If you’re determining which plastic parts to use in semiconductor manufacturing, you’ll need materials that meet the industry’s high standards for precision and resistance to extreme conditions. In this article, we examine the role of plastic parts for semiconductor, specifically focusing on the performance and reliability of materials like PEEK and PPS. We’ll guide you through selecting the most suitable plastics, ensuring your semiconductor components meet the required quality and consistency.
Key Takeaways
- Plastic parts are critical in semiconductor manufacturing due to their high precision, chemical resistance, and ability to withstand electrical shock; materials like PEEK, PAEK, PEI, and PPS are commonly used for their superior chemical, thermal, and mechanical properties.
- To maintain high quality and consistency in semiconductor manufacturing, adherence to Copy Exact standards and the use of Coordinate Measuring Machines are crucial for ensuring parts meet stringent dimensional and compositional specifications.
- Custom solutions in semiconductor manufacturing, including custom automation and the use of expert partners like Atlas Fibre, are essential for advancing technology and efficiency, improving cost-effectiveness, and meeting the specific performance needs of the industry.
Understanding the Role of Plastic Parts in Semiconductor Manufacturing
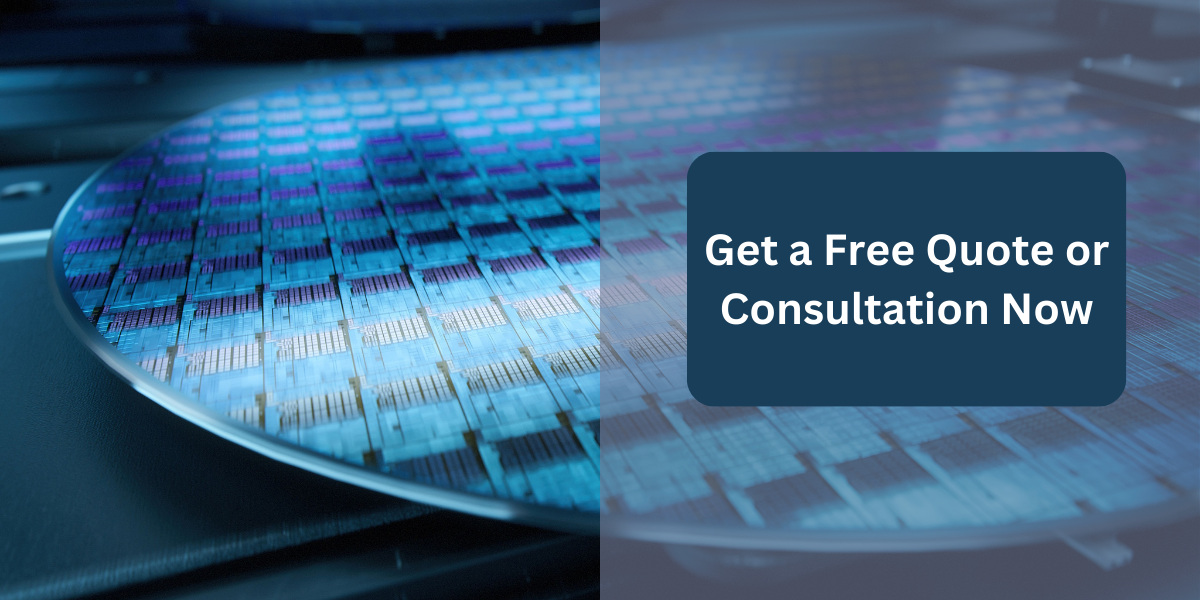
Grasping the significance of plastics in semiconductor manufacturing paves the way for a deeper appreciation of these essential components. Plastic parts uphold stringent standards of precision and purity, facilitating the production of plastic semiconductors and components like electrical insulators and integrated circuits, and are utilized in both wet and dry processes. These components guarantee uniform product manufacturing specifications, thus ensuring quality and consistency.
High performance properties and chemical resistance make plastic ideally suited for producing components like flexible connectors, laminates, and shielding films in semiconductor manufacturing. Such attributes have a direct bearing on the performance of semiconductor industry products. Moreover, the precision of plastic parts plays a crucial role in upholding the exacting standards of precision and purity necessary in semiconductor manufacturing, ensuring the quality and performance of semiconductor products.
