As the global demand for electric vehicles (EVs) continues to surge, the role of innovative composites for EV performance becomes increasingly apparent. These lightweight yet durable materials have the potential to enhance efficiency, improve safety, and transform energy storage. In this blog post, we’ll explore the world of glass-epoxy and phenolic composites for EV, the advancements in structural battery composites, fire protection strategies, and the future market trends that will shape the EV industry.
Key Takeaways
- Glass-epoxy and phenolic composites are revolutionizing EV efficiency with improved battery technology, boosted mechanical properties, and design flexibility.
- Atlas Fibre is a specialist provider of composite materials for EVs that offers an extensive selection of materials & precision machining services tailored to unique requirements.
- Composites offer advantages over traditional materials such as weight reduction, increased strength & stiffness, corrosion resistance & thermal insulation, making them ideal for electric vehicle applications.
Revolutionizing Electric Vehicle Efficiency with Glass-Epoxy and Phenolic Composites
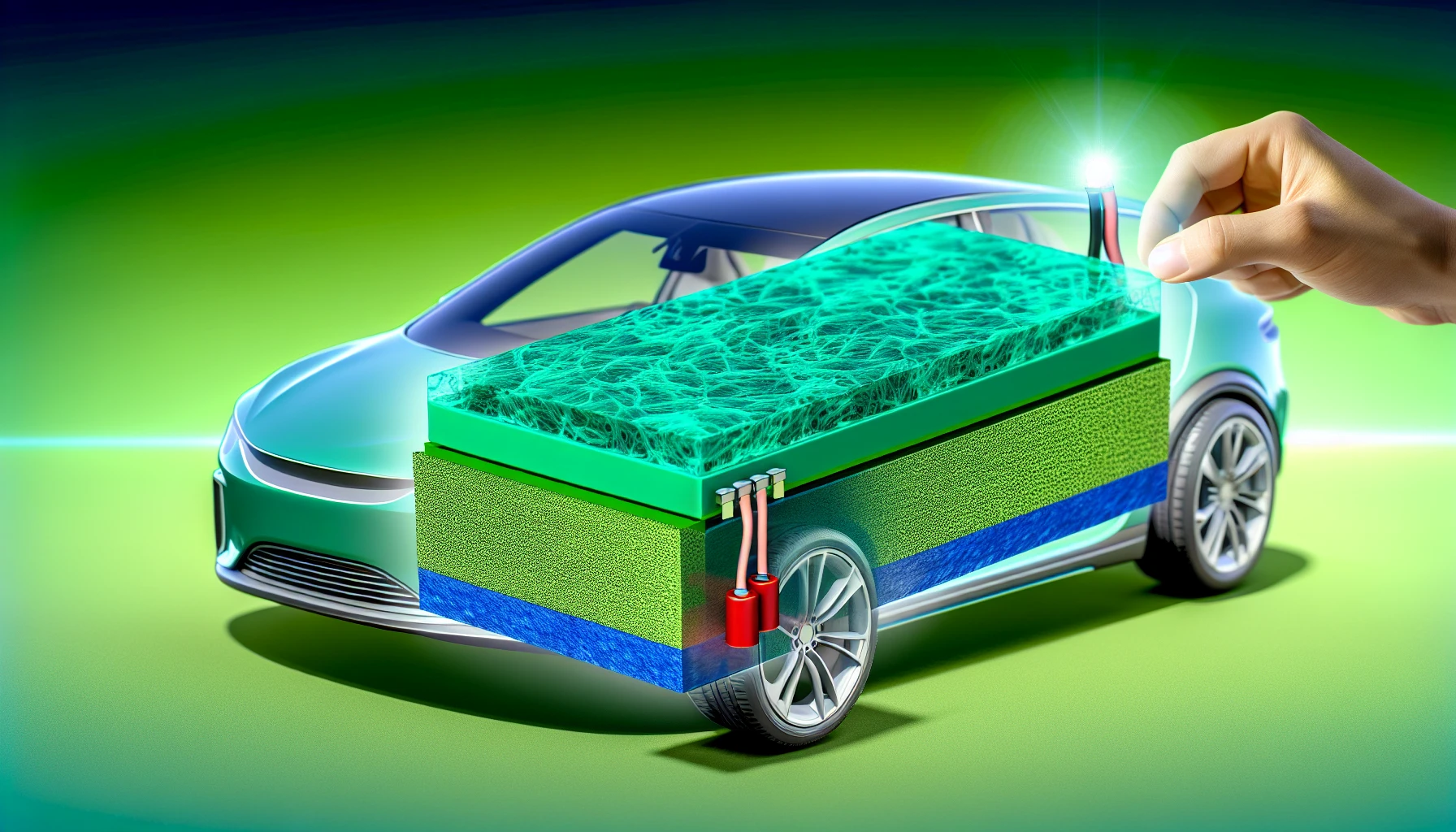
The use of glass-epoxy and phenolic composites is transforming the efficiency of electric vehicles by improving battery technology and boosting mechanical properties. These materials are significantly lighter and stronger than traditional alternatives used in internal combustion engine vehicles, allowing for enhanced performance and greener transportation.
