Are you looking to maximize efficiency and precision in your high volume plastics machining operations? Look no further! In this blog post, we dive deep into the world of high volume plastics machining and the Production Part Approval Process (PPAP). Discover the secrets to optimizing your production process, leveraging advanced technologies, and maintaining quality control with appearance approval reports and inspection. Get ready to supercharge your high volume plastics machining process with expert insights and strategies!
Key Takeaways
- High volume plastics machining is a process used to manufacture large quantities of plastic parts with specialized techniques and machinery.
- CNC technology, Statistical Process Control (SPC), calibration of materials and equipment, validation testing, assembly processes optimization are strategies for success in high volume plastic machining.
- Atlas Fibre provides advanced equipment, quality control systems & customer service culture making them an ideal partner for prototype through production projects.
Understanding High Volume Plastics Machining
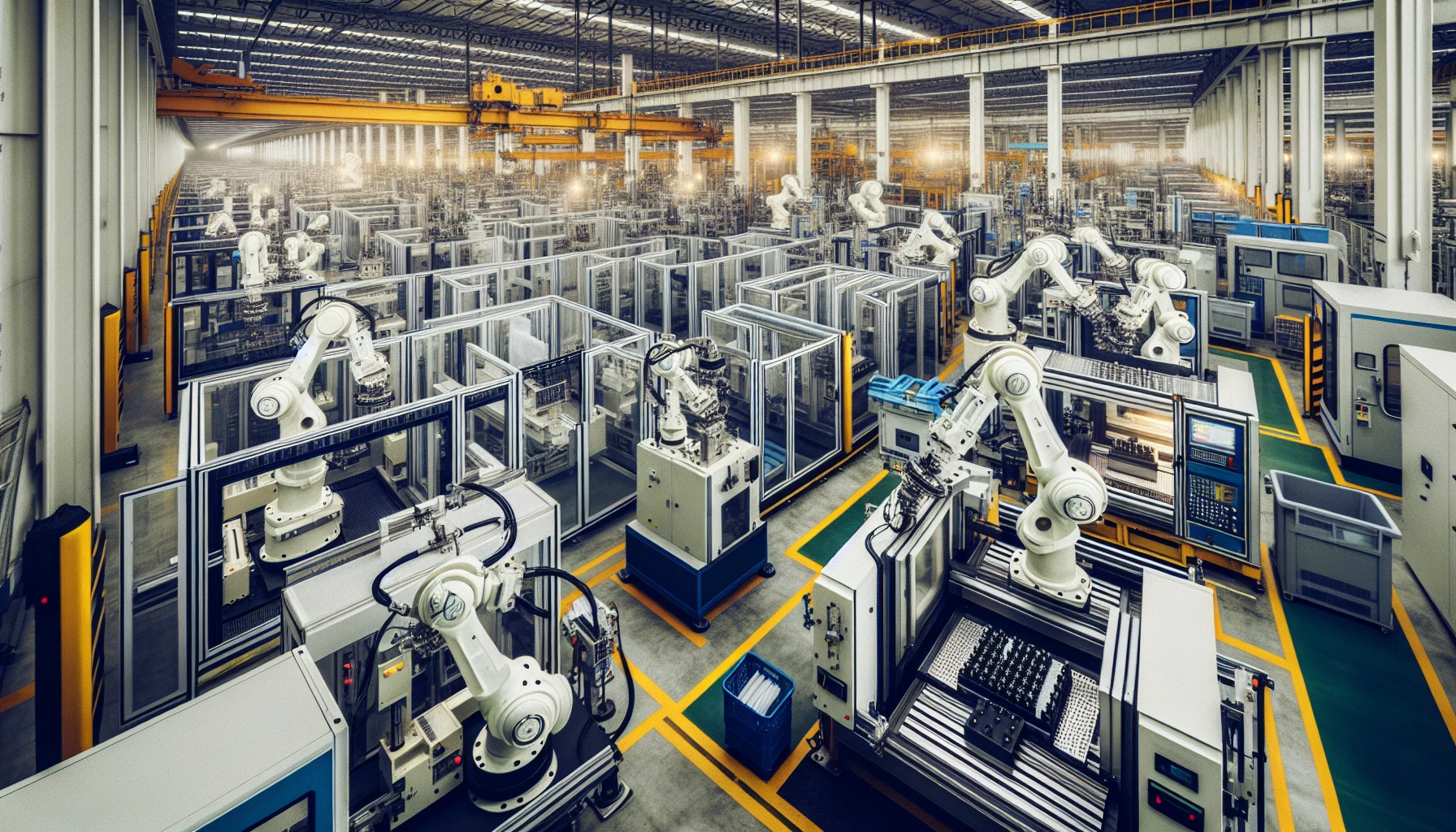
High volume plastics machining refers to the process of manufacturing plastic parts in large quantities using specialized techniques and machinery, such as CNC machining. This process is widely employed in industries that require a high volume of plastic parts, such as automotive, electronics, and consumer goods manufacturing. Process failure mode analysis can be used to identify potential risks and improve the efficiency of the machining process.