Material Properties and Resistance
Assessing material properties and resistance is critical when choosing plastics for semiconductors, given the industry’s requirement for suitable chemical resistance properties. The use of appropriate materials ensures the prevention of harmful contamination.
The resistance of plastics in semiconductor applications is significant for various reasons. For instance, polycarbonate, a semiconductor plastic, is able to resist electrical shock and mitigate static electricity, essential in the production of semiconductor devices.
Furthermore, plastics utilized in semiconductors demonstrate exceptional chemical resistance, rendering them suitable for processes involving corrosive chemicals, such as wet benches in semiconductor manufacturing.
Precision and Form
The reliability and performance of plastic parts in semiconductor manufacturing rely significantly on precision and form. The precision in manufacturing processes has a direct influence on the performance and reliability of plastic semiconductor parts. Even small deviations can have an impact on the dimensional stability and quality of the parts, which in turn can affect their functionality and lifespan.
Utilizing plastic machining techniques, especially automated CNC processes, results in high-precision plastic parts in semiconductor manufacturing. These techniques prove the accuracy and consistency of the plastic parts, ensuring their reliability in the semiconductor manufacturing process.
The form of these parts, influenced by factors such as the plastic packaging process and the form of solder joints, can also have a substantial impact on component reliability.
The Most Common Plastics Used in Semiconductors
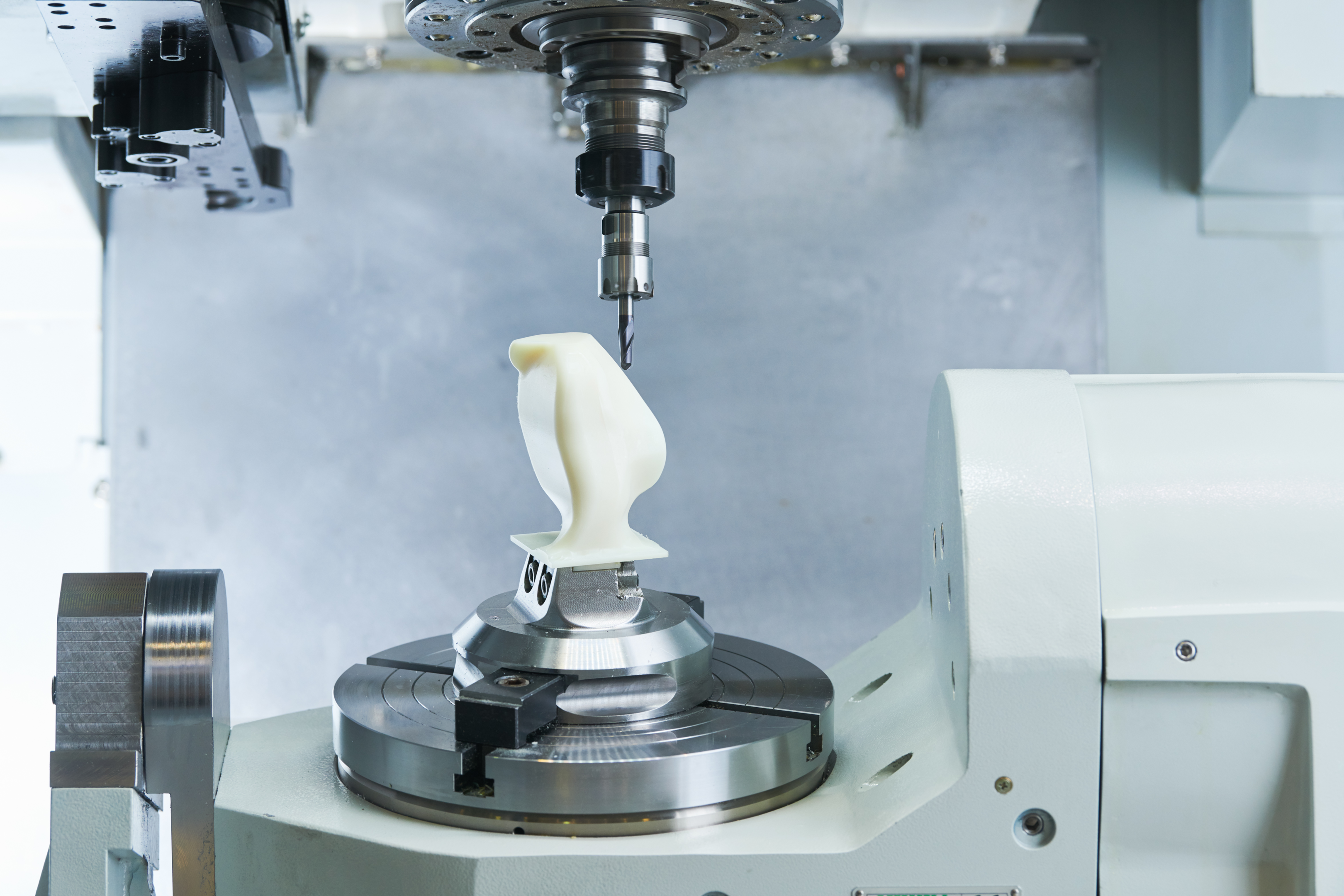
Several types of plastics, each boasting unique properties and advantages, find common use in semiconductors. Among the most common plastics used in semiconductor manufacturing are:
- PEEK
- PAEK
- PEI
- PPS
In the subsequent sections, we will delve into the specific properties of these plastics and how they contribute to the overall performance and function of semiconductors.
The remarkable properties of PEEK make it indispensable for semiconductor manufacturing, including:
- High-temperature resistance
- Exceptional mechanical strength
- Chemical stability
- Minimal moisture absorption
- Superior chemical and wear resistance
- Effective static electricity management
Owing to its high-temperature strength, robust mechanical properties, FDA compliance, chemical resistance, advantageous electrical properties, and flame retardance, PAEK is particularly suitable for the semiconductor industry.
