In the engineering of composite materials, compressive strength is a crucial metric for assessing their capacity to withstand force without yielding. Directly relevant to material selection and design, compressive strength ensures components can endure real-world pressures. This guide dives into the evaluation of compressive strength in composite materials, its significance, and how cutting-edge research and testing methods are driving industry standards and applications.
Key Takeaways
- Compressive strength is critical in determining a material’s ability to resist size reduction under load and is a key factor in designing structures for durability and resilience.
- Several factors influence the compressive strength of composite materials, including fiber reinforcement, resin type, and manufacturing processes, with specialized testing methods like the Universal Testing Machines and standards such as ASTM D695 and ISO 604 used for accurate assessment.
- High compressive strength composite materials find applications across diverse industries, including construction, aerospace, and automotive, due to advantages such as improved strength-to-weight ratios and resistance to environmental factors, with recent advancements including the development of nanocomposites and novel manufacturing techniques.
Understanding Compressive Strength in Composite Materials
Compressive strength quantifies a material’s capacity to withstand size reduction when subjected to load, without fracturing. It is calculated as CS = F / A, where F represents the maximum load applied to the material, and A is the original cross-sectional area of the specimen being tested. This property is of paramount importance in the design of structures as it directly influences the material’s ability to withstand maximum compressive stress and maintain integrity under compression.
Composite materials, commonly used in a variety of applications, owe much of their durability and resilience to their compressive strength. These materials include a combination of two or more constituent materials with different physical or chemical properties, which when combined, produce a material with characteristics different from the individual components. In cases where the material fails completely, it is often due to a lack of sufficient compressive strength.
Compressive vs. Tensile Strength
While compressive strength refers to the capacity of a material to resist fracture under compression, tensile strength resists tension, referring to its ability to resist fracture under tension or tensile forces. The scientific rationale behind this disparity is that tensile stresses tend to separate the atoms of a material, while compressive strength resists compression, bringing the atoms closer together.
Grasping the concepts of both compressive and tensile strength carries significant weight in materials science, as they dictate how materials behave and perform under diverse forces and loads. Tests for compressive and tensile strengths are imperative to comprehend material properties, with tensile stress measures taken through compression and tensile testing.
Role of Compressive Strength in Composite Materials
