Looking for a customized part with a quick turnaround? ‘Machine shop online’ services are reshaping manufacturing with their speed, convenience, and cost-effectiveness. Understand how to choose the right service, the benefits of direct manufacturing, and ways to avoid common pitfalls in online machining. This guide provides the insights you need to make informed decisions, from evaluating service providers to receiving your high-quality custom parts.
Key Takeaways
Online machine shops leveraging CNC machining provide several benefits, including cost savings, faster production, and increased efficiency, but it’s vital to choose direct manufacturers like Atlas Fibre to ensure consistent quality and avoid pitfalls associated with marketplace fabricators.
Custom plastic parts manufacturing is essential for various industries, with material selection being critical to the parts’ performance. Atlas Fibre offers expert manufacturing of custom plastic parts with a focus on in-house production to maintain high-quality standards.
Atlas Fibre’s approach to direct manufacturing in the USA provides significant advantages, including protection of intellectual property, cost savings, and compliance with strict quality controls, contributing to supporting local economies and competitive lead times.
Discovering Online Machine Shop Services
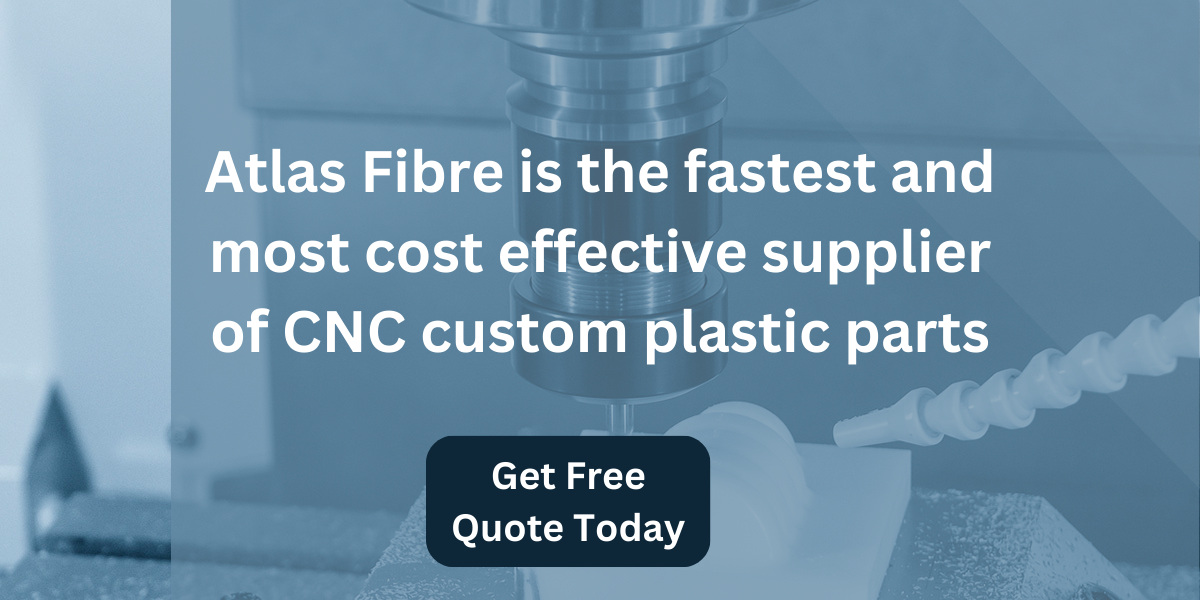
As the world becomes more digital, traditional manufacturing processes have transformed, leading to the emergence of online machine shops. Utilizing data and analytics, these platforms increase efficiency throughout production, providing substantial advantages over conventional manufacturing methods. The advent of cloud-based connectivity has set high expectations for instant product availability, making it easier than ever for consumers to acquire customized CNC machined parts through the use of a CNC machine, which employs computer numerical control machining.
Advanced digital technologies enable these online CNC milling shops to provide data-driven pricing, ensuring competitive costs devoid of traditional RFQ processes. The ability to quickly acquire parts is a key influencer of market competitiveness. Delaying the adoption of online manufacturing and cloud-based machining may result in losing out on early adopter benefits and market share. Therefore, embracing online manufacturing methods is not just an option, but a necessity to thrive in the competitive landscape.
