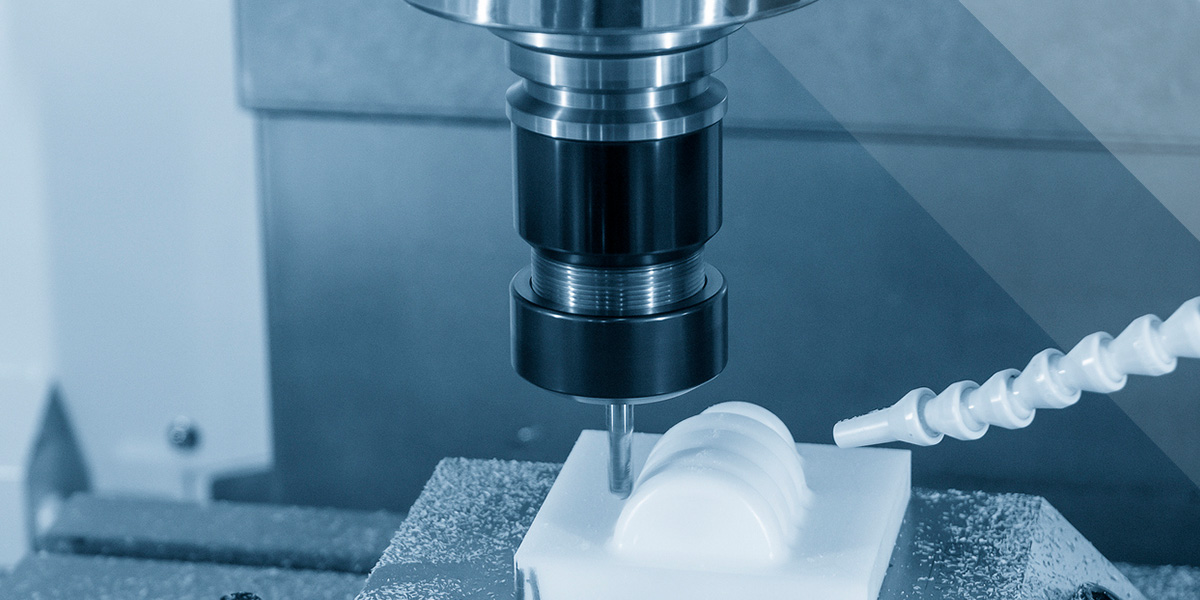
The plastic industry is one of the biggest in the world. It is estimated to grow by $643.37 billion globally by 2029, which is paramount to why businesses must enhance their manufacturing processes. Low-quality plastic products and slow production can have various impacts on businesses.
Multiple plastic manufacturing processes like thermoset manufacturing, computer numerical control (CNC) machining, and thermoforming can help companies produce premium quality plastic parts and products. It can also enhance production speeds and prototype developments and offer numerous design options.
While injection molding is a common application in industries, various alternatives can offer businesses a more cost-effective and quality process. Companies can select a suitable solution for their needs and budget by understanding multiple plastic forming processes. Businesses can also prioritize methods to give them the highest success rate, especially in an exponentially competitive market.
What Is Injection Molding?
Injection molding is a process used for forming plastic products and parts like bottle tops, door handles, television, toys, automotive parts, and computers. Manufacturers use thermoplastic molding to create desired products. They heat and inject plastic products with chemicals like nylon and polymers under high pressure and cool them in a metal mold.
The process helps enhance the shape and quality of products. It also allows manufacturers to develop bulk products more efficiently. Producers use injection molding for various industry applications like medical, aerospace, and construction.
While injection molding is a widely-used process, it is one of many. Manufacturers can use various injection molding alternatives like CNC machining, thermoset manufacturing, rotational molding, and thermoforming.
Alternatives to Injection Molding
Alternative plastic manufacturing processes like CNC Machining, thermoset compression molding, blow molding, and 3D printing can offer various advantages like durability, weight, efficiency, and affordability.
CNC Machining
CNC machining is an automated plastic manufacturing process. It is one of the oldest and most reliable processes for molding plastic and other materials parts like wood and metal. CNC machining is computer-aided and uses advanced software to speed up manufacturing.
Using tech features, a CNC Machine can complete various actions like drilling and cutting in manufacturing without manual intervention. It offers high-quality products and high performance in different thermoplastic production. CNC machining is versatile and offers numerous applications like cutting, shaping, and spinning. Some CNC plastic machining includes:
- CNC mills: Uses a rotating spindle to cut and form various plastic shapes from raw material.
- CNC routers: Forms plastic shapes using a rotary cutting tool that moves backward and forward.
- CNC latches: Using computer-aided commands, a material rotates on a spindle forming various shapes. The cutting tool remains stationary and cuts around the rotating material. The machining can rotate a material in multiple directions using computer-programmed software.
Thermoset Manufacturing
Thermoset manufacturing is the process of forming plastic products by combining thermoset composites like polymer and fibers like glass. Using illiquid molding processes, it manufactures heat and cures polymers and fibers to form various plastic products.
