Custom machined parts offer unparalleled precision for projects demanding exact specifications. But what does it take to create these bespoke components, and how do you ensure your design is both cost-effective and precise? This article delves into the details of custom CNC machining, covering material selection, design optimization, and real-world applications that benefit from this high-precision manufacturing technique.
Key Takeaways
CNC machining operates as an automated subtractive process that uses pre-programmed computer software to guide machinery in creating tailored parts. The specific material selected, machine’s capabilities, and precise tolerances are crucial to the custom part’s success.
Custom CNC machining is highly versatile, employing different methods like milling and turning to create complex or cylindrical parts. The online CNC services offer rapid quotes, efficient project management, and fast turnaround times, revolutionizing the manufacturing of custom parts.
The application of finishing touches through surface treatments and coatings plays a significant role in the functionality and aesthetic of machined parts. Different industries, particularly aerospace, medical, and automotive, rely on the precision of CNC machining for critical part production.
The Essentials of Custom CNC Machining
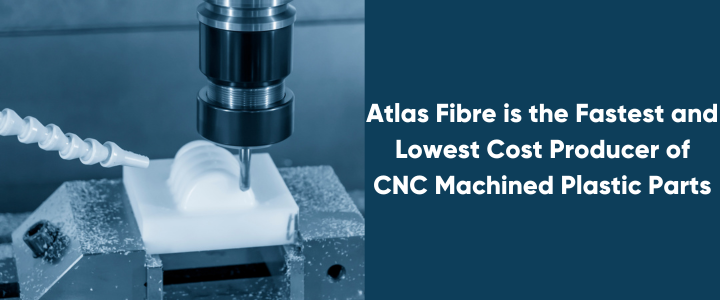
CNC machining fundamentally operates as an automated process, where computer software, pre-programmed with specific instructions, guides factory tools and machinery. This process, known as a subtractive manufacturing process, starts with a larger piece of material and whittles it down to create a custom-designed part. It’s not about mass production, but rather about creating tailored parts that fit precise specifications for unique applications.
CNC machining can handle a broad range of CNC machining materials, including metals and plastics. However, the design’s complexity and efficiency are bound by the machine’s operational capabilities.
Understanding the CNC Machining Process
The commencement of the CNC machining process involves the following steps:
Creation of a digital blueprint using computer-aided design (CAD) software.
Conversion of the 3D model into a set of instructions for the CNC machine.
Translation of the 3D model into a language that the CNC machine can understand, such as G-code or M-code, using computer-aided manufacturing (CAM) software.
