From the sleek exterior of an airplane to the intricate components of a life-saving medical device, custom machined plastic parts play a crucial role in countless industries. These parts boast unique properties and precision that make them indispensable in various applications. In this blog post, we’ll delve into the exciting world of plastic machining, exploring the essentials, benefits, and innovative technologies that shape this field. Join us on this journey to uncover the secrets behind high-quality plastic components and learn how to select the perfect partner for your custom plastic machining needs.
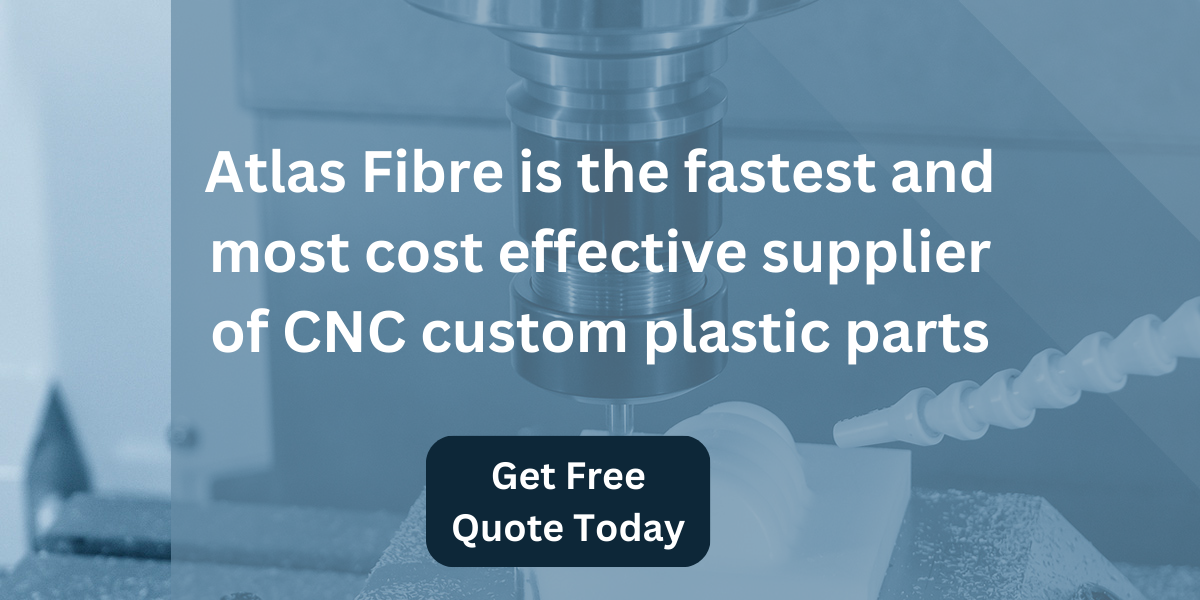
Key Takeaways
- Atlas Fibre provides machined plastic parts with over 60 years of experience.
- Successful custom plastic part projects rely on essential factors such as material selection, cutting-edge equipment, and precision techniques.
- Atlas Fibre is a trusted supplier offering expertise, quality, and comprehensive services for custom plastic machined parts.