Composites like these are used in the construction of insulation kits, which are straightforward to install and can dampen vibration, absorb and neutralize corrosive battery acids, and prevent premature failure and hazardous leaks. The ability to create more complex shapes in the design of EV components is another advantage offered by these innovative composites.
The Role of Composites in Battery Technology
Battery performance optimization, weight reduction, and thermal management enhancement in electric vehicles heavily rely on composites. They allow for complex shapes in the design of EV components, providing more design flexibility. In comparison to steel and aluminum, composites offer significant benefits in meeting flame retardancy requirements and reducing the risk of thermal runaways in relation to rapid charging.
Various composites, such as plastic composites with embedded fibers composed of glass or carbon, as well as thermoplastic composite materials, are employed in electric vehicle battery technology. Carbon fiber composites, which are lighter than steel and aluminum, offer strength, durability, and lightweight properties to boost the performance of electric vehicle batteries.
Boosting Mechanical Properties for Better Performance
Advanced composites offer superior mechanical properties, contributing to better overall EV performance. Some of the mechanical properties of glass-epoxy composites employed in electric vehicles include:
- High mechanical strength
- Remarkable impact resistance
- Minimal shrinkage
- Desirable surface texture
- Efficient resistance to bending loads
These properties make glass-epoxy composites an excellent choice for electric vehicles.
Phenolic composites offer superior mechanical properties, such as strength and impact energy absorption, providing over 65% property retention after fire testing compared to cast aluminum. The various methods employed to enhance the mechanical properties of composites for improved EV performance include combining different types of fibers, increasing electrical current capacity, integrating carbon nanotubes, using boron carbide, and optimizing the design and composition of composites.