Advantages of Online Machine Shops
Online machine shops primarily stand out due to the following reasons, including cnc machining advantages:
Considerable cost savings
Faster production times
Lower labor costs
More affordable CNC machining services
Improved overall productivity
Time, regarded as a priceless commodity, is another area where online machine shops excel. By streamlining the traditionally time-consuming RFQ process into a quicker, less distracting operation, businesses are able to focus more on product development and customer satisfaction. The accessibility to a wide range of materials and advanced manufacturing capabilities further adds to the allure of these online services.
Pitfalls of Marketplace Fabricators
Despite its numerous benefits, the digital manufacturing landscape also has its drawbacks. A common issue with marketplace fabricators is that they often do not produce their own parts. Instead, they send the work through a network, leading to inconsistencies in quality from different manufacturers. This outsourcing methodology can also introduce additional costs in the form of markups, making it more expensive than working with a shop that manufactures in-house.
Moreover, dealing with online part marketplaces can be unpredictable, as customers have no control over which manufacturer within the network will create their part. This uncertainty often leaves them unsure of the quality to expect.
Fortunately, there is a reliable alternative – Atlas Fibre. As a direct manufacturer, Atlas Fibre assures quality, consistency, and delivery, manufacturing parts 100% in-house.
Custom Plastic Parts Manufacturing
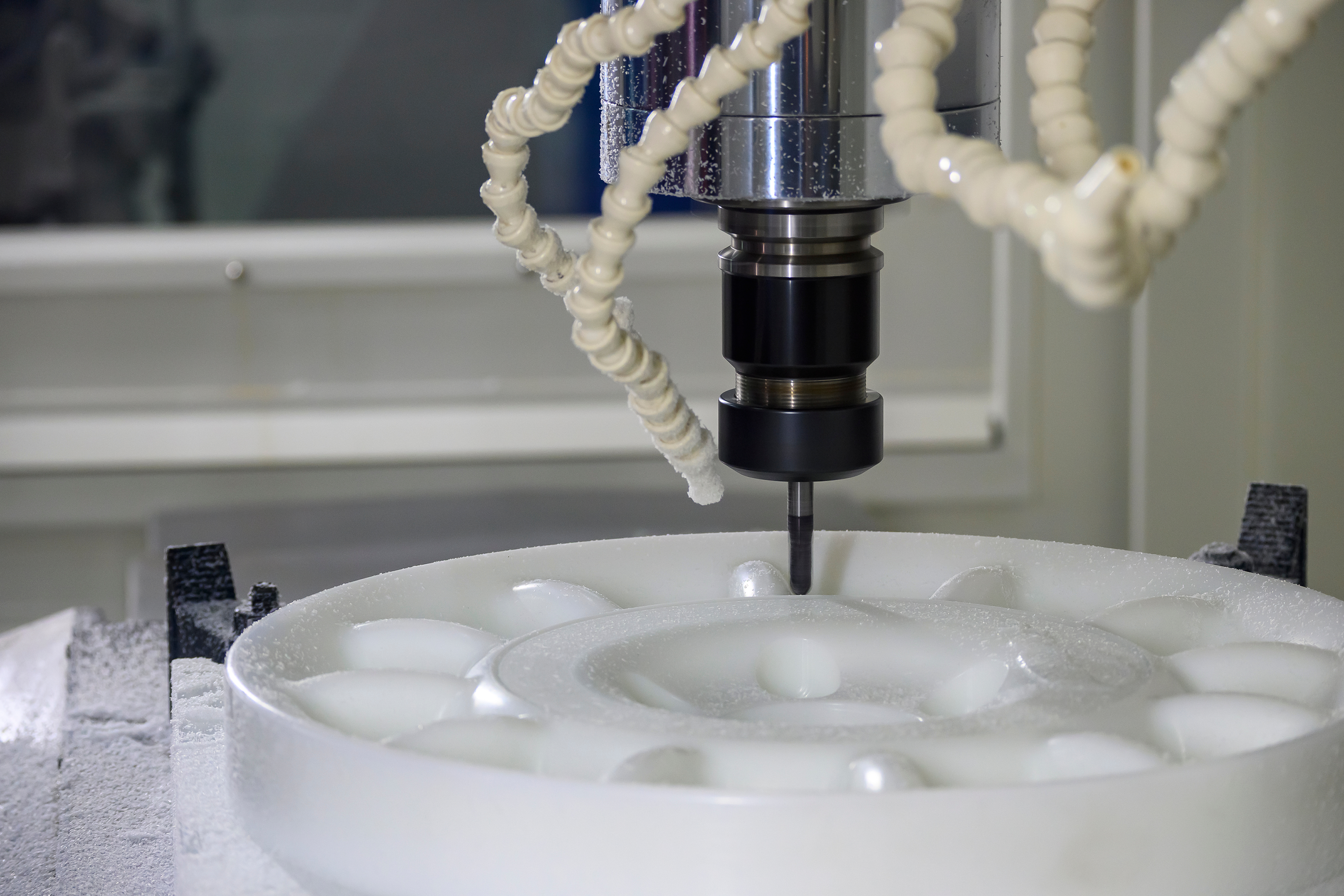
Within the manufacturing sector, custom plastic parts have become a flexible and economical solution for numerous industries. The manufacturing technology of choice in this arena is custom CNC machining, a subtractive manufacturing technology that uses CAD modeling and G-code to remove material from a solid workpiece with precision and speed. Plastics offer a wide selection, are less expensive, and allow for faster machining time compared to other CNC machining materials, making them incredibly advantageous in the CNC machining process. Custom CNC machining services have become essential for industries seeking high-quality, precise plastic components.
One of the preferred processes for custom plastic parts manufacturing is plastic injection molding. This method strikes an efficient balance between cost and functionality, making it a favored choice for many manufacturers. Atlas Fibre, a dedicated plastics and composites-only machine shop, specializes in manufacturing custom plastic parts, offering unparalleled expertise and quality in the field.
