Navigating the selection and machining of plastic parts? Central to countless high-precision applications, machined plastic blends technical performance with design freedom. This guide unpacks material choice, CNC machining precision, and the versatile applications of machined parts, setting you up to leverage their full potential in your industry.
Key Takeaways
CNC plastic machining is a vital subtractive process that transforms plastic materials into precise parts, necessary for a wide range of industries due to their durability, lightweight, and cost-effectiveness.
Selecting the right plastic material is critical for machining operations, with common choices including PEEK, ABS, and PTFE, each offering unique properties such as high impact strength or chemical resistance which affect the machinability and application suitability.
Quality control measures, specialized CNC plastic machining techniques, and expert knowledge of material properties and handling are imperative for the production of high-quality, precision machined plastic parts.
Exploring the World of Machined Plastic
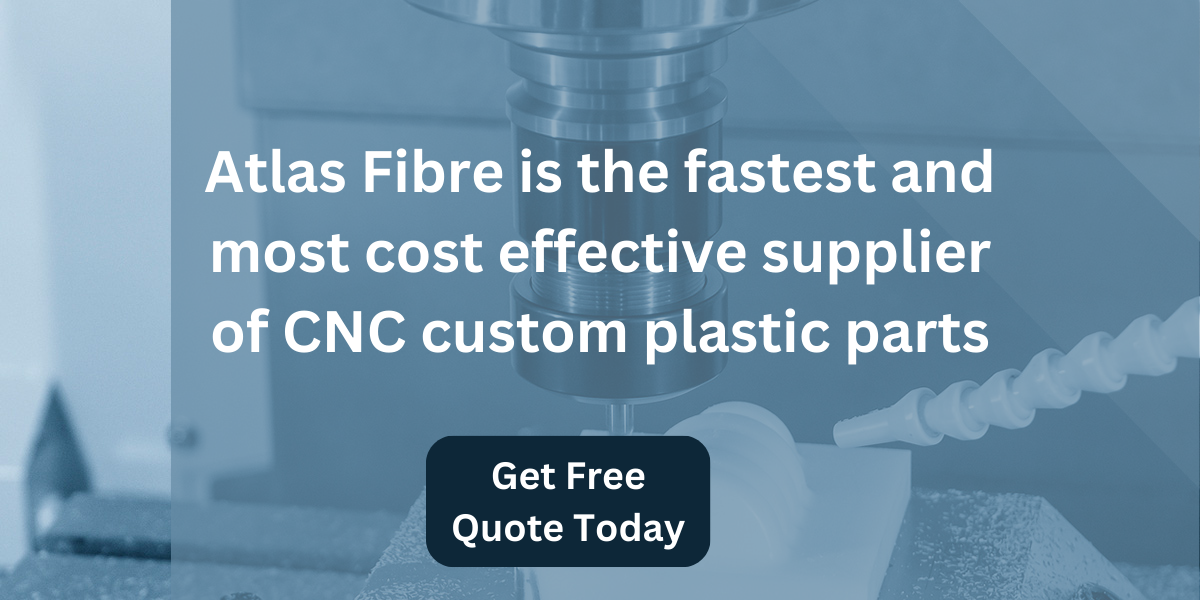
Plastic machining refers to shaping plastic materials into final products by removing excess material. This is achieved through a manufacturing process known as CNC plastic machining. This subtractive process transforms plastic materials into intricate and precision parts that fulfill a multitude of modern industries’ needs, underlining its significance in the manufacturing sector.
From the automotive industry to medical technology, machined plastic parts are everywhere, thanks to their durability, light weight, and cost-effectiveness. Moreover, the flexibility of plastics allows manufacturers to create parts in a wide array of shapes and sizes to meet the diverse requirements of various industries.