Understanding Machined Plastic Parts
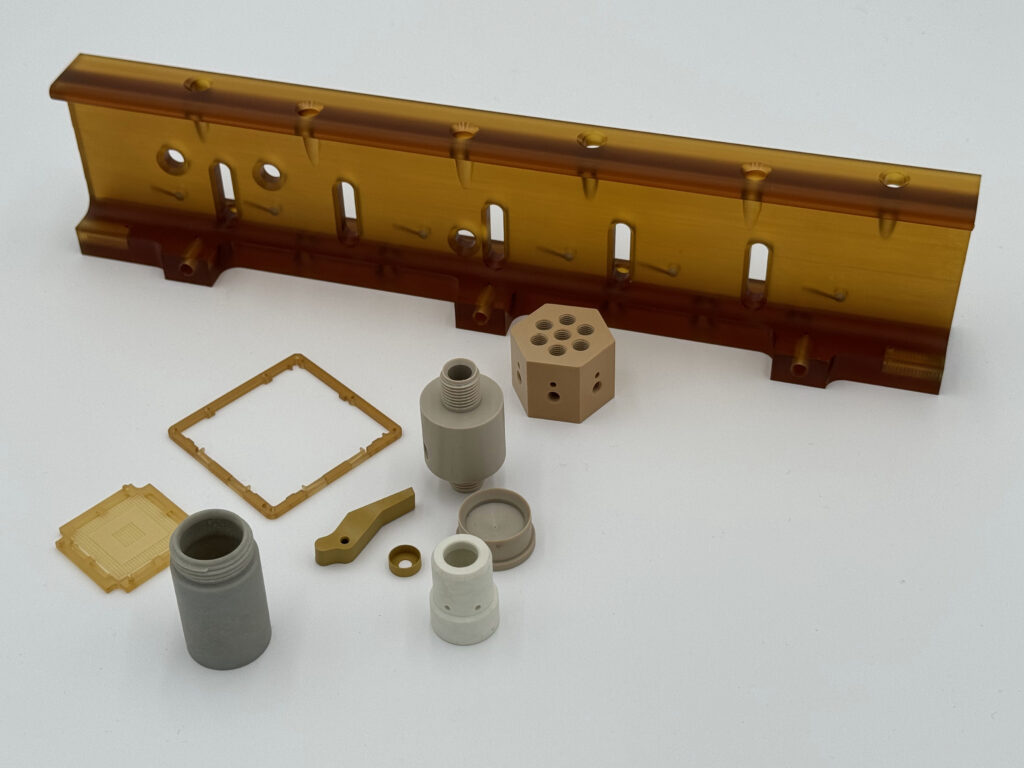
Machined plastic parts are in high demand across numerous industries, including:
- Aerospace
- Medical
- Electronics
- Telecommunications
With over 60 years of experience, Atlas Fibre offers a wide range of plastic machining solutions, including plastic machining services, ensuring that your custom plastic fabrication needs are met with precision and expertise.
The Essentials of Plastic Machining
Plastic machining is a complex process that involves cutting, shaping, and forming plastic materials into the desired shapes and dimensions. The key to producing high-quality custom machined plastic parts lies in mastering the essentials: material selection, cutting-edge equipment, and precision techniques. These elements work in harmony to ensure optimal results in the final product.
We will subsequently delve into the significance of these factors and their role in delivering outstanding machined plastic parts.
Material Considerations
Selecting the right plastic material is critical to achieving the desired properties and performance in machined plastic parts. Factors such as the type of plastic, its properties (e.g., hardness, temperature resistance), and the intended application must be carefully considered when selecting the appropriate plastic material for machining. For instance, carbide-tipped tools are essential for machining glass-reinforced materials.
In machining, chip control is crucial. Without effective chip control, chips can disrupt the process and lead to delays. Thus, material considerations play a crucial role in ensuring the success of plastic machining projects.
Cutting-Edge Equipment
Utilizing cutting-edge equipment is key to ensuring high-quality and efficient production of custom plastic parts. Companies like Atlas Fibre use high-precision CNC systems equipped with both dry and wet processing along with internally cooled tools to achieve superior results.
Modern CNC machining centers offer the capability of producing complex, small and large parts made of plastic. Investment in advanced technology and cutting-edge equipment enables plastic machining companies to produce precise and consistent results, catering to the continuously changing demands of diverse industries.
Precision Techniques
Precision techniques are vital for achieving tight tolerances and intricate designs in machined plastic parts. These techniques include:
- Selecting an appropriate machining process
- Reducing clamping forces
- Utilizing a suitable cutting tool
- Maintaining a cool temperature
- Employing CNC machining
Utilizing CNC technology guarantees exact cuts and avoids errors, leading to less material waste and quicker turnaround times.
Mastering precision techniques enables plastic machining companies to produce final components that meet the highest standards and address the specific needs of each application, including plastic polishing.