By offering high strength and preserving excellent electrical properties, even at high temperatures, PEI enhances the functionality of semiconductors.
PPS is chosen for semiconductor manufacturing due to its exceptional resistance to high temperatures, chemicals, and its robust mechanical strength.
PEEK
PEEK is well-suited for semiconductor manufacturing because of its outstanding mechanical properties, including:
- Resilience
- Durability
- Strength
- Resistance to wear, moisture, and chemicals
- Exceptional strength
- Dimensional stability
- Stiffness
These properties make it ideal for this advanced technology.
PEEK’s exceptional chemical resistance and ability to maintain strength at elevated temperatures make it well-suited for the challenging conditions encountered in semiconductor processing. Its high temperature tolerance, reaching up to 260 °C/500 °F, holds significant importance in semiconductor applications, where stability and performance at elevated temperatures are essential.
PEEK for semiconductor applications can be manufactured through injection molding, additive manufacturing, or CNC machining, which offer the repeatability and precision required for parts with tight tolerances.
A common application for PEEK in semiconductor materials is CMP retaining rings, a use case we detail here.
PAEK
PAEK possesses characteristics such as high-temperature resistance, exceptional strength, chemical resistance, and low moisture absorption, all of which contribute to its suitability for use in semiconductor manufacturing. PAEK, particularly PEEK, finds application in the semiconductor industry for purposes including serving as screws and fasteners in wet benches, as well as being utilized in components for semiconductor manufacturing equipment.
Typical processing techniques for PAEK in semiconductor manufacturing encompass deposition, removal, patterning, and modification of various components. However, the use of PAEK in semiconductor manufacturing is not without challenges. Reducing leachables, friction, and contamination, as well as extending product lifespan, decreasing wear, enhancing sealability, and mitigating outgassing, can all present difficulties.
PEI
PEI plastic exhibits resistance to high temperatures due to its high mechanical strength, stability, and favorable chemical and temperature resistance. It maintains stiffness and impact resistance even at elevated temperatures, and its high heat deflection temperature makes it suitable for applications operating under high-temperature conditions.