Some specialized techniques involved in high volume plastics machining include minimizing clamping forces, utilizing the correct cutting tool, and cooling. Equipment used in high volume plastics machining includes rotary transfer machines, multispindles, and Swiss-type lathes. Efficiency and accuracy in high volume plastics machining are maintained through advanced CNC machining, tooling optimization, process monitoring, and control, among other strategies.
The Role of CNC Plastic Machining in High Volume Production
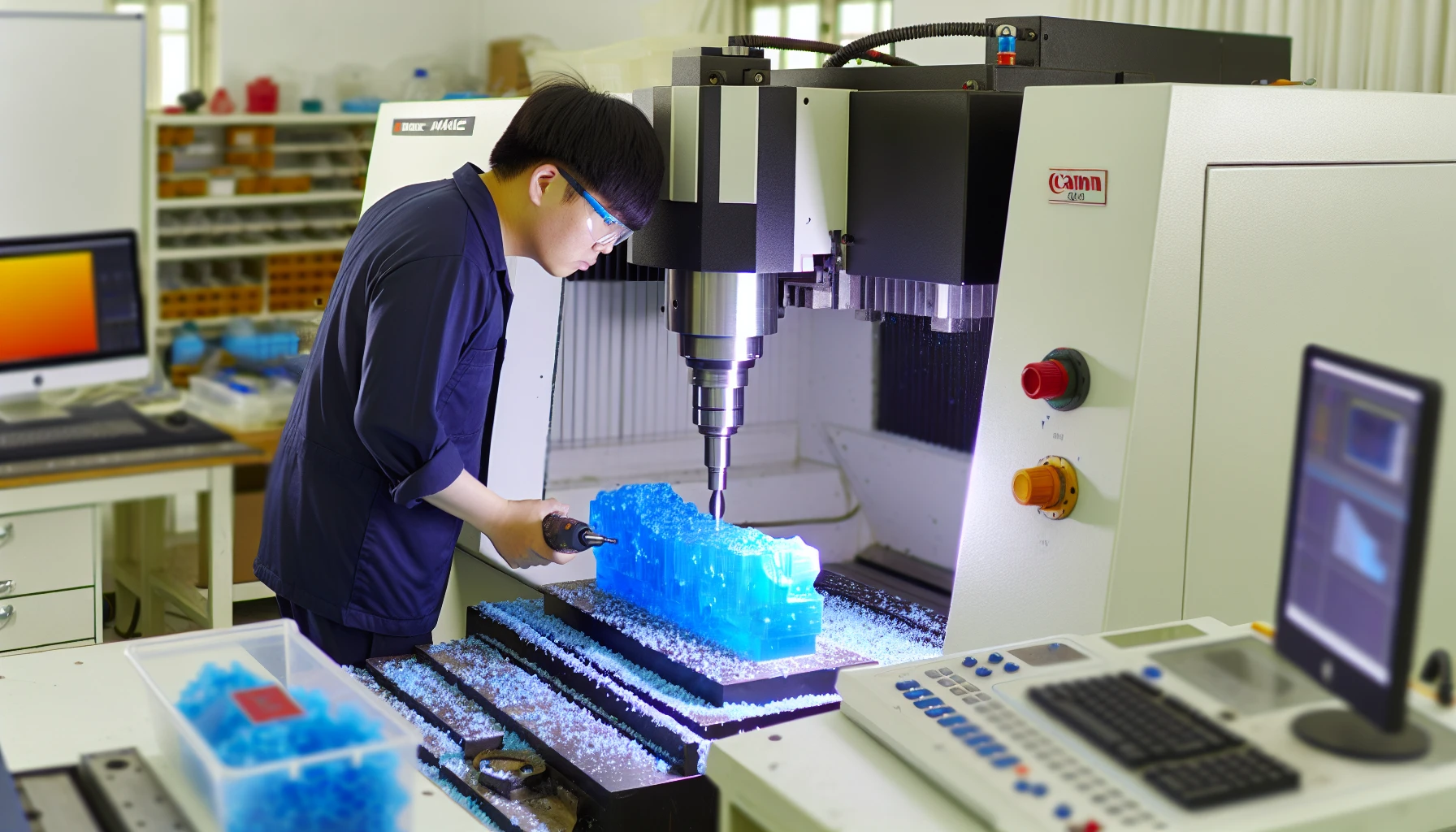
CNC plastic machining is a subtractive manufacturing process that utilizes a computer-controlled machine to shape a solid block of plastic into a desired product. This advanced technology ensures consistent and precise manufacturing of plastic parts, resulting in a high-quality output. CNC machining facilitates prototyping and is a cost-effective and efficient process for producing parts and products in large quantities.
