Imagine a material that can withstand extreme temperatures, resist chemicals, and remain dimensionally stable, all while being inherently flame-retardant. Unfilled Ultem, a high-performance polyetherimide (PEI) material, is designed to meet these requirements and more. In this blog post, we will explore the unique properties of Ultem, how it compares to other PEI grades, its applications in various industries, processing techniques, and compliance with regulatory standards. So, buckle up and get ready to discover the world of this high performance plastic!
Key Takeaways
- Ultem 1000 is a highly reliable material with superior mechanical, electrical and dimensional properties for various industries.
- It provides excellent heat resistance, chemical resistance and flame retardancy for applications such as medical devices and aerospace components.
- When selecting an Ultem 1000 supplier consider factors such as material quality, technical support & customization options.
Understanding Ultem 1000
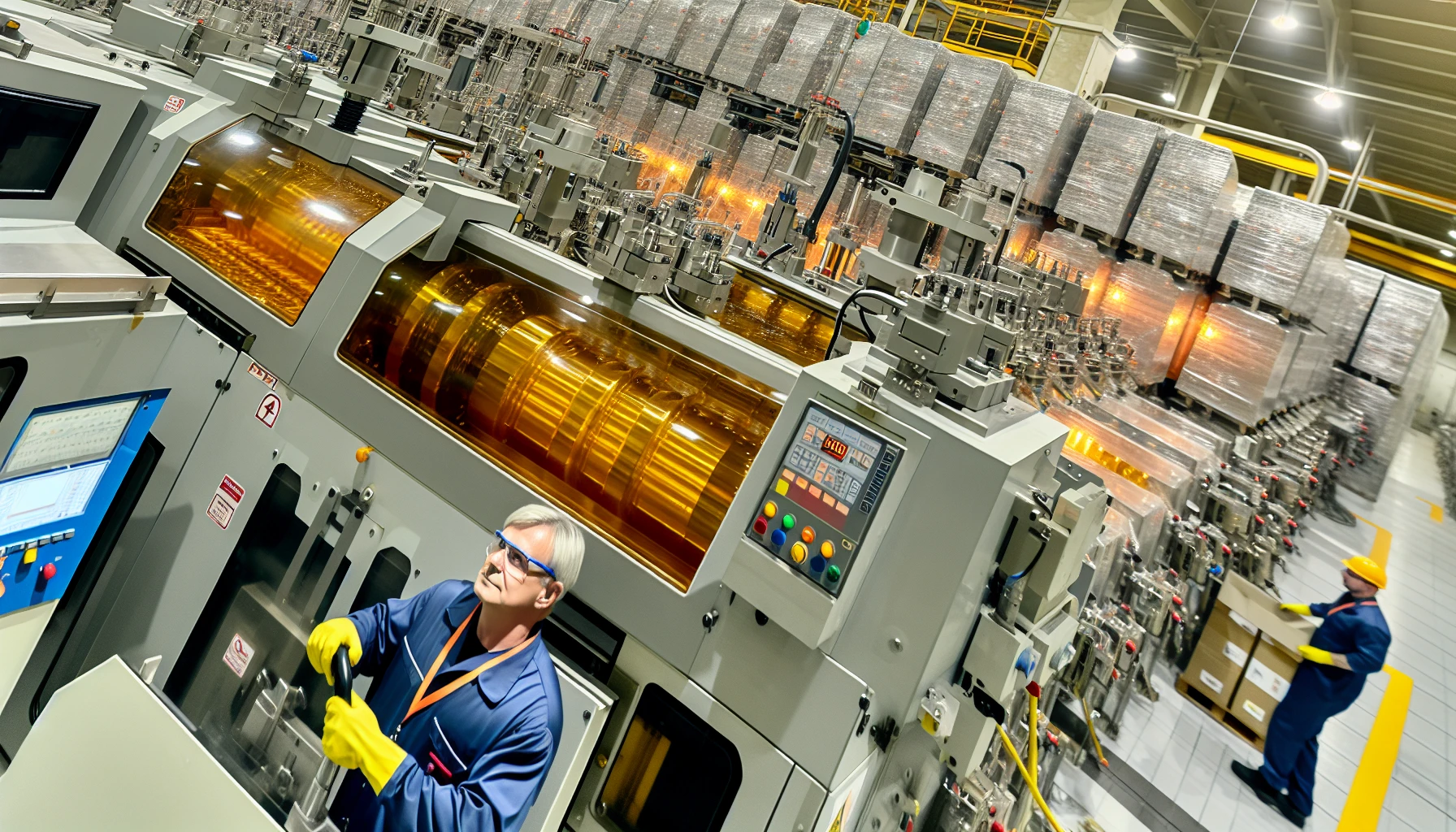
Ultem 1000, a high-performance polyetherimide (PEI) material, is recognized for its superior mechanical, thermal, and chemical properties. It stands out for its extraordinary mechanical, electrical, and dimensional characteristics at elevated temperatures that allow it to cater to a broad spectrum of applications in industries like aerospace, medical, automotive, and transportation.