PEI provides excellent dimensional stability due to its outstanding resistance to thermal deformation, a low coefficient of thermal expansion, and minimal moisture absorption—all critical factors for maintaining precise dimensions under varied environmental conditions. Its mechanical strength and rigidity render it well-suited for the production of precise and stable parts essential in the semiconductor industry.
PPS
PPS is considered a cost-effective material for semiconductor manufacturing due to its exceptional thermal properties and chemical resistance, which make it well-suited for the industry’s needs. The benefits of PPS in semiconductor manufacturing include:
- Exceptional thermal properties
- Chemical resistance to acids, alkalis, ketones, and hydrocarbons
- Outstanding structural performance in harsh chemical environments
These properties make PPS an ideal choice for the semiconductor industry.
PPS exhibits the following properties:
- High thermal stability, enabling it to retain its mechanical strength and rigidity even when exposed to temperatures exceeding 200°C
- Chemical stability at elevated temperatures
- Resistance to a wide array of chemicals
PPS exhibits the following properties:
- High dimensional stability
- Exceptional mechanical strength (even at elevated temperatures)
- Outstanding strength-to-weight ratio in comparison to other plastic types employed in the semiconductor industry.
Ensuring Quality and Consistency in Plastic Part Production
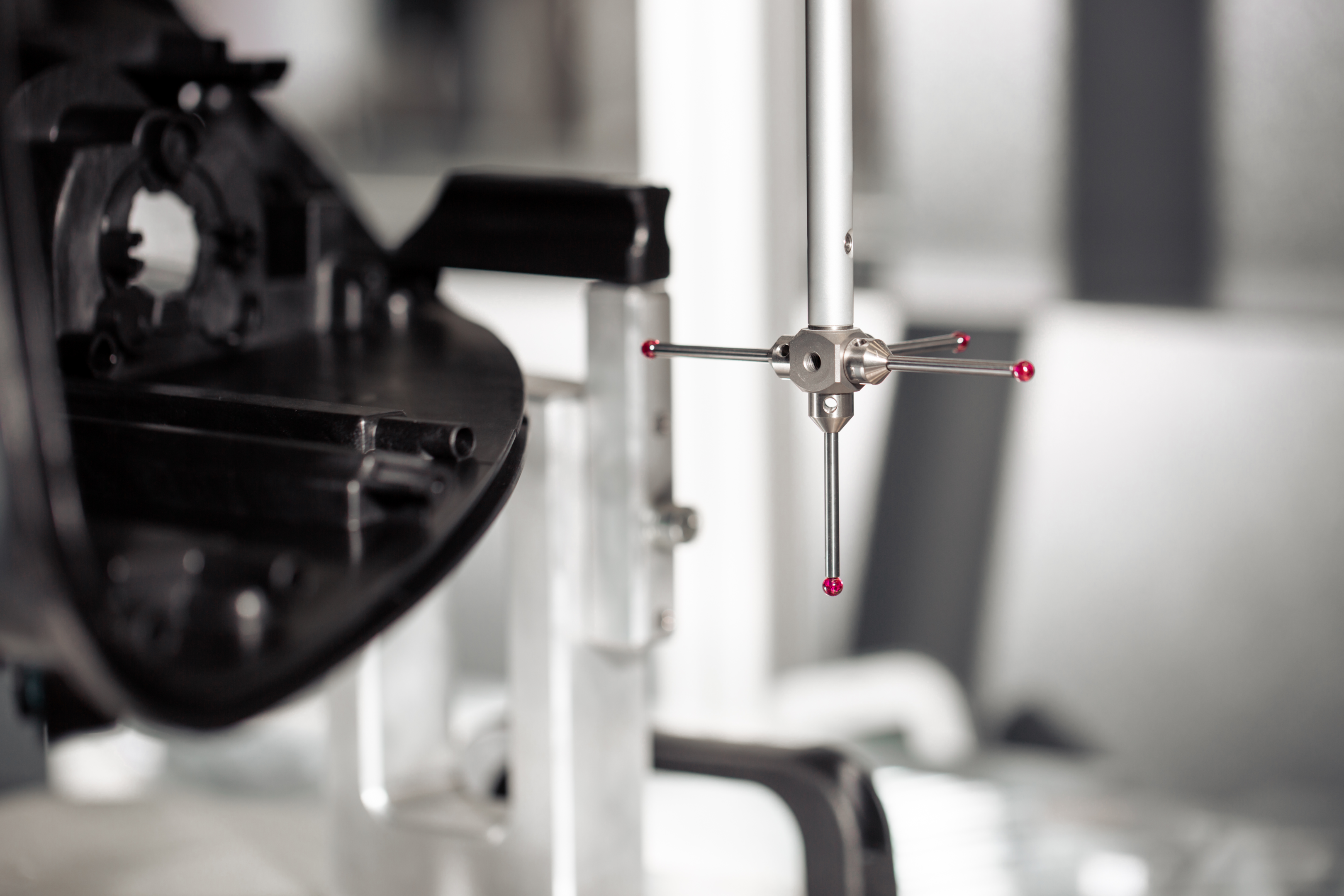
Guaranteeing the quality and consistency of produced plastic parts holds paramount importance. In the semiconductor industry, Copy Exact standards play a crucial role in preventing variations in part dimensions or material composition, which is significant for maintaining high quality and consistent output. Coordinate Measuring Machines (CMMs) also play a critical role in guaranteeing the accuracy of plastic parts in semiconductor manufacturing by validating dimensional precision, identifying imperfections, and ensuring compliance with stringent quality standards.