As soon as the instructions are programmed, the CNC machine springs into action. The computer inside the machine uses the generated instructions to control the movement of the cutter. As the cutter moves, it removes material from the workpiece, gradually shaping the final custom part. The beauty of this process is that it requires minimal manual intervention.
The machine follows the programmed instructions with a high degree of precision, ensuring the final part matches the original design perfectly.
Selecting the Right Plastic for Your Custom Parts
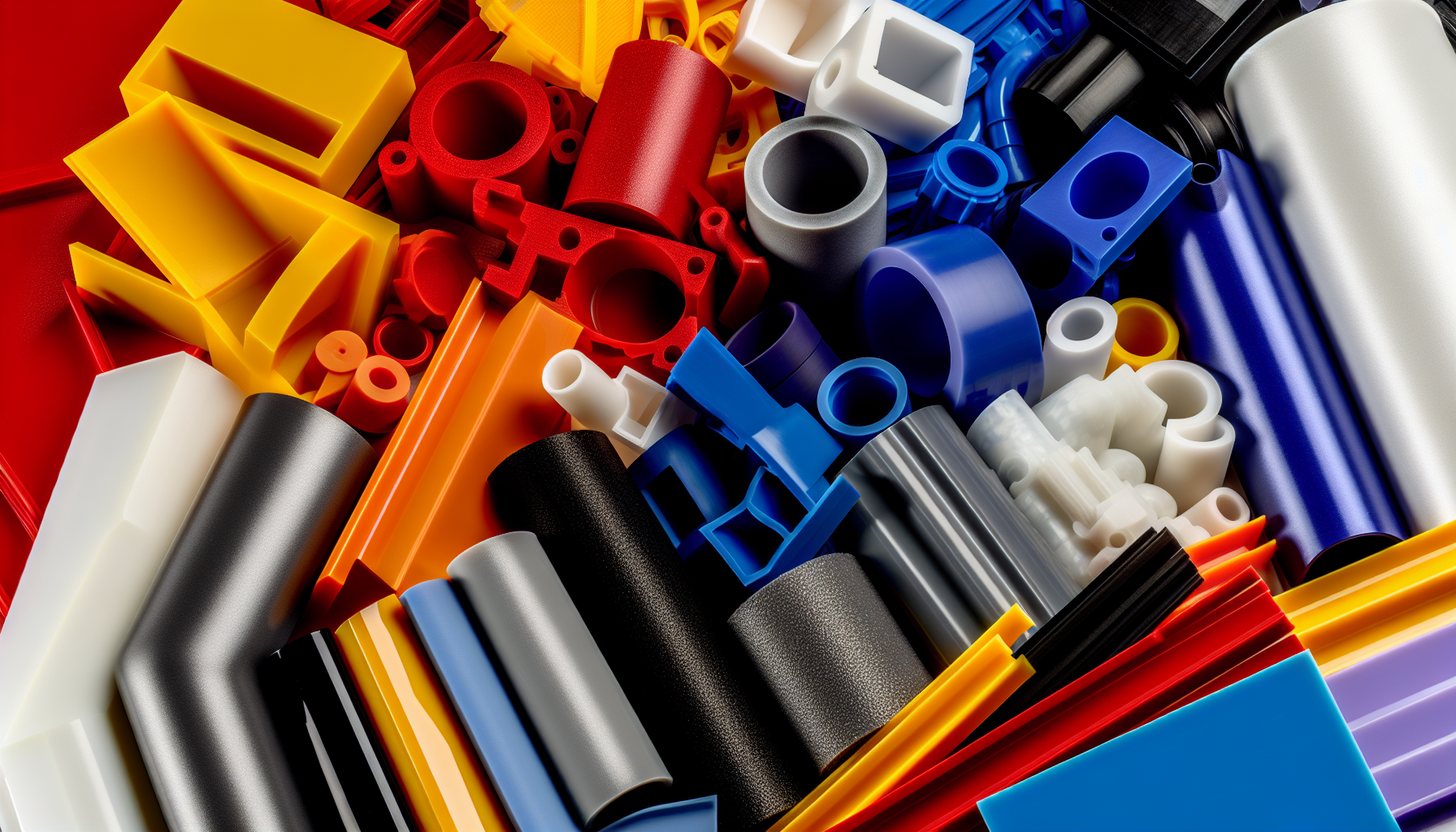
Material selection plays an indispensable role in the CNC machining process. The right material can mean the difference between a part that functions perfectly and one that falls short. When it comes to plastic materials, there are many factors to consider, including the intended application, required durability, and expected appearance.
Material selection guides are a great resource, matching material properties such as hardness, tensile strength, and thermal properties with the specific needs of the designed part. Each plastic material brings unique attributes to the table. For example, Acetal (Delrin) is often chosen for its high stiffness, low friction, and excellent machinability. On the other hand, materials like ULTEM 1000 offer strength, stiffness, and heat resistance, making them suitable for demanding environments. The choice of material can also affect the achievable tolerances for a part, further influencing the selection decision.
The Role of Precision Instruments in CNC Machining
In CNC machining, precision holds utmost importance. The ability to create parts that fit exact specifications is what sets this process apart. This precision is measured in terms of tolerance, which is a permissible limit of variation in a physical dimension. In other words, tolerance is the allowance for slight deviation from the specified dimension, which ensures that the parts fit together properly and function as intended.
To ensure that the machined parts meet these precise tolerances, precision instruments such as calipers, micrometers, and Coordinate Measuring Machines (CMMs) are used. These instruments measure the parts and ensure they conform to the specified tolerances. Regular calibration of these tools, along with careful management of tool and spindle wear, helps maintain ongoing precision and accuracy in CNC machining.
Adherence to precision and quality standards, such as those upheld by Atlas Fibre’s ISO 9001:2015 certification, directly influences the efficiency and durability of CNC machined parts under operational stresses.