Compressive strength plays a pivotal role in the performance and durability of composite materials. It directly influences the design, particularly in the stress block area, where high compressive strength is sought to avoid failure. For instance, the compressive strength of carbon fiber composites typically ranges from 30 to 50% of their tensile strength, making it a crucial property in determining the material’s ability to endure compressive forces, mitigate matrix cracks, and minimize permanent failures caused by impact tests.
Testing Methods for Compressive Strength in Composite Materials
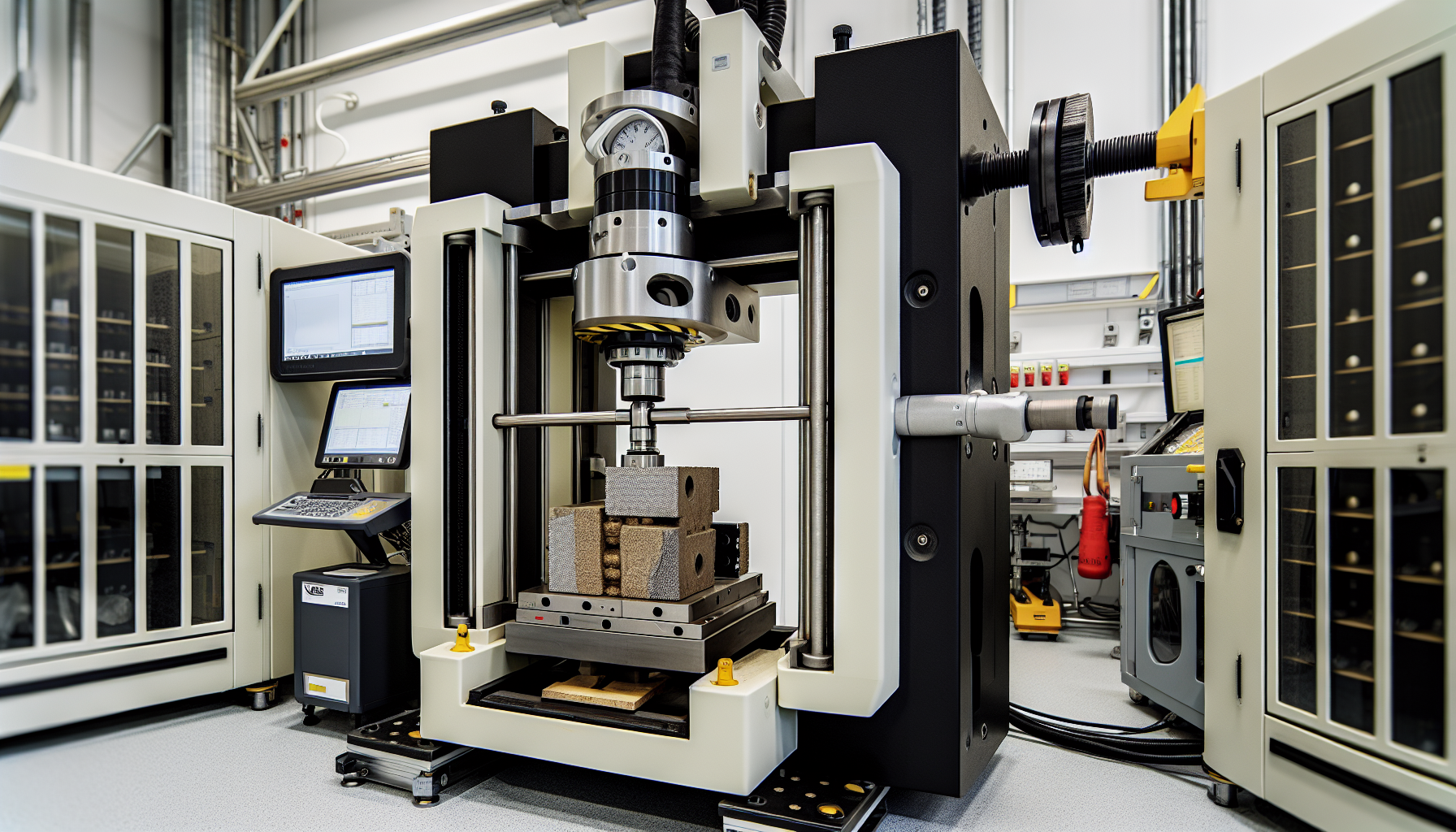
Different testing methods are employed to gauge the compressive strength of composite materials, thereby ensuring their suitability for particular applications. Among these, Universal Testing Machines are frequently employed for assessing the ultimate compressive strength by exerting a controlled compressive force on the material and gauging its reaction.
One such machine is the Universal Testing Machine, which applies a controlled compressive load to the specimen being tested and measures its response. It is reliable for measuring compressive strength as it can conduct a wide range of tests with exceptional precision, such as:
- Tensile tests
- Compression tests
- Flex tests
- Peel tests
- Puncture tests
- Friction tests
- Shear tests
For a standardized, comparable evaluation across various materials, test methods like ASTM D695 and ISO 604 are used. These tests guarantee uniform application of load and clear procedures, facilitating an accurate and reliable assessment of the materials under compression.
Universal Testing Machines
Universal Testing Machines deliver precise and dependable outcomes by determining the uniaxial compressive stress reached by a material before failure. They operate by utilizing a rotating ball screw to drive a load-bearing crosshead up and down, allowing them to apply forces in tension, compression, and other modes. However, drawbacks may stem from calibration issues or specimen misalignment, resulting in inconsistent results.
Specific Test Methods for Composite Materials
Besides universal testing machines, specific test methods like ASTM D695 and ISO 604 are also employed to measure compressive strength. Compressive strength tests, such as ASTM D695, are utilized for the assessment of compressive characteristics of inflexible plastic materials, mainly within the United States, while ISO 604 functions as the corresponding compressive strength test method utilized within the ISO system to assess the same property in composite materials.
While both methods involve applying an external compressive force to the material and measuring its response, their suitability may be constrained by the particular circumstances, material characteristics, and testing criteria. However, the results obtained from the ASTM D695 and ISO 604 tests exhibit minimal variance, suggesting coherence between these two standard methodologies.
Factors Affecting Compressive Strength in Composite Materials
Several factors can affect the compressive strength of composite materials. These include:
- Fiber reinforcement, which significantly enhances the compressive strength of composite materials by improving their static and fatigue strength.