Material Selection
Selecting the appropriate material is a vital step in the manufacturing of custom plastic parts. With over 85,000 commercial plastic materials available, broadly categorized under thermosets and thermoplastics, the selection process can be daunting. The chosen material significantly influences the final plastic part’s:
Durability
Resistance to environmental conditions
Flexibility
Impact resistance
Tensile strength
Materials such as ABS, Acetyl, Acrylic, Nylon, PEEK, ULTEM, G10/FR4, CE, and Polycarbonate are among the various options used in custom parts manufacturing. Each offers unique benefits such as:
Impact strength
Toughness
Optical clarity
Resistance to heat
When selecting a resin for custom plastic parts, it’s imperative to consider factors like chemical and mechanical properties, availability, and cost to achieve the desired balance between functionality and budget constraints.
Direct Manufacturer vs. Network
Despite their flexibility and ability to alleviate supply chain disruptions through their distributed manufacturing model, online networks of machine shops have significant disadvantages. The inconsistency in quality and the potential lack of personalized interactions due to dealing with various suppliers can be a significant drawback.
This is where direct manufacturers like Atlas Fibre come into play. With personalized services and more consistent quality control over their products, Atlas Fibre offers clear advantages over online networks. The assurance of quality, coupled with the convenience of an online platform, makes Atlas Fibre a go-to solution for custom plastic parts manufacturing.
In-House Production: The Atlas Fibre Advantage
Atlas Fibre’s commitment to quality and consistency is evident in their in-house production facility. Specializing in the customization of phenolic and thermoset materials for specific applications, Atlas Fibre ensures a high degree of precision and conformity to customer requirements. With a wide array of CNC machines, including:
mills
lathes
routers
Swiss machines
they can precisely machine various phenolic, glass thermosets, and thermoplastics.
An added advantage of working with Atlas Fibre is the enhanced protection of intellectual property and confidentiality. With direct handling and centralized management of design and production, they provide better security for client designs and ideas.
Consistent Quality
Atlas Fibre’s in-house production enables rigorous control over manufacturing processes, leading to uniformly high-quality custom plastic parts. The use of advanced CNC machining technology ensures precise and repeatable production, contributing to the uniform quality of their custom parts.
