Flexural modulus is the metric that defines material stiffness and its resistance to bending. It is paramount for design engineers who rely on these values to select materials for structural durability and safety. This article will cover the principles of flexural modulus, including how it is measured, factors that affect its value, and its practical applications in various fields such as aerospace and construction.
Key Takeaways
- Flexural modulus, key for material selection in engineering, measures a material’s stiffness and resistance to bending through standard testing methods such as ASTM D790, often influencing design decisions in aerospace and automotive industries.
- Factors like resin system selection, thermoset composite substrates, and reinforcement with fibers in plastics significantly affect a material’s flexural modulus, leading to varied rigidity and load-bearing capacities among different materials.
- Current flexural modulus testing has limitations and can be affected by errors; however, advancements in technologies like 3D printing and the development of new composites promise improvements in assessing and enhancing the flexural modulus of materials.
Defining Flexural Modulus
Flexural modulus, also known as bending modulus, is a term that describes a material’s stiffness and its resistance to bending. It is calculated using a specific formula applied to a rectangular beam subjected to force causing deflection, with units typically expressed in Megapascals (MPa) or Pounds per square inch (psi). In this context, bending modulus comments can provide valuable insights into the material’s performance under various conditions, including its compressive modulus. Elastic beam theory plays a significant role in understanding these properties and their applications in engineering and design, as well as their relationship to the elastic modulus, such as Young’s modulus.
A higher flexural modulus signifies a stiffer material, indicating a greater resistance to bending. This property is closely related to tensile modulus, which measures a material’s resistance to being pulled apart. These properties are significant for architects and engineers, as they provide insights into a material’s weight capacity when implemented as structural support, thus informing their material selection for various load-bearing applications.
Key Terminology
In the world of materials engineering, the term flexural modulus is used to describe a material’s capacity to resist deformation under bending, a property that becomes particularly important when comparing unreinforced and reinforced plastics. Another key term is stiffness, which pertains to a material’s ability to revert to its original shape once an external force is removed, indicating the material’s ability to resist deformation under an applied load.
Rigidity, on the other hand, specifically refers to the resistance to bending or flexing, also known as the flexural or bending modulus. Resistance to bending, therefore, indicates a material’s rigidity, showing its capacity to withstand bending when subjected to stress. Each of these terms plays a significant role in comprehending the flexural modulus and its impact on material selection and design.
The Role of Flexural Modulus in Material Selection
In material selection, the flexural modulus is essential as it provides engineers with a means to measure a material’s resistance to bending and ascertain its stiffness. It represents the ratio of stress to strain during flexural deformation and directly affects the material’s flexural rigidity.
Particularly in fields like aerospace engineering, automotive engineering, sports, and load-bearing applications, the flexural modulus is vital as specific stiffness and rigidity are required. It defines the material’s strength and load-bearing capacity, especially in applications that require specific stiffness and rigidity properties.
Factors Affecting Flexural Modulus
The flexural modulus is not a constant value but can be influenced by several factors. The choice of a thermoset composite substrate, for instance, can significantly impact the flexural modulus by influencing the material’s mechanical properties like impact strength and interfacial adhesion. Similarly, the selection of resin systems can also affect the flexural modulus as specific resin systems demonstrate improved flexural modulus.
Moreover, the type of plastic, whether unreinforced or reinforced, can affect the flexural modulus. Reinforced plastics generally demonstrate an elevated flexural modulus due to the reinforcing fibers or materials aiding in the transfer of stress from the weaker polymer matrix to themselves, consequently leading to an increased overall flexural strength of the composite.
Thermoset Composite Substrate and Resin System Selection
The selection of a resin system can have a significant impact on the flexural modulus of thermoset composites by affecting the interfacial adhesion between the substrate and the resin, as well as the mass ratio of thermoplastic resin to composite fillers.
In the industry, thermoset composite substrates such as polyester, phenolic, and epoxy are commonly used as electrical insulating materials. Notably, these materials are prevalent in the aerospace industry due to their high flexural modulus characteristics, essential for applications demanding durability and resistance to bending.