The quality of plastic parts in semiconductor manufacturing is also evaluated using testing fixtures, such as test sockets and inspection fixtures, as well as thermal quality testing for semiconductor components. These evaluations are conducted to ensure that the parts perform reliably under the conditions they will encounter in use.
Copy Exact Standards in Plastic Manufacturing
Copy Exact standards encompass the requirements and procedures aimed at ensuring the precise replication of a specific product or component with the same specifications. While there is no universally acknowledged industry standard, Copy Exact manufacturing involves rigorous contamination control and heightened verification measures to achieve the desired level of replication.
The procedures required for the implementation of Copy Exact standards include aligning the physical inputs, providing training and qualification for personnel, and maintaining proper documentation. Upholding Copy Exact standards in plastic manufacturing for the semiconductor industry can present challenges due to the industry’s stringent environmental considerations, the necessity for precise control over molding and machining procedures, and the obligation to guarantee the absence of particles and impurities in all components.
Coordinate Measuring Machines for Accuracy
A Coordinate Measuring Machine (CMM) serves as a tool in the production of plastic parts, employed to assess the physical geometrical attributes of an object and verify its adherence to the specified design parameters. Coordinate Measuring Machines (CMMs) operate based on two primary principles: utilizing a mechanical probe that makes contact with the object for measurements and employing a coordinate system to define the position and orientation of the object being measured.
Coordinate Measuring Machines (CMMs) ensure exceptional value by providing precision up to a micrometer, carefully assessing physical attributes, taking into account factors such as the feature being measured, workpiece conditions, environmental influences, and surface properties.
A diverse range of Coordinate Measuring Machines (CMMs) are employed in the manufacturing of plastic parts, encompassing:
- Bridge CMMs
- Cantilever CMMs
- Gantry CMMs
- Horizontal arm CMMs
Each type is tailored to specific measurement requirements and production configurations.