Precision CNC Machining and Plastics
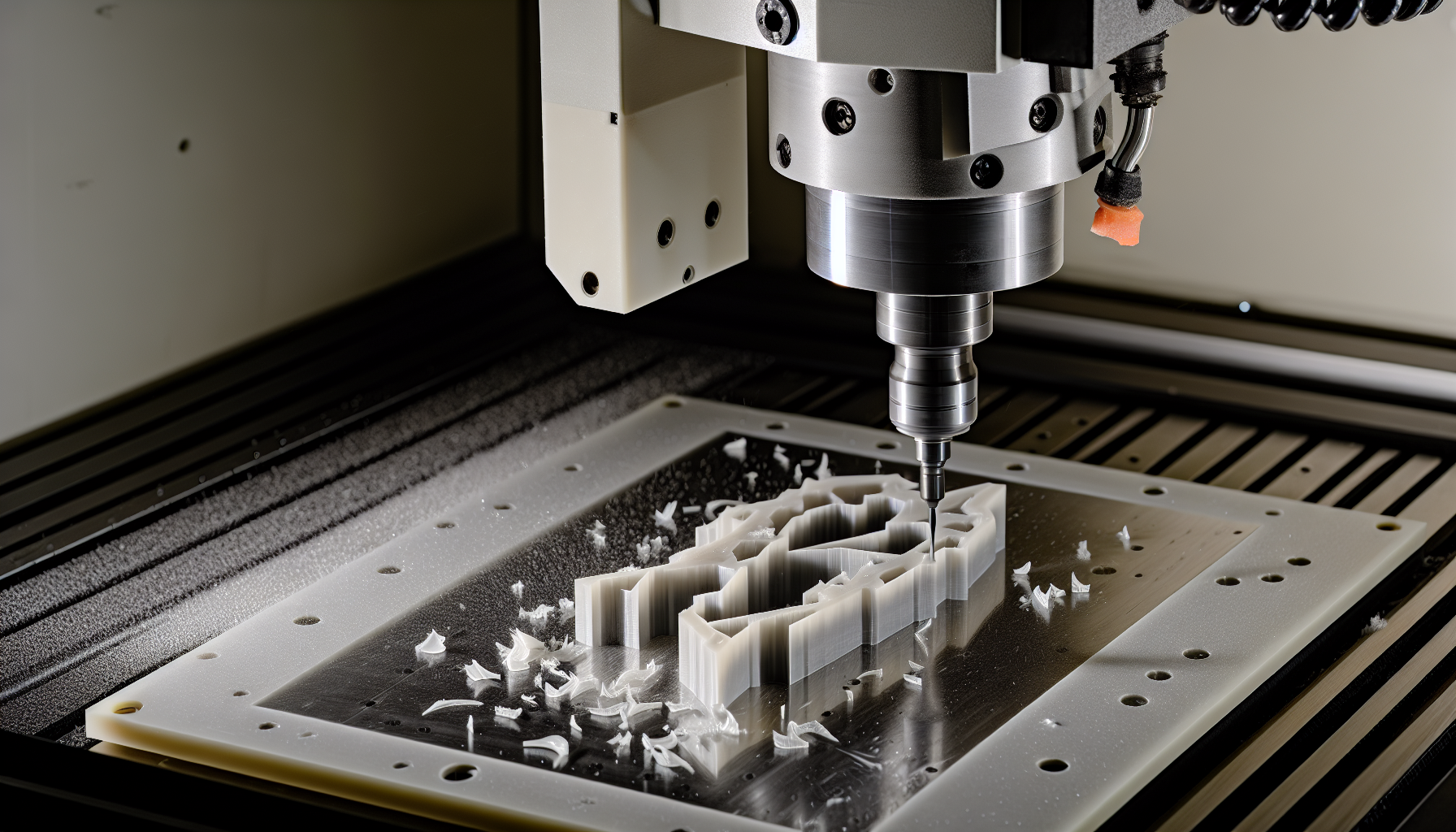
Computer Numerical Control (CNC) machining is an automated method preferred for high-volume production of complex plastic parts. It offers high-precision tolerances down to 0.0001 inches, enabling the creation of small and large intricate parts out of various plastics.
High-performance CNC systems equipped with advanced features ensure efficient machining, good heat removal, and adherence to tight tolerances, responding to various industries’ needs for highly precise components.
The Role of CNC Machines in Plastic Work
Temperature control plays a fundamental role in plastic CNC machining. As the process generates heat, it can alter the dimensional accuracy of the machined parts. Hence, frequent cooling and adjustments for thermal expansion are necessary to manage the temperatures during machining.
This helps maintain tight tolerances and ensure the quality of the final product.
Achieving Tight Tolerances with CNC Plastic Machining
The process of achieving tight tolerances on plastic parts is intricate, requiring the use of a high-quality CNC machine capable of effectively controlling design parameters. And the less complex the design, the more conducive it is to precision. Moreover, the size of the plastic part impacts the achievable tolerances.