Unreinforced vs. Reinforced Plastics
Reinforced plastics, also known as fiber-reinforced plastics (FRP), typically demonstrate elevated flexural modulus values compared to unreinforced plastic materials. Reinforced plastics are produced by amalgamating two or more materials to create a composite with enhanced properties.
The increased flexural modulus in reinforced plastics is primarily attributed to the type and volume of fibers used in the reinforcement. These fibers aid in the transfer of stress from the weaker polymer matrix, leading to an overall increase in the flexural strength of the composite.
Testing Methods for Flexural Modulus
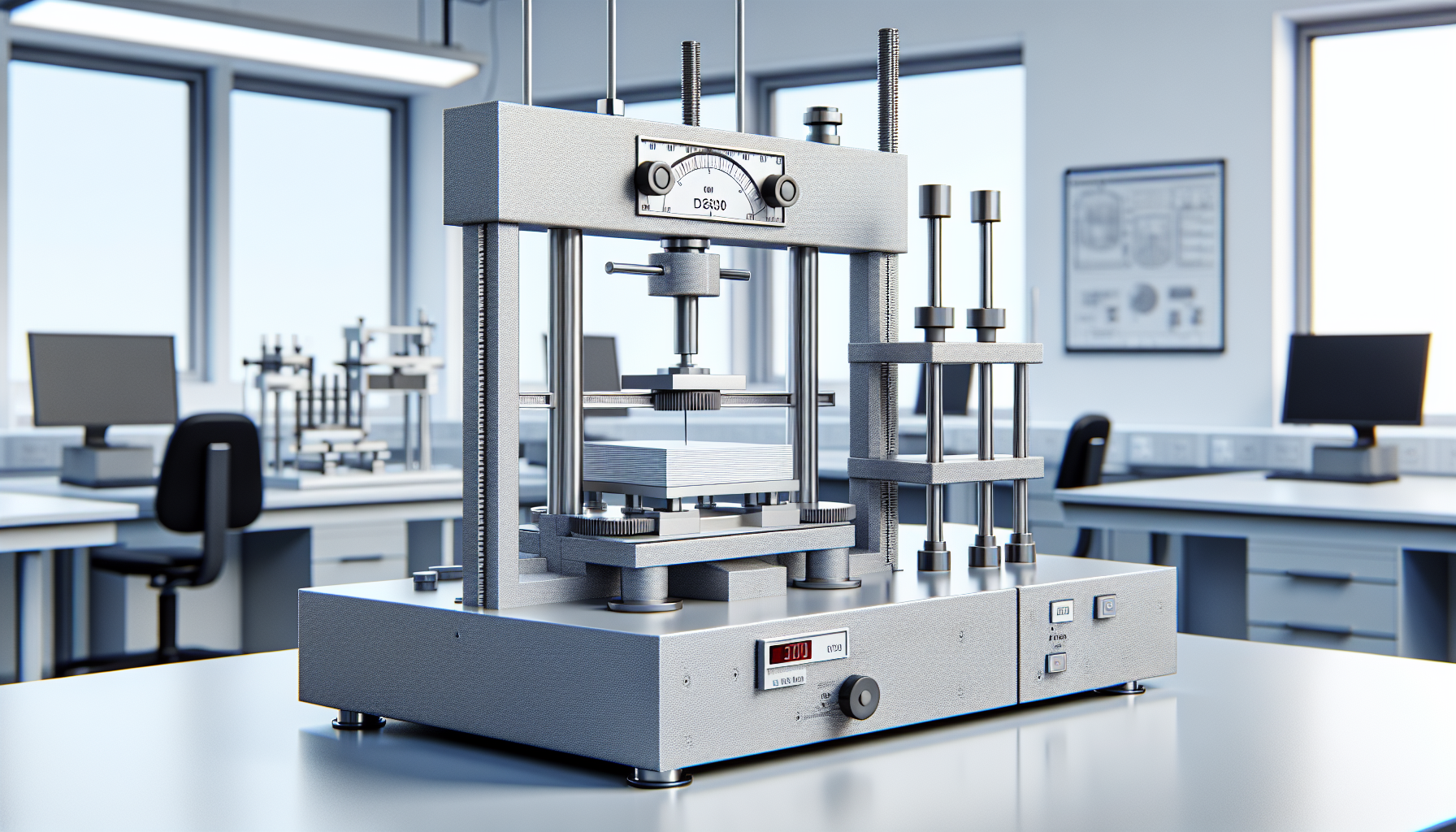
Applying appropriate testing methods is essential for understanding a material’s flexural modulus. These tests are usually carried out using universal testing machines equipped with bend fixtures. The flexural modulus is then determined using a specific mathematical equation that considers various parameters, such as:
- the applied force
- the distance between the supports
- the width and height of the specimen
- the deflection.