Its adherence to food contact regulations, RoHS standards, USP Class VI certification, and ITAR registration amplifies its reliability for a plethora of applications.
Key Properties of Ultem 1000
Ultem 1000 is celebrated for its superior mechanical, electrical, and dimensional characteristics under high temperature conditions. Its minimal staining, microwave transparency, and cool touch solutions make it an attractive choice for various applications. Ultem 1000 is an amorphous material that offers excellent chemical resistance. Additionally, it achieves impressive UL94 V0 and 5V ratings, and FAR 25.853 compliance for aerospace use..
The exceptional dimensional stability of Ultem 1000 distinguishes it from other materials. It maintains its integrity when exposed to various fuels, coolants, and lubricants, making it suitable for applications that require continuous use under extreme conditions. This high-performance thermoplastic is a game-changer for industries that demand materials with high strength, resistance to stress cracking, and overall durability.
Comparison with Other PEI Grades
Ultem 1000 is a reinforced Polyetherimide material containing 10% glass fibers. Its features include:
- Glass transition temperature (Tg) of 217C
- High temperature resistance
- Broad chemical resistance
- Suitable for applications that require higher temperature resistance and flame retardancy than other PEI grades.
Other PEI grades like HU1110, even though they display high-performance attributes, are more apt for varied applications. For instance, Ultem 1000 is ideal for medical devices and pharmaceutical applications due to its outstanding electrical properties, while other PEI grades are more suitable for automotive lighting applications where highly metallized, reflective surfaces are needed.
Grasping the distinctions between Ultem 1000 and other PEI grades equips engineers and designers with the insight needed to pick the most suitable material for their respective application.
Applications of Ultem 1000
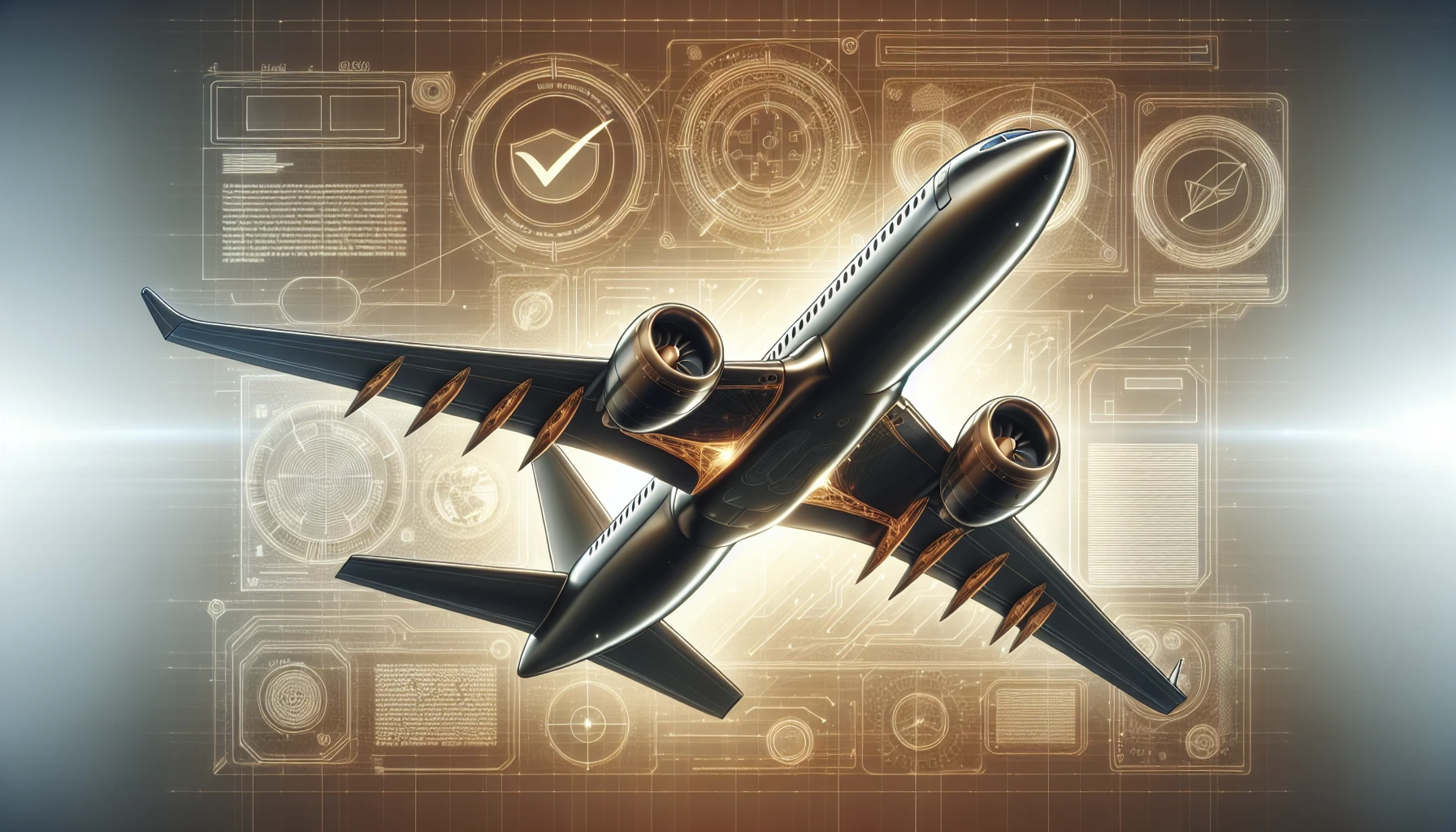
The unique amalgamation of properties and certifications equips Ultem 1000 with versatility, enabling it to serve a diverse range of industries and applications. The subsequent sections will spotlight the specific applications of Ultem 1000 across the aerospace, medical, and automotive sectors, illustrating its role in revolutionizing these industries.