Some key considerations for achieving tight tolerances on plastic parts include:
Using a high-quality CNC machine
Controlling design parameters effectively
Simplifying the design
Minimizing thermal damage, especially for smaller parts
By following these considerations, you can increase the likelihood of achieving tight tolerances on your plastic parts.
In certain applications, machined components require tolerances of a few 1/100 mm and surface quality down to Ra 0.05µm. This demonstrates the level of precision that CNC machining can deliver, which is critical for industries such as aerospace, medical technology, and electronics that demand extreme precision.
Selecting Suitable Plastic Materials for Machining
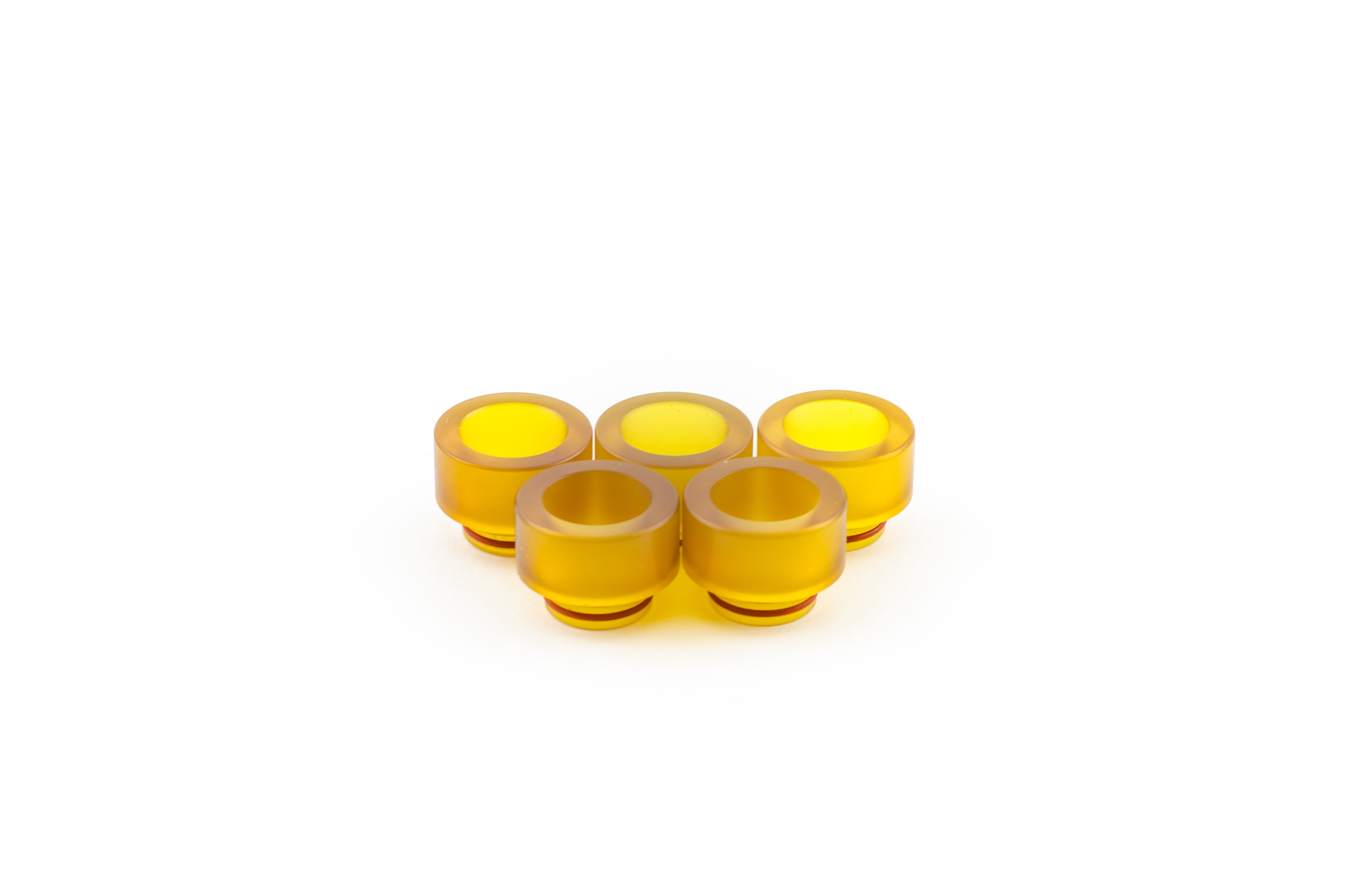
The process of selecting the appropriate plastic for machining constitutes a significant step in manufacturing. It involves carefully considering the properties of various materials and how these properties affect the machinability, strength, and application suitability of the final product. Common materials used in CNC machining include:
Polyetheretherketone (PEEK)
Acrylonitrile Butadiene Styrene (ABS)
Polyamide (PA)
Polyacetal Polyoxymethylene (POM)
Glass Epoxy Composites (G10/FR4)
Phenolic Composites (CE)
Polytetrafluoroethylene (PTFE)
Each material offers unique properties.