- Resin types, which influence the compressive strength through factors such as filler volume, resin formulation, and the degree of cross-linking.
- Manufacturing processes.
The microstructure of composite materials, and thus their mechanical properties including compressive strength, are largely influenced by manufacturing processes. By adjusting process parameters like resin content during manufacturing, the internal structure of composites can be customized, leading to enhanced performance and superior quality output.
Fiber Reinforcement
The type, orientation, and volume fraction of fiber reinforcement can significantly impact the compressive strength of composite materials. High-modulus carbon fiber reinforced polymers (CFRPs), for instance, can notably enhance mechanical stiffness. The orientation of fibers plays a crucial role, as fibers aligned in specific directions can enhance the compressive strength of the material based on the load and application.
Furthermore, a higher volume fraction of fibers typically results in enhanced compressive strength as it elevates the overall density and strength of the composite material.
Resin Types
The choice of resin can also influence the compressive strength of composite materials, as different resins offer varying levels of strength, stiffness, and durability. The prevalent varieties of resin utilized in composite materials include:
Epoxy resins can significantly enhance compressive strength due to their specific characteristics.
Manufacturing Processes
Manufacturing processes, such as molding pressure and curing conditions, can affect the compressive strength of composite materials by influencing their microstructure and overall quality. When the optimal molding pressure, in combination with other process parameters, is applied, it can enhance the impact strength and tensile behavior of the fabricated composites.
Furthermore, curing conditions, including temperature and time, significantly influence the compressive strength by affecting the polymer cross-linking process and the resulting microstructure of the material.
Applications of High Compressive Strength Composite Materials
Owing to their outstanding performance and durability, high compressive strength composite materials find usage across multiple industries such as construction, aerospace, and automotive. They offer improved strength-to-weight ratios, lightweight and enhanced performance, versatility, resistance to environmental factors, corrosion resistance, flexible design options, and the ability to customize performance properties for specific applications.
In the aerospace industry, they play a crucial role in the construction of aircraft, spacecraft, and re-entry vehicles, offering various benefits such as resistance to weathering, fatigue, high temperatures, and providing exceptional strength and stiffness-to-density ratios.
In the automotive industry, these materials provide benefits such as:
- Increased structural strength
- Improved fatigue resistance
- Reduced weight leading to enhanced fuel efficiency
- Cost-effective reinforcement solution when combined with metal structures
Aerospace Industry
Aerospace applications of high compressive strength composites include aircraft structures, engine components, and lightweight materials for improved fuel efficiency. Composites such as carbon fiber-reinforced plastic (CFRP) and glass-fiber-reinforced plastic (GFRP) are utilized in aircraft structures to achieve larger fan sizes and reduce weight by integrating structural components.
High compressive strength composites also contribute to significant weight reduction, improved engine performance, reduced emissions, and enhanced resistance to corrosion.
Automotive Industry
The automotive industry utilizes high compressive strength composites for lightweight components, improved crashworthiness, and enhanced performance. Composites such as continuous carbon fiber and carbon fiber reinforced plastics (CFRP) contribute to the automotive industry by enabling the development of lighter, safer, and more fuel-efficient vehicles. They also facilitate innovation in low-volume high-end vehicles and motorsports, and their utilization is extending to various engineering disciplines.
Advancements in Composite Materials for Enhanced Compressive Strength
Recent advancements in composite materials have led to the development of nanocomposites and novel manufacturing techniques for enhanced compressive strength. Nanocomposites, characterized by the inclusion of nanoparticles, hold the promise of significantly augmenting the compressive strength of composite materials. They improve the mechanical properties of the composites, leading to improvements not only in compressive strength, but also in tensile strength and fracture toughness.
Meanwhile, exploration into innovative manufacturing methods, such as improving the compressive strength and ductility of glass fiber reinforced polymer (GFRP) composite bars, as well as enhancing the compressive properties and flexural stiffness of CFRP composite surfaces, have been undertaken to address the challenges posed by brittle materials.
Nanocomposites
Nanocomposites, which incorporate nanoscale particles or fibers, can significantly improve the compressive strength of composite materials by optimizing their microstructure and mechanical properties. The superior compressive strength is a result of the distinctive mechanical and physical properties of nanomaterials such as carbon nanotubes, known for their high moduli and exceptional strength. These nanoscale additives play a crucial role in improving the mechanical properties of the nanocomposites and are selected based on the specific property enhancements sought.