Aerospace Industry
In the aerospace industry, Ultem 1000 is employed in engine components, fuel tanks, and airframes of aircraft. Its compliance with FAA regulation 25.853 regarding flammability makes it a trusted choice for applications that require flame resistance and excellent mechanical properties.
Ultem 1000’s resistance to creep and ability to maintain its integrity when exposed to various fuels, coolants, and lubricants make it a popular choice for weight reduction and cabin interior components in the aerospace industry. Additionally, its high temperature resistance, inherently flame resistant nature, and excellent electrical properties make it suitable for potable water applications in the industry. Its long term heat resistance further solidifies its position as a top choice for these applications.
Medical Sector
Ultem 1000 is formulated from HU1000 resin specifically for medical devices and pharmaceutical applications. It is compliant with biocompatibility standards (ISO 10993 or USP Class VI) and can be sterilized using the following methods:
- Steam
- Gamma
- EtO
- E-beam
The material’s biocompatibility, dimensional stability, and machinability make it suitable for intricate medical devices.
Medical devices manufactured using Ultem 1000 include disposable and re-usable medical devices, medical monitor probe housings, and medical devices that are sterilized through high-temperature processes. Its ability to withstand repeated sterilization is a critical factor in the medical industry, making Ultem 1000 a go-to material for various medical applications.
Automotive and Transportation
In automotive applications, Ultem 1000 finds utilization in areas such as lighting and interior components. Its high heat resistance, flame resistance, chemical resistance, and high rigidity make it an ideal choice for various automotive applications.
ULTEM 1000 is utilized for a variety of components in automotive lighting, as well as in the interiors of cars and other vehicles for a range of applications. Its high heat resistance and mechanical integrity make it suitable for electrical and lighting systems, circuit boards, and other components in automotive and aviation interiors.