Transforming Energy Storage: Structural Battery Composite Advancements
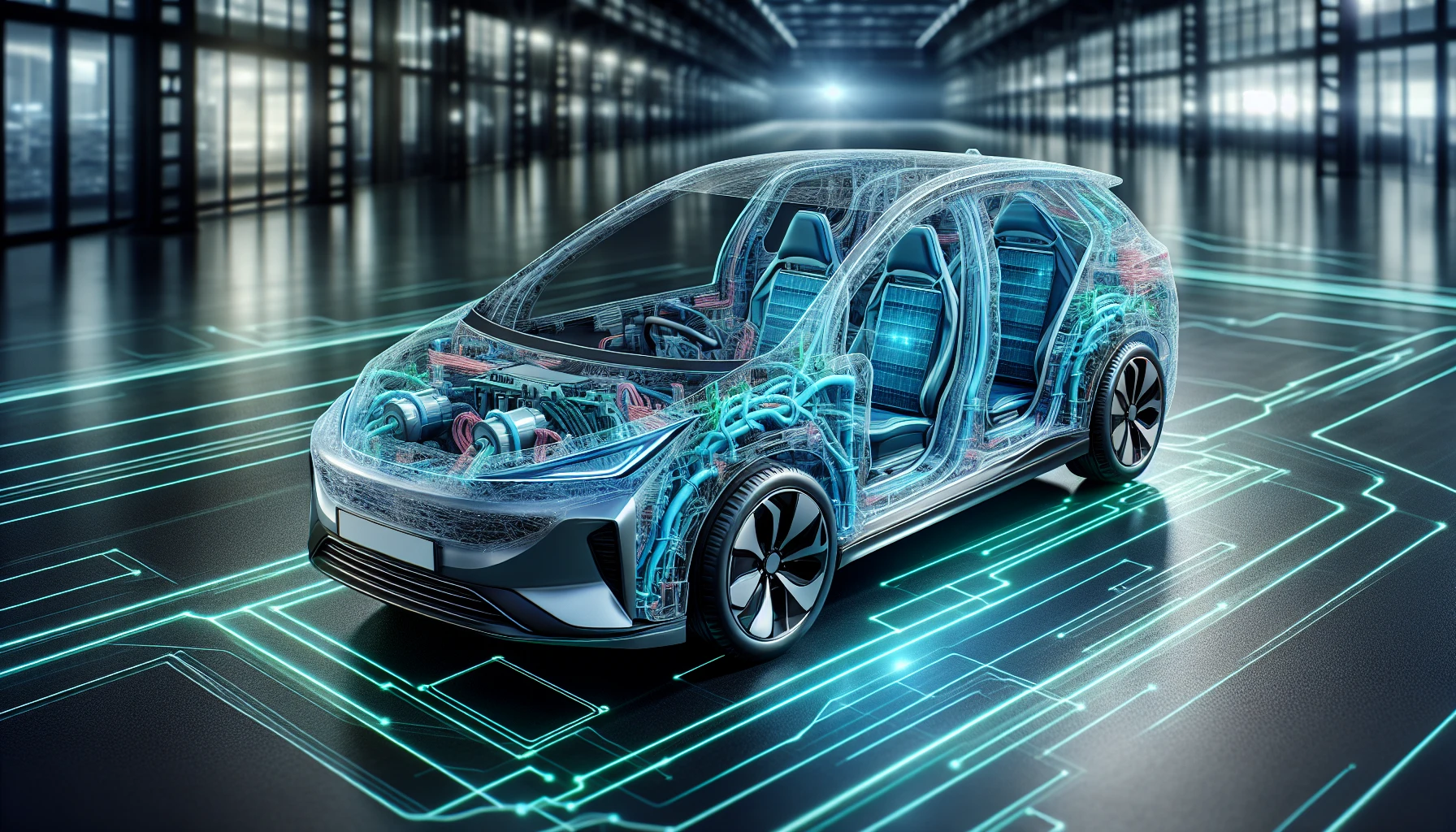
Structural battery composites (SBCs) are revolutionizing energy storage, including battery packs. They use a vacuum bagging process to encapsulate active materials within composite shell layers. These innovative materials enable the enhancement of energy density and integration of structural components for optimized design.
SBCs feature a laminated structure, made up of:
- An LFP cathode
- Glass fiber separator
- Graphite anode
- Two composite layers
The two layers are orientated in 0/90° and 90/0° vectors respectively. These composites present vast potential for improving energy storage and mechanical performances in electric vehicles.
Enhancing Energy Density for Extended Range
The driving range of an electric vehicle is directly impacted by the total energy capacity of the battery, making enhancing the energy density of the battery essential for extending the vehicle’s range. Composites provide a lightweight and strong material for battery enclosures and structural components, thus reducing the overall weight of the battery system. This leads to improved vehicle performance and increased range.
Innovative composites that have significantly improved energy density include:
- SBCs with enhanced energy storing and mechanical performance
- Poly(vinylidene fluoride) composites with induced PDA-coated 0.5Ba(Zr0.2Ti0.8)O3-0.5(Ba0.7Ca) for a notable increase in energy storage density
- BN-P(VDF-HFP)/BT-BN composites with improved energy density due to the addition of BN
Li2FeSiO4, LiFePO4 (LFP), and composites with silicon integrated into graphite anodes are the most effective composite materials for increasing energy density in EV batteries.
