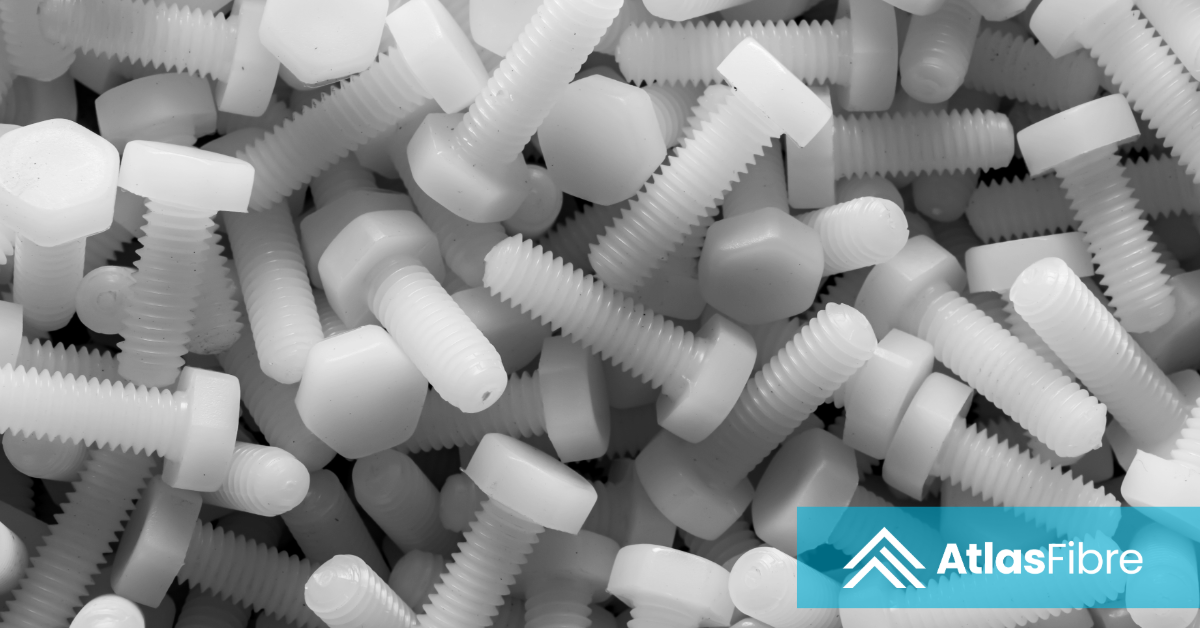
When precision matters, engineers increasingly turn to advanced plastic materials like thermoset composites and thermoplastics for fastener solutions. These materials offer distinct advantages over traditional metals, depending on the specific needs of their application.
Thermoset Composite Laminates: Built for Extreme Environments
Thermoset composites, including phenolic and epoxy laminates, are engineered through a curing process that results in highly cross-linked molecular structures. This unique chemistry makes them especially suited for demanding environments.
High Strength-to-Weight Advantage
Thermoset composites offer remarkable strength combined with significantly lighter weight compared to metals. In industries such as aerospace, automotive, and marine, where every gram counts, these materials deliver high-performance fastening solutions without compromising structural integrity.
Unmatched Thermal and Dimensional Stability
Unlike conventional plastics, thermosets do not soften or deform under extreme temperatures. Their stability makes them ideal for high-temperature applications such as engine compartments, spacecraft components, and industrial equipment, maintaining shape and performance under intense conditions.
Superior Corrosion and Chemical Resistance
One of the greatest threats to metallic fasteners—corrosion—is a non-issue for thermoset composites. These materials resist degradation from moisture, saltwater, and aggressive chemicals, extending lifespan and reducing maintenance costs in marine, chemical processing, and industrial environments.
Excellent Fatigue and Wear Resistance
With their rigid and durable molecular structure, thermoset composites withstand repetitive stress, vibrations, and mechanical wear. This durability is critical in applications like railway components, heavy machinery, and infrastructure systems, where consistent performance is essential.
Electrical Insulation and Flame Retardancy
Thermosets inherently provide strong electrical insulation and resistance to combustion, offering added safety benefits in electrical enclosures, electronics manufacturing, and environments with potential fire hazards.
Thermoplastics: Versatile, Adaptable, and Sustainable
Thermoplastics, such as polyetheretherketone (PEEK), nylon (PA), and acrylonitrile butadiene styrene (ABS), are reshaping fastener technology through flexibility, rapid manufacturing, and sustainability.
Innovative Design Flexibility and Net-Shape Production
Thermoplastics enable precise, complex shapes through injection molding, compression molding, or additive manufacturing like 3D printing. Advanced techniques like Composite Flow Molding (CFM) provide optimal fiber alignment, enhancing strength precisely where it’s needed. This allows designers unprecedented freedom to innovate and streamline components for sectors like automotive, medical devices, and electronics.
Property | Thermoplastic Fasteners | Metal Fasteners |
---|---|---|
Flexural Strength | UP to 7x higher than aluminum | Moderate to High |
Weight | Significantly lighter | Heavier |
Corrosion Resistance | Excellent inherent resistance | Requires protective coatings |
Promoting a Circular Economy
Unlike thermosets, thermoplastics can be repeatedly melted and reshaped without significant loss of material integrity. This recyclability aligns perfectly with sustainability and circular economy goals, allowing industries to reduce environmental footprints while maintaining performance standards.
Accelerated High-Volume Manufacturing
Thermoplastics support high-speed production, reducing lead times dramatically. Injection molding and 3D printing enable rapid prototyping and scalable mass production. For instance, parts made from ABS or polyoxymethylene (POM) can be produced much faster—and often at lower cost—than machined metallic counterparts.
Robust Chemical and Thermal Performance
High-performance thermoplastics like PEEK withstand extreme conditions, resisting chemical attacks and maintaining structural integrity at temperatures up to 500°F (260°C). This resilience makes them highly suitable for demanding applications such as medical implants, aerospace fasteners, and high-performance automotive components.
Choosing the Right Plastic Fastener Material
When deciding between thermoset composites and thermoplastics for fasteners, consider the following guidelines:
- Choose thermosets for extreme environments that demand durability, thermal stability, corrosion resistance, and flame retardancy, typically found in aerospace, marine, electrical, and heavy-duty industrial applications.
- Opt for thermoplastics when design flexibility, sustainability, recyclability, and rapid manufacturing are critical, such as in automotive innovations, medical devices, consumer electronics, and high-volume commercial products.
By selecting the appropriate plastic material, engineers and designers can significantly enhance performance, reliability, and sustainability of their fastening solutions, ensuring precision engineering that meets the evolving demands of modern industries.