Additionally, it is used in the manufacturing of household items and food preparation equipment.
Processing Techniques for Ultem 1000
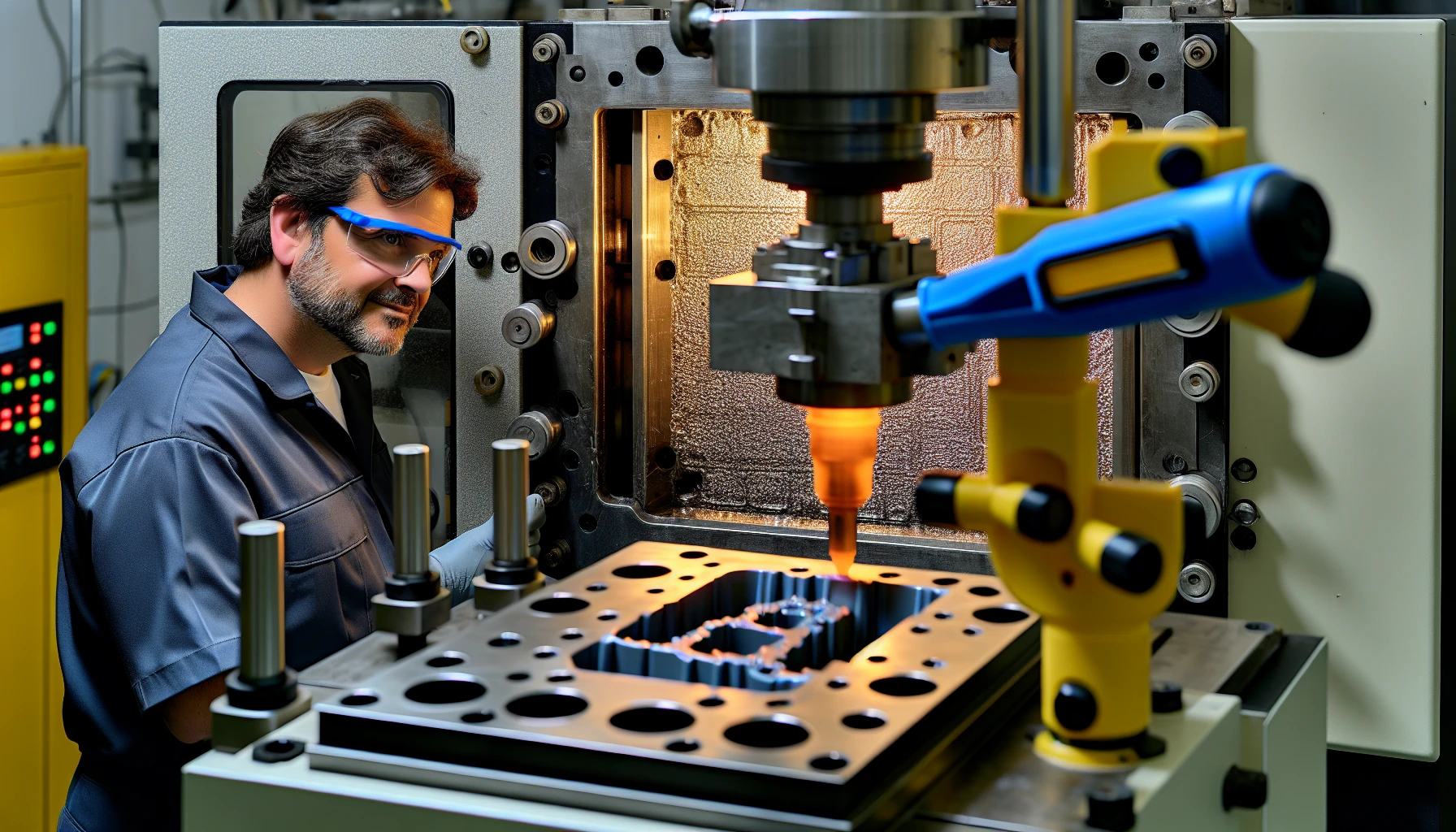
Various processing techniques that can be employed with Ultem 1000 include:
- Injection molding
- Extrusion blow molding
- Thermoforming
- CNC machining
Each technique presents a unique blend of benefits and challenges, necessitating the selection of the most fitting processing method for a particular application.