Thermoplastics with High Impact Strength
The suitability of a thermoplastic material for developing durable plastic components, which are enduring and machined, is largely determined by its impact strength. Plastics like:
ABS
Polycarbonate
High-Density Polyethylene (HDPE)
High Impact Polystyrene
demonstrate high impact resistance and are suitable for demanding applications. These materials offer excellent impact resistance, making them versatile for various uses.
Aside from their impact strength, these thermoplastics are known for their ease of machining, resistance to chemicals, and suitability for various finishing techniques. Therefore, selecting a thermoplastic with the appropriate impact strength is imperative to ensure the long-term durability and performance of the machined part in its final application.
Balancing Chemical Resistance and Machinability
Finding a plastic material that offers both chemical resistance and machinability can pose a challenge. Materials like:
Vespel
Torlon
PEEK
Ultem
Teflon (PTFE)
are preferred for their balance of high heat resistance, chemical resistance, and dimensional stability in CNC machining applications. However, some plastics like Nylon, while robust and versatile, can absorb moisture and warp, potentially affecting tight tolerance requirements in machined parts.
To prevent warping and maintain precision, materials with high moisture absorption like Nylon and Torlon should be conditioned or dry machined to achieve equilibrium moisture content before processing. Consideration of environmental aspects such as sunlight, high temperatures, and humidity is critical to ensure the integrity of plastic materials throughout their use in industrial applications.
The Intersection of Durability and Machinability in Plastics
The choice of plastic material has a direct impact on the durability of the final part as well as its machinability during production. Machined plastics like Delrin with glass fibers offer superior stiffness, dimensional stability, and high creep resistance. This makes them a valuable choice in applications where these properties are crucial. This contributes to their durability when machined into parts that face high-stress situations.
However, it’s not just about selecting the right plastic material. The actual machining process can also significantly influence the part’s durability. Proper management of stresses in plastic materials during CNC machining is necessary to avoid critical flaws in the final product, ensuring dimensionally accurate parts. This is where experts, including sales and technical teams, come into play. They can help navigate material selection challenges in plastic machining, ensuring an optimal balance between durability and machinability is achieved.
Intricacies of the Plastic Machining Process

The process of machining plastic materials is intricate and requires special considerations. From managing stresses to ensuring safety and optimizing the process, there are many factors to take into account. Some key considerations include:
Managing stresses in the material to prevent warping or cracking
Using the appropriate cutting tools and techniques for the specific type of plastic
Ensuring proper cooling and lubrication during the machining process
Using personal protective equipment and proper ventilation to minimize exposure to harmful byproducts released when plastics are heated
By taking these factors into account, you can ensure a successful and safe machining process for plastic materials.
Additionally, the adjustment of feeds and speeds through trial and error is crucial in optimizing the machining process for plastics to prevent poor chip formation.
Tool Materials and Cutting Techniques
Choosing the correct tool material and cutting technique can have a significant effect on the efficiency and quality of the machining process. For instance, unreinforced thermoplastics can be machined with high-speed steel (HSS) tools, while glass-reinforced materials require solid carbide tools for efficient machining. Tools like carbide and diamond-tipped tools are preferred for their hardness and heat resistance, aiding in maintaining sharpness and precision during plastic machining. Carbide tooling is especially beneficial in these situations due to its durability and performance.
Moreover, proper tool sharpening is essential for the quality of the machined parts and the efficiency of the machining process. Using sharp tools is critical for achieving a smooth finish on machined parts. Cutting techniques such as high-feed milling and trochoidal milling are instrumental for rapid material removal rates, minimizing heat generation and tool wear during CNC machining of plastics.