Thermoset manufacturing creates a chemical bond between materials, producing durable and robust plastic products. Manufacturers can use composite methods like compression molding, injection molding, and high-pressure lamination to produce numerous shapes and chemical bonds:
- Thermoset injection molding: Manufacturers can use injection molding to form products using thermoset materials like polymers. Unlike thermoplastic injection molding, manufacturers inject materials into a heated mold, curing the product. Once the material is solidified, it is resistant to melting or warping.
- Compression molding: Plastic molding process that uses heat and force to create various shapes. A thermoset composite-like sheet-molding compound is placed into a molding press with a die and is compressed under force and pressure, forming shapes.
- High-pressure lamination: Manufacturers use a thermoset prepreg composite to produce robust, high-quality products. They place the composite into a molding press and apply heat and pressure, forming g-10 fiberglass laminate and FR4-reinforced fiberglass laminate.
Rotational Molding
Rotational molding or rotomolding rotates liquid thermosets in a mold cavity, forming various shapes. It is commonly used for round and hollow objects like bins, toys, automotive parts, and storage tanks. Liquid composites harden in heated rotational mold cavities, forming a shape on the cavity surface.
Rotational mold is also used for creating complex and more significant industrial plastic parts. Rotomolding is excellent for creating large-scale and robust products. The process helps produce thick plastic walls, providing more durable products.
Blow Molding
Blow molding uses a molding tube to create hollow plastic products like bottles and containers. The process forms lightweight parts with thick and consistent plastic walls. Manufacturers melt plastic and expand it in the mold cavity using compressed air. The plastic material forms a shape in the cavity. Blow molding is used for producing large quantity plastic parts.
3D Printing
3D printing or additive manufacturing produces three-dimensional objects by building up layers of liquid composite. A 3D printer creates plastic parts and objects based on a mold design. The liquid material hardens with a UV-laser beam and forms an object according to the mold design. The object is reinforced with numerous material layers. Manufacturers can use 3D printing to create customized and consistent plastic parts. It can also be an affordable alternative to injection molding.
Casting
Casting uses a molding cavity to shape solid plastic parts or objects. Manufacturers pour a liquid composite into a mold cavity. The materials create a chemical bond and harden in the shape of the cavity, producing a finished product. Popular casting methods include silicone and urethane molding.
Manufacturers design and print a silicone or urethane mold with a distinct pattern. They pour liquid materials into the mold pattern to create uniform products with intrinsic designs. Casting is an excellent solution for producing low-volume customized products like automotive engine parts.
“While injection molding is better for producing complex parts, thermoforming is better for manufacturing high-quality finished products.”
What Is Better Than Injection Molding?
While injection molding is better for producing complex parts, thermoforming is better for manufacturing high-quality finished products. Manufacturers can use thermoforming for developing large-scale products and parts. Thermoforming also offers an efficient and cost-effective molding process. It is also an excellent solution for creating numerous durable components.
Thermoforming vs. Injection Molding
Businesses want to use a suitable plastic manufacturing process for their applications. Considering various factors like affordability, quality, and performance is one of the best ways to select an appropriate method. Both methods can be effective in numerous industrial applications. Understanding thermoforming and injection molding capabilities can help identify the most suitable process for business needs.
What Is Thermoforming Used For?
Thermoforming is a manufacturing process for molding durable plastic objects like packaging, appliances, and consumer goods. A heated thin plastic sheet is compressed and stretched across a mold, forming a shape. The methods for thermoforming include:
- Low pressure: Manufacturers heat a plastic sheet over a mold cavity. Pressure is applied, sealing the sheet to the mold.
- Vacuum: The vacuum tool suctions the sheet against the mold surface, and compressed air is applied to the outer sheet surface, securing it to the mold and producing the desired plastic shape.
- Mechanical force: A heated plastic sheet is placed between two mold cavities and is drawn together by vacuum. Compressed air between the cavities causes the plastic sheets to inflate on each end. The inflated sheet takes the shape of the mold cavities and joins together, creating a hollow plastic object.
Thermoforming Applications
Here are some common thermoforming applications:
- Automotive: Thermoformed vehicle components like seats, fenders, dashboards, door panels, windows, and controls with various thermoplastic materials to provide rigid, corrosion, and damage-resistant parts.
- Aerospace: Thermoformed aircraft components like air ducts, control panels, lighting fixtures, and windows to withstand extreme conditions like high temperatures and speed.
- Defense: Shaping and creating durable, corrosion-resistant military weapons and equipment.
- Medical equipment: Applying thermoset materials over equipment like hospital beds and table tops, X-ray, and ultrasound components for lightweight, durability, strength, and corrosion resistance effects.
- Packaging: Thermoformed plastic pallets, cosmetic packaging, and consumer goods packings like food trays, ice cream time, sandwich packs, and micro van containers. Manufacturers can use thermoset materials like polyvinyl chloride (PVC) for lightweight, transparency, and strength properties.
- Tech equipment: TV or plasma, cellphone towers, and electronic packaging screens thermoformed with flame retardant and high-impact polymers to protect from heat and impact damage.