Quality control protocols, including dimensional testing and defect analysis, are integral to meeting customer specifications and maintaining consistent quality. The dedicated support and tailored experience offered by direct manufacturers like Atlas Fibre foster closer relationships and contribute to more consistent quality control for long-term projects.
Cost Savings
A significant advantage of working with direct manufacturers like Atlas Fibre is the potential for cost savings. By bypassing intermediaries, Atlas Fibre’s approach to direct manufacturing leads to more competitive pricing and direct cost savings for customers seeking custom plastic parts.
Made in the USA
Atlas Fibre’s commitment to manufacturing in the USA is a testament to their dedication to quality and regulatory compliance. With the capacity and capability to make any plastic part 100% in-house at their facility in Northbrook, Illinois, they ensure stringent quality control over each product.
In addition, by choosing Atlas Fibre, customers are also supporting local economies. Considering the fully automated machining philosophy, Atlas Fibre guarantees the lowest cost, even beating foreign machinists, with significant lead time savings.
Navigating the Online Ordering Process
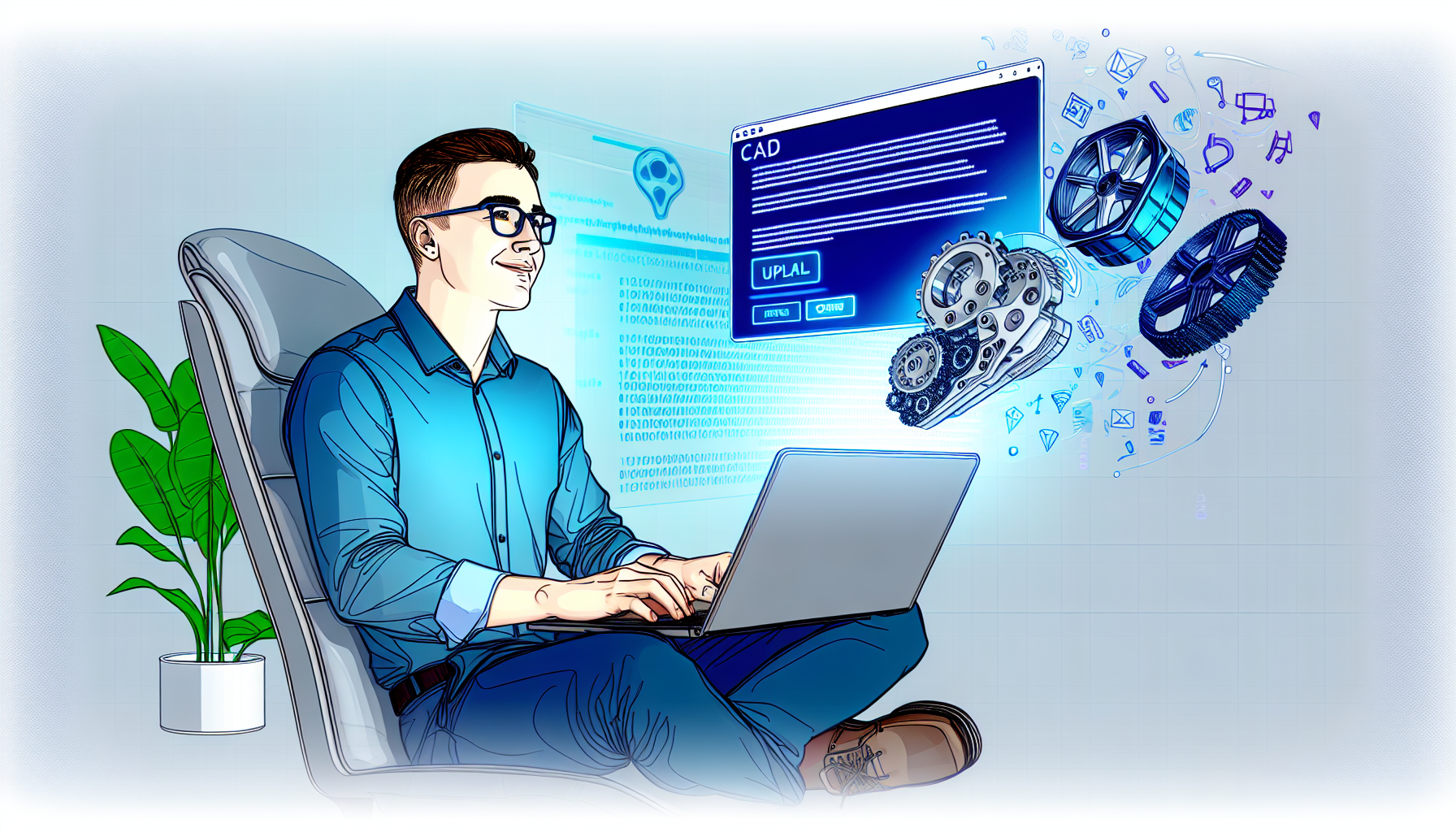
The ease of online ordering makes obtaining custom plastic parts simpler than ever. The online ordering process typically includes the following steps:
Create an account on the machine shop’s website, allowing customers to save their project details and preferences.