Designing Plastic Components for Semiconductor Applications
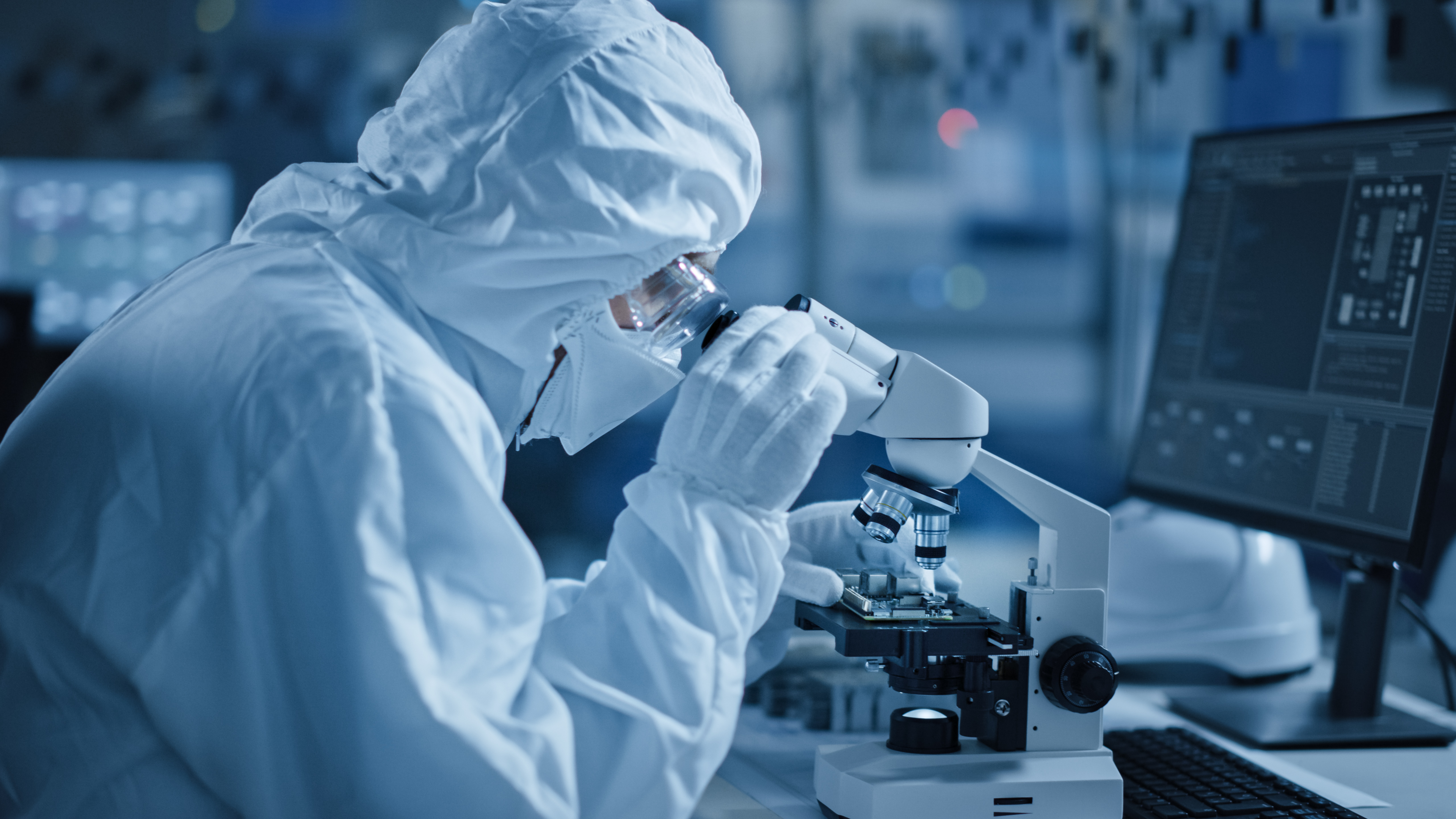
Designing plastic components for semiconductor applications requires a delicate balance of various factors. Designers can achieve a balance between cost and performance by carefully selecting the appropriate plastic package for the specific application, utilizing high-performance polymers to attain the desired characteristics, and optimizing the production process to minimize costs while upholding or enhancing part quality. The design of plastic components for semiconductor applications is influenced by performance, as high performance plastics must maintain excellent dimensional stability and exhibit exceptional chemical resistance properties to meet the demands of semiconductor manufacturing environments.
Following ISO standards is also vital when designing and manufacturing plastic components for semiconductor applications. Standards such as ISO/TS-16949 and ISO 15494:2015 guarantee quality and uniformity in the design and manufacturing procedures for plastic components utilized in semiconductor applications.