CNC plastic machining in high volume production can be used to produce the following plastic parts:
- ABS (Acrylonitrile Butadiene Styrene)
- Nylon 66
- Polyetheretherketone (PEEK)
- Polyacetal (Polyoxymethylene)
- G10/FR4
- PPS
- Vespel
By addressing customer specific requirements, manufacturers can tailor the machining process to meet the unique needs of each customer, further enhancing the value of CNC plastic machining.
Optimizing the Production Part Approval Process (PPAP Approval) for Plastics
Optimizing the PPAP requirements and PPAP process for plastics is crucial to ensuring quality and compliance. In this section, we will delve into the importance of identifying critical characteristics and conducting validation testing as part of the critical processes to guarantee that plastic parts meet customer requirements and specifications.
Critical Characteristics in Plastic Parts
Critical characteristics in high volume plastic parts include material options, stiffness, durability, toughness, consistency, and mechanical strength. Factors that influence these characteristics include material considerations, radius, wall thickness, gate location, draft, inclusion of ribs, mold shrinkage, and tolerances.
Several strategies can be implemented to optimize the critical characteristics in plastic parts during the machining initial process studies. These include:
- Choosing the right machine
- Defined Process
- Adherence to injection molding tolerance guidelines
- Part design enhancement
- Accurate specification of injection molding tolerances
- Identification of Critical-to-Quality (CTQ) features
Completing Validation Testing for Plastic Components
Carrying out validation testing is necessary for verifying that plastic components comply with customer requirements and specifications, as well as identifying any potential design failure mode. Mechanical durability testing, raw material verification, and Production Validation Testing (PVT) are typically conducted to guarantee the quality and reliability of plastic components in high volume production parts.
A plastic component must satisfy certain criteria to pass validation tests, including:
- Meeting the specified requirements at each design stage
- Passing test specifications and methods
- Achieving a process capability index (Cpk) of 1.33 or 1.67
- Providing fully documented dimensional and process-related results
- Fulfilling testing requirements for specific applications or industries.
Streamlining Process Flow for Maximum Efficiency
Efficiency can be maximized by streamlining process flow through the implementation of statistical process control and adjustments for material certification and calibration schedules. A well-designed process flow diagram can be a valuable tool in achieving this goal.
In the following subsections, we will explore statistical process control and material certification and calibration schedules in detail.
Implementing Statistical Process Control
Statistical Process Control (SPC) is the utilization of statistical techniques to monitor and control the machining process in high volume plastics machining. SPC allows for the recognition and addressing of factors that contribute to product quality variation, enabling operators, engineers, and managers to make data-driven decisions for process improvement.
Utilizing SPC for high volume plastics machining provides numerous benefits, such as:
- Determining the factors responsible for product quality variation
- Providing real-time observation of parts during production
- Reducing scrap and improving quality
- Achieving process stability and reducing variability
- Gaining control of the plastics processing method
Adjusting for Material Certification and Calibration Schedules
Accounting for material certification and calibration schedules in high volume plastics machining can have a notable impact on efficiency. The use of correctly certified materials in the machining process can help avoid potential issues like material inconsistencies or defects that can lead to rework or scrap.
Regular calibration of the machining equipment and measuring devices helps maintain accuracy and precision, minimizing the risk of errors and enhancing overall efficiency in the production process.
Mastering Assembly Processes in Plastic Machining
The assembly process plays a crucial role in the production of complex plastic components. Typical assembly processes involved in plastic machining include:
- Press-to-fit joints
- Snap-to-fit joints
- Rivets
- Screws
- Mechanical joining
- Adhesive bonding
- Welding
Mastery of assembly processes in plastic machining requires understanding and selection of the most appropriate process for the assembly of plastic parts. Knowledge of plastic manufacturing techniques such as thermoforming, blow molding, and injection molding is also vital. Additionally, secondary machining processes like CNC machining, milling, turning, drilling, grinding, and tapping are commonly employed in plastic machining.