Before placing an order, consider factors such as the lead time, which varies based on complexity and order volume.
Consider the expected delivery date.
By following these steps, you can easily order custom plastic parts online.
Once an account is set up, customers can upload their custom part design files directly on the machine shop’s platform. Supported file types usually include formats like DWG, DXF, and IGES. Upon submitting design files, customers receive a quote, which includes a cost breakdown and a detailed report on manufacturability issues if there are any. This step is crucial and customers should ensure the quote aligns with their design requirements.
Uploading Design Files
The first step in the online ordering process is uploading a 3D CAD file of the machined part to receive an online CNC quote. Along with the CAD files, customers need to provide any supplemental files that specify tolerances, threading, or other special requirements.
Upon uploading, users may receive instant CNC quotes or be directed to one of the company’s engineers for potential design for manufacture guidance. This not only ensures accurate pricing but also provides a platform for feedback and improvements.
Receiving Quotes
One of the key advantages of online CNC machining services is the ability to receive quotes quickly and conveniently, which includes getting an estimate of the CNC machining service cost. By uploading design files to a CNC machining service platform, customers can get detailed pricing, lead times, and Design for Manufacturability (DFM) feedback. Some shops even offer an instant quote using their free CAD software, making the process even more efficient with their fast CNC machining capabilities.
Following the quote, customers are provided with a payment link to facilitate easy order placement should they decide to proceed. It’s crucial to review the quote for accuracy and alignment with design requirements and request adjustments or clarifications if necessary.
Communication and Support
Smooth communication and dedicated support are vital elements of a successful online machine shop experience. Online machine shops offer round-the-clock customer support with dedicated representatives who assist with part design, material selection, surface finishing, and determining lead times. Some shops even incorporate B2C experiences into their B2B services to ensure a familiar and efficient customer experience.
