Welcome to the fascinating world of plastics machining, where innovation and precision merge to create intricate components for various industries. As you delve into this comprehensive guide, you will discover the essentials of materials, techniques, and compliance. Prepare to embark on a journey that will enrich your knowledge and empower your decision-making when selecting the right plastics machining partner.
Key Takeaways
- Plastics machining is an accurate and secure process used for creating intricate parts from various materials.
- Selecting the right cutting tools, and taking necessary quality control measures are essential for successful plastics machining.
- If needed, choosing a partner with the appropriate security controls and ITAR registration
- Atlas Fibre offers precision fabrication capabilities with ISO 9001:2015 certification to meet all your plastics machining needs.
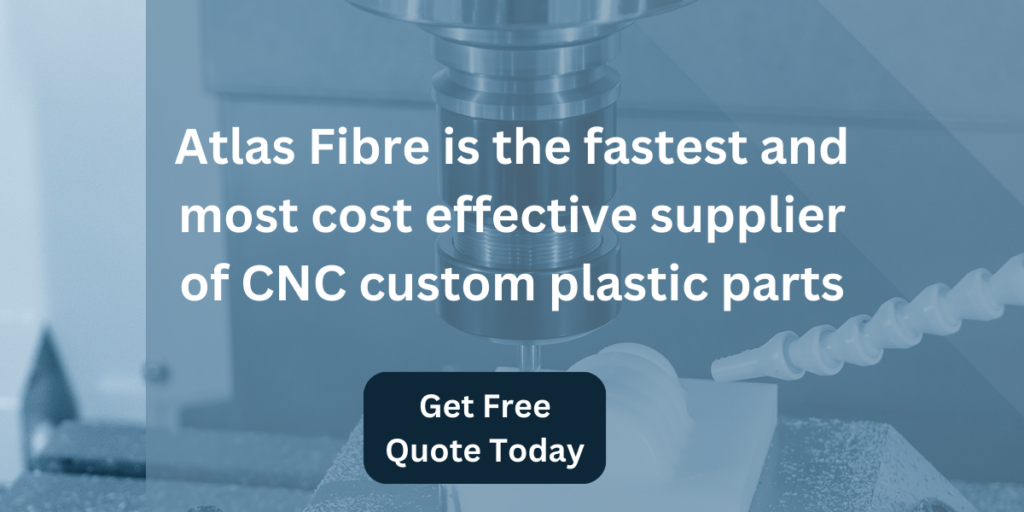
Understanding Plastics Machining: An Overview
The realm of plastics machining revolves around the use of computer numerical control (CNC) machines to produce intricate plastic parts for various applications. CNC machining is a procedure known for its extreme accuracy. It begins with a CAD drawing, which is then converted into a computer program for the CNC system to operate. This manufacturing method is commonly used for processes such as ultrasonic welding, hole-punching, and laser cutting.
CNC Machines have enabled designers to create complex patterns on various materials, including:
- Aerospace parts
- Automotive components
- Decorations
- Consumer goods pieces
- Medical parts
This has revolutionized the design process of these components. However, when handling defense-related components, secure and responsible management of ITAR data is paramount. To ensure data security, it is crucial to regularly test security systems.
Types of Plastic Materials
The machinability of plastic materials is significantly influenced by their properties, such as hardness, strength, creep resistance, solubility and swelling, moisture absorption, and mechanical properties. Some typical plastic materials used in machining include Teflon, Delrin, Nylon, PTFE, ABS plastics, acrylic, HDPE, G10, Phenolic Laminates, and polycarbonate. These materials have a wide range of applications, such as CNC machining, injection molding, manufacturing medical devices, producing parts for the food and beverage industry, creating semiconductor parts, and manufacturing automotive components.
The advantages of common plastic materials include their lightweight nature, insulating properties, corrosion resistance, and versatility. However, they may also possess some disadvantages, such as lower strength compared to metals, limited temperature resistance, and lower wear resistance. Consequently, choosing the right plastic materials for machining operations like polycarbonate, PVC, and Polypropylene is crucial to avoid possible civil fines and other penalties for non-compliance with ITAR regulations.
Key Techniques in Plastics Machining
In the realm of plastics machining, Computer Numerical Control (CNC) lathes hold a significant position. They are instrumental in creating complex designs that are otherwise unattainable with manual machines. The programming of CNC lathes can be done with G-code or specific proprietary code. When dealing with sensitive data like ITAR-regulated materials, robust access control measures are essential.