Ensuring Quality with Appearance Approval Reports and Inspection
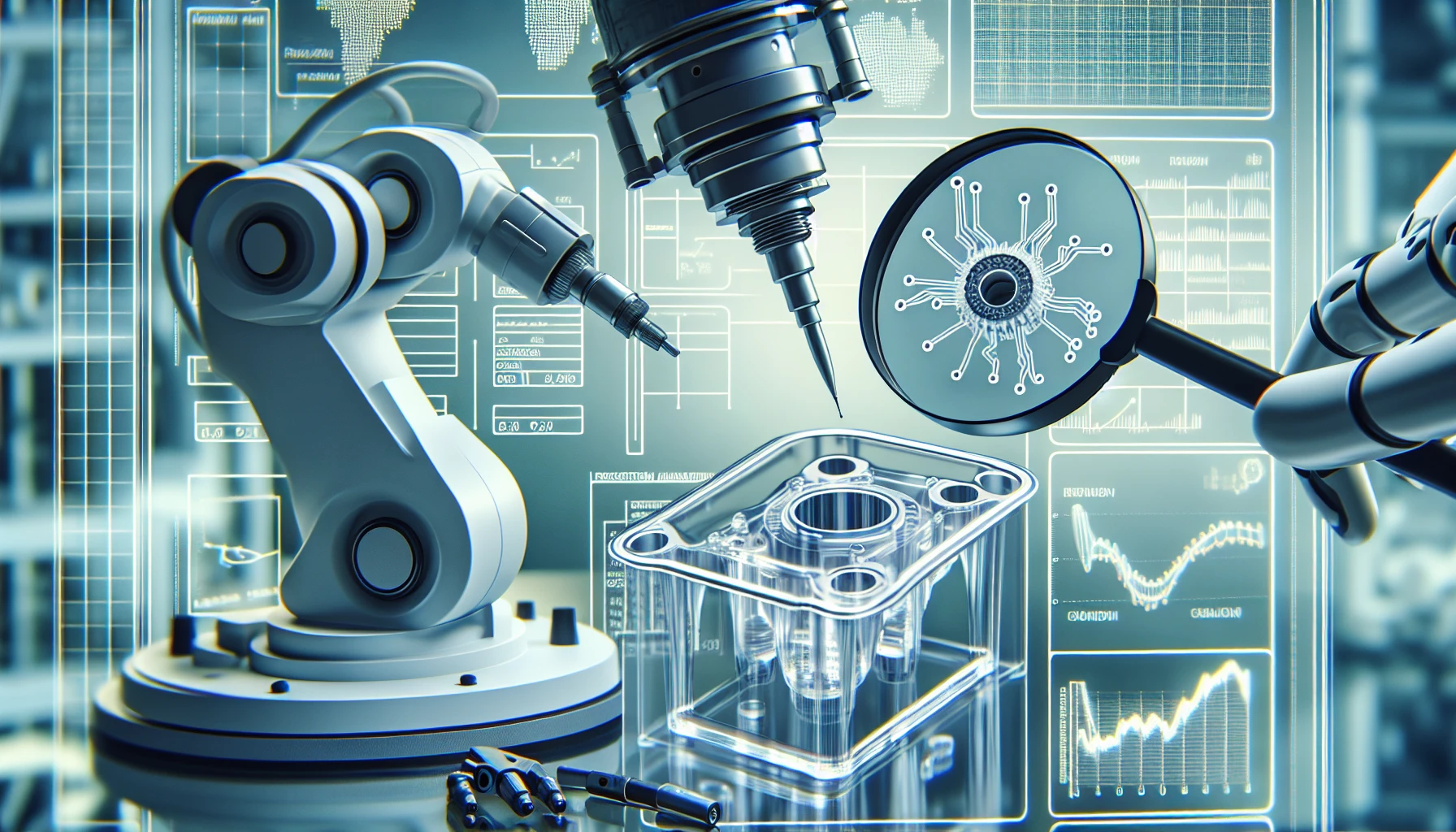
Quality assurance in plastic machining involves the use of an appearance approval report, inspection, and measurement system analysis studies.
In the next subsection, we will discuss the importance of measurement system analysis studies in ensuring accuracy and precision in plastic machining processes.
Measurement System Analysis Studies for Plastic Machining
Measurement System Analysis (MSA) is a process that evaluates the reliability and accuracy of the measurement system employed to collect data from the machining process. MSA assists in pinpointing and quantifying sources of variation in the measurement system, enabling enhancements to be made to improve the overall quality of the plastic machining process.
Implementing MSA in plastic machining ensures accuracy, precision, and reliability of the measurement instruments and techniques used in the machining process. By conducting MSA studies, manufacturers can recognize and tackle any sources of measurement error, guaranteeing that the measurements taken during the machining process are exact and uniform.
Managing Engineering Changes and Documentation
Quality and consistency in high volume plastic machining can be maintained by effectively managing engineering changes and documentation. Effective documentation management can enhance the machining process by:
- Guaranteeing uniformity and adherence
- Aiding process enhancement
- Allowing precise quoting and cost control
- Shortening time to market
Challenges associated with managing engineering changes and documentation in high volume plastic machining include:
- Uncontrolled modifications
- Meeting tight tolerances
- Documenting plastic parameters
- Navigating manufacturing intricacies
- Dealing with delamination
Through addressing these challenges, manufacturers can maintain efficiency and consistency in their plastic machining processes.