Customers are kept informed about their orders through automated email notifications with order details and tracking numbers. They can also access real-time information about their in-process orders through secure website logins. This transparency in communication not only encourages customer trust but also fosters long-term business connections.
Applications of Custom Plastic Parts
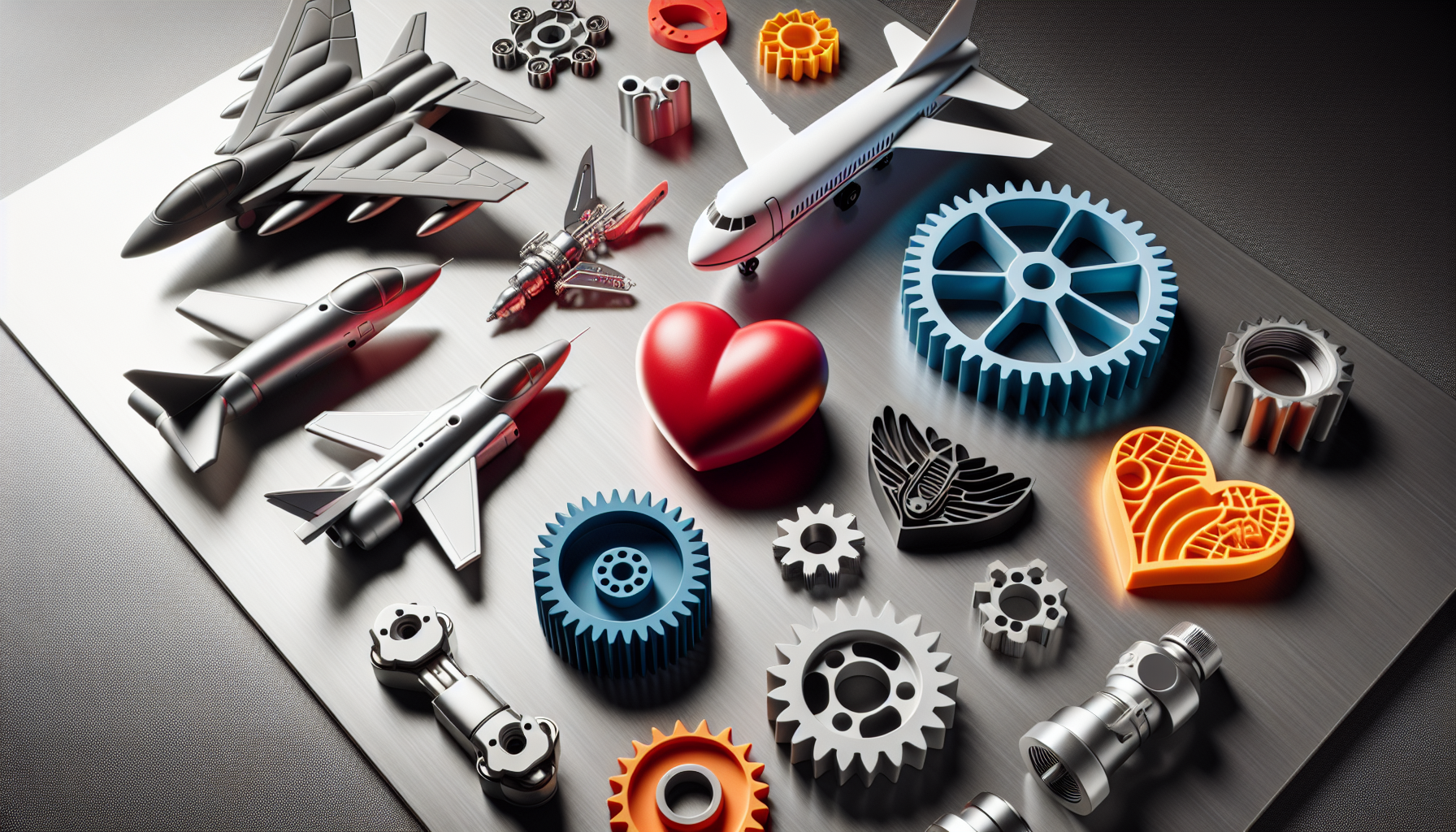
Custom plastic parts are widely used in a variety of industries, including:
Aerospace: due to their precision, corrosion resistance, and impressive strength-to-weight ratio
Medical: for creating specialized and sterile medical devices
Automotive: for manufacturing durable, lightweight, and cost-effective components
These parts are known for their versatility, adaptability, and the benefits they bring to different industries.
Beyond these industries, custom plastic parts have also found significant applications in robotics and electronics. Whether it’s constructing lightweight and durable components for robotics or providing insulation and support for delicate electronic components, custom plastic parts have proven to be invaluable.
Medical Devices
In the medical industry, custom plastic parts are essential for creating a variety of medical devices, including:
Bone and joint replacements
Artery repair tools
Prosthetics
Implants
Syringes
Respirators
Insulin pens
Dialysis machines
Surgical instruments
Heart rate monitors
MRI machines
Medication pumps
The ergonomic potential of plastic allows for the creation of medical products that are easier to use and more comfortable for patients. With the right design and manufacturing process, custom plastic parts can significantly enhance the functionality and usability of medical devices.
Aerospace and Automotive
Custom plastic parts play a significant role in aerospace and automotive industries. In aerospace, these parts serve as key components in interior and exterior aircraft design, including:
Interior wall panels
Luggage storage compartments
Aircraft doors
Exterior panels made from materials like ABS, known for being lightweight and strong.
In the automotive industry, custom plastic parts are integral to building components such as:
body panels
bumpers
dashboards
fluid reservoirs
These parts are prized for their durability and design flexibility, enabling manufacturers to create components that not only serve their functional purpose but also contribute to the aesthetics of the vehicle.