Advantages of CNC Plastic Machining
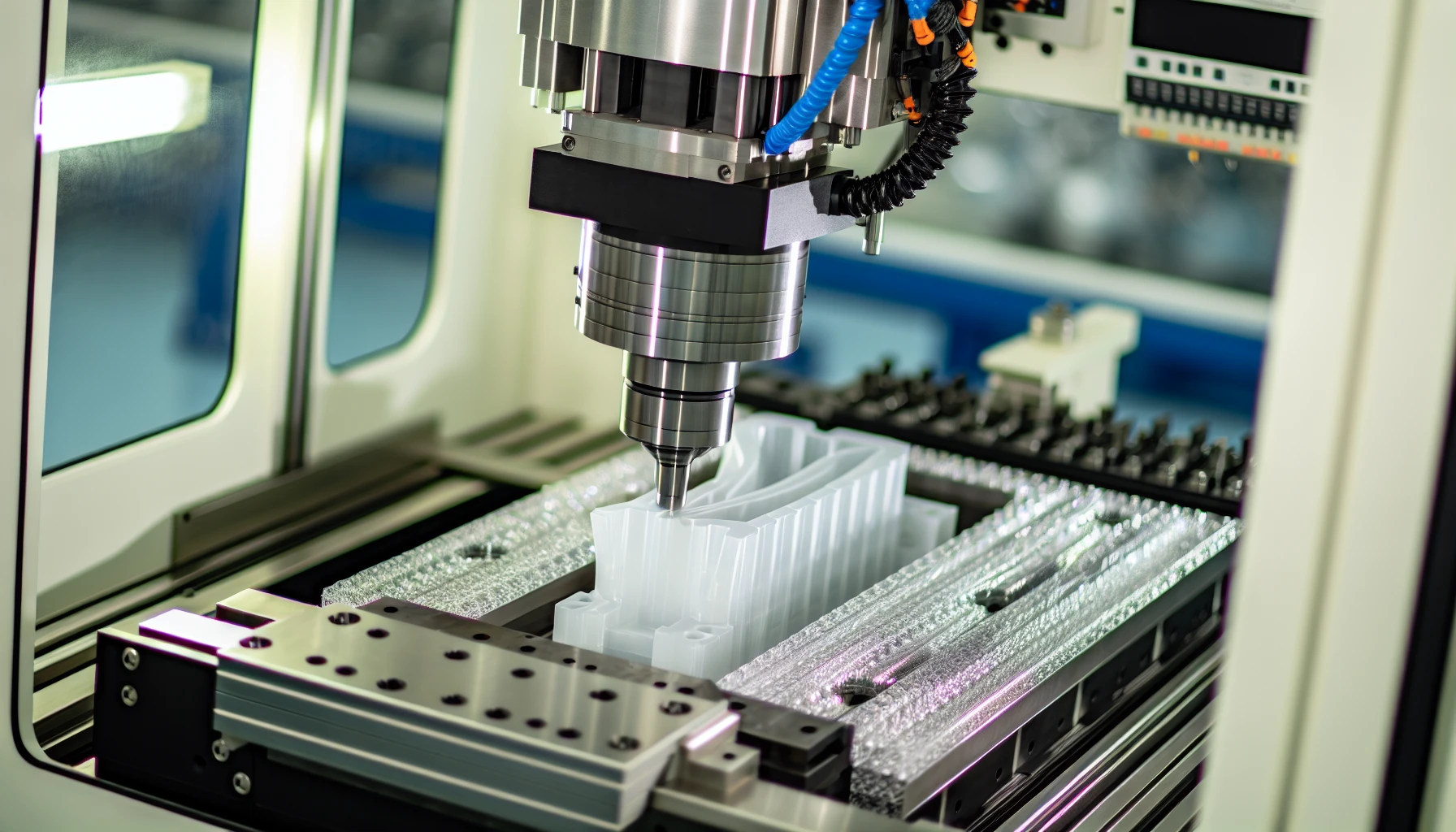
CNC plastic machining offers numerous advantages over traditional methods, including speed, accuracy, and cost-effectiveness. The use of CNC technology in plastic machining ensures precise and consistent results, leading to high-quality plastic components. With the ability to produce custom machined plastic parts with tolerances as tight as 0.0001”, CNC machining is an indispensable tool in the production of high-performance plastic parts.
Moreover, the increased efficiency and reduced waste associated with CNC plastic machining make it an attractive choice for businesses seeking to optimize their production processes and reduce overall costs.