Novel Manufacturing Techniques
Novel manufacturing techniques, such as additive manufacturing and advanced molding processes, can enhance the compressive strength of composite materials by optimizing their design and fabrication. Techniques like incorporating reinforcement materials like ceramic or carbon fibers within a metallic matrix can improve their compressive strength.
Furthermore, advanced molding processes, such as compression molding, have the potential to enhance the compressive strength of composite materials.
Case Studies: Successful Implementation of High Compressive Strength Composites
Several case studies demonstrate the successful implementation of high compressive strength composites in various industries. In civil engineering, materials such as:
- Man-made composite honeycomb
- Steel
- Ultra-high-strength concrete (UHSC)
- Cement composites
- Circular CFFT columns with FRP confinement
Steel beams offer benefits such as robustness, support in complex structures, and versatility in diverse applications that demand durability, resilience, and the ability to withstand loads.
In aerospace applications, high compressive strength composites contribute to:
- significant weight reduction
- improved engine performance
- reduced emissions
- enhanced resistance to corrosion
The use of carbon fiber-reinforced polymers (CFRP) and glass-fiber-reinforced plastic (GFRP) in aircraft structures is a testament to this.
In the automotive industry, high compressive strength composites, such as continuous carbon fiber and carbon fiber reinforced plastics (CFRP), enable the development of lighter, safer, and more fuel-efficient vehicles.
Civil Engineering
In the realm of civil engineering, applications like porous concrete pavement with nanosilica and lightweight self-consolidating concrete have leveraged high compressive strength composites. The incorporation of nano-silica enhances the compressive strength of the concrete, making it more resilient to substantial loads and traffic.
Similarly, high compressive strength composites play a significant role in lightweight self-consolidating concrete as they enhance the mechanical properties, particularly the compressive strength of concrete.
Aerospace Applications
In the aerospace sector, high compressive strength composites find their use in aircraft structures with the help of carbon fiber-reinforced polymers and in engine components through advanced composite materials. The integration of structural components using composites such as carbon fiber-reinforced plastic (CFRP) and glass-fiber-reinforced plastic (GFRP) allows for larger fan sizes and weight reduction.
The use of high compressive strength composites also contributes to significant weight reduction, improved engine performance, reduced emissions, and enhanced resistance to corrosion.
Automotive Innovations
Innovations in the automotive industry involving high compressive strength composites encompass the creation of compressed oil palm frond composite boards and the integration of fibrillated polypropylene fibers into high-performance concrete. The former is employed for the production of diverse components such as package trays, door panels, headliners, and dashboards.
On the other hand, the incorporation of fibrillated polypropylene fibers into high-performance concrete results in increased strength, improved energy absorption capacity, and a decrease in plastic shrinkage cracks.
Summary
Understanding the compressive strength of composite materials and the factors that influence it can pave the way for more efficient and durable applications in various industries. From the construction industry making use of high-strength concrete to the aerospace and automotive industries leveraging lightweight and high-strength composites, the role of compressive strength is undeniably significant.
With advancements in nanotechnology and manufacturing techniques, the potential for enhancing the compressive strength of composites is vast. As we continue to explore and innovate, the limits of what we can achieve with high compressive strength composites continue to expand, promising a future of stronger, lighter, and more efficient structures and materials.
Frequently Asked Questions
Are composites good in compression?
Composites are strong in tension and compression due to the combination of materials, with one strong in tension but weak in compression, and the other strong in compression but weak in tension. However, the compressive strength of composites is generally lower than their tensile strength.
What material has good compressive strength?
Steel, concrete, ceramics, and composite materials like glass epoxy have good compressive strength
What is the meaning compressive strength?
Compressive strength refers to a material or structural element’s ability to withstand loads that reduce its size when applied, through a test that applies force until the sample fractures or deforms.
What is the importance of compressive strength in composite materials?
Compressive strength is crucial in composite materials because it directly affects their ability to withstand stress and maintain integrity under compression, thus impacting the design of structures.
How does the type of fiber reinforcement affect the compressive strength of composite materials?
The compressive strength of composite materials can be significantly impacted by the type, orientation, and volume fraction of fiber reinforcement. Varying these factors can lead to different levels of strength.