Leveraging Advanced Technologies in Plastic Machining
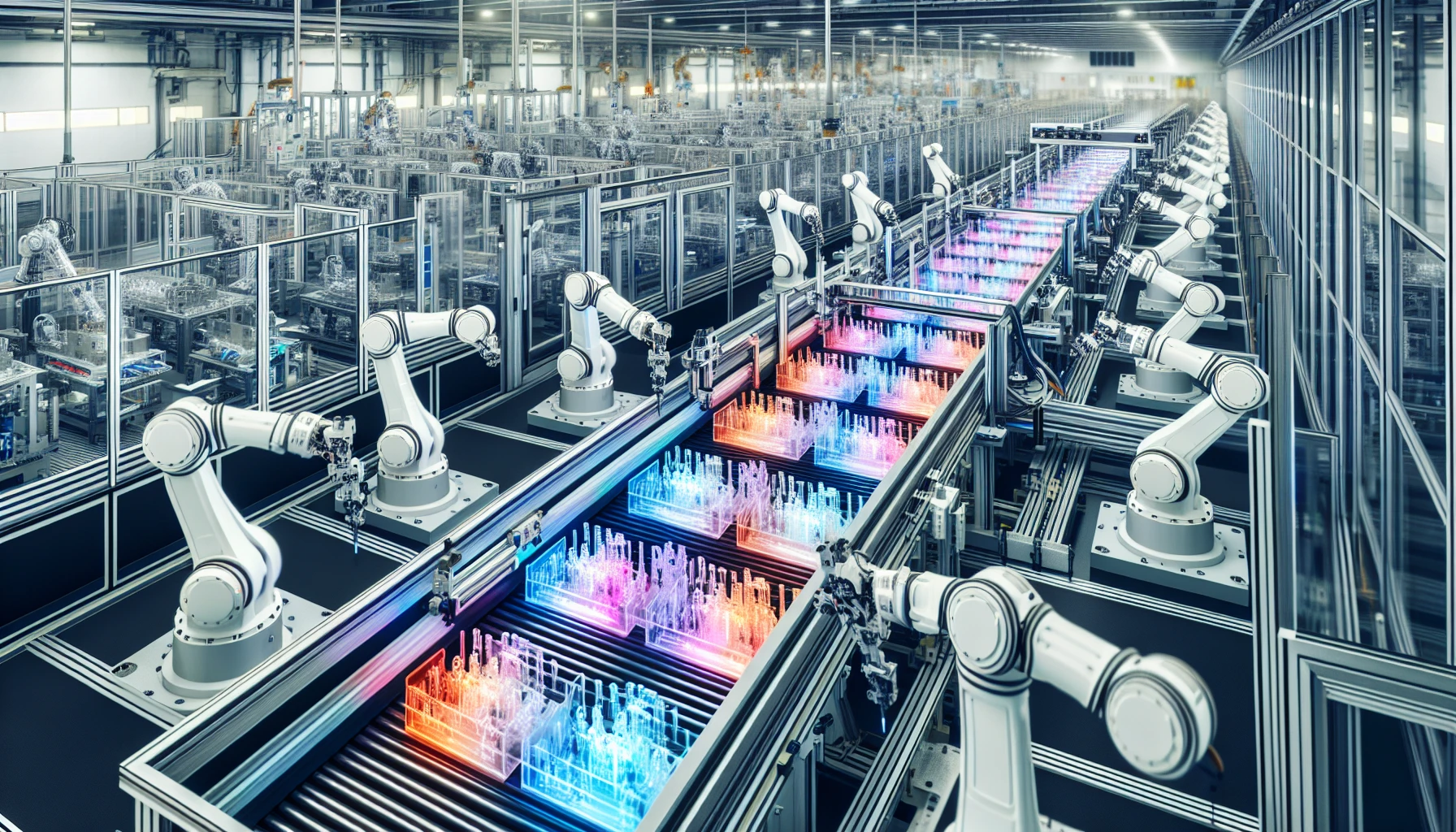
Advanced technologies in plastic machining, such as:
- Automation
- Robotics
- Artificial intelligence
- Computer Numerical Control (CNC) technology
can improve efficiency and precision in high volume production. These are the most advanced technologies currently utilized in plastic machining.
Utilizing automation and robotics in high volume plastic machining delivers a range of benefits, including:
- Boosting production efficiency
- Reducing costs
- Enhancing quality control
- Speeding up production runs
- Improving operator safety
- Increasing productivity and consistency
- Decreasing waste from rejected or misshapen components
The Impact of Customer Engineering Approval in the Approval Process
Customer engineering approval plays a significant role in the approval process, ensuring that plastic parts meet customer requirements, design documentation, and specifications. The process involves:
- Submitting various levels of sample and process documentation
- Conducting a sample run of typically 100 or so parts
- Obtaining customer approval
- Mitigating any identified issues
Verifying that plastic parts fulfill the customer’s quality requirements necessitates customer engineering approval, such as the Production Part Approval Process (PPAP). Obtaining customer engineering approval enables manufacturers to ensure the superior quality of the plastic parts they produce and their alignment with the customer’s expectations.