Custom Plastic Fabrication Solutions
Custom plastic fabrication solutions provide tailored services to meet specific requirements, from prototype to full-scale production. By partnering with a plastic machining company that offers comprehensive services and expertise in custom plastic fabrication, businesses can ensure that their plastic components are designed and manufactured to the highest standards.
We will subsequently discuss how custom plastic fabrication solutions are designed to meet specific requirements, and their ability to handle projects from prototype to mass production.
Tailored for Your Specifications
Custom plastic fabrication solutions are designed to ensure that machined plastic parts meet exact specifications and industry standards. By crafting a detailed blueprint, selecting the appropriate custom plastic machining process, adhering to tight tolerances and precise designs, and customizing manufacturing solutions, plastic machining companies can deliver high-quality plastic components tailored to fit the unique requirements of each application. This level of customization ensures optimal performance and functionality of the final product, as well as cost savings by optimizing the custom solutions to fit specific requirements and budgets.
From Prototype to Production
Comprehensive services in custom plastic fabrication cover all stages of production, including:
- Prototyping
- Design and engineering
- CNC machining
- Vacuum forming
- Injection molding
- Assembly and finishing
- Packaging and shipping
By working with a plastic machining company that offers a complete range of services, businesses can ensure a smooth transition from prototype to full-scale production.
The plastic fabrication process typically involves the following steps:
- Design
- Prototype
- Testing and iteration
- Manufacturing process selection
- Tooling
- Production
- Certification and testing
Partnering with a company that can manage every step of this process ensures that the final product meets the highest quality standards and is delivered on time and within budget.
Selecting the Right Plastic Machining Company
Selecting the right plastic machining company is crucial to the success of any custom plastic part project. Factors to consider include:
- Expertise
- Technical knowledge
- Quality management certifications
- Vertical integration capabilities
- Track record of excellence in the industry
We will further discuss various considerations when choosing potential plastic machining partners, such as:
- Criteria for excellence
- Partnership and support
- ISO 9001:2015 certification
- The advantages of collaborating with a vertically integrated company.
Criteria for Excellence
Partnering with a plastic machining company that meets the criteria for excellence is vital for ensuring top-quality custom machined plastic parts. These criteria include experience, technical knowledge, and a proven track record in the industry. By selecting a company that demonstrates expertise in plastic machining processes, material selection, and effective new product introduction, businesses can be confident that their custom plastic parts will be produced with the highest level of quality and attention to detail.
Partnership and Support
A robust partnership and support system are pivotal for seamless execution and enduring success of any custom plastic part project. Working with a plastic machining company that offers comprehensive support, from design to production, ensures that all aspects of the project are handled efficiently and with the utmost care.
A successful partnership should be based on trust, effective communication, and a shared commitment to delivering high-quality plastic components that meet or exceed the expectations of both parties.
ISO 9001:2015 Certification
ISO 9001:2015 certification is an important factor to consider when selecting a plastic machining company, as it demonstrates a commitment to quality management and continuous improvement. A company with this certification has established a quality management system that is compliant with the requirements outlined by the International Organization for Standardization (ISO).
This certification ensures that the company has executed processes and procedures to consistently provide high-quality products and services to its customers, guaranteeing traceability, documented procedures, and a process approach to increase customer satisfaction and overall performance.
Vertically Integrated
Working with a vertically integrated plastic machining company offers numerous advantages, such as:
- Streamlined process from material sourcing to final product delivery
- Optimization of efficiency, cost reduction, quality control, and improved coordination throughout the entire process
- Production of custom plastic parts with the highest level of quality
- On-time delivery and staying within budget
These advantages help ensure that your custom plastic parts are produced with the highest level of quality and delivered on time and within budget. Atlas Fibre has the volume to purchase directly from plastics manufacturers and not through distribution, saving money on your project.