This section will delve into a detailed exploration of each technique.
Injection Molding
Injection molding is a manufacturing process for producing parts through the injection of molten material into a mold. Ultem 1000 is capable of being injection molded and is applied in this process. Injection molding offers a rapid and cost-efficient solution for producing consistent parts in large amounts.
During injection molding, Ultem 1000 is melted and injected into a mold, where it cools and hardens before being pushed out via the ejector pin. The benefits of using injection molding for Ultem 1000 compared to other processing techniques include:
- Efficient high production
- Excellent process abilities
- Temperature resistance
- Cost savings
- Part reliability and consistency
Extrusion Blow Molding
Extrusion blow molding is a manufacturing process that produces hollow objects from thermoplastic. Ultem 1000 is capable of being extrusion blow molded and is utilized in this process. The process involves:
- Heating the material to a molten state
- Extruding it through a die to form a hollow tube
- Inflating the tube using compressed air to take the shape of the mold cavity
- Cooling and solidifying the material
- Opening the mold and removing the finished product.
This technique is widely used for producing bottles, containers, and other hollow plastic products.
Advantages of extrusion blow molding for Ultem 1000 include:
- High output velocities
- Precise products
- Repeatability
- Cost-effectiveness
- Simpler material flow
Thermoforming
Thermoforming is a process in which a plastic sheet is heated to a malleable forming temperature, shaped to a specific form in a mold, and trimmed to create a functional product. Ultem 1000 is capable of being thermoformed and is employed in this process. Thermoforming offers a number of benefits for Ultem 1000, such as increased tensile strength, rigidity, and dimensional stability compared to other materials.
It is also highly versatile, working with both thick-gauge and thin-gauge plastic sheets, making it suitable for a range of applications. Furthermore, Ultem 1000 has remarkable resistance to creep, guaranteeing long-term performance. Thermoforming is a popular processing technique for this high-performance thermoplastic due to its unique combination of properties.
CNC Machining
CNC machining of Ultem 1000 is a manufacturing process that involves the use of computer numerical control (CNC) technology to control machine tools and shape and cut Ultem 1000 material into desired shapes and dimensions with precision and accuracy. Ultem 1000 has good machinability, but there are certain challenges that must be addressed when CNC machining.