Robotics and Electronics
In the world of robotics, custom plastic parts are essential for constructing lightweight and durable components that can endure repetitive movements and strain. The use of plastics in robotics enhances the efficiency of the robots by reducing the overall weight, which in turn lowers energy consumption and operational costs.
Similarly, in electronics manufacturing, plastic parts provide insulation, protection, and support for delicate electronic components within devices. Whether it’s housing for a circuit board or a protective casing for a smartphone, custom plastic parts play a vital role in the functionality and longevity of electronic devices.
Tips for Designing Custom Plastic Parts
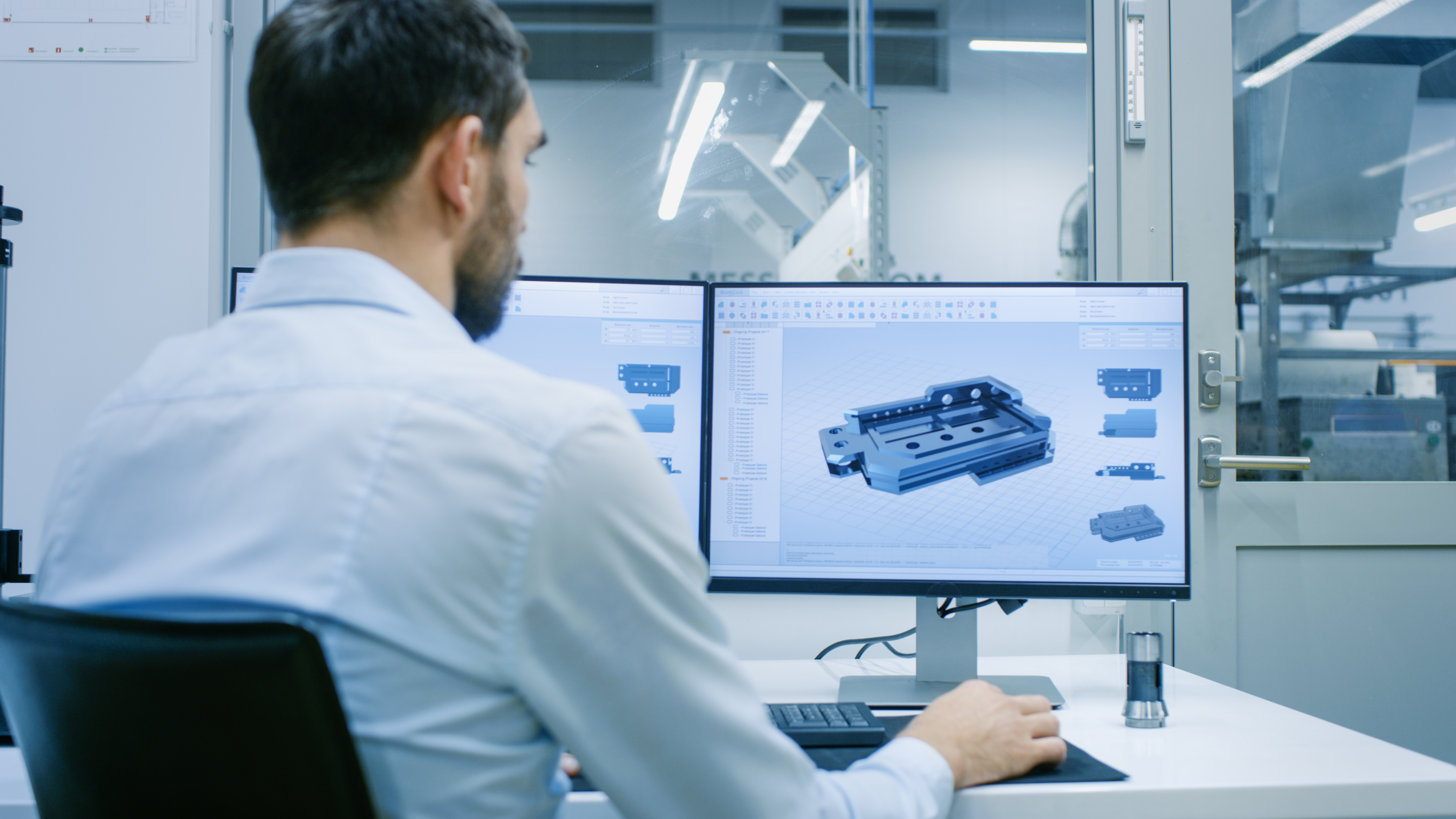
The design of custom plastic parts necessitates a thorough comprehension of the product’s functional requirements, the manufacturing process, and the intended use. It’s advisable to start with a detailed sketch or consult an engineer to create a 3D model, which can help identify any potential flaws in the design early in the process. Engaging with plastic part engineering experts ensures the design is both manufacturable and will function as intended.