Primary considerations when designing plastic components for semiconductor applications include:
- Evaluating material properties
- Ensuring the components can withstand harsh chemicals and static electricity
- Considering the precise dimensions required for the application
Balancing Cost with Performance
To balance cost and performance in the design of plastic components for semiconductors, one must factor in:
- Material considerations
- Performance requirements
- Dimensional attributes
- Target cost
Optimizing part dimensions to minimize material waste in machining is one approach. Additionally, utilizing high-performance plastics with superior dimensional stability can help uphold tight tolerances across temperature variations.
The influence of design is pivotal in achieving a harmonious balance between product performance and cost-effectiveness in the production of plastic components for semiconductors. The use of high-performance polymers in parts can significantly contribute to this equilibrium. Furthermore, increased intricacy in design and manufacturing processes may result in elevated costs. Considering an appropriate model for these processes can help optimize the balance.
ISO Standards in Design and Manufacturing
The ISO standards relevant to plastic component design and manufacturing comprise ISO 20457 for manufacturing tolerances, ISO 68000 for safety requirements of injection moulding machines, and ISO 13485 for quality standards in the manufacturing process. ISO standards have a significant impact on the global semiconductor industry by defining requirements, facilitating collaboration between customers and suppliers, managing continual improvements, ensuring product quality, and meeting regulatory requirements.
The procedure for a company to obtain ISO certification in manufacturing plastic components entails implementing the requisite requirements specified in the pertinent ISO standard, typically requiring a minimum of six months to a year from implementation to registration. ISO 15494:2015 outlines the characteristics and requirements for plastic components, including pipes, fittings, and valves, that are utilized in semiconductor manufacturing.
Custom Solutions for Advanced Semiconductor Needs
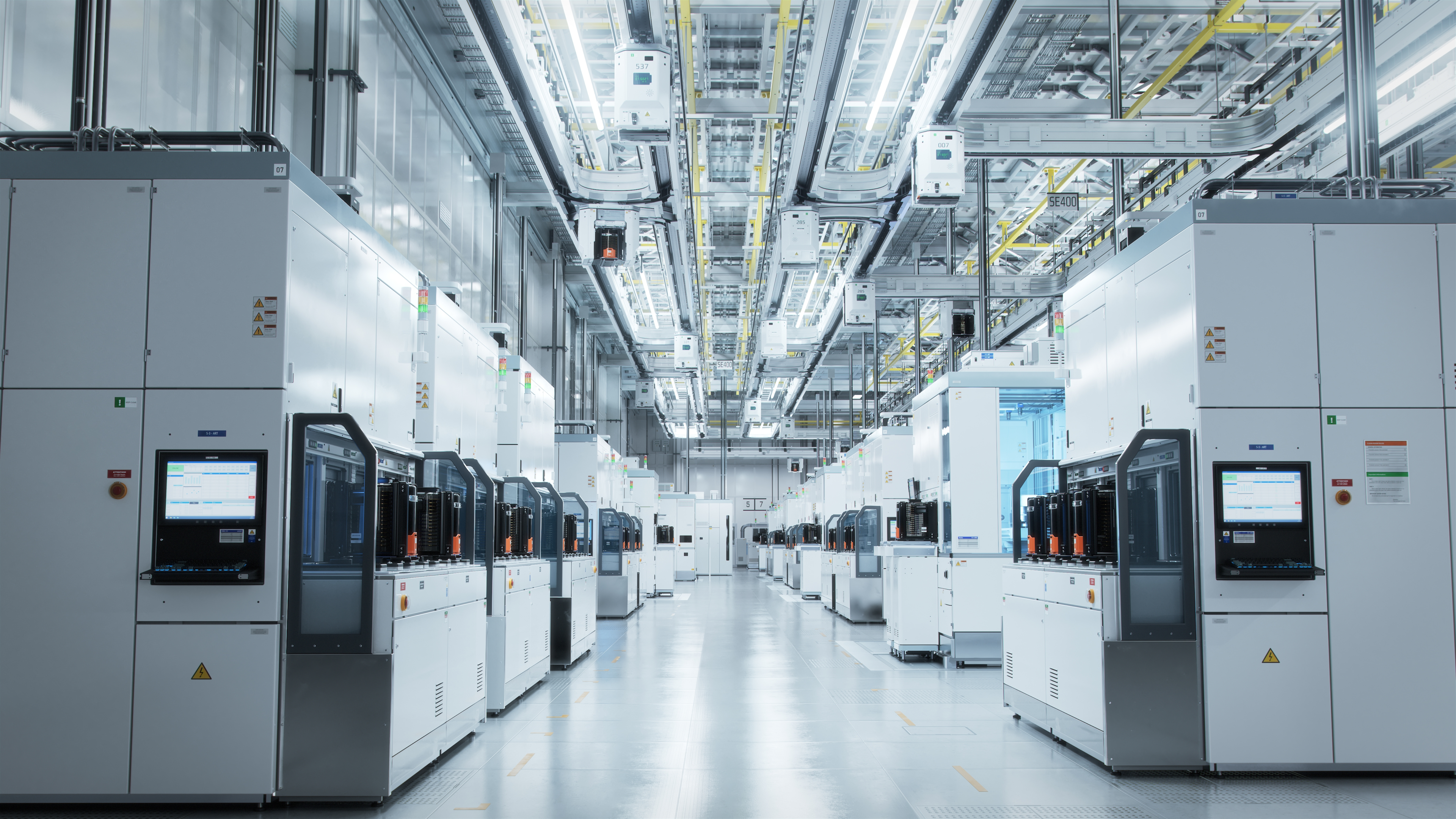
As the semiconductor industry progresses, the needs and demands of its participants also evolve. Custom solutions for advanced semiconductor needs encompass:
- Manufacturing solid-state memories (DRAM)
- MOSFETS
- 3-D NAND flash memories
- DSPs
- MPUs
- Advanced chip packaging utilizing chiplets
- Creation of custom packages to fulfill specific demands.
The impact of customization on semiconductor performance is evident through the use of customized equipment for silicon wafer processing, which provides performance advantages and differentiation. Customization involves finely tuning custom silicon to the precise needs of an application, further enhancing semiconductor performance.