Industry Applications for Machined Plastic Parts
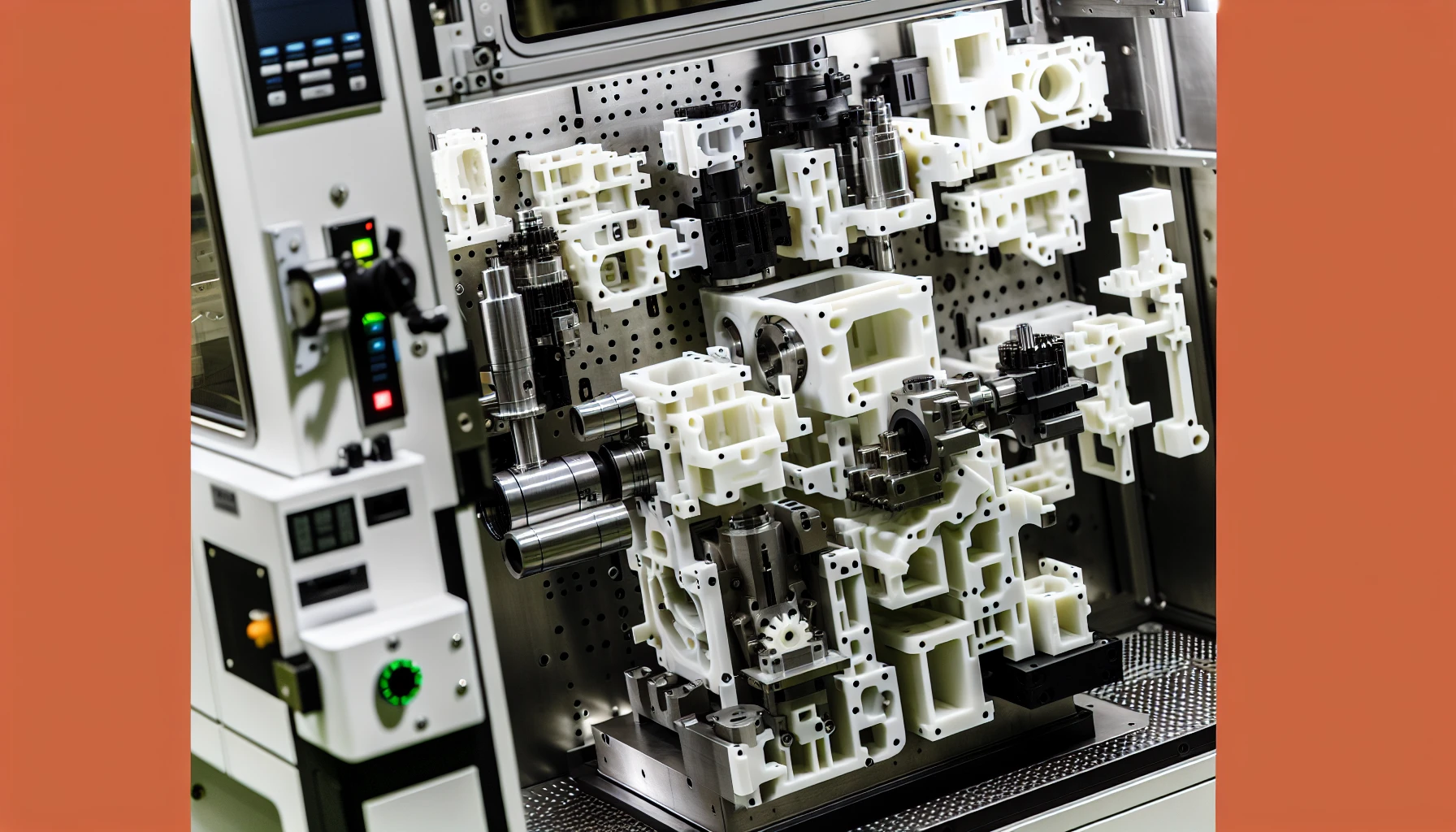
Machined plastic parts play an essential role in a variety of industries, including:
- Aerospace
- Medical
- Electronics
- Telecommunications
The unique properties of these high-quality plastic components, including their thermoplastic materials, make them suitable for numerous applications, ranging from lightweight aerospace components to intricate medical devices with complex components.
With the advancements in plastic machining technology, the potential applications for machined plastic parts continue to expand, making them an integral part of many industries’ daily operations.