Different bending tests, such as three-point or four-point bending tests, can be used to evaluate the flexural modulus. A three-point bending test, for instance, concentrates the load at a single point under the loading nose, leading to a maximum bending moment and axial fiber stress at the center of the sample.
On the other hand, a four-point bending test distributes the load over two points, resulting in the maximum bending moment and stress occurring between the two inner loading points.
ASTM D790 Test Method
The ASTM D790 test method is widely used to ascertain the flexural modulus of a material. This method involves either a three-point or four-point bending test. In a three-point bending test, the test bar is placed on a three-point bend fixture, and the test is continued until the sample reaches 5% strain or breaks.
However, the distinctions between the two bending tests should be noted. While a three-point bending test concentrates the load at a single point, a four-point bending test distributes the load over two points, resulting in a more uniform bending moment between the two loading points.
Interpreting Test Results
Interpreting the results of a flexural modulus test involves understanding the stress-strain curve and calculating the flexural modulus from the linear portion of the graph. The flexural modulus is determined by analyzing the initial slope in the stress-strain curve.
However, challenges may arise from:
- System deflection in travel measurements
- Compliance in the supports and machine base
- Inaccurate force and flexural strain measurements
- A non-linear stress-strain curve, which can indicate varying stiffness at different stress levels and complicate the interpretation of flexural modulus.
Applications of Flexural Modulus in Industry
The flexural modulus finds a multitude of applications in various industries, from construction and infrastructure to automotive and aerospace. It is used to augment the tensile and flexural strength of materials like fiber-reinforced concrete, enhancing resistance to bending and cracking, and making it suitable for a variety of construction applications, including water infrastructure and underground construction.
In the automotive and aerospace industries, the flexural modulus plays a crucial role in the design of lightweight and durable components that meet specific stiffness requirements. The flexural modulus also plays a significant role in determining the structural integrity and load-bearing capacity of beams and other structural elements, making it crucial for ensuring the stability and durability of the structures.
Construction and Infrastructure
In the construction and infrastructure industry, the flexural modulus is utilized to evaluate their stiffness or resistance to bending. This assessment is crucial in determining the performance of materials in withstanding bending forces and in the design of structures capable of withstanding such forces.
Materials like plywood, reinforced concrete, and reinforced plastics such as polycarbonate, ABS, polyamide, and polypropylene offer enhanced rigidity and bearing capacity for various construction applications due to their high flexural modulus. These materials safeguard the structural integrity and safety of the constructed edifices, thus underlining their importance in the construction and infrastructure industry.
Automotive and Aerospace
In the automotive and aerospace industries, the flexural modulus is leveraged to enhance the mechanical properties of brackets or braces made from composite materials when subjected to bending. These brackets, especially when made from high-performance composites like These brackets, especially when made from high-performance composites like G10 or carbon fiber, demonstrate the material’s rigidity and resistance to deformation under stress.
By determining the material’s resistance to bending, the flexural modulus significantly influences the design of lightweight components within these industries. A higher flexural modulus implies a stiffer material, which contributes to improved structural integrity and support, crucial for applications where lightweight components are required to withstand bending forces, such as in airplanes and automobiles.