Tailored CNC Milling and Turning Services
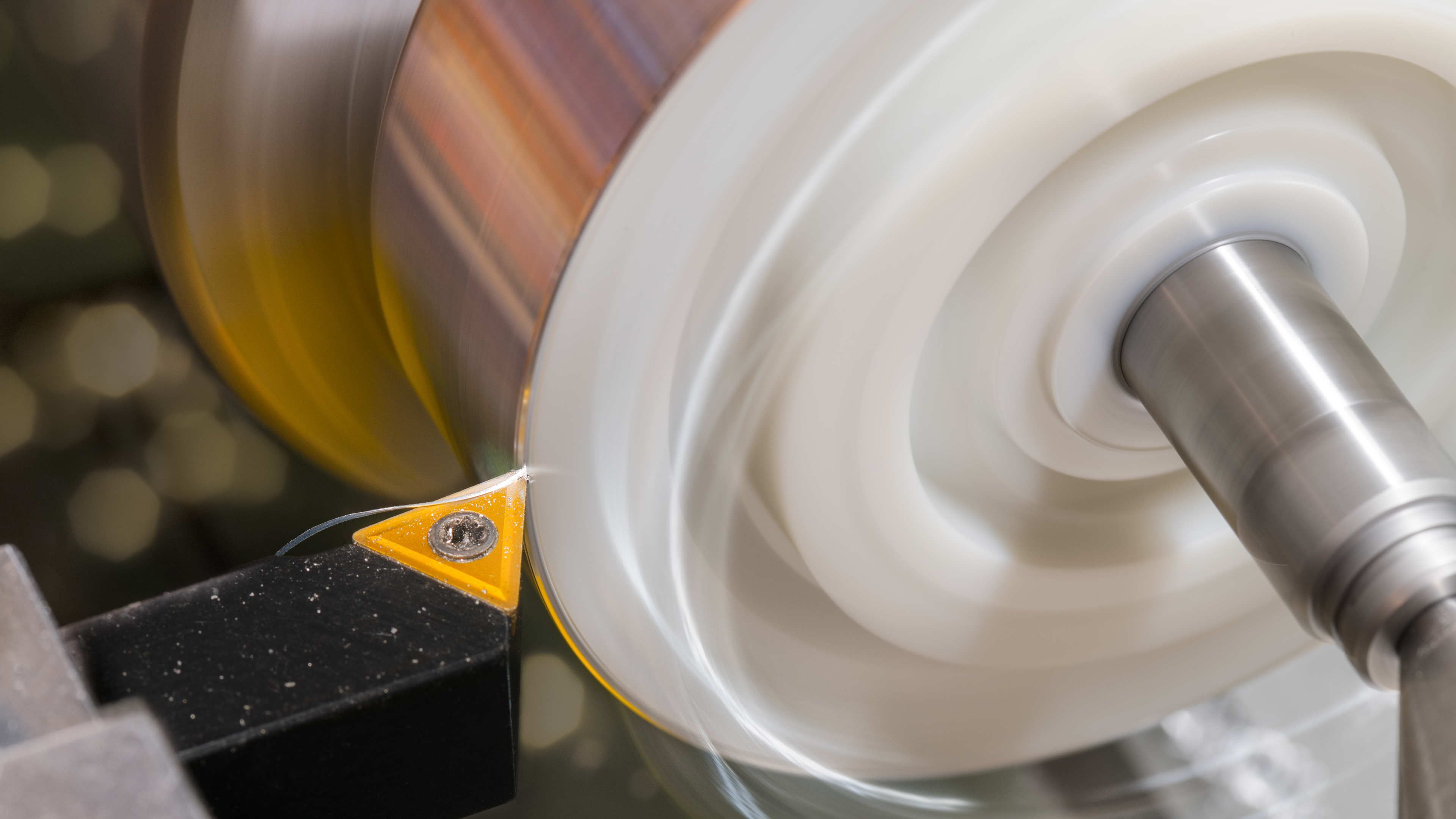
CNC machining doesn’t follow a uniform solution approach. The process can be tailored to fit a range of part complexities and shapes. Two of the most common methods used in custom CNC machining are milling and turning, which are examples of CNC machining processes. Each of these methods has its own strengths and areas of application.
CNC milling machines are capable of performing multi-axis operations. These can include 3-axis, 4-axis, and 5-axis machining processes, for example. These capabilities offer precision and efficiency in creating complex designs. On the other hand, the turning process is particularly beneficial for parts with a long length to diameter ratio, such as pistons and shafts.