- OEM equipment: Thermoforming equipment like laptops, computer parts, and car components with thermoplastic polymers can protect them from heat damage, ultraviolet radiation, and corrosion. It can also make equipment more robust and durable.
Injection molding is used for developing industrial, household, and complex plastic products and components. Manufacturers can use an injecting molding machine to form various plastic shapes.
What Is Injection Molding Used For?
Injection molding is used for developing industrial, household, and complex plastic products and components. Manufacturers can use an injection molding machine to form various plastic shapes. The device has a clamping unit that holds it close and applies force to the mold cavities. A melted plastic material is injected and heated into the mold structure and, under pressure, fills and takes the shape of the mold cavities. The plastic is cooled and hardened on the mold cavities’ surface, forming a shape.
Injection Molding Applications
Here are some common injection molding applications:
- Building accessories, door and window components like locks and handles, and building tools
- Automotive parts like bumpers, panels grilles and turbine blades
- Agricultural harvest equipment components, animal troughs, containers, and bins
- Tupperware, furniture like couch seats and set covers
- Bottle caps, plastic bottles, and microwave or freezer dinner trays
Thermoforming vs. Injection Molding
Thermoforming and injection molding can impact your product quality differently. Understanding thermoforming and injection molding differences like cost, quality, and efficiency is essential. Weighing the pros and cons of thermoforming and injection molding can help you identify which process is more suitable for your business.
Pros and Cons of Thermoforming
Here are some pros of thermoforming:
- Product size: Manufacturers can use thermoforming for more oversized plastic products and parts.
- Quality: Thermoforming can produce durable, weather, and corrosion-resistant components. Thermoformed objects can also withstand high-impact heat and last longer.
- Customization: Creating a distinctive design is more convenient, and manufacturers can adapt products to various sizes and shapes with thermoforming.
- Cost: Thermoforming offers lower start-up, material, and tooling costs and can be an affordable long-term investment.
- Aesthetics: Thermoforming offers various plastic colors, textures, and attractive finishes, providing companies with more aesthetic options to meet their needs.
- Weight: Thermoformed objects and components can be more lightweight, enhancing their quality and making them more convenient for transportation.
- Production speed: Shorter tooling time can result in faster lead, turnaround times, and high-volume productions.
- Porotype development: Lower tooling costs can make prototype development more efficient.
- Versatility: Thermoforming offers various methods like vacuum, pressure, and mechanical force to meet clients’ needs.
- Small volume runs: Changing designs and tooling can be more convenient and cost-effective for making product changes or edits.
- Sustainable options: Various sustainable plastic materials like high-density polyethylene can be used in thermoforming.
Here are some cons of thermoforming:
- Uniformity: Stretching plastic over molds can produce less uniform products.
- Complexity: Thin wall production can limit geometry and make it more challenging to design complex smaller shapes.
- Plastic quantity: While thermoforming can use sustainable plastic types, it can require more plastic usage than other methods.
Pros and Cons of Injection molding
Pros of injection molding include:
- Complexity: Injection molding can produce more complex shapes, especially in smaller products.
- Reproducibility: Injection tooling mold can be used numerous times for production before requiring a new mold tool
- Plastic usage: Manufacturers can require less plastic in injection molding.
- Range: Various materials like chemical-resistant plastic can be used in the process.
Cons of injection molding include:
- High cost: Injection molding can require custom tooling, making it costly, especially for low-volume productions.
- Size limitations: Creating more oversized plastic products can require complex machinery, making them more challenging and expensive.
- Completion time: Complexity injection molding tooling can result in longer product completion times and slower production.
- Costly design changes: Making product changes and edits can require a new mold design, increasing production time and costs.
- Design limitations: Injection molding can have fewer design finishes and options than thermoforming.
What Is an Alternative to Injection Molding?
Thermoforming is one of many injection molding alternatives. It offers high-quality products that withstand heat, impact, pressure, and corrosion.
Thermoforming can also offer less complex tooling and operations at lower costs. Thermoforming offers adaptable molding solutions for various industries. Other injection molding alternatives include compression molding, blow molding, 3D printing, rotational molding, CNC machining, and casting.
Atlas Fibre is the fastest and most cost-effective supplier of CNC custom plastic parts.
Work With Atlas Fibre for High-Quality Thermoset Composite Materials
Thermoset plastics offer various industries premium quality, robustness, attractiveness, chemical, corrosion-resistant, and lightweight plastic products.
While there are many injection molding alternatives, Atlas Fibre is a leading thermoset composite material manufacturer. We are a trusted supplier of thermoset laminate composite in North America. We offer CNC machining for various thermoset materials like thermoplastics, glass expoy, and paper.
As one of the largest thermoset manufacturers and distributors, we offer numerous composite manufacturing variants, including compression molding and high-pressure lamination. Our batch size one production provides automated and continuous production, reliable supply, and lower storage costs. Our materials offer durability, corrosion resistance, high strength, and lightweight for long-lasting premium products.
Contact us today to learn more about our thermoset composite materials and manufacturing.