Flexural Modulus of Common Materials
The value of the flexural modulus can vary greatly among different materials. For instance, in the world of plastics, Low-Density Polyethylene (LDPE) demonstrates a flexural modulus of 335 MPa, while fiber-reinforced Nylon 12 exhibits a much higher flexural modulus of 13,700 MPa.
On the other hand, metals and alloys typically demonstrate a greater flexural modulus compared to plastics and polymers, suggesting that they possess more rigidity and less flexibility. Specific alloys like the Aluminum alloys in the 3xxx, 5xxx, and 6xxx series, such as aluminum alloy 6063, are recognized for their high flexural modulus.
Similarly, the Zr-2.5% Nb alloy is acknowledged for its strength and high flexural modulus.
Flexural Modulus of Thermoset Composites: G10 and Carbon Fiber
Thermoset composites like G10 and carbon fiber exhibit high values of flexural modulus, indicating their exceptional rigidity and resistance to bending.
G10, a high-pressure fiberglass laminate, is a type of epoxy grade thermoset composite known for its high strength, low moisture absorption, and excellent electrical insulating properties. The flexural modulus of G10 is remarkably high, typically around 20,000 MPa, which makes it an ideal material for applications requiring superior mechanical strength and rigidity.
Carbon fiber, on the other hand, is a composite material consisting of extremely thin fibers composed primarily of carbon atoms. Carbon fiber composites have a flexural modulus that can range from 70,000 to over 150,000 MPa, depending on the orientation of the fibers and the type of resin used. This high flexural modulus makes carbon fiber composites a popular choice in industries requiring materials with high stiffness and low weight, such as aerospace and automotive.
Plastics and Polymers
The composition of plastics and polymers can significantly influence their flexural modulus. Factors such as the molecular structure of the polymer and the composition of the composite, including reinforcement materials, can lead to a diverse range of values in different materials.
For instance, materials like Sheet Moulded Compound (SMC) and Dough Moulded Compound (DMC) exhibit a high flexural modulus, in addition to a high distortion temperature and high solvent resistance, which render them advantageous compared to other types of plastics.
On the other hand, materials such as elastomers, which display the lowest flexural modulus, are notably more flexible and prone to bending when subjected to stress.
Thermoset Composites
Thermoset composites, a type of composite material, fabricated with thermoset matrices typically utilizing fibers such as glass, carbon, or aramid, and combined with resins like polyesters and vinyl ester, can have varying flexural modulus values based on the choice of substrate and resin system.
The choice of substrate can influence the flexural modulus of thermoset composites. Factors such as the span length-to-specimen thickness ratio and the properties of the substrate material can impact both the flexural modulus and the strength of the composites.
Similarly, the selection of a resin system can have a significant impact on the flexural modulus of thermoset composites by affecting the interfacial adhesion between the substrate and the resin, as well as the mass ratio of thermoplastic resin to composite fillers.
Metals and Alloys
Compared to plastics and polymers, metals and alloys typically exhibit higher flexural modulus values, signifying their greater rigidity and resistance to bending. The higher flexural modulus in metals and alloys is primarily attributed to their modulus of elasticity, or Young’s Modulus, which represents the material’s stiffness and ability to resist bending.
The flexural modulus of metals and alloys can be influenced by the atomic structure. For example, the body-centered cubic structure commonly found in most steels can significantly impact the flexural modulus. Specific alloys like the Aluminum alloys in the 3xxx, 5xxx, and 6xxx series, such as aluminum alloy 6063, are recognized for their high flexural modulus, making them ideal for applications requiring high stiffness and rigidity.
Challenges and Future Developments in Flexural Modulus Research
Despite the valuable insights that the flexural modulus provides about a material’s properties, current testing methods have their limitations. For instance, flexural modulus testing methods are restricted in their ability to accurately measure flexural strength for specific materials. Moreover, several inconsistencies in testing procedures can impact the test results, making it challenging to get accurate measurements.