The world of plastics machining also heavily relies on milling techniques. CNC mills, much like lathes, can be programmed with G-code.
The final key technique in plastics machining is measuring with Coordinate Measuring Machines (CMMs). CMMs are used to measure the physical geometrical characteristics of an object. This measurement may be done in a number of ways including manually by an operator or it may be computer controlled. This technique allows for precise measurements, ensuring the accuracy and quality of the machined plastic parts.
Essential Tools and Equipment for Plastics Machining
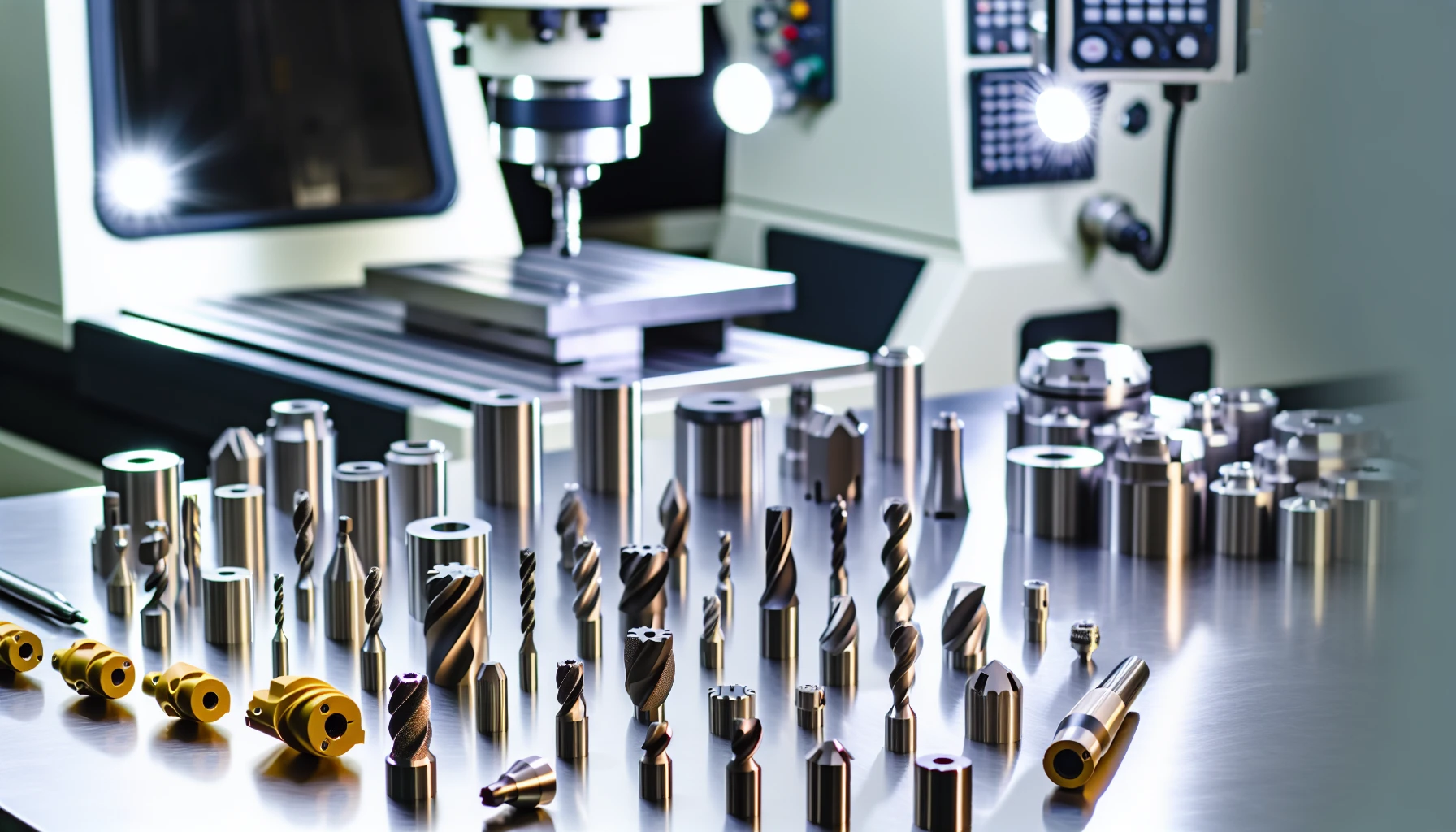
Possessing the right tools and equipment is vital for achieving optimal results in plastics machining. Essential cutting tools for the process include:
- Plastic cutting end mills
- Cutters with appropriate geometry
- Rotary tools
- Reamers
A milling machine plays a significant role in plastics machining by using rotary cutters to remove material from a workpiece in a precise manner, cutting out pockets and altering the overall shape of the plastic material.