Managing Heat Reduction and Surface Finish
Managing heat and achieving smooth surface finishes are other essential aspects of plastic machining. Techniques like High Efficiency Milling (HEM) effectively distribute heat along the cutting edge, thus managing heat. Moreover, maintaining a constant radial depth of cut, leveraging climb milling, and using appropriate coolant can significantly mitigate overheating and prolong tool life.
A smooth surface finish not only enhances the appearance of plastic parts but also improves functionality by:
reducing friction
preventing contamination
preventing dirt accumulation
preventing premature wear
Therefore, achieving a smooth surface finish is a critical consideration in the machining process. In fact, faster machining processes can facilitate a smoother finish, yielding a higher-quality part outcome.
Customized Solutions with Machined Plastic Parts
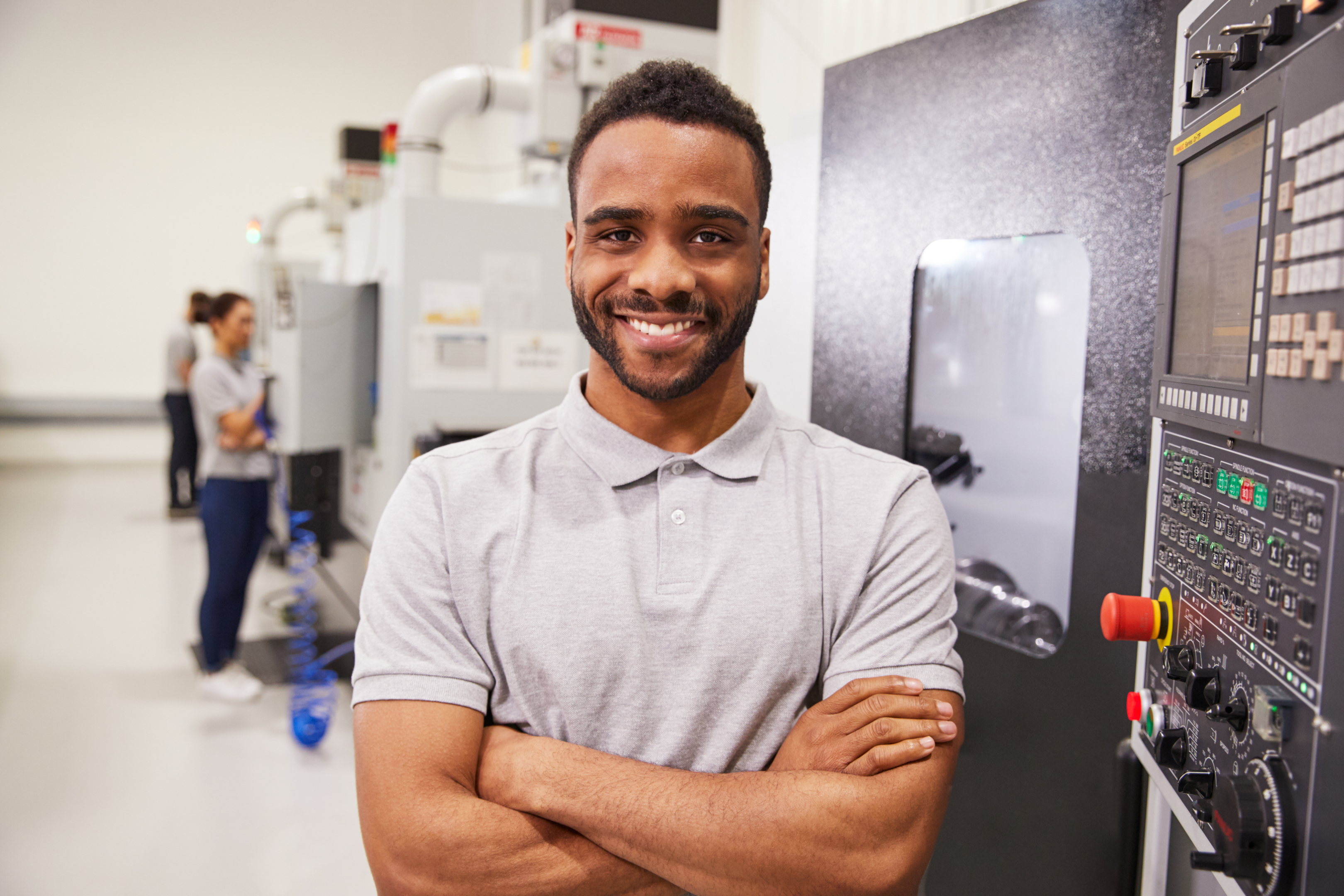
Modern, high-performance CNC machining centers offer virtually unlimited processing possibilities for creating customized machined plastic parts. These parts find wide-ranging applications in industries such as:
Industrial and heavy equipment
Medical
Electronics
Aerospace
Materials like Polyvinyl Chloride (PVC) and High-Density Polyethylene (HDPE) offer great design flexibility with various colors, grades, and textures, catering to bespoke customer requests.