However, recent advancements in materials and technologies offer new opportunities for improving flexural modulus properties and expanding applications. Some of these advancements include:
- The exploration of functional polymers and composites using 3D printing-based technologies
- The examination of the impact of temperature on the flexural strength and modulus of PLA
- The comparison of flexural moduli of composites made from old newspaper fibers and polypropylene with other composites
These developments show promise in enhancing flexural modulus properties and opening up new possibilities for various applications.
Limitations of Current Test Methods
Certain constraints are inherent in current test methods for flexural modulus, including the ASTM D790 method. For instance, these methods may not accurately measure flexural modulus in real-world applications due to unaccounted errors in crosshead movement that can impact accuracy, and the need for a deflectometer to achieve more precise modulus determination.
Typical inconsistencies in testing procedures encompass errors in determining flexural strength, such as:
- Wedging stress
- Contact stress
- Load mislocation
- Beam compliance
Potential errors introduced by support and machine base compliance can also lead to variations in test results. However, advancements in testing methods, such as the use of fillers like fiber-like wollastonite or cube-shaped calcium carbonate to improve the flexural modulus, offer potential solutions to these challenges.
Emerging Materials and Technologies
With emerging materials and technologies, like advanced composites and additive manufacturing, there’s exciting potential for enhancing flexural modulus properties and broadening applications. Advanced composites, for example, can increase the fiber content and integrate different fillers, resulting in a notable elevation of stiffness and overall mechanical properties of isotropic materials.
Additive manufacturing technologies, particularly Fused Deposition Modeling (FDM), can influence the flexural modulus by allowing precise manipulation of reinforcement distribution and build orientation, both of which are vital for flexural properties. Furthermore, advancements in 3D printing technology enhance the flexural modulus in customized products through the freedom to create complex shapes and reinforce with fibers.
Summary
In conclusion, the flexural modulus plays a critical role in determining a material’s resistance to bending, making it a vital property in material selection across different industries. While the current testing methods have their limitations, the emergence of new materials and technologies promises to improve the accuracy of flexural modulus evaluation, propelling us towards a future where we can make more informed decisions in material selection and design.
Frequently Asked Questions
Is higher flexural modulus better?
Yes, a higher flexural modulus indicates a stiffer material, while a lower flexural modulus signifies greater flexibility.
What is the difference between Flexural Modulus and Flexural Strength?
Flexural Modulus and Flexural Strength are two key properties used in material science and engineering to describe the mechanical properties of materials. However, they denote different aspects of a material’s behavior under stress.
Flexural Modulus, also known as the bending modulus, is a measure of a material’s stiffness. It quantifies the material’s resistance to bending deformation under an applied load. In other words, it’s the ratio of stress to strain in flexural deformation or the slope of the stress-strain curve in the elastic region. A higher flexural modulus signifies a stiffer material, indicating a greater resistance to bending.
On the other hand, Flexural Strength, also known as bending strength or modulus of rupture, is the maximum amount of stress a material can withstand without breaking. It signifies the highest stress experienced within the material at its moment of rupture. It’s a measure of the maximum load carrying capacity of a material before it fails under bending.
In summary, while flexural modulus is a measure of the stiffness of a material (resistance to deformation), flexural strength is a measure of the maximum stress a material can withstand before it breaks.
How do you calculate flexural strength?
To calculate the flexural strength of concrete, use the formula F= PL/ (bd2), where F represents the flexural strength in MPa, P is the failure load in N, L is the effective span of the beam (400mm), and b is the breadth of the beam (100mm).
What does a high flexural strength mean?
A high flexural strength means that the material can withstand more impacting forces before breaking, as it indicates the amount of force required to break a test sample of a defined diameter.
What is meant by flexural modulus?
Flexural modulus refers to the stiffness or resistance to bending of a material. It describes the material’s ability to deform under bending stress.
How does flexural modulus influence material selection?
The flexural modulus affects material selection by indicating stiffness and resistance to bending, which is crucial in industries like construction and aerospace. Therefore, it is an important factor to consider when choosing materials for applications.