In addition to cutting tools, other equipment such as waterjet cutters may be employed for cutting materials in the plastics machining process. Selecting the right tools and equipment ensures that the plastic parts are produced with accuracy and precision, maintaining the highest quality standards.
Cutting Tools
The types of cutting tools used in plastics machining include plastic cutting end mills, cutters specifically designed for machining plastics, and bandsaws for cutting sheets of plastic. For optimal results in the plastic machining process, it’s crucial to align the plastic’s characteristics with appropriate cutter geometry, elect efficient cutting tools and operating parameters, and choose tools that operate within the machine’s power band.
The selection of cutting tools affects the machining of different types of plastic materials by influencing chip compression, plastic deformation, and overall cutting conditions. For instance, metals are typically harder and more rigid than plastics, so machining metals usually necessitates sturdier and more wear-resistant cutting tools. Therefore, the selection of the right cutting tool is instrumental in achieving the desired precision and quality in plastic machining processes.
Machine Setup
Setting up a machine for plastic machining involves the following steps:
- Use multi-axis mills or CNC machine tools capable of processing plastic materials and forming parts with intricate geometries.
- Thoroughly clean the CNC machine and workbench.
- Securely install the necessary tools and fixtures.
- Load the CNC program into the machine tool controller.
Safety measures must be taken into account during the machine setup process. These include:
- Using appropriate cutting fluids
- Avoiding measurement while the spindle is in motion
- Ensuring the machine is not running when loading a tool magazine
- Inspecting tools for sharpness and cracks
- Wearing necessary safety gear.
Correct machine calibration is also a key aspect of plastic machining, as it guarantees accuracy, precision, and regulatory compliance.
ITAR Compliance in Plastics Machining
ITAR compliance is of utmost importance in the plastics machining industry, as it regulates the export of defense and military products. To identify ITAR data and ensure a company is ITAR compliant, it is crucial to properly handle and prevent unauthorized sharing ITAR technical data. The following measures are required:
- End-to-end data encryption
- Key management
- Access control
- Data loss prevention
- Persistent protection of ITAR data
- Strong access control measures
Failure to adhere to ITAR regulations when dealing with international traffic can result in substantial financial penalties, damage to brand reputation, and potentially, a competitive disadvantage.
The cost of ITAR registration follows a three-tier structure, with annual fees ranging from $2,250 to $2,750, plus additional fees for those who have had more than 10 applications reviewed. Maintaining ITAR compliance is vital for companies that handle sensitive defense-related components and operate in respective industries.
Understanding ITAR Regulations
ITAR regulations classify drawings, illustrations, photographs, and other documentation used to construct ITAR-governed military equipment as “technical data”. Under ITAR, any person in the United States who manufactures, exports, temporarily imports, or furnishes defense articles or services must be registered. The US Munitions List (USML) encompasses defense and space-related articles and services, divided into 21 categories of Defense Articles, such as firearms, ammunition, launch vehicles, guided missiles, explosives, and energetic materials, all subject to arms regulations. In this context, related technical data plays a crucial role in ensuring compliance with these regulations.
Violators of ITAR regulations may incur fines of up to $1.2 million, criminal penalties of up to $1 million and up to 10 years imprisonment, as well as civil penalties of up to $500,000. Comprehending and following ITAR regulations is vital for companies engaged in manufacturing, selling, and distributing defense-related products.
Ensuring ITAR Compliance
Achieving ITAR compliance involves registering with the Directorate of Defense Trade Controls (DDTC) and recognizing all ITAR-controlled items in the company’s possession, obtaining prior authorization for any related activities. Non-compliance with ITAR regulations can result in serious consequences, such as civil and criminal penalties, debarment from future exports, and even imprisonment.
An ITAR compliance checklist can be a valuable resource for arms suppliers to assess their ITAR compliance, create an identification system for ITAR-controlled products, and implement a successful ITAR compliance program. Maintaining ITAR compliance is crucial for businesses that handle defense-related components and industries, as it ensures security, privacy, and responsible management of sensitive projects.