It’s also recommended to:
Develop and test prototypes using rapid prototyping to catch design issues and make necessary adjustments before committing to mass production.
Ensure that the part specifications meet the actual needs of the end product, balancing factors such as durability, color, resistances, and production costs.
Collaborate with an experienced team and adopt a realistic and flexible approach to streamline the production process.
Material Selection
Choosing the appropriate material is vital in the design process of custom plastic parts. Factors such as hardness, flexibility, durability, and heat resistance need to be taken into account to ensure the performance requirements of the part are met. The cost and availability of different plastic resins should be balanced against the required performance of the part, making them crucial factors in material selection.
Material selection should also account for the intended end-use of the part, special appearance considerations, potential chemical exposure, and mold design to ensure the final product meets all application needs. Defined tolerances based on the part’s function and fit are also crucial, with tighter tolerances typically increasing costs due to the need for greater manufacturing precision, such as in CNC machining tolerances. For non-critical dimensions, using general tolerances or industry standard tolerances can help in reducing costs and streamlining the quoting process.
Design for Manufacturability
Considering design for manufacturability (DFM) is a key element in the process of designing custom plastic parts. Selecting manufacturing processes, such as plastic injection molding, that consistently produce high-quality parts with complex geometries in a cost-effective manner can greatly enhance the product’s success. It’s important to maintain flexibility throughout the design process to limit time spent on revisions and streamline the transition from design to production.
Understanding that some plastic materials may require secondary operations, like custom inserts and trimming, which can raise production costs, is also important. Using common material sizes and standard tooling in designs can minimize the necessity for custom work and decrease quoted part costs. Clear communication of any specific machining or finishing requirements ensures these are accounted for in the cost and lead time estimates.
Engaging with engineering experts early in the design process can verify that the part design is both manufacturable and functional. Be open to the process of trial and error, and be ready to include constructive feedback to improve design manufacturability.
Summary
In conclusion, the advent of online machine shops has revolutionized the manufacturing landscape, offering unmatched efficiency, convenience, and a host of benefits. However, understanding the potential pitfalls is as crucial as recognizing the advantages. Atlas Fibre emerges as a reliable solution, combining the convenience of online services with the consistency, quality, and cost-effectiveness of in-house production. With the right knowledge, material selection, and design, custom plastic parts can be a game-changer across various industries. So, step into the future of manufacturing and embrace the potential of online CNC machining services.
Frequently Asked Questions
Where to get cnc work done?
You can get CNC work done through Atlas Fibre,
What are the advantages of online machine shops?
The advantages of online machine shops include significant cost savings, time efficiency, access to a wide range of materials and advanced manufacturing capabilities, as well as a streamlined RFQ process, enabling businesses to focus on product development and customer satisfaction.
How does Atlas Fibre ensure consistent quality in custom plastic parts?
Atlas Fibre ensures consistent quality in custom plastic parts through in-house production, strict control over manufacturing processes, utilization of advanced CNC machining technology, and implementation of rigorous quality control protocols to meet customer specifications.
What is the process of ordering custom plastic parts online?
To order custom plastic parts online, you need to create an account on the machine shop’s website, upload your design files, receive quotes, and finalize your order on the platform. Good luck with your custom parts order!
Why is material selection important in designing custom plastic parts?
Material selection is crucial in designing custom plastic parts because it significantly affects the part’s durability, resistance to environmental conditions, flexibility, impact resistance, and tensile strength, as well as cost considerations.