CNC Milling for Complex Geometries
CNC milling machines are a marvel of modern engineering. Equipped with the ability to move on five different axes, these machines can create complex designs without the need for reorientation of the workpiece. This makes 5-axis CNC milling machines especially proficient at producing intricate machine parts with high precision.
The complexity of the part often determines the selection of CNC machinery. Simpler designs can be effectively handled by three-axis mills, while more intricate geometries may require the enhanced capabilities of five-axis machining centers. The choice between these machines can greatly impact the design and finishing potential of a part.
For example, the aerospace industry often leverages 5-axis milling for reduced error, and the medical field frequently requires machined components that are critical for surgery and patient safety.
CNC Turning for Cylindrical Components
While milling is ideal for complex designs, turning is the go-to process for creating cylindrical parts. CNC turning uses lathes and turning centers to shape plastic stock. Its main application is in creating cylindrical parts. The process is highly efficient, ensuring consistent dimensions and smooth finishes.
The turning process is particularly beneficial for parts with a long length to diameter ratio, like pistons and shafts. It can efficiently produce features like:
grooves
threads
chamfers
tapers
using standard tooling, proving its superiority for specific part shapes over other machining processes. The selection of the appropriate raw material shape is also crucial in CNC turning. Typically, round stock is used for creating turned components.
Moreover, live-tool CNC turning capabilities enable the creation of diverse features like off-center holes and slots, offering complex geometries and additional functions beyond standard turning processes.
Advantages of Online CNC Machining Services
In the ongoing digital era, the sphere of CNC machining has also adapted to online platforms. Online CNC machining services offer a bevy of benefits, including:
Fast quotes: Customers can obtain CNC quotes quickly, often within 24 hours, by simply uploading their design files.
Efficient project management: Online platforms offer comprehensive project management features, including order tracking and instant access to design feedback, pricing, lead time, and DFM details.
Rapid turnaround times: With online CNC machining services, customers can expect quick turnaround times for their projects.
These benefits showcase the CNC machining advantages, making online CNC machining services a convenient and efficient option for customers.
The strategic advantages of using online CNC services include:
Convenience
Performance-driven partner success scores
Dozens of redundant CNC machining centers, ensuring consistent quality
Flexibility of on-demand production, especially beneficial for short-run or prototype projects
Features for efficient coordination such as team creation and shared access to quotes and orders
Online CNC machining services, including our top-notch online CNC machining service, are revolutionizing the way we manufacture custom parts at CNC machining shops, while keeping CNC machining service cost in mind.
Optimizing Design for CNC Machined Parts
Despite the vast possibilities offered by CNC machining, optimizing your design is crucial to fully harness this potent process. Factors to consider include:
Machining time
Start-up costs
Material costs
Special requirements like tight tolerances or thin walls
Several factors can significantly impact the CNC machining cost.
Therefore, understanding these factors and optimizing your design accordingly can help reduce costs and enhance manufacturing efficiency.
Design Tips to Minimize CNC Machining Costs
When it comes to minimizing CNC machining costs, design plays a significant role. Here are some tips to keep in mind:
Keep the design simple. Complexity often requires special tooling, multiple machine setups, or special materials, which can increase costs.
Design cost-effective parts with fewer components that still maximize performance.
Minimize overhead costs by enhancing manufacturing efficiency.
By following these tips, you can reduce CNC machining costs and improve the overall efficiency of the manufacturing process.
Another way to minimize cost is by using standard tooling and designing parts to match standard milling cutter radii and hole sizes. This can lead to reduced programming and machining times, thus lowering costs. Similarly, optimizing wall thickness, internal corner radii, and feature aspect ratios within the design can simplify machining and reduce costs.
Furthermore, designing parts to fit within common stock material sizes can minimize wasted material, reducing machining time and cost. Lastly, reducing the number of fixturing setups by designing parts that can be machined in fewer orientations can significantly decrease CNC machining production time and cost.
Preparing CAD Files for Optimal Machining
Preparing a CAD file for optimal machining involves more than just creating a 3D model of your part. It requires careful consideration of the machining process and the capabilities of the CNC machine.
To prepare your CAD files for machining, follow these steps:
Create a 3D model of your part using CAD software.
Save the file in a neutral format like STEP (AP214 or AP242 recommended).
Create a technical drawing that details all specifications, dimensions, and special requirements.