When CNC machining with Ultem 1000, it is important to use moderate feeds and speeds, control heat input, and use coolant. Ultem CNC machining can achieve very fine surface finishes up to ± 1µm. Utilizing CNC machining for Ultem 1000 provides a high level of precision and accuracy, making it an ideal processing technique for various applications.
Regulatory Compliance and Certifications
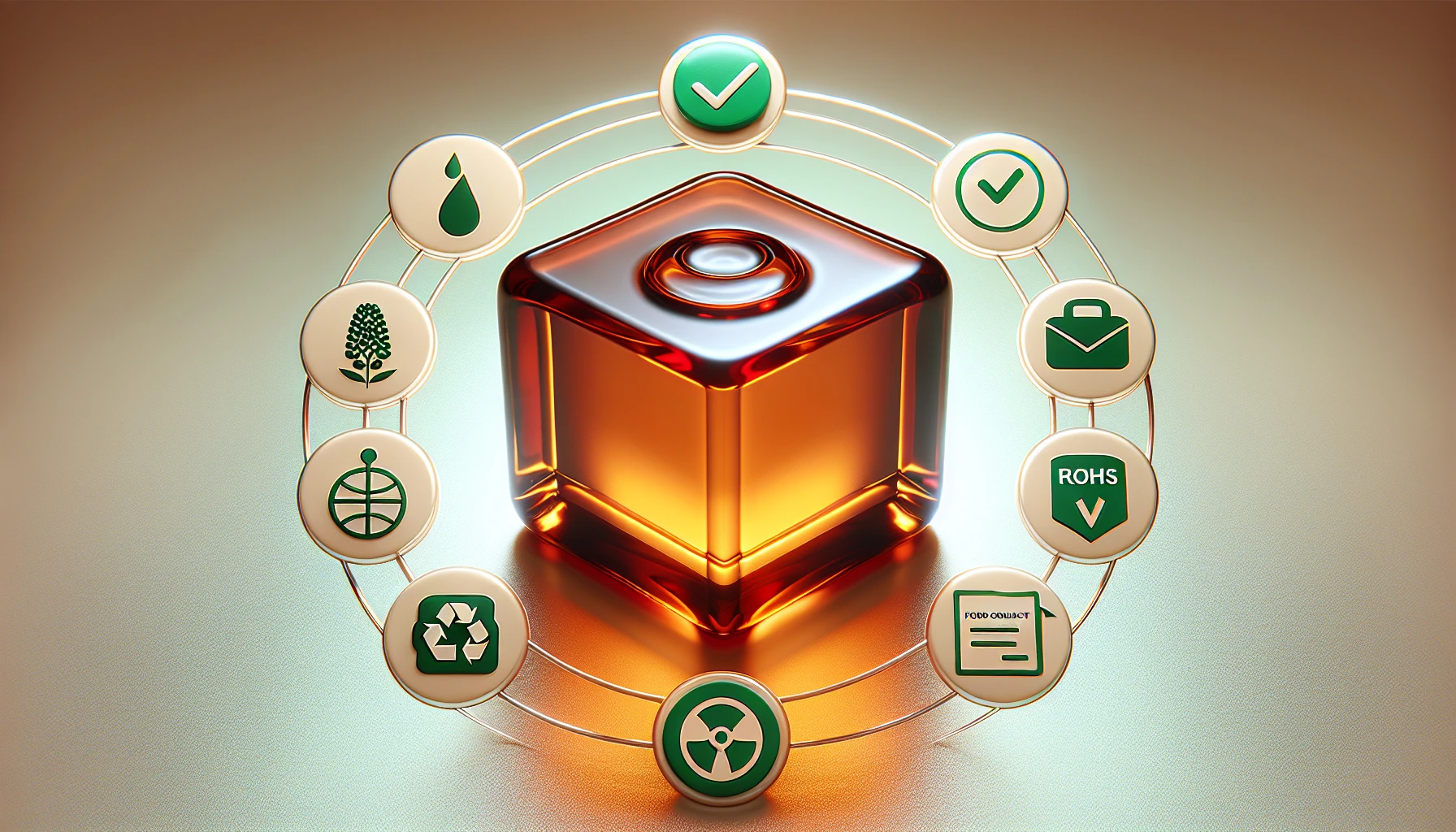
Ultem 1000 adheres to an array of standards and certifications including:
- Food contact
- RoHS
- USP Class VI
These standards ensure the safety and suitability of Ultem 1000 for various applications.
The subsequent sections will provide an in-depth examination of each certification and compliance standard.
Food Contact Compliance
Ultem 1000 is compliant with both US FDA and EU food contact regulations, making it eu food contact compliant. This food contact compliant material ensures safety for use in food processing and handling applications. The material’s high heat resistance, chemical resistance, and excellent mechanical properties make it a popular choice for food contact applications.
Ultem 1000 holds the following certifications for utilization in potable water applications:
- KTW
- WRAS
- ACS
- NSF-61
- W270
This wide range of certifications and compliance demonstrates the versatility and safety of Ultem 1000 in food contact and potable water applications.
RoHS Compliance
RoHS compliance is a directive that limits the use of certain hazardous substances in electronic and electrical equipment. Ultem 1000 meets the requirements of the Restriction of Hazardous Substances directive, meaning it is free from these restricted substances. This compliance is essential for ensuring that materials used in electronic and electrical equipment are safe and environmentally friendly. In addition to RoHS compliance, Ultem 1000 also has a high limiting oxygen index, which further contributes to its safety in these applications.
Ultem 1000’s adherence to RoHS standards makes it a suitable choice for electronic components and devices, thanks to its stable electrical properties. Its excellent mechanical properties, high temperature resistance, and chemical resistance contribute to its suitability for electronic applications.
USP Class VI Certification
Ultem 1000 has been certified USP Class VI, making it suitable for medical applications. USP Class VI certification is a standard that ensures the biocompatibility of materials used in medical devices. Ultem 1000’s compliance with this standard demonstrates its safety for use in medical environments.