In addition to the diverse range of applications, machined plastics also allow for the creation of precision components in life-critical applications. Examples include a fully machined and assembled breast biopsy unit or a complex cranial surgery headrest assembly. Moreover, stress-relieved raw materials and post-machining services like annealing, polishing, and coating enhance the functional and aesthetic properties of the machined products.
Advanced Machining Operations for Plastic Materials
Advanced machining operations suitable for plastics include:
CNC Turning
CNC Milling
CNC Drilling
CNC Broaching
These operations are preferred over most other machining processes for their precision and efficiency.
Each of these methods must be tailored to the special properties of the plastic material to ensure successful outcomes. Additional operations include cutting, turning, milling/routing, drilling, and grinding/lapping.
Milling Machines and Plastic Materials
Milling plastic materials requires a different approach compared to milling metal due to vibrations and potential chatter marks. Down-milling is preferred when milling plastics because it efficiently removes plastic chips. Furthermore, milling machines require specific tool types for machining plastics, such as:
Straight cutting knives for various shapes and sizes
Round head knives for arcs and curves
Tools like squeegees and ball sharp knives for harder plastics and spherical parts.
Achieving Dimensional Accuracy in Turning Operations
Turning is a process using a lathe machine to rotate the workpiece and shape it with stationary tooling. This process is particularly adapted for creating dimensionally accurate symmetrical plastic parts. Achieving dimensional accuracy in turning operations requires considering material shrinkage during cooling and adjusting designs with an allowance for post-processing or assembly.
Factors Influencing the Choice of Plastic for Machining
The process of selecting the appropriate plastic for machining requires consideration of numerous factors. For instance, thermal expansion rates of plastics are generally higher than those of traditional engineering materials, which is a critical consideration for designing machined parts to prevent issues like buckling or misalignment. Furthermore, essential material properties such as the impact of the chemical composition on strength, chemical resistance, and overall wear resistance of the material also play a role in the material selection process.
However, selecting the appropriate plastic material is not just about its properties. The specific needs of the machining project and the balance between material performance and budget constraints are also critical considerations. Therefore, it’s important to carefully weigh all these factors to make an informed decision about the right plastic material for your machining project.
Cost-Effective Strategies in Plastic CNC Machining
In any CNC machining project, cost-effectiveness plays a vital role. Here are some strategies to improve cost-efficiency:
Use advanced toolpath optimization software like CGTech’s Vericut Force to reduce cycle times. Atlas Fibre uses Vericut extensively.
Simplify part designs to minimize machining complexity.
Decrease the number of setups in the machining process.
Use multi-functional components to simplify the assembly process.
Implementing these strategies can lead to significant cost savings in your CNC machining projects.
In addition to optimizing designs and processes, optimizing CNC programs for consistent cutting forces and minimizing excessive cutting in turning operations can extend tool life and decrease machining costs. Furthermore, leveraging economies of scale in CNC machining operations implies that the cost per unit tends to decrease with increased production quantity, providing an opportunity for cost savings on large orders.
Maximizing the Potential of Machined Plastics
CNC plastic machining offers numerous benefits and immense potential. It provides:
Precision
Accuracy
Support for prototyping
Cost-effectiveness
Speed in the production process
Therefore, to maximize the potential of machined plastics, it’s crucial to select suitable materials for plastic machining projects. This requires deep knowledge of material properties and their interactions with various machining processes.
However, it’s not just about knowing the materials. You also need to understand the behavior of plastics under machining conditions, such as stress-relieving stock, the impact of moisture absorption on materials like nylon, and the tendency for dimensional changes during machining. This is where experts come in. They can guide you through the process and help you refine your techniques to consistently produce precision-machined plastic parts.