Integrating Structural Components for Optimized Design
Structural battery composites in electric vehicles are a type of multifunctional material that combines the functions of energy storage and structural support. They utilize materials such as carbon fiber for the negative electrode and aluminum film for the positive electrode, integrated into the vehicle’s structure. This allows for massless energy storage, thus reducing the weight and improving the overall performance of the electric vehicle.
Integrating energy storage and structural components in electric vehicles provides several advantages, such as optimized utilization of space, improved energy management, and increased grid integration. The Tesla Model S and the BMW i3 are examples of electric vehicles that have successfully integrated structural components for optimized design.
Fire Protection Strategies in EV Composites
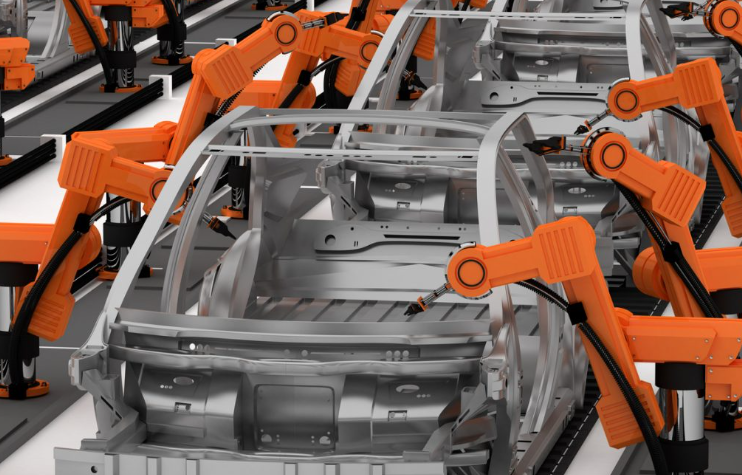
As the energy density of EV batteries increases, so does the risk of thermal runaway. To address this concern, fire protection strategies are being developed for EV composites, including:
- The use of flame retardant materials
- Enhanced cooling systems
- Advanced battery management systems
- Improved battery packaging and enclosure designs
These measures aim to minimize the risk of fire and ensure the safety of electric vehicles.
Phenolic and epoxy composites, including intumescent coatings, are designed to provide flame resistance and contain thermal runaway events, thereby reducing the risk of fires and ensuring passenger safety. These composites are capable of withstanding high temperatures and act as a protective barrier for the battery.
Flame Retardant Composites
Flame retardant composites in electric vehicles (EVs) are materials used in the construction of EV components that possess the ability to impede or slow down the propagation of flames. These composites are designed to increase the safety of EVs by reducing the risk of fire and enhancing the overall fire resistance of the vehicle. They are commonly implemented in high-voltage components of EV batteries, such as separator plates, cover plates, and control units.
The fabric structure and high fiber content of flame retardant composites act to prevent flames from spreading, thereby enhancing the safety of electric vehicles. The flame retardants used in composite housings also enhance fire safety and environmental sustainability.
The Future of EVs: Material Innovation and Market Trends
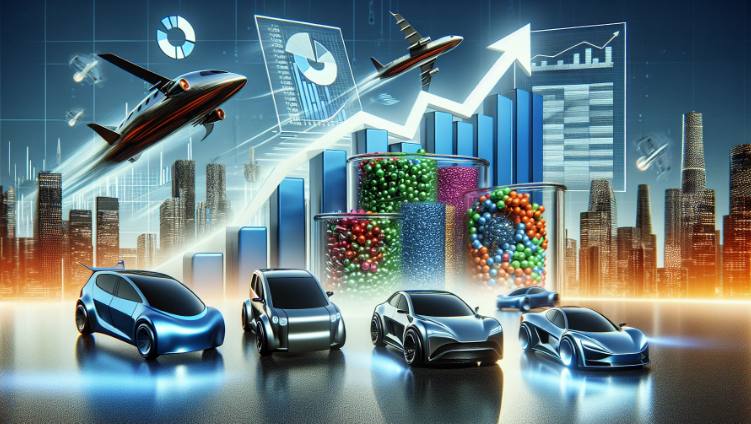
Material innovation and market trends, with a key role played by composites, will shape the future of electric vehicles, as they meet demand and outperform traditional materials. With the expansion of the EV market, the demand for composites in the automotive industry is expected to grow considerably.
