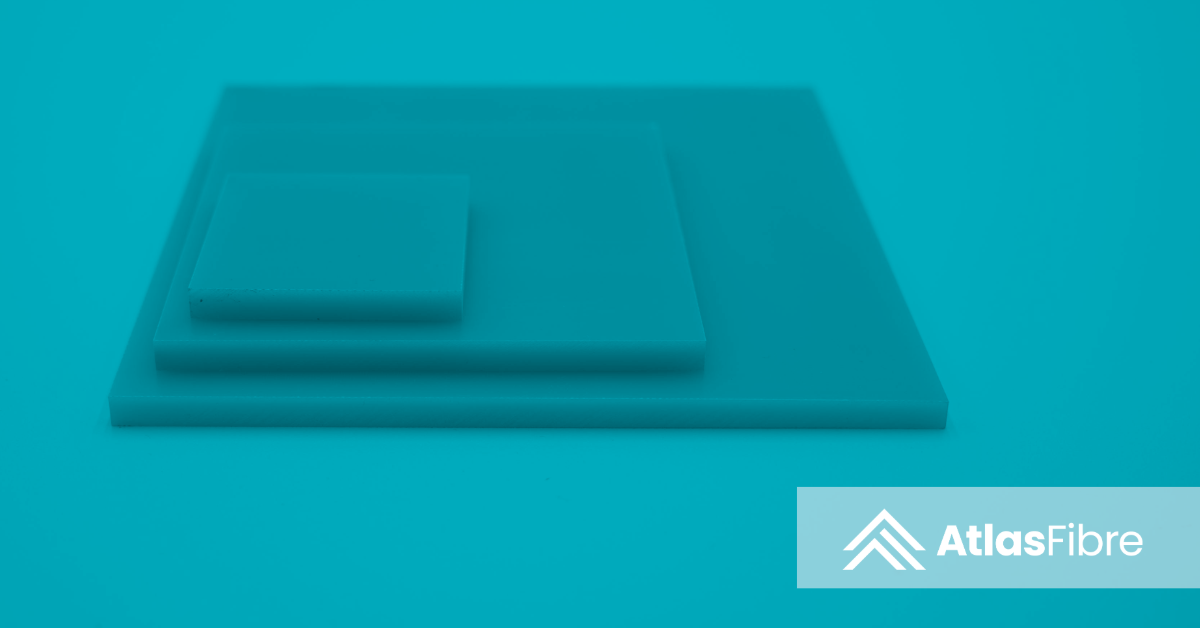
The toughest stuff on the material shelf is only getting tougher.
In the 1930s, a curious class of materials emerged – laminates packed with glass fibers that promised superhuman strength and resilience. But there was one problem: nobody really knew how to machine them.
Fast-forward to today, and glass-filled composites are not just manageable—they’re essential. From aerospace and EV’s to next-gen circuit boards, they’re driving innovation in industries where performance at the extremes is non-negotiable. But machining them? That’s still an art backed by science—and a lot of diamond-coated tooling.
The Problem with Machining Tiny Shards of Glass
Let’s get one thing straight: these glass epoxy materials aren’t like the fiberglass in your fishing boat or insulation. We’re talking about engineered composites, where up to 60% of the material is glass—rigid, abrasive, and brutal on tools. The rest? A resin matrix that binds it all together and defines how it behaves under stress.
Here’s the catch: different resins mean different risks. Epoxies and phenolics are strong and cohesive. Melamines and silicones? Not so much—they tend to delaminate under pressure. And if you don’t account for the grain direction, you might machine a beautifully flawed part that cracks under load.
The glass content, while critical to performance, is also what shreds tooling and fills the air with fine, lung-damaging dust. Tool wear skyrockets. Heat builds. Resin breaks down. In short: machining glass composites is a high-stakes balancing act between physics and patience.
Why We Still Love Them
So why bother? Because glass-filled composites are nearly unmatched in some of the most demanding material categories on Earth.
- Thermal resistance? They hold their shape in a fire.
- Electrical insulation? Excellent, even at high voltages.
- Moisture absorption? Practically zero.
- Strength-to-weight ratio? Off the charts.
In short, they’re materials built for extremes—from satellites and submarines to EV battery casings and industrial transformers. And in a world increasingly obsessed with lighter, stronger, greener solutions, these composites are ticking all the right boxes.
The New Rules of Fabrication
Working with glass-filled laminates means following new machining playbooks. You’re not just cutting material—you’re navigating a minefield of thermal expansion, resin breakdown, and fiber fragmentation.
Here’s what modern machinists know:
Sawing: Use a diamond blade, run it between 3,000–3,600 RPM, and don’t skimp on dust extraction. Water cooling? Even better. Today’s NC saws can power through stacked sheets—but blade quality and motor power are key.
Drilling: Carbide drills only. And don’t get greedy – holes deeper than 1.5x the diameter need pilot holes to stay true. Coolant helps, but a high-quality dust collection system is often just as critical.
Tapping & Threading: Standard taps? Good for prototyping. For production, go carbide, and buy them oversized to reduce binding. Whether you’re cutting internal or external threads, take light passes and know that coolant is a luxury, not a necessity—unless you want to stretch tool life.
Shearing & Slitting: Keep it under 3/32″ thickness if you want clean cuts. Always go with the grain unless you enjoy edge cavitation. Remember, these materials weren’t made for brute-force stamping.
General Machining: Use zero-rake carbide tools, lower surface speeds than you’d use on phenolics, and accept that tool deflection is part of the game. Machining dry is common—but a smart operator always knows when a little coolant can change the outcome.
The Demand Curve is Just Warming Up
Today, industries are scrambling for materials that can survive heat, resist electricity, and hold tight tolerances in the harshest conditions. Glass-filled composites check all those boxes—and they’re increasingly used in battery housings, high-frequency electronics, aerospace structural components, and next-gen energy systems.
The push for lighter, tougher, more reliable components means these laminates are no longer niche—they’re front and center in product innovation. And as new machining technologies emerge, like ultrasonic-assisted cutting or AI-optimized toolpaths, the once-impossible is becoming standard.
Final Word: Fragile Like a Bomb, Not a Flower
Glass-filled composites aren’t delicate—they’re just demanding. If you understand their makeup and approach them with precision, they’ll reward you with performance metal alloys can’t match. But if you ignore their quirks? They’ll chew up your tooling, ruin your tolerances, and send your project off-course.
In the world of modern materials, machining composites is no longer a mystery—it’s a craft. One that’s evolving with every spindle rotation.