PPAP Submission: Navigating the Levels and Requirements
Navigating PPAP submission levels and requirements involves preparing the part submission warrant, understanding qualified laboratory documentation for plastic parts, and providing complete supporting data.
In the following subsections, we will discuss these aspects in detail.
Preparing the Part Submission Warrant for Plastic Parts
The Part Submission Warrant (PSW) is a comprehensive overview of the complete PPAP submission, documenting the submission and the approval or rejection of the parts prior to production. The PSW includes critical information such as drawings and product specifications, providing a summary of the PPAP documentation and ensuring the required specifications and standards are met.
Understanding Qualified Laboratory Documentation
Qualified documentation is essential to the PPAP approval process for plastic parts, as it ensures the accuracy and reliability of test results. This documentation includes lab certification and accreditation, which demonstrate that the laboratory meets the necessary standards and qualifications for conducting the required tests.
The qualified laboratory documentation provides assurance that the test results are valid and can be relied upon for the evaluation and approval of the plastic parts for production. Maintaining qualified laboratory documentation is crucial for ensuring the quality and performance of the plastic parts in high volume production.
Customizing Control Plans for High Volume Plastic Machining
Efficient production processes tailored to specific customer needs can be guaranteed by customizing control plans for high volume plastic machining. Control plans in high volume plastic machining systematically monitor and control the quality of the machining process. This includes:
- Defining critical control points
- Establishing inspection and measurement techniques
- Formulating criteria for acceptance or rejection of the machined parts
Factors to consider when customizing control plans for high volume plastic machining include:
- Plastic type
- Production volume and capacity
- Design considerations
- Quality control
- Tooling and equipment
- Cost considerations
- Environmental and safety considerations
- Supplier capabilities
- Communication and collaboration
- Continuous improvement
Case Study: Success Stories in High Volume Plastic Machining
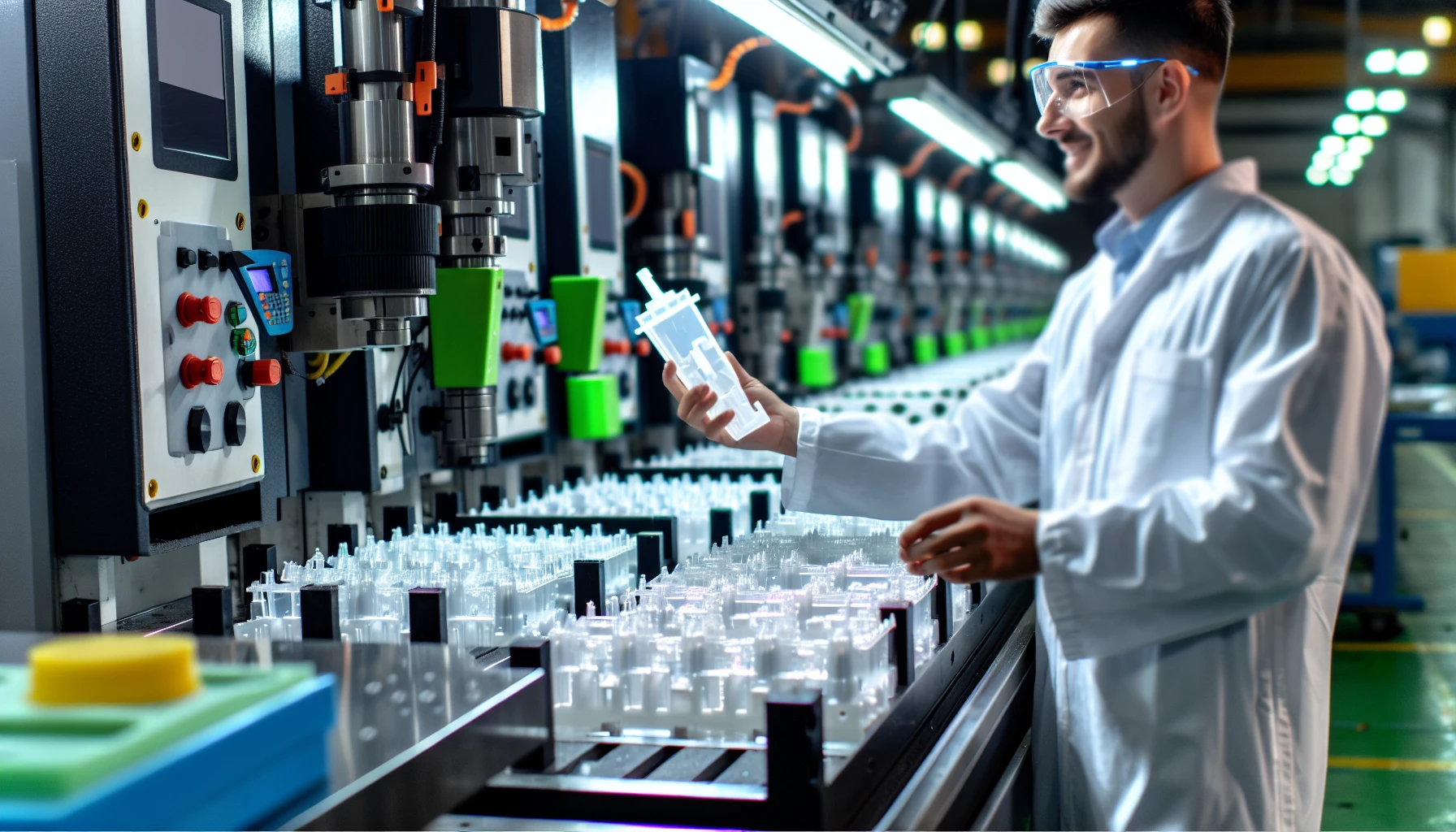
Optimized production processes and quality control are showcased in successful high volume plastic machining projects. Examples of such projects include:
- CNC milling for automotive, medical device, and semiconductor parts
- Injection molding for building and construction industry components such as window and door hardware
- Plastic CNC machining for medical devices, food and beverage industry parts, and semiconductor parts
These success stories exemplify the optimization of production processes in high volume plastic machining through:
- Efficiency
- Optimized mold design
- Production parameters
- Material selection
- Reliability and repeatability of processes
- Optimized part designs for manufacturing
These measures lead to increased productivity, cost reduction, improved product quality, and rapid and efficient production cycles.
Atlas Fibre is the Ideal High Volume Machining Partner