Quality Control and Inspection in Plastics Machining
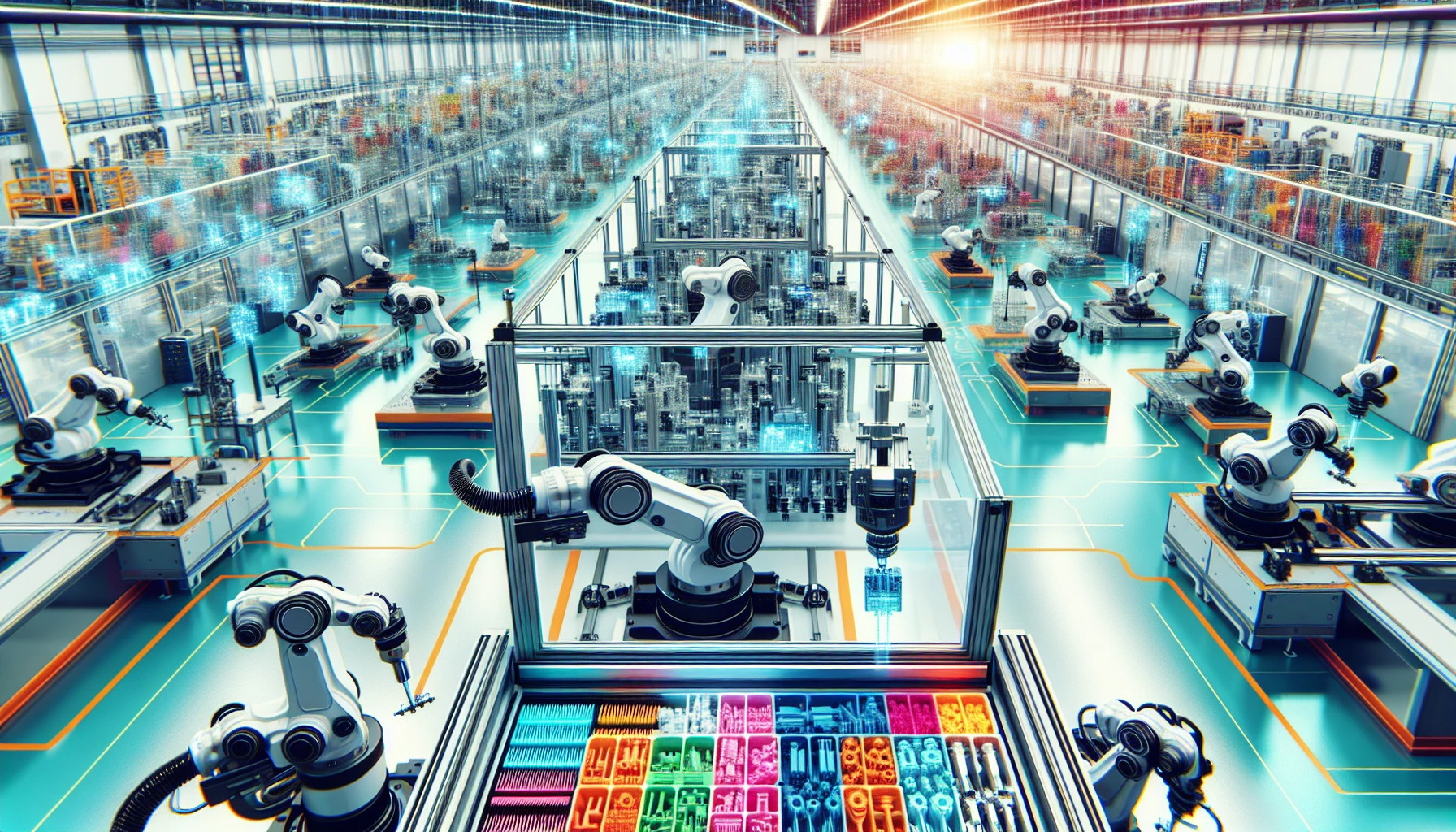
Quality control and inspection in plastics machining play a crucial role in ensuring that the machining process produces goods that meet specifications and standards. In plastics machining, quality control practices typically involve:
- Detecting, recording, and classifying defects such as warping, sink marks, and voids
- Establishing quality standards and implementing total quality management (TQM) practices
- Utilizing computer-aided quality (CAQ) systems and advanced quality planning (AQP)
- Inspecting at various stages of the machining process
The tools typically employed for inspection in plastics machining include:
- Tooth gauge
- Needle gauge
- Vernier caliper
- Micrometer
- Altimeter
Additionally, measuring tape can be utilized for measuring product dimensions during inspection. Maintaining quality control and inspection in plastics machining is crucial to uphold high-quality standards and minimize defects.