Recent advancements in composite materials for electric vehicles include:
- Lightweight composites that improve range and performance
- Battery enclosures made from composites for sustainability
- New techniques to increase the electrical current capacity of copper composites
Mitsubishi Chemical has also presented its electric vehicle composite material portfolio for advanced energy storage.
Market Dynamics and Demand for Composites
Current market trends indicate a significant increase in electric vehicle sales, constituting 5.8 percent of all new vehicles sold in the United States in 2022. Major automakers are intensifying their electrification efforts by launching new models and reducing prices. It is projected that electric vehicle sales could reach 40 percent of total passenger car sales in the United States by 2030.
The market demand for composites in EVs is anticipated to experience substantial growth as EVs become increasingly popular in the automotive industry. According to market projections, the Automotive Composites Market is expected to reach USD 14.3 billion by 2028 and is projected to exceed US$ 20 billion by 2032. The increasing demand for lightweight and electric vehicles is driving the expansion of the automotive composites market.
Comparing Composites to Traditional Materials
Composites offer numerous advantages over traditional materials like aluminum and steel, making them a preferred choice for EV applications. Utilizing composites in electric vehicles offers a number of advantages in comparison to aluminum and steel, such as:
- Weight reduction
- Enhanced strength and stiffness
- Design flexibility
- Corrosion resistance
- Thermal insulation
Although composite materials may be more costly to manufacture than traditional materials, such as metals or plastics, the use of composites in EVs can help to reduce weight by up to 30%, which can enhance fuel economy and decrease greenhouse gas emissions. The perceived cost-effectiveness of composites relative to traditional materials is a key factor in the decision-making process for EV manufacturers.
Installation and Accessibility: Overcoming Challenges in EV Composites
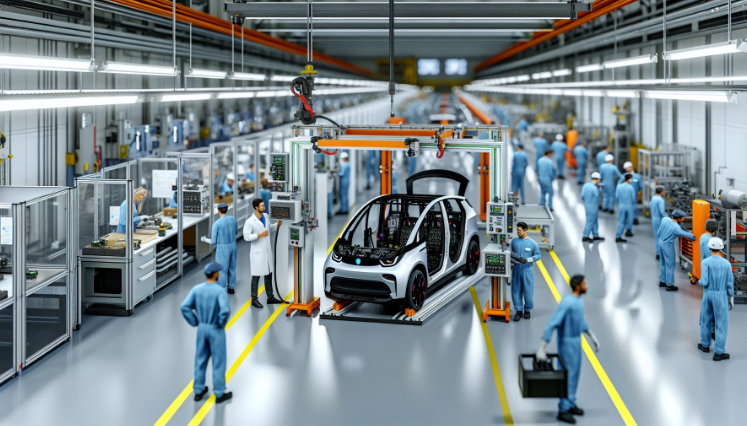
Resolving challenges in EV composites, including production streamlining and supply chain and cost factors navigation, will be pivotal for mass adoption. The production of EV composites presents various challenges, including:
- The need to reduce manufacturing costs and improve production performance
- Developing advanced battery technology
- Addressing strategic and logistical issues in the extraction, refining, manufacturing, and assembly of EV components
Efficient production processes and techniques are needed to make composites more accessible for widespread EV use. Resolving supply chain and cost challenges will be pivotal for the successful integration of composites in EVs.
Streamlining Production for Mass Adoption
Currently, prepregs manufacturing, automated and efficient production lines for mid- and high-volume production, dry filament winding, and the use of cost-efficient and lightweight materials are being utilized for EV composites. The challenges associated with the mass production of EV composites include addressing the substantial curb weight of electric vehicles, managing the thermal runaway of batteries, creating lightweight components with improved flame retardancy, and addressing the complexities of manufacturing EV components in comparison to traditional vehicle components.
Innovative production techniques for composites in the electric vehicle industry include the development of hybrid metal-based composites using thermoset polymers, presenting new opportunities and challenges for composites in electric vehicles. Additionally, lightweight composite materials and techniques like ‘patching’ can be used to streamline production and adapt existing production lines for electric vehicle composites.