Offering advanced equipment, lot and batch tracking, a quality and customer service culture, and expertise in prototype through production, Atlas Fibre makes an ideal partner for high volume plastic machining. Trust Atlas Fibre to deliver exceptional results in high volume plastic machining, meeting and exceeding your expectations in every project.
Atlas has the most modern and advanced CNC machining equipment in plastics machining
Atlas Fibre’s advanced CNC machining equipment contributes to high volume plastics machining by providing precise and efficient manufacturing capabilities. Our cutting-edge machinery allows for:
- Automated and repeatable processes
- Minimizing the time and labor required for production
- Handling high volumes of plastic materials with accuracy and consistency
- Guaranteeing consistent quality throughout the manufacturing process
Most advanced lot and batch tracking in the industry
Atlas Fibre has implemented a robust system that ensures efficient tracking and traceability, guaranteeing quality control and customer satisfaction. Their advanced lot and batch tracking system allows for greater control and traceability throughout the manufacturing process, enabling improved quality control and the identification of any potential issues or defects.
A culture of quality and customer service
Atlas Fibre is devoted to offering outstanding service and unparalleled quality in the world of thermoset composites. Their culture of quality and customer service is integral to their commitment to providing exceptional service and unparalleled quality in high volume plastic machining.
Atlas Fibre continues to set industry standards for quality and service in plastic machining by making customer satisfaction a priority.
Excellent partner for prototype through production due to heavy investment in Fastems Flexible Manufacturing Systems
Fastems Flexible Manufacturing Systems (FMS) provide economic manufacturing of variable workpieces in small and repeatable batches, allowing for greater flexibility and efficiency when transitioning from prototypes to full-scale production. By investing in Fastems FMS, Atlas Fibre demonstrates its commitment to providing customers with the most efficient and flexible manufacturing solutions for high volume plastic machining.
FMS advances the science of machining, providing stable and predictable processes for high-mix, low-volume shops, making Atlas Fibre an excellent partner for prototype through production. With their heavy investment in Fastems FMS, Atlas Fibre guarantees efficient, flexible, and high-quality production of plastic components, ensuring customer satisfaction throughout every stage of the manufacturing process.
Summary
In conclusion, high volume plastic machining is a complex process that requires specialized techniques, equipment, and quality control measures. By optimizing the PPAP process, streamlining process flow, mastering assembly processes, leveraging advanced technologies, and ensuring customer engineering approval, manufacturers can achieve superior results in high volume plastic machining. Atlas Fibre stands as an ideal partner in this journey, offering advanced equipment, lot and batch tracking, a culture of quality and customer service, and expertise in prototype through production. Embrace the future of high volume plastic machining and unlock the full potential of your production processes today!
Frequently Asked Questions
What specialized techniques are utilized in high volume plastics machining?