In addition to its biocompatibility, Ultem 1000 offers excellent dimensional stability and machinability, making it suitable for intricate medical devices. Its ability to withstand repeated sterilization is a critical factor in the medical industry, further solidifying Ultem 1000 as a go-to material for various medical applications.
Choosing the Right Ultem 1000 Supplier
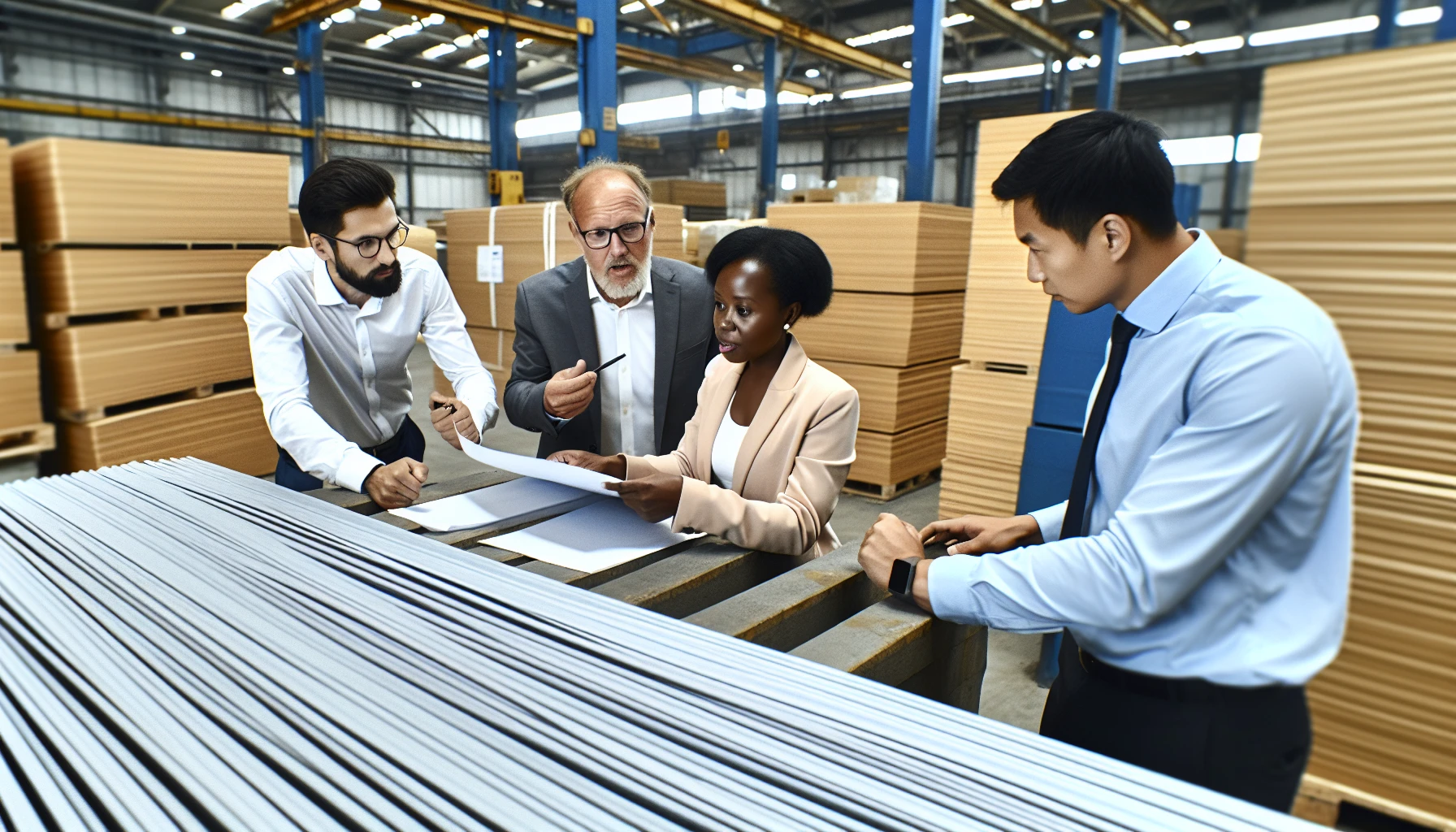
Choosing the most suitable Ultem 1000 supplier is paramount to guarantee top-notch material quality and support tailored to your specific application. This section will discuss the aspects to ponder upon when selecting an Ultem 1000 supplier, such as material quality, technical support, and the availability of customization options.