Inspection Techniques
Various inspection techniques are employed in plastics machining to ensure high-quality products. These techniques include:
- visually inspecting the products to ensure they meet quality standards
- utilizing testing standards such as ASTM D638 for tensile properties
- inspecting plastic products and raw materials for any potential defects in design or mechanical properties.
Visual inspection in plastics machining is conducted using advanced vision inspection systems, which utilize sophisticated imaging technologies such as machine vision. Cameras and sensors capture images of the plastic parts, which are then processed by algorithms and compared to pre-defined quality criteria to detect any flaws or discrepancies. This inspection is critical in guaranteeing the quality and reliability of the plastic parts produced.
Addressing Common Defects
Common defects encountered in plastics machining include:
- Flow lines
- Sink marks
- Voids
- Delamination
- Weld lines
- Short shots or extrusions
- Air traps
- Brittleness
- Burn marks
- Flash
- Warping
- Jetting
- Vacuum voids
These defects are typically caused by mistakes in the manufacturing process and are closely linked to plastic materials, molding processes, and molds. Addressing these defects is essential for maintaining the quality and precision of the plastic parts produced.
Flow lines, sink marks, voids, delamination, weld lines, short shots, warping, and insufficient pressure in the mold during low-volume production are some of the common causes of defects in plastics machining. Recognizing and resolving these defects is vital for guaranteeing high-quality products and reducing waste and rework.
Selecting the Right Plastics Machining Partner
Selecting an appropriate plastics machining partner is crucial to ensure they can meet your requirements, possess the required equipment and technology, adhere to regulations, and can deliver high-quality products and services promptly. Factors to consider when selecting a plastics machining partner include:
- Their capability and how it aligns with your needs
- The size and variety of their machines
- Their design capabilities
- Their production volume and capacity
- Quality and compliance standards
- Communication and collaboration practices
- Cost and pricing
While assessing a plastics machining company’s capabilities, several factors should be considered including:
- Experience
- Expertise
- Equipment and technology
- Material capabilities
- Quality control measures
- Capacity and turnaround time
- Customer reviews and references
- Compliance and certifications
By taking these factors into account, you can make an informed decision when selecting the right plastics machining partner for your needs.
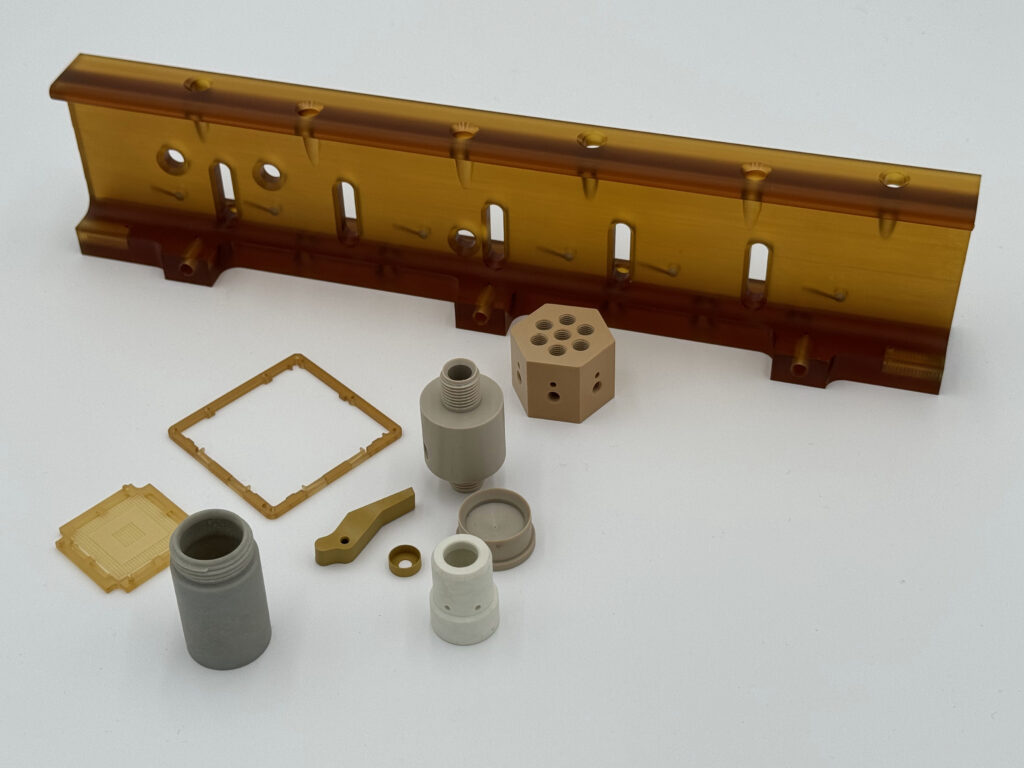
Evaluating Capabilities
Experience is a critical factor in the capabilities of a plastics machining company. With experience, a company develops expertise and knowledge in the exacting processes of plastic machining, enabling them to meet tight tolerances, realize intricate designs, and address issues such as inferior surface finishes and dimensional changes. Additionally, experienced companies typically have a thorough understanding of the various plastic materials and their machining requirements.