Specialized techniques utilized in high volume plastics machining include minimizing clamping forces, using the appropriate cutting tool, and cooling to ensure an efficient and high-quality process.
What are the benefits of using advanced CNC machinery for plastic machining?
Advanced CNC machinery allows for faster production, reduced lead times, increased cutting efficiency, and improved quality control, resulting in higher quality machining.
What is the purpose of control plans in high volume plastic machining?
Control plans in high volume plastic machining ensure consistent and dependable production of high-quality plastic components by systematically monitoring and controlling the quality of the machining process.
How does customer engineering approval guarantee that plastic parts comply with customer requirements and specifications?
Customer engineering approval ensures that plastic parts comply with customer requirements and specifications by providing evidence that the supplier is capable of satisfying those requirements.
What are the advantages of utilizing automation and robotics in high volume plastic machining?
Utilizing automation and robotics in high volume plastic machining offers numerous benefits, including improved production efficiency, cost reduction, quality control, operator safety, productivity, consistency, and waste reduction.
In a market that demands precision, capacity, and procurement, it’s critical to understand the requirements of machining high-performance plastics like PEEK, PEI (Ultem), Torlon, and PPS. As industries from aerospace to medical tech seek components that withstand extreme conditions, the expertise of an excellent partner in high-volume, high-precision manufacturing becomes a cornerstone for success. This blog post delves into the seamless integration of Flexible Manufacturing Systems (FMS), strategic material sourcing, and competitive pricing, are a requirement in selecting a partner for plastics machining.
Unveiling the Potential of High-Performance Plastics:
Before examining the manufacturing prowess of a partner, it’s critical to understand the plastics in play:
- PEEK: Renowned for its endurance, PEEK resists thermal degradation and chemical attacks, ideal for harsh operating conditions.
- PEI (Ultem): This material boasts high thermal resistance and mechanical strength, with an intrinsic flame resistance, making it indispensable in demanding engineering applications.
- Torlon: Noted for its exceptional strength even at high temperatures, Torlon is synonymous with reliability over extended periods.
- PPS: Its excellent chemical resistance and dimensional stability under thermal stress make PPS a favorite in corrosive environments.
Look for advanced technologies:
Partners who have embraced next generation machining automation such as deployment of FMS within their operations is a game-changer. The few machinists globally to adopt such a system, provide unmatched precision across high-volume orders with benefits that include:
- Consistent Quality: FMS ensures uniform quality and adherence to stringent tolerances, vital for high-performance plastic components.
- Efficient Production: With the ability to operate around the clock, FMS maximizes output without sacrificing the precision machining of complex parts.
- Rapid Turnaround: Streamlined processes afforded by FMS mean shorter lead times, getting essential components into the hands of customers faster.
The Importance of Tool Selection and Machining Parameters:
Machining high-performance plastics is not a one-size-fits-all process. Here’s how they tailor their approach:
- Tool Selection: Employ diamond or carbide tools to match the durability of these robust materials.
- Speed and Feed Rates: Precise calculations for cutting speeds and feed rates are made to prevent the plastics from overheating.
- Coolant Use: In cases where heat generation is a concern, utilizing a coolant that does not impact the performance of the finished part is needed to maintain the integrity of the plastics.
Atlas Fibre is an ideal partner:
- Direct Material Sourcing: As a direct distributor for Mitsubishi Chemical Advanced Materials, Ensinger, and Gehr, Atlas Fibre acquires high-grade thermoplastics at competitive prices, with savings passed on to customers.
- Advanced Automation: A focus on automation beyond FMS, including state-of-the-art CNC machines and robotics, enhances efficiency and leads to cost savings.
- Comprehensive Solutions: They don’t just machine parts; they provide end-to-end solutions tailored to customer specifications, backed by technical expertise and customer support.
Real-World Applications and Success Stories:
Atlas Fibre’s capabilities have been proven across various industries:
- Medical Sector: Machined PEEK implants exemplify biocompatibility and durability.
- Aerospace: Ultem parts, leveraging their high strength-to-weight ratio, are integral to aircraft design.
- Automotive: Components made from Torlon showcase the material’s ability to endure extreme automotive environments.
Conclusion:
Atlas Fibre is reshaping the landscape of plastics machining, combining technological innovation with strategic material partnerships to offer unmatched value in high-volume and high-precision manufacturing. Their use of FMS systems, coupled with their role as a direct distributor for some of the industry’s most trusted material providers, enables them to offer competitive pricing and lead times that set them apart. Whether you need components that offer thermal resistance, mechanical strength, or chemical stability, Atlas Fibre has the expertise and the resources to deliver.
Explore a partnership with Atlas Fibre and take advantage of their advanced approach to precision plastics machining—where quality meets efficiency at the most competitive prices.