Quality Control in Plastic Machining
Quality control is a critical aspect of plastic machining, ensuring that the final products meet safety, performance, and regulatory standards. This process encompasses various stages, including:
- Design
- Mold and pre-production inspection
- In-process quality control
- Final inspection
By implementing stringent quality control measures and utilizing state-of-the-art equipment, plastic machining companies can guarantee the production of high-quality plastic components that exceed customer expectations and adhere to industry standards.
Innovations in Plastic Machining Technology
Recent innovations in plastic machining technology have revolutionized the field, contributing to improved efficiency, accuracy, and cost savings.
These advancements have made it possible to produce high-quality plastic components more effectively and sustainably.
As technology continues to advance, the potential for even greater innovations in plastic machining remains an exciting prospect for the future.
Choosing a Heavily Automated Partner
Selecting a heavily automated partner for your plastic machining needs offers numerous advantages, including reliability, flexibility, and lower costs due to reduced manual labor and higher utilization. Automation in plastic machining enables increased precision, productivity, and consistency, resulting in a more efficient and cost-effective production process.
We will further analyze the benefits of selecting a heavily automated partner for plastic machining.
Ensures Reliability of Schedule
Automation in plastic machining ensures schedule reliability by optimizing the production process, minimizing errors, and enhancing efficiency, resulting in dependable schedules and timely delivery of machined plastic parts.
Automated systems offer several advantages for plastic machining companies:
- They can operate with minimal supervision, enabling round-the-clock operation.
- They reduce the need for manual labor, increasing efficiency and reducing costs.
- They allow for consistent and precise machining, resulting in high-quality components.
- They enable companies to deliver components on time, ensuring customer satisfaction and the success of your project.
Flexible Response Due to Excellent Processes
Excellent processes in plastic machining facilitate a responsive approach by:
- Generating less waste
- Implementing machining techniques that reduce material removal
- Permitting variability in feeds and speeds
- Providing finish flexibility
As a result, a heavily automated partner can quickly adapt to any schedule changes and accommodate new orders or modifications, ensuring the smooth execution of your plastic machining project.
Lower Costs Due to Less Manual Labor and Higher Utilization
Automation in plastic machining offers cost savings due to decreased manual labor and increased utilization. With less manual labor involved, machines can be operated for longer periods of time, resulting in increased utilization and reduced labor costs. Furthermore, automation enhances efficiency and productivity, allowing for more machined plastic parts to be produced within a given timeframe. This ultimately leads to lower costs and a more cost-effective production process.
Atlas Fibre is the Ideal Plastic Machined Parts Supplier
Atlas Fibre is the ideal plastic machined parts supplier, offering expertise, quality, and comprehensive services for all your custom plastic part needs. With extensive experience in machining and fabricating plastics and non-metallic materials, Atlas Fibre is a manufacturer and supplier of:
- thermoset sheet
- rod
- tube
- precision fabrication services
A partnership with Atlas Fibre guarantees the production of your custom plastic parts with superior quality and expertise, contributing to the success of your project.
Summary
In conclusion, custom machined plastic parts play a vital role in various industries, offering unique properties and precision. By understanding the essentials of plastic machining, such as material selection, cutting-edge equipment, and precision techniques, businesses can ensure the production of high-quality plastic components. Partnering with a reliable and heavily automated plastic machining company, such as Atlas Fibre, guarantees the success of your custom plastic part project. As plastic machining technology continues to advance, the potential for even greater innovations and applications in this field remains an exciting prospect for the future.
Frequently Asked Questions
What industries commonly use machined plastic parts?
Machined plastic parts are commonly used in aerospace, medical, electronics, and telecommunications industries.
How does automation in plastic machining improve cost-effectiveness and efficiency?
Automation in plastic machining reduces manual labor, increases productivity, and improves accuracy, resulting in improved cost-effectiveness and efficiency.
What factors should be considered when selecting a plastic machining company?
When selecting a plastic machining company, look for one that has expertise and technical knowledge, as well as quality management certifications and vertical integration capabilities.
How do recent innovations in plastic machining technology impact the industry?
Recent innovations in plastic machining technology have enabled manufacturers to produce high-quality components more efficiently, accurately, and cost-effectively, benefiting the industry.
What role does quality control play in plastic machining?
Quality control plays an essential role in plastic machining, ensuring that the finished products meet safety, performance, and regulatory standards.