Material Quality
High-quality Ultem 1000 material is characterized by:
- Heat, solvent, and flame resistance
- High dielectric strength and stability
- Excellent mechanical properties such as tensile strength and flexural strength
The quality of Ultem 1000 material has a significant impact on its performance, providing high strength, impact resistance, hardness, and thermal stability.
When selecting a supplier, it is essential to choose one that can supply consistent and high-quality Ultem 1000 material. Some methods available for testing and verifying the quality of Ultem 1000 material include:
- Mechanical testing
- Thermal analysis
- Chemical analysis
- Dimensional inspection
Technical Support
Technical support is highly beneficial when using Ultem 1000 due to its status as a high-performance thermoplastic with various grades and material properties. Access to technical expertise and professional support can ensure that the material is utilized correctly and any arising issues are addressed promptly.
Moreover, when selecting an Ultem 1000 supplier, businesses should consider the following factors:
- Expertise in Ultem 1000 and its applications
- Access to technical support
- Available resources
- Testing and validation capabilities
- Willingness to collaborate
Ultem 1000 also has particular machining requirements, and technical support can provide direction on machining techniques and optimal practices.
ITAR Registration
The International Traffic in Arms Regulations (ITAR) is a set of regulations established by the U.S. Department of State to control the export and import of defense-related items and services in order to protect national security interests. While Ultem 1000 is not explicitly ITAR compliant, it is a material that is regularly employed in the aerospace and defense industries owing to its high-performance characteristics.
ITAR registration is obligatory for companies involved in the export and import of defense articles and services. It is essential for companies to adhere to ITAR regulations when engaging with defense-related applications, but it does not particularly affect the use of Ultem 1000.
Ultem 1000 is a popular choice for defense applications due to its high-performance properties, including:
- Resistance to high temperatures
- Solvent resistance
- Flame resistance
- High dielectric strength and stability
- Excellent mechanical properties
Customization Options
Ultem 1000 is available in transparent and opaque custom colors, as well as glass-filled grades. Color customization can be achieved through painting or finishing techniques, such as bead blasting. These customization options allow Ultem 1000 to be tailored to specific requirements and design preferences.
In addition to color customization, it is also possible to modify the mechanical properties of Ultem 1000 by adding certain materials or through particular processing techniques, such as annealing. When selecting an Ultem 1000 supplier, consider their ability to provide customization options that meet your specific needs and requirements.
Summary
Ultem 1000 is a high-performance polyetherimide (PEI) material with a unique combination of properties that make it suitable for various applications in aerospace, medical, automotive, and transportation industries. Its excellent mechanical, thermal, and chemical properties, as well as its compliance with food contact, RoHS, USP Class VI, and ITAR regulations, make it a reliable choice for numerous applications. By understanding the material, its properties, applications, processing techniques, and compliance standards, and by choosing the right supplier, you can unlock the full potential of Ultem 1000 for your specific application.
Frequently Asked Questions
What is ultem?
Ultem® is a high strength plastic with semi-transparent properties, making it ideal for use in high temperature environments. It is resistant to hot water and steam, and there are FDA compliant grades available.
What is PEI material?
Polyetherimide (PEI) is an amorphous thermoplastic known for its high temperature resistance, outstanding mechanical and electrical properties, and excellent strength and rigidity. It has the same qualities as polyarysulfones and can resist creep at high temperatures, making it suitable for continuous use.
What industries commonly use Ultem 1000?
Ultem 1000 is widely used in the aerospace, medical, automotive, and transportation industries.
What makes Ultem 1000 resistant to heat and chemicals?
Ultem 1000’s high glass transition temperature, excellent mechanical properties, and broad chemical resistance make it highly resistant to heat and chemicals.
What are the primary processing techniques for Ultem 1000?
Ultem 1000 is typically processed through injection molding, extrusion blow molding, thermoforming, and CNC machining, allowing it to be shaped and molded into a variety of products.