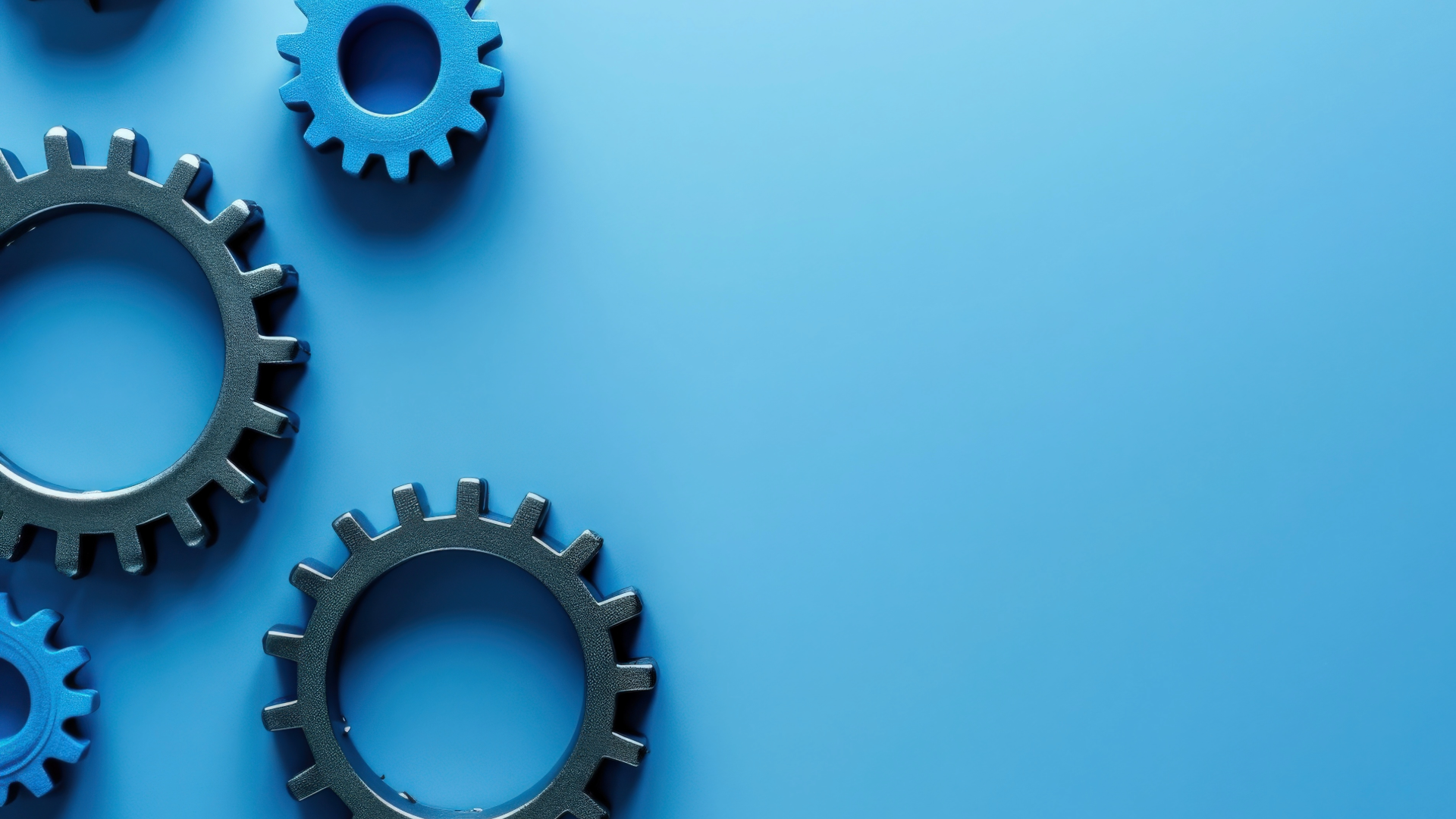
Composite materials are increasingly being recognized as a superior option for gears over metals in a variety of applications, thanks to several key advantages. Reduced weight, lower cost, improved design flexibility, and enhanced corrosion resistance are some of the common reasons for this shift. But for many, the deciding factor is the silence of it all. Noise reduction is a standout benefit that sets composite gears apart, offering a quieter and more efficient alternative to traditional metal gears.
The Common Advantages of Composite Gears
Weight Reduction
One of the primary benefits of composite gears is their significantly lower weight compared to metal gears. This lightweight nature makes composite gears ideal for:
- Weight-sensitive applications like drones and portable machinery
- Reducing inertia and improving dynamic performance
- Lowering energy consumption
- Extending the operational life of motors and bearings
Cost-Effectiveness
Composite gears can also provide a more economical solution. Their manufacturing processes, such as molding or extrusion, are generally faster and less energy-intensive than those used for metal gears. They also eliminate the need for expensive alloys or specialized treatments, leading to overall lower production costs.
Corrosion Resistance
Unlike metal gears, which can be susceptible to rust and corrosion, composite gears offer inherent resistance to corrosion. This makes them particularly suitable for environments involving exposure to chemicals or moisture, such as marine or industrial applications. This advantage leads to greater reliability and reduces the need for additional protective measures.
Design Flexibility
Composite materials offer greater design flexibility, enabling:
- More complex and customized shapes and structures
- Integration of additional functionalities, such as damping features or hybrid designs
The Quiet Advantage: Noise Reduction
Among all the benefits, noise reduction stands out as a key reason why composites are favored for gear production, particularly in industries like aerospace and automotive where minimizing noise and vibration is crucial.
Lower Noise Levels
Composite gears generally produce less noise and vibration compared to their metal counterparts. Their inherent damping properties absorb vibrations and reduce noise transmission effectively. In fact, studies have shown that composite gears can be 2-4 dB quieter than comparable metal gears. This difference can have a significant impact in applications where noise levels are a concern.
Noise Reduction Mechanisms
Several factors contribute to the quieter operation of composite gears:
- The lower density and elastic modulus of composites result in lower impact forces during tooth engagement, which helps reduce noise.
- Composite materials have a natural ability to absorb and dissipate vibrational energy more effectively than metals.
- The ability of composite gear teeth to slightly deform helps maintain smoother tooth contact, which further reduces noise.
Design Flexibility for Noise Control
Composite gears allow for greater optimization in design to further reduce noise. Complex tooth profiles and integrated damping features can be manufactured more easily compared to metal gears. Additionally, hybrid metal-composite designs can combine the strength of metal with the noise-reducing properties of composites, offering a balanced solution.
Additional Benefits and Applications
Beyond noise reduction, composite gears offer other advantages that indirectly contribute to quieter and more reliable operation:
- Lighter weight reduces overall system vibrations.
- No need for lubrication eliminates the noise caused by inadequate or inconsistent lubrication.
- Corrosion resistance helps maintain smooth operation over time without degradation.
Composite gears are particularly advantageous in low to medium load applications, environments where lubrication is difficult or undesirable, and situations requiring corrosion resistance or chemical inertness. While composite gears excel in many areas, they may not be suitable for all scenarios. High-load, high-temperature, or high-precision environments may still require metal gears.
The Bottom Line
Composite gears offer a compelling alternative to metal gears, especially when noise reduction, weight savings, and design flexibility are critical – discover other reasons engineers and products designers choose thermosets. While their initial costs might be higher, the long-term benefits in terms of reduced maintenance, efficiency, and performance often outweigh these initial investments. As advancements in materials continue, composites are becoming an increasingly attractive option for gear design, delivering the silence and performance many industries are seeking.