Navigating Supply Chain and Cost Factors
The supply chain has a direct effect on the production and accessibility of EV composites. It can affect:
- The availability and cost of raw materials
- The efficiency of manufacturing processes
- The reliability and stability of the supply of composites, which can have an impact on the overall production of electric vehicles
- The sourcing and transportation of composites, which can affect their accessibility to manufacturers.
The costs associated with the production of EV composites include the cost of materials such as composites, aluminum alloys, and high-performance materials, as well as the cost of essential raw materials like cobalt, nickel, and lithium. Additionally, production-related costs, excluding materials, can also contribute to the overall cost of EV composites.
Selecting a Material and Machining Partner for EV Composites
Selecting a material and machining partner like Atlas Fibre can provide expertise in composite materials and create bespoke solutions for specific EV applications. When deciding on a material and machining partner for EV composites, consider factors such as:
- Composites expertise
- Advanced manufacturing capabilities
- Material selection skills
- Quality control and testing
- Collaboration and communication
Atlas Fibre provides a wide range of composite solutions, tailored to meet the unique requirements of EV applications. We have extensive experience in developing and manufacturing composite materials that are lightweight, durable, and possess excellent mechanical properties. We collaborate closely with EV manufacturers to understand their specific needs and provide customized solutions that meet their performance and design requirements.
Atlas Fibre is Both a Material Supplier and Machining Expert for Composite Materials
Atlas Fibre is a trusted supplier and machining expert for composite materials, providing a comprehensive selection of materials and machining services for a variety of applications. We offer a variety of materials for EV composites, including:
- Glass reinforced composites (GRCs)
- Thermoset composites such as glass epoxy, glass silicone, glass melamine, and phenolics
- Prepreg composites for various applications.
We provide a variety of machining services for composite materials, such as CNC machining, stamping, waterjet cutting, and precision grinding. Our extensive material expertise and the largest inventory of thermoset composites in North America guarantee the quality and performance of our composite materials for EV applications.
Atlas Fibre can make a Material Bespoke to Your Application
Atlas Fibre can develop custom composite materials tailored to specific EV applications, ensuring optimal performance and efficiency. We specialize in carbon fiber, fiberglass, and aramid fiber composites for electric vehicle applications.
Our bespoke materials are made using thermoset manufacturing techniques. This involves:
- Heating fibers and polymers until they reach a liquid state
- Forming them into the desired shape
- Allowing them to cool through a high-pressure lamination process
By providing custom composite solutions, we help EV manufacturers create vehicles with improved performance and efficiency.
Summary
The world of innovative composites holds immense potential for revolutionizing the electric vehicle industry. With their ability to improve efficiency, safety, and energy storage, these materials are poised to play a crucial role in the future of transportation. As the demand for EVs continues to grow, the need for advanced composites will only increase, making it essential for manufacturers and suppliers to invest in the development and integration of these materials.
Make the Right Choice… Consult the Experts at Atlas Fibre
With our extensive inventory, rapid response, and advanced technology, we can help you choose the optimal material for your unique needs. Connect with our team to request a quote.
Frequently Asked Questions
How do composites improve electric vehicle efficiency?
Composites enable EVs to become more efficient by enhancing battery performance and providing increased mechanical properties such as strength and lighter weight.
What role do composites play in battery technology?
Composites play a crucial role in battery technology, enabling improved performance, reduced weight, and improved thermal management for electric vehicles.
How do flame retardant composites improve EV safety?
Flame retardant composites help improve EV safety by impeding the propagation of flames, thus enhancing the vehicle’s fire resistance and reducing the risk of fire.
What factors are driving the demand for innovative composites in electric vehicles?
Government incentives, investments in EV technology, and the need for lightweight vehicles to improve fuel economy are driving the demand for innovative composites in electric vehicles.
How can composites be integrated into the structure of an electric vehicle?
Structural battery composites can be integrated into the structure of an electric vehicle, optimizing design and performance and providing seamless energy storage.