Partnering with Experts in Plastic Manufacturing
Partnering with plastic manufacturing experts like Atlas Fibre can yield manifold benefits. Such collaboration can improve cost-effectiveness, operational efficiency, and the longevity of the parts. Atlas Fibre, for instance, provides exceptional strength, resistance to chemicals, weight reduction, flexibility in design, utilization of advanced equipment, stringent quality control measures, and personalized services designed to meet specific requirements.
Atlas Fibre upholds high standards of quality in its plastic manufacturing process for semiconductors by conducting meticulous batch and sheet testing to control quality and assess properties. The company has made a significant contribution to the semiconductor industry as the foremost supplier of thermoset composite materials, providing the largest selection of in-stock materials in the United States, including carbon fiber thermoset plastics crucial for semiconductor manufacturing. Contact us today!
Summary
In conclusion, plastics play an indispensable role in semiconductor manufacturing, due to their properties including precision, purity, and resistance. The most common plastics used in this industry include PEEK, PAEK, PEI, and PPS, each with its unique attributes and advantages. To ensure quality and consistency in the production of these plastic parts, methods such as Copy Exact standards and the use of Coordinate Measuring Machines are implemented. Balancing cost with performance and adhering to ISO standards are crucial considerations in designing plastic components for semiconductor applications. Finally, custom solutions and expert partnerships can significantly enhance the performance and efficiency of semiconductors.
Frequently Asked Questions
Which plastic is used in semiconductors?
Semiconductors often use HDPE (high-density polyethylene), PEEK, PAEK, PPS, or PEI for their strength, resistance to acids, and versatility in creating quality and pure plastic parts.
Is plastic a good semiconductor?
Generally plastics are insulative but can have fillers or additives that make them conductive or suitable for ESD applications. This transformation allows plastics to be used effectively in these fields.
What measures are taken to ensure quality and consistency in plastic part production?
To ensure quality and consistency in plastic part production, we implement Copy Exact standards and utilize Coordinate Measuring Machines. These measures help maintain high standards and accuracy in the production process.
What considerations are important when designing plastic components for semiconductor applications?
When designing plastic components for semiconductor applications, it’s crucial to balance cost with performance and adhere to ISO standards to ensure quality and reliability.