By following these steps, you can ensure that your CAD files are ready for optimal machining.
Online platforms can streamline the design process by offering immediate feedback on manufacturability and design cost implications. Choosing suitable 3D modeling software can help avoid the need for file conversions, which may reduce costs and expedite the CNC design process. Also, understanding tool reach and avoiding the design of deep, narrow features are essential to prevent machining complications. Implementing Geometric Dimensioning and Tolerancing (GD&T) is critical for minimizing ambiguities and ensuring high-quality production while optimizing manufacturing costs.
Finishing Touches: Surface Treatments and Coatings
Following the machining of a part, it’s appropriate to apply the finishing touches. Surface treatments and coatings can provide both aesthetic and functional finishes to CNC machined parts. For instance, powder coating provides a strong, wear and corrosion-resistant polymer layer, available in multiple colors. On the other hand, black oxide coating offers reduced light reflection and improved friction and corrosion properties for ferrous materials. However, it’s important to note that specifying simpler finishes like a standard roughness or a single finish when possible can avoid the costs associated with more complex surface finishing processes.
Achieving Aesthetic and Functional Finishes
CNC machined parts can receive a variety of surface treatments to enhance their functionality. For instance, brushing is a preliminary surface treatment that removes contaminants and preps CNC machined parts for further operations or final use. Painting with lacquer or polyurethane provides a protective layer over machined parts, safeguarding them from water, contaminants, and adverse atmospheric conditions, while also improving their aesthetic appeal.
For critical applications such as aerospace components and robotic parts, specialized finishes like polishing, and powder coating are applied to improve durability, functionality, and surface texture. These finishes not only enhance the part’s performance but also give it a professional, high-quality appearance. Therefore, the right surface treatment can make a significant difference in the overall success of a CNC machined part.
Automotive Innovations with Custom Machined Components
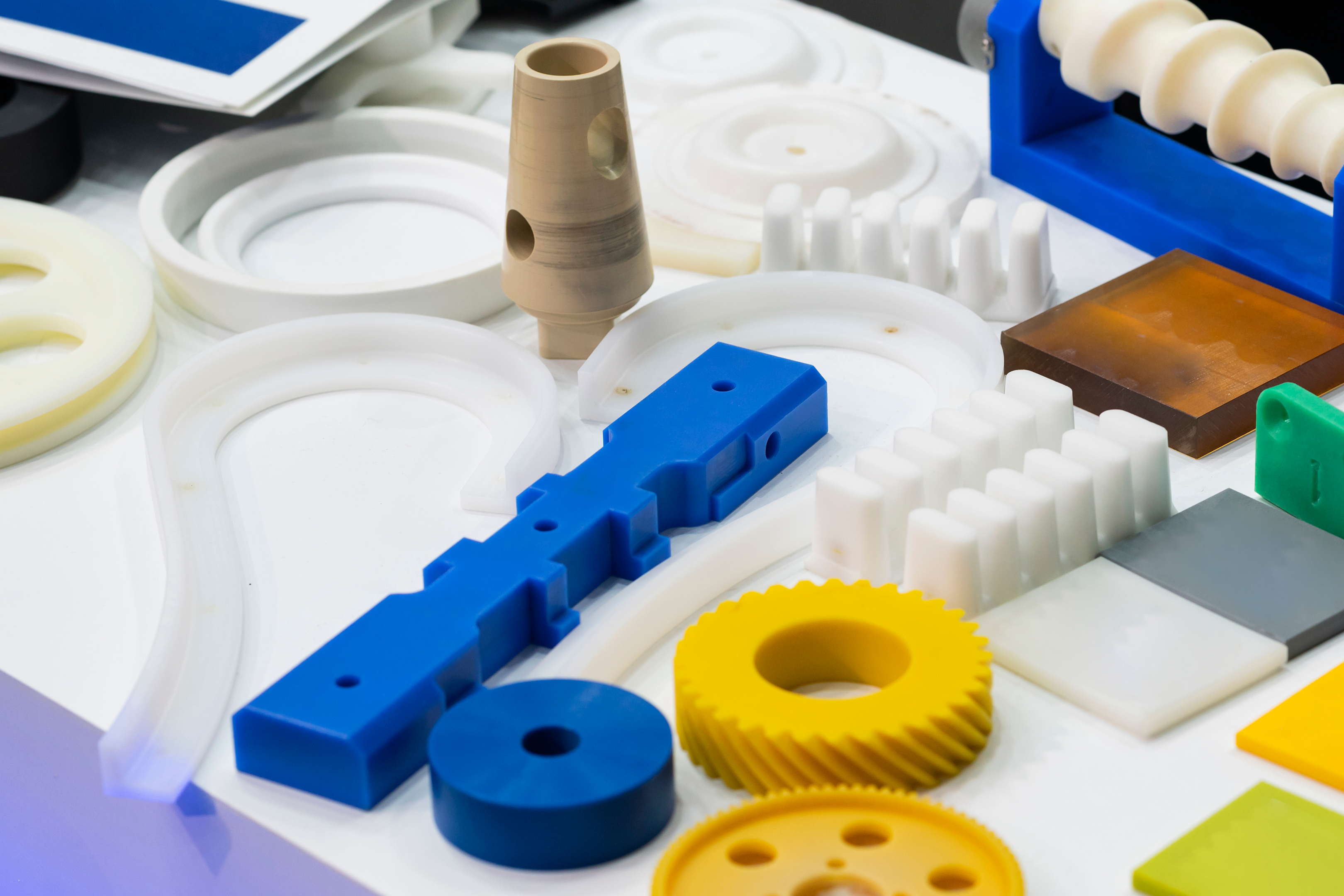
Automotive innovations heavily rely on the crucial role played by custom CNC machining. The industry demands precision, reliability, and durability, all of which are delivered by custom CNC machined components. Some examples of these components include:
ABS bumpers
PC/ABS dashboards
Reflectors
Lenses
Steering wheel components
Vital engine and transmission parts
Each component plays a critical role in the functionality and safety of a vehicle.
The ability to create custom parts with precise specifications opens up a world of possibilities for automotive innovation. With CNC machining, manufacturers can produce parts that are lighter, more durable, and more efficient than ever before. This not only improves the performance of the vehicles but also contributes to advancements in fuel efficiency and safety.
Medical Breakthroughs Enabled by Precision Machining
Another sector where CNC machining exerts a substantial influence is the medical field. With its ability to produce precision parts to exact specifications, CNC machining enables medical breakthroughs. Some examples of medical applications of CNC machining include:
Stainless steel or titanium bone plates
Prostheses
Respiratory devices
Handheld diagnostic equipment
Anatomical models
Surgical instruments
CNC machining is at the heart of modern medical technology.
Certain materials are particularly suited to medical applications. For instance, PEEK is highly valued in the medical machining sector for its superior strength-to-weight ratio and corrosion resistance. These qualities make it ideal for use in implants and surgical instruments. Thus, the precision and versatility offered by CNC machining continue to drive innovation in the medical field.
Navigating CNC Machining Tolerances
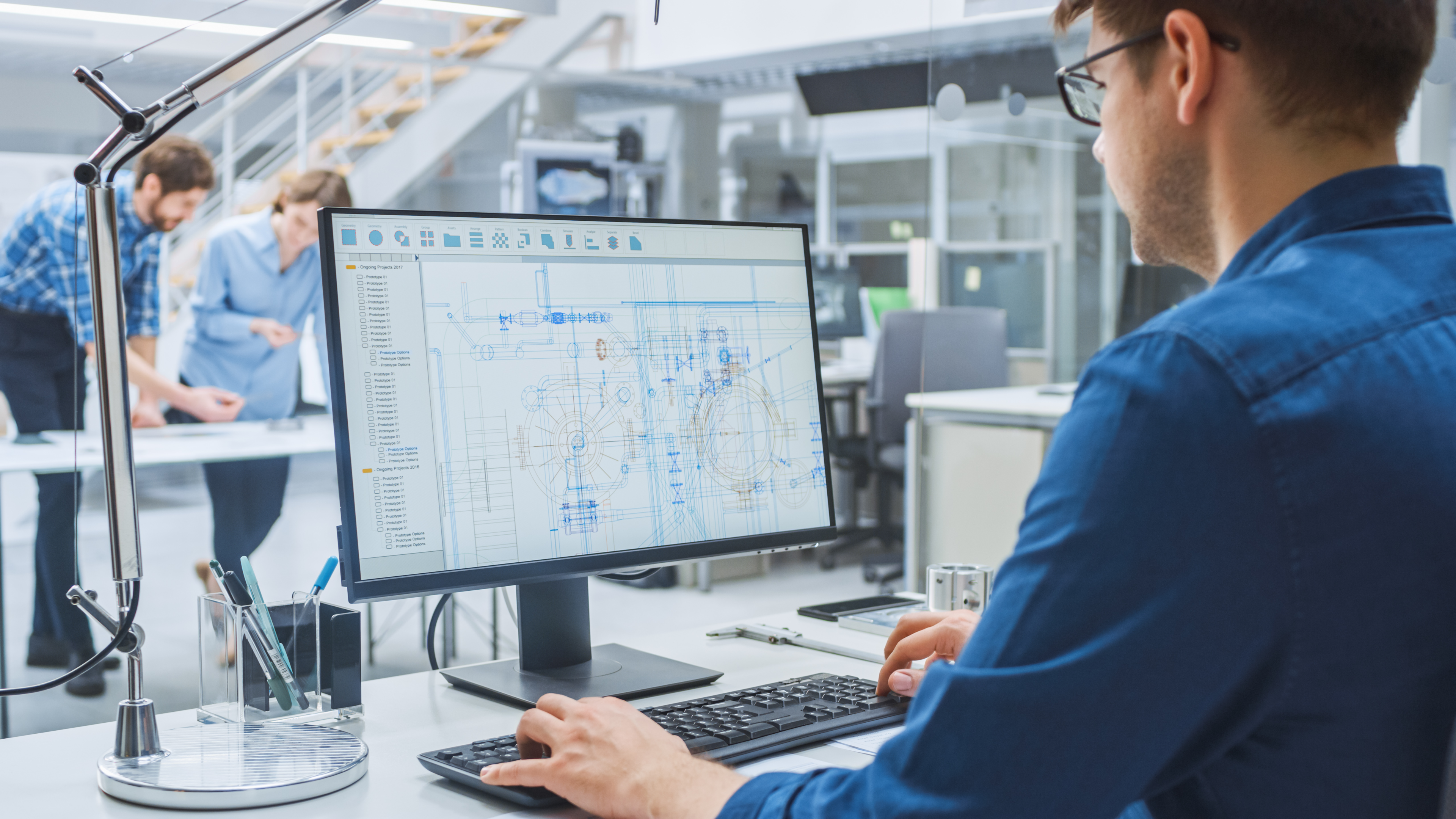
In CNC machining, tolerance is a concept of pivotal importance. It refers to the allowable variation in a physical dimension, which ensures that the parts will fit together properly and function as intended. CNC machines can achieve tolerances as tight as +/- 0.0002 inches.
Understanding these tolerances and how to navigate them is an essential part of the CNC machining process.
Importance of Tight Tolerances in Critical Applications
In certain applications, tight tolerances are absolutely essential. For instance, in the aerospace industry, there is zero margin for error. Every part must meet strict size and tolerance standards to ensure the safety and reliability of the aircraft. Similarly, in the medical field, precision is paramount. Whether it’s a surgical instrument or an implant, the parts must meet exact specifications to ensure patient safety and the effectiveness of the treatment.
However, while tight tolerances are necessary for certain applications, they can also increase costs. This is because they require more machining time and additional quality control measures. Therefore, it’s important to balance the need for tight tolerances with the cost implications. This can be achieved by applying tolerances selectively to only those features requiring high precision and by using surface finishes to improve the visual appearance of CNC machined parts, which may affect the dimensional tolerances.
Balancing Tolerances and Machining Costs
Balancing tolerances and machining costs is a delicate act. While tighter tolerances can increase precision, they also raise costs and lead times due to the need for additional processes, operations, and specialized tools and machines. By applying tolerances selectively to only those features requiring high precision, it is possible to avoid unnecessary costs linked to over-tolerancing that results in increased machining and inspection time.
In addition, a strategic approach to achieving a cost-effective balance between manufacturing costs and tight tolerances includes:
Adopting lean process optimizations
Choosing the right materials
Leveraging technology for enhanced control
Fostering good supplier relationships for competitive pricing
This ensures that the final product meets the required specifications without inflating the cost unnecessarily.
Industrial Applications of Custom CNC Machining
The adaptability and precision carried by custom CNC machining render it a beneficial asset across diverse industries. Some of the industries that benefit from CNC machining include:
Aerospace
Automotive
Telecommunications
Robotics
CNC machining is instrumental in creating precisely machined parts that meet strict tolerances and design specifications. Moreover, the rapid prototyping capabilities of CNC machining enable industries to refine design concepts swiftly, cutting down development time and costs while accelerating market readiness.
Even in the energy sector, custom CNC machining is used for manufacturing critical components such as:
heat exchangers
valves
pipes
hydraulic parts
battery components
parts for solar panels and frames.
Aerospace: Meeting High-Stress Demands with Custom Parts
Custom CNC machining distinctly showcases its benefits within the aerospace industry. With no room for error, every part used in aerospace applications must meet strict size and tolerance standards. Composites are often favored in aerospace applications for their excellent resistance to corrosion, chemicals, and extreme temperatures, along with a strong strength-to-weight ratio. These materials are ideal for producing critical aerospace components such as turbine blades, engine parts, and fasteners.
Custom machined parts are integral to a range of aerospace components, including:
engines
fuselages
turbines
brakes
tire parts
lighting systems
vacuum pumps
fuel pump parts
With the precision and reliability offered by CNC machining, the aerospace industry can create advanced aircraft that are not only safe and efficient but also push the boundaries of what’s possible in flight.
Robotics and Automation: Crafting the Future with CNC Machining
Within the field of robotics and automation, precision is of paramount importance. Custom CNC machining plays a crucial role in creating specialized components such as:
Robotic end effectors
Custom jigs
Manipulator parts
Actuators
Motors
Control equipment
Clamps
Housings
Each of these components is tailored to meet the unique requirements of varying applications. The precision and versatility offered by CNC machining allow manufacturers to create robots and automated systems that are more advanced and capable than ever before.
The robotics industry also benefits from the rapid production lead times offered by CNC machining. This provides the ability to quickly iterate and refine robotic components, thus accelerating the development process. Moreover, the integration of robotic arms into the CNC machining process enhances productivity and accuracy by assisting in tasks such as material loading and unloading, process control, and automated quality inspections.
Atlas Fibre: A Leader in High-Performance Engineering Plastics
Atlas Fibre leads the domain of high-performance engineering plastics. With the largest inventory of thermoset composites in North America and processing over 7,000,000 pounds of material per year, Atlas Fibre has earned recognition as the best plastics-only machine shop in the United States.
The company specializes in high-performance engineering plastics such as:
G10
FR4
PEEK
PEI
PPS
Vespel
reflecting their expertise in the precision custom machining sector. Atlas Fibre’s capabilities extend beyond machining; they are also adept in the custom formulation and fabrication of thermoset materials.
With manufacturing facilities in the United States and strategic partnerships with Accurate Plastics in Massachusetts and Lamtuf in India, Atlas Fibre has established a global manufacturing reach, demonstrating its commitment to delivering the highest quality products and services to its customers.
Summary
In conclusion, CNC machining is a powerful tool that brings designs to life with precision and efficiency. Its applications span numerous industries, from aerospace and automotive to robotics and healthcare. Whether it’s creating a part with complex geometries or manufacturing a simple component to precise tolerances, CNC machining delivers reliable and high-quality results. As technology continues to advance, the possibilities and capabilities of CNC machining will only continue to expand, paving the way for more innovative solutions and breakthroughs.
Frequently Asked Questions
What is a custom machine shop?
A custom machine shop is a facility that utilizes advanced technology and equipment, such as CNC machine tools, to provide tailored manufacturing solutions for its clients.
How much is custom CNC milling?
Custom CNC milling costs can range from $75 to $200 per hour, depending on factors such as part complexity, material type, machining time, and precision requirements.
What is CNC machining?
CNC machining is the automated control of machining tools through pre-programmed computer software, allowing for precise custom designs by removing material from a blank workpiece.
How does the CNC machining process work?
The CNC machining process works by creating a CAD model, which is then translated into a CNC program using CAM software. The computer within the CNC machine then uses numerical coordinates to control the cutter’s movement and shape the final custom part.
Why is selecting the right plastic material for CNC machining important?
Selecting the right plastic material for CNC machining is crucial because it affects the manufacturing process, cost, and performance of the final product. It’s essential to consider the intended application, required durability, and expected appearance.