Material handling capabilities can have a substantial effect on the output of a plastics machining company. Appropriate material handling and feed systems can significantly enhance the efficacy and output of the machining process, guaranteeing that the necessary materials are supplied to the machine in a timely manner, minimizing downtime and maximizing productivity. Furthermore, optimal materials handling equipment can help reduce defects and enhance overall product quality.
Assessing Compliance and Certifications
Evaluating certifications and compliance standards in plastics machining is vital to ensure that the produced parts are of optimal quality and adhere to all relevant regulations. Essential certifications for a plastics machining company include Scientific Molding Certifications, American Society of Mechanical Engineers (ASME) Certifications, and Automotive Injection Molder Certifications. Compliance standards such as ISO 9001, ISO 13485, ISO 14001, ISO 45001, and AS9100 are also crucial in the plastics machining industry.
ITAR compliance is critical when selecting a plastics machining partner, as it guarantees that the partner is capable of:
- Managing the production, sale, and distribution of defense-related products
- Having a comprehensive knowledge of ITAR regulations
- Guaranteeing the utmost caution, privacy, and security when dealing with delicate projects.
Atlas Fibre is the Ideal Partner
Atlas Fibre stands out as the ideal partner for all your plastics machining needs. We specialize in CNC machining, injection molding alternatives, and precision fabrication in plastics machining. With a wide range of manufacturing options, precision fabrication capabilities, and ISO 9001:2000 certification, Atlas Fibre sets itself apart from other plastics machining companies.
Atlas Fibre employs a variety of innovative technologies and techniques in plastics machining, such as:
- CNC mills
- lathes
- routers
- Swiss machines
These machines offer precise and efficient machining capabilities. Atlas Fibre also provides a high-quality finish to the machined parts through computer numerical control (CNC) sanding materials. With their expertise and advanced technologies, Atlas Fibre is the perfect partner for your plastics machining requirements.
Summary
In conclusion, the world of plastics machining is a complex yet fascinating domain that requires a keen understanding of materials, techniques, and compliance, particularly ITAR regulations. By selecting the right plastics machining partner, such as Atlas Fibre, you can ensure the production of high-quality, precise, and compliant plastic parts for various industries and applications. Equipped with this comprehensive guide, you are now ready to embark on your journey towards successful plastics machining endeavors.
Frequently Asked Questions
What plastics can be machined?
Plastics such as nylon, polycarbonate, ABS, HDPE, UHMW, PEEK and Delrin can be machined to create precision parts and components.
What is the process of plastic machining?
Plastic machining is a subtractive machining process that removes material from plastic raw stock to generate a prespecified shape and size. It involves the use of lathes, mills, cutting machines, drill presses, grinders, and other controlled machines to fabricate parts or products, which require different properties than those for machining metals.
Which types of machining processes are good for plastics?
Milling, drilling, grinding and turning are all effective machining processes for working with plastics. These techniques allow for precision shaping, cutting and forming of the plastic material.
What is an ITAR registration?
ITAR registration is the process through which the U.S. Government monitors companies involved with defense-related products, services, and data. To register, a company should seek help from an ITAR consultant as the process can be complex.
What are the benefits of using CNC machines for plastics machining?
CNC machines offer great precision and accuracy, enabling intricate designs on plastic parts for multiple applications, making it an ideal choice for plastics machining.