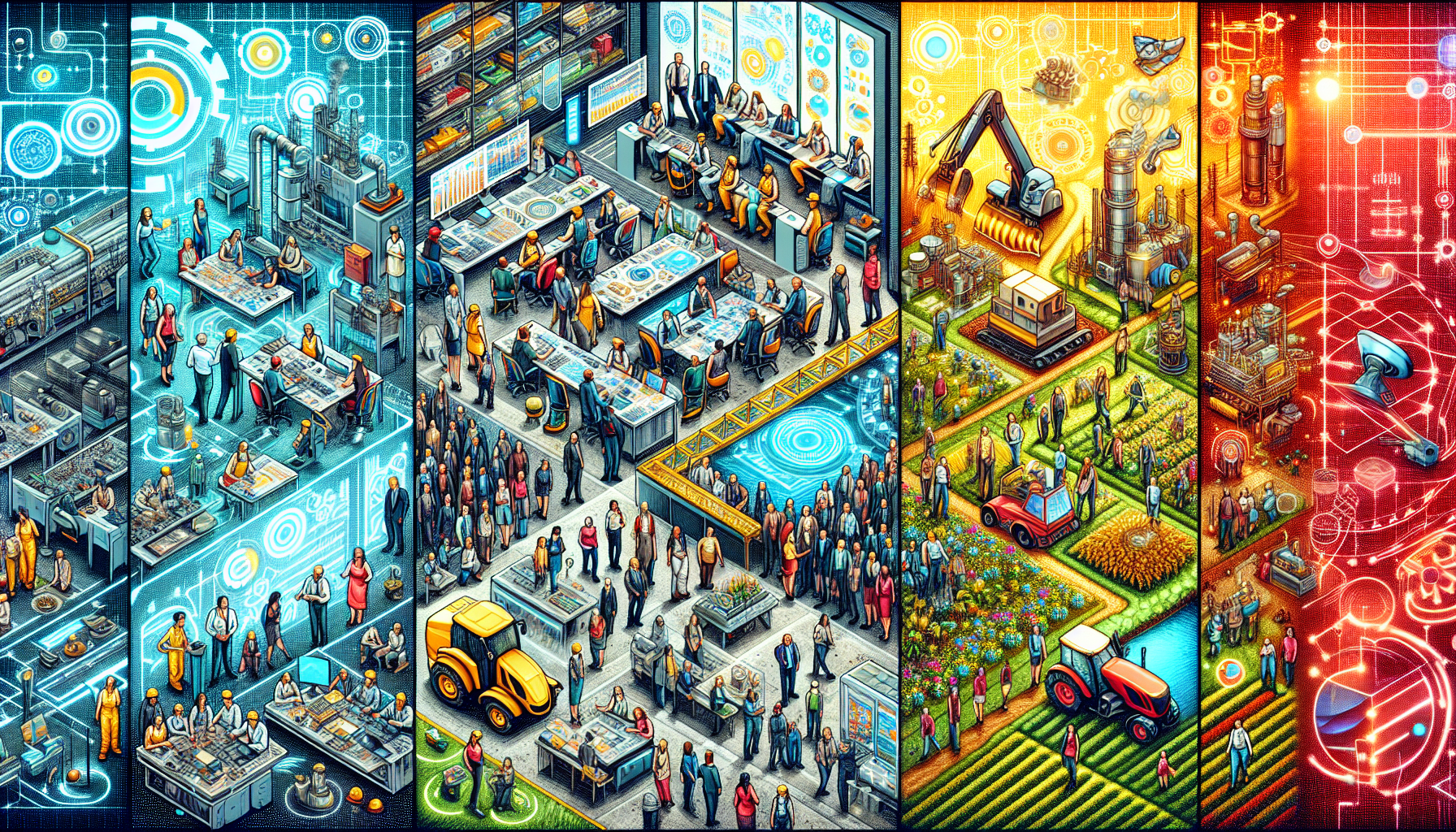
Implementing compatibility measures successfully can enhance safety and efficiency. Here are some examples of how compatibility measures have been implemented in different industries:
A pharmaceutical company integrated a chemical compatibility system, reducing hazardous reactions in the lab.
In a petrochemical plant, the application of compatibility measures prevented equipment corrosion and subsequent operational disruptions.
Proper segregation of oxidizing agents from flammable materials in a warehouse effectively prevented a potential fire outbreak.
The utilization of specific types of PPE for handling chemicals with high reactivity ensured the safety of workers in a chemical manufacturing facility. Following best practices for chemical storage, a research institution avoided degradation of sensitive compounds and maintained the integrity of scientific results. These success stories serve as a testament to the importance and effectiveness of proper compatibility measures.
Cautionary Tales: The Consequences of Neglect
While success stories inspire us, cautionary tales act as vivid reminders of the potential hazards of overlooking chemical compatibility. Neglecting chemical compatibility can lead to the formation of highly unstable or explosive compounds. Reactive combinations such as peroxides with organics or metals, inorganic nitrate salts with organics, and ammonium nitrate with organic material are known to form highly dangerous compounds.
Mixing azides with metals is an example of a hazardous practice as it can generate shock-sensitive salts capable of detonation. These cautionary tales underscore the importance of understanding and respecting the dance of chemicals, reminding us that neglecting chemical compatibility can lead to dangerous reactions and accidents.
Summary
Navigating the world of chemical compatibility is akin to learning a complex dance. It requires understanding the individual ‘dancers’ (the chemicals), knowing how to pair them correctly, and ensuring they have the right ‘stage’ (storage conditions) to perform. From identifying incompatible chemicals to decoding the chemical compatibility chart and selecting the right materials for chemical exposure, each step is critical in ensuring safety and preventing accidents.
The dance of chemicals is intricate, but with the right knowledge and precautions, it can be safely navigated. Whether you’re a laboratory technician, a chemical engineer, or anyone dealing with chemicals, understanding chemical compatibility is not just crucial—it’s non-negotiable. So, as you continue your dance with chemicals, remember the importance of understanding compatibility, taking the necessary safety precautions, and always being prepared for the unexpected. Because in the dance of chemicals, every step matters.
Frequently Asked Questions
What is meant by chemical compatibility?
Chemical compatibility refers to the resistance of materials to corrosion and chemical damage when exposed to different substances. It is a measure of how stable a substance is when mixed with another substance.
What is the chemical compatibility chart?
The Chemical Compatibility Chart is a useful tool for determining which materials are suitable for use with different chemicals, helping to ensure safety and effectiveness in various applications.
What are the five compatibility groups for chemicals in stores?
Chemicals in stores are typically organized into five compatibility groups, as required by GT EHS. This helps ensure safe storage and handling of chemicals.
How can I identify incompatible chemicals?
You can identify incompatible chemicals by referring to chemical compatibility charts provided by manufacturers, which help determine the resistance of materials when in contact with different chemicals. Be sure to consult these charts before using any chemicals together.
What factors affect the compatibility of chemicals?
The compatibility of chemicals is affected by factors such as temperature and concentration, which can alter a material’s resistance to the chemicals it encounters. These factors play a crucial role in determining the interaction between different chemicals.