Innovative Uses of CNC Machined Plastic Components
CNC plastic machining caters to a diverse range of industries, including:
Aerospace: CNC machined plastics are used for components that demand lightweight characteristics, along with resistance to corrosion, high temperatures, and flames.
Medical: CNC machined plastic parts are used in medical devices and equipment, where precision and cleanliness are crucial.
Automotive: CNC machined plastic components are integral to producing intricate, high-quality parts used in vehicle interiors and assemblies.
Electronics: CNC machined plastic parts are used in electronic devices and equipment, where precision and durability are important.
These industries rely on a precision plastic machining company for its high precision CNC plastic machining and the ability to create complex shapes.
The medical and electronics industries also benefit from CNC machined plastics. In medical applications, machined plastics are used in everything from disposable syringes and dialysis machines to sophisticated bone and joint replacements. In electronic devices, the non-conductive, static-dissipative, and flame-retardant properties of CNC machined plastics enable the creation of advanced electrical designs.
Ensuring Quality in Every Machined Plastic Part
The utmost importance is placed on ensuring quality in every machined plastic part. This requires:
Establishing quality control processes
Setting precise goals, standards, and determining measurement metrics
Training personnel
Maintaining meticulous documentation to uphold these standards consistently.
Quality control measures such as statistical process control (SPC), visual inspections, and mechanical testing, along with strict measures for preventing and catching errors, are critical techniques employed throughout the CNC plastic machining process. Inspections start with the raw materials, ensuring they are defect-free and meet required specifications, followed by stringent monitoring of the production process, and culminating with a thorough finished product inspection for quality assurance before delivery.
Adapting Machining Techniques for Different Plastics
Understanding how various plastics behave under machining conditions is required for their machining. For instance, stress-relieving stock is critical for producing dimensionally accurate plastic parts, and materials with high moisture absorption like Nylon and Torlon should be conditioned or dry machined to achieve equilibrium moisture content before processing.
Moreover, machining parameters for plastics, including:
cutting speed
feed speed
depth of cutting
cutting clearance
In order to ensure quality and efficiency in the machining process, it is crucial to carefully optimize the handling of each plastic workpiece. Ongoing research and experimentation with various plastics are key for machinists to refine their techniques and consistently produce precision-machined plastic parts.
Expert Tips for Successful Plastic Machining Projects
A deep understanding of material properties and machining processes is required for successful plastic machining projects. Consulting with experienced plastic machining professionals can offer critical insights and recommendations for material selection tailored to specific applications. For complex projects, working with a knowledgeable manufacturer is advisable to prevent costly defects and ensure product success.
Moreover, tackling the broad selection of plastics and their unique properties demands partnering with suppliers who specialize in plastic fabrication challenges. Therefore, selecting suitable materials for plastic machining projects requires deep knowledge of material properties and their interactions with various machining processes. This is a crucial step in ensuring the success of any plastic machining project.
Summary
In conclusion, the world of machined plastics is vast and complex, offering immense potential for various industries. From understanding the intricacies of the machining process to selecting the right plastic material and balancing durability and machinability, every aspect of the process requires careful consideration and expertise. By leveraging advanced machining operations, employing cost-effective strategies, and ensuring quality in every machined part, you can maximize the potential of machined plastics and achieve successful outcomes in your plastic machining projects.
Frequently Asked Questions
What is the best way to machine plastic?
The best way to machine plastic is to use milling, which involves a high-speed cutting tool to subtract from the plastic shape in different directions, and utilizing computerized numerical control (CNC) milling for improved accuracy and efficiency.
What is the easiest plastic to machine?
The easiest plastic to machine is high-density polyethylene. It offers flexibility, easy machinability, excellent stress-cracking, and good chemical resistance, making it suitable for use in corrosive environments.
What is machined plastics?
Machined plastics are precision plastic components created through a subtractive machining process, used in aerospace, automotive, electronics, and other sectors to produce finished products of specific shapes and sizes.
What is the importance of plastic machining in modern industries?
Plastic machining is crucial in modern industries like aerospace, medical, automotive, and electronics, highlighting its significance in manufacturing.
How does CNC machining contribute to the production of plastic parts?
CNC machining contributes to the production of plastic parts by providing a precise and efficient method for high-volume production of complex parts with high-precision tolerances, allowing the creation of small and